Introduction: Pallet Coffee Table With Lifting Top and Landing Gear
A coffee table made from upcycled pallet wood and bed slats. The table top lifts to be used as a work surface when seated and also reveals a storage compartment beneath. A pedal-controlled retractable castor wheel system allows the table to be moved smoothly and easily, yet remain stable when in use.
[Please note I had no intention of creating an Instructable when beginning this project, so I apologise if some stages are a little thin on the photograph side of things - I'll do my utmost to fill in the blanks using notes in the photos I do have.]
Our original coffee table was an IKEA Lack which was, appropriately, lacking in various areas: The dimensions were not ideal for the size and shape of our living room - it was slightly too long (900mm), slightly too narrow (550mm) and slightly too tall (500mm). So came the decision to build my own.
While we have a nice desk (converted base from an old sewing machine, if you're interested,) it does involve some minor gymnastics to reach it behind the sofa which is far from ideal. I wanted to create something that had a sturdy surface just over knee height for writing/typing, etc, which could be used instead of the desk for brief periods.
The other major consideration is that I have an ~18-month-old son running around the place. Whatever I ended up with needed to be safe for him and easy for us to move around - for all its faults, the old coffee table was good at blocking off areas of the living room.
Perusing Instructables during my lunch hour, I found user lofgren's wonderful Coffee table upgrade! which, in terms of functionality, was exactly what I wanted to achieve. As I very much liked the various and clever pallet projects found on Instructables and (having never made furniture before) knowing the process would involve trial and error, re/upcycling cheap and imperfect pallet wood seemed the obvious route.
Tools, parts and materials used:
• Three or four clean pallets
• A stack of not-too-worn bed slats
• Scrap/spare wood
• Drill, various bits including hole saw
• Jigsaw, originally with a crappy flexing blade, later with a stiff neat-cut blade
• Power sander, with coarse and not-so-coarse paper
• Various spanners, screwdrivers, chisels, mole grip, piers, pincers, crowbar
• Rasp
• Set square
• Steel ruler
• Measuring tape
• An assortment of screws I have
• Gorilla wood glue (I can't recommend this stuff enough)
• Clamps. I had only four, but the more you have the merrier you will be
• Wood stain, lint-free cloth
• 10mm dowel
• Screws, various
• M8 x 100mm bolts
• Regular, ny-lock nuts and T-nut
• Washers, various
• x4 50mm rubber castor wheels, no brakes
• x2 80nm gas struts/stays
• x5 Screw-in eyelets.
• x4 M8 adjustable feet
• Cork pads to attach to feet
• Springs, various
Step 1: Planning
Having acquired a few decent pallets from friends, I set about pulling them apart. This Instrucable on How To Dismantle a Pallet may be useful, though I admit to having only properly read it post-build. (I used a crowbar, a large old screwdriver, pliers, pincers, patience, cursing and brute force to get mine apart - you'll find the combination that works for you.)
Once dismantled, I gave the pieces a once-over and quick attack with the power sander to get rid of any obvious mess/splinters. I soon realised a rasp is invaluable when working with pallet wood too; just being able to quickly take any particularly nasty edges or ends off in order to make the wood easier to handle was a boon.
After measuring the different parts I ended up with, I jotted my inventory into a Moleskine to try and work out what would/could go where. I had four half-decent planks at 1200mm and around 150mm wide. Using those four planks as a top/lid which, combined, have a 600mm width (and deciding its height based on our legs/sofa seats,) I had the dimensions of my coffee table: 800mm long, 600mm wide and 450mm high, with the table top to lift to a useable 600mm high in the raised position.
I then spent a few lunch times using the excellent web-based Tinkercad which I highly recommend for those wanting a simple and free tool to play around with basic CAD. (I only say 'basic' because that's what I used it for, but it's undoubtedly far more capable than I am, so try it for yourself.) Once I had decided more or less what I could do with the parts at my disposal, I set about building it.
Step 2: Measure, Cut, Sand, Glue, Screw, Repeat
After cleaning and sanding the rough pallet wood to within an inch of its life, I cut four planks to 600mm in length and glued them to the four support blocks (is there a proper name?) of the pallets. These blocks would form the corners of the upper section of the coffee table with the planks crossing its width, so essentially I built the upper end sections of the table.
I then glued four of the 800mm bed slats to these sections, creating the length of the table and the basic box/frame of the upper section. The basic dimensions were now in place.
The four corners on the top side were drilled and 10mm dowel glued and inserted - partially because I wasn't sure how good the glue was (very good) but primarily for it to look a little smarter. The undersides were screwed in for strength.
To act as a foundation for the storage space beneath the table top, I attached (by glue and screws) two more 800mm slats on the underside of the frame, parallel to the existing ones. (I'm not sure if that makes sense, hopefully photos in the next step will bring a little clarity.)
The four table top-to-be planks were cut down to just over 800mm and tested for fit. It began looking like it might not be a complete disaster...
Step 3: Legs / Base
After toying various ideas for styles of leg, I decided (influenced in some part by the lack of a mitre powersaw) to make a 'double-decker'-style lower section that aped the upper, i.e. four corner blocks held in pairs by two 600mm planks.
Two 800mm slats connected these 'legs' on the underside along the length of the table. I decided it would be easier to create a lower shelf with these in place, as well as making the whole thing a bit more robust.
(I cannot find a photograph of the table at this stage, so you'll have to take my word for it and trust the before and after pictures, sorry.)
Using dowel (10mm) and screws, I attached the lower (leg) half to the upper (table top/storage) half. I decided against glue so I'd have the option to replace the legs should they not prove suitable. For strength, I later used two 8mm bolts on each end (through the 600mm planks) to hold the two sections together securely.
By now I had something vaguely reminiscent of a small pallet on, well, other parts of a small pallet. Almost precisely what it was.
Step 4: Lifting the Top...
The mechanism to lift the table top is fairly straight forward and nothing you won't have seen before. Battens are screwed to the corner posts on the inner side wall of the short ends of the table. The ends of two wooden arms are bolted to each of these battens, one approximately half-way along the baton and the toward the 'front' end of the table, toward the direction the table top will lift.
The 'front' batten, when in the upright position, must learn slightly forward of center and rest on the edge of the table for stability as it is less likely to get knocked back into its lowered position. Spacing the battens in this way I found to be the best compromise of sturdiness and maximum height for the table top.
The top ends of the arms are then bolted to two battens running parallel to the lower ones on the underside of the table top. The space between the holes on both the lower and upper battens must be equal - in the case of my table, ~230mm apart - so the arms remain parallel to one another regardless of position. Needless to say, this ensures the table top remains parallel to the floor whether lifted, lowered, or anywhere between.
I'm sure someone with a better grasp of geometry and numbers would work out the perfect measurements to achieve the the optimum distances between the various points and parts, I did it through trial and error. Cardboard
Using a jigsaw, I cut out a curve from the front and rear lengths of the upper table frame to allow the edges of the table top to be grasped and lifted or lowered without having to force finger nails between the frame or risk pinched fingers on the way down. Secondary to the ergonomic benefits, it also encourages the person lifting the table top to apply force along the centre-line of the top rather than either the left or right. While it will lift to an extent when this is done, it's certainly not healthy to the mechanism in the long run.
Though the lift-top mechanism now works as expected (and by as much luck as judgement, lifted to exactly the height I required,) the top it was still awkward to lift with one hand and slammed shut with an almighty bang. Gas struts are required. These had been planned since day one, so now I just had to fit them. While they're available for surprisingly little online, I opted to go into a shop to pick them up as I had no idea what 80nm or 120nm would feel like when deciding on how powerful to go. Again, someone with a head for maths would undoubtedly work this out in a moment or two, but my route was to play with them and see how it all fit and subsequently felt.
I settled on two 80nm struts and, after the obligatory trial and error period, screwed mounting plates to the 'front' arms of the mechanism. The second mounts needed to be higher than the base of the storage section would allow, so I glued a slat along the bottom of the inside the base and added a smaller additional block of wood to raise the strut mount by around 40mm with more glue/screws. Again, I loosely followed the guidelines that came with the struts, but it was mostly done by feel and eye. It took a bit of playing around with to get right, but when I found the sweet spots for the mounts, the struts worked their magic.
Now the table top could be lifted with just a couple fingers under the front side of the lid and would gently rise to its maximum height and stop with a gentle thud. It takes a bit of effort to shut the lid, but this is preferred as we don't have to worry the lid will suddenly drop down during normal use and our son won't be able to close it and trap and/or hurt himself.
Step 5: 'Hidden' Storage Compartment
The box-type pallet design I used to build the top has a natural cavity at its centre which would naturally be exposed when lifting the lid. The options were to either block it off entirely and allow it to be used as a secondary table top when the lid was raised or use its full depth and have somewhere to store things. Easy choice for me, so I went for the latter.
The lift-top lever arms and gas struts were already in place at the sides, so knowing the space they took up at either end of the table, it was fairly straight-forward working out how large the storage space could be.
I measured and cut eight planks of pallet wood to size and sanded them well. Using two to form walls to block off the exposed lift-top mechanism, the remaining six formed the base of the storage space. I put a two or three large washers onto a bolt and used the combined depth of the washers as a spacer to get the base planks an even distance from one another and clamped them in place while I drilled and screwed them to the supporting beams beneath.
Two longer planks were cut to length and fitted in the open sections at the front and rear of the table, simultaneously neatening the table and forming and front and back walls of the storage compartment. These are each connected by four screws to the ends of the upright planks that form the compartment walls. I tried to sand the wood as minimally as possible on the outer faces of these planks as I rather liked the texture. The inside received a more thorough sanding and smoothing.
There is a gap around 30mm on the top of the these facing planks. Initially, I was going to block them off entirely but they've actually proved rather useful as books/magazines, etc, can be slid into the compartment without having the lift the table top. The far left and right sides of this gap (both front and rear) will, however, be blocked off to prevent things being pushed into the end sections where the arms and gas struts are found.
Step 6: Lifting the Rest of It...
Knowing my son would climb on the table and try to push it around, I wanted the table to be simultaneously sturdy and hard to move, but relatively easy to move around the living room to either block parts of it off or make room for playing.
At first I considered castors on each corner, but figured, even with the brakes on (which in themselves would be a pain to use frequently) it would be too unstable. I was hoping, therefore, it'd be as simple as having two castors on one side and two static feet on the other which would allow us to lift only the side of the table with feet mounted and roll it on the side with the castors.
I bought some cheap plastic castor wheels (25mm diameter, 40mm from bottom of wheel to top of bracket) and screwed them through a 10mm square of wood and onto the underside of the table. The result is that the table is raised by 50mm, on one side at least.
The static feet were two smaller blocks I had as scrap which I cut down to 50mm in height and sanded smooth. Next I drilled about two-thirds of the way through the blocks using a 13mm flat bit and went the rest of the way using a regular 8mm bit - this allowed me to fit shorter screws through the block and into the underside of the table.
The castors were positioned on the 'rear' (the side away from which the table lid opens) of the table and the feet at the 'front'. I acknowledged that this might not be ideal positioning in terms of closing the lid, which takes a firm hand, as force would be transferred to the castors rather than static feet and cause the whole table to slide back, which is what I wanted to avoid. However, assuming that more often than not you would be sat facing the 'front' of the table, it is easier to lift the nearest edge than have to reach over/walk around the table to do so.
In practice this is precisely what happened - the table would slide back when closing the lid unless you placed a foot on the bottom to hold it in place. In conjunction with the castors being utterly useless and disinclined to rotate without jostling the entire table to position them. In short: either moving or keeping the table still was a pain in the backside.
The current set-up was not cutting the mustard, so a better one was required - ideally: perfectly mobile when needed to be and perfectly static the rest of the time. After sketching out a few wholly impractical and increasingly complex ideas on how I might lift and lower the table, I turned to YouTube in hope of some inspiration, eventually stumbling across user Uhlan's video Retractable Landing Gear for My Table Saw...
Step 7: Landing Gear
The landing gear consists of two 450mm lengths of wood each with two castor wheels at their ends which are hinged onto the inside edge of the table. When these wheel bars are horizontal (the lowest point the hinges allow) the wheels are engaged (by stepping on a foot pedal) and raise the table slightly off its feet allowing it to be moved on the castors. A second pedal, located above and inward of the first pedal releases the mechanism and lowers the table back onto its feet.
As the foot operated lever moves downward, it presses onto a shorter (half-length) lever attached to the opposing wheel bar and pointing in the opposite direction. Both levers are slightly off-centre of their respective wheel bars as they run side-by-side, albeit pointing toward one another, so the gap between the levers is the centre line.
A bolt holding two sets of bearings on it is mounted on the underside of the shorter lever (half-way between the two wheel bars) and it is these bearings that the longer bar pushes down on ensuring the wheels lower simultaneously.
When at the lowest (horizontal) position at which the wheels are engaged and the feet lifted, a spring-loaded wooden hook holds the longer foot pedal to the wheel bar on the opposite site meaning that it is not necessary to keep constant pressure on the lever to force the wheels down. The second pedal releases the hook and the weight of the table pushes the castor wheels up until the table feet are firmly on the floor. I added some more contracting springs to the top side of the shorter lever to make sure the wheels are forced up and off the floor as much as possible.
This system was made using some of the remaining bed slats and bolts. The longer lever (with the pedal) consists of two lengths of wood with one overlapping the other to form the foot pedal. I rounded the pedal off with the jigsaw and gave it a thorough sanding to make it more bare foot/sock friendly.
I wanted the hook to be as close to the middle of the wheel bar it would latch onto - strength in symmetry, I figured - so I used the jigsaw to cut a curved section out of the lower section of the lever and half the upper section (which goes onto form the foot pedal) deep enough to allow the hook to sit in flush. This also meant I could have the shorter lever very close to the longer one without interfering with the hook movement.
As I had originally (pre-landing gear) planned to have a lower shelf under the main table, keeping the lifting mechanism as narrow as possible would also leave a decent amount of space to make and fit two storage spaces/shelves on the front and rear of the table.
Step 8: Feet
To replace the original block feet/plastic castor arrangement, I decided to use four adjustable feet. As the landing gear was designed to lift the table only the smallest amount necessary from the floor (to avoid excess bumping or unsettling anything that might be on the table) being able to minutely control the height of the feet would come in very useful.
Threaded feet made the most sense in this respect. They're unobtrusive, easily adjustable, fairly strong and cheap. I decided against mounting them in holes drilled directly in the table as they would have to be long, and therefore susceptible to sideways (I'm sure there's a word for this that has escaped me) stress if the table had force put on it from the sides rather than straight down.
I had some left over M8 T-nuts, so ordered four M8 x ~38mm threaded adjustable feet. Knowing the height the feet needed to hold the table from the floor, 38mm was idea to allow the feet to move up or down as necessary without having to mount them directly to the table base.
Using a flat bit, I drilled four holes a few millimetres deep (deep enough to sink a T-nut into leaving it flush with the top of the wood) into scrap bed slat, which is around 20mm thick. I then took a hole saw (let's say 56mm, for the sake of argument) cut four disks using the centre of the flat bit holes as a guide, before partially widening the holes with 10mm bit (to allow the wider collar of the T-nut to fit) and going the the rest of way through with an 8mm.
Two screw holes were drilled through each disc - either side of the central hole - and into the base of the table. T-nuts were pushed into each of the recesses on the tops of the discs before they were glued and screwed to the table.
Nuts were threaded onto the feet, followed by a wide flange (?) washer before inserting through the wooden discs and finally the T-nut on the other side. Tightening the nut pulled the teeth of the T-nut into the wood, pulling flush with the lip of the recess it sat in. After making sure the feet were an even height with my ruler, self-adhesive cork pads were attached to the bottom of them (the surface of which I had already scored with a Stanley knife) and the table lifted and turned upright.
I tested the landing gear a couple of times to make sure the table lifted far enough from the ground, adjusted the feet slightly as required, and I was done!
Step 9: Finishing Off and Conclusion.
When everything was put together and tested as working, I set about sanding it all over firstly with the power sander (mainly to get the harsh corners off the outside) again and later with finer grit papers by hand. This (and staining) was done before the landing gear made an appearance, so that whole system will need doing at some point.
I was loathe to stain the thing to be honest, and didn't give it nearly as much time or attention as I ought to have done, so I shan't dedicate a step to it. There are much better Instructables for that. I'm not particularly fond of its colour as it stands if I'm honest, though I might remedy that and go darker. My better half (pictured while kindly modelling for me) likes it though, so we'll see what I can be motivated to do. My interested was always the building and practicality of it.
That aside, I'm very happy with the table as it stands - particularly the moving parts and mechanisms. At the very least, it met my initial criteria of being the desired dimensions and looking better than the old one.
With the benefit of hindsight, there are many things I would do differently - perhaps not so much in design - though there is obviously room for improvement - but rather process. A second attempt would see more do things in a more orderly fashion and with more attention to the order in which I did things.
And tools. I hadn't used the jigsaw or power sander in a long time and just dusted them off and got cracking. Until I replaced the blade on the jigsaw (quite far into the project, I might add) I didn't realise that it wasn't just me being rusty and that the original blade was flexing to one side quite severely. The new one was a dream and immediately made everything that bit quicker, neater and easier. Ditto sand paper for the power sander. I just used whatever brand I happened to have and it was only after buying better paper that it hit home what a difference higher quality paper made. So check and maintain your gear, especially if you've not played with it for a while. If you have a circular saw and/or mitre/chop saw, you'll make rapid progress with such a project.
The entire project started around mid-August and is still not fully completed. I get home from work later than I'd like so I try and cram in as much time with my family as possible evenings and weekends, as a consequence the table building was squeezed in when and wherever possible, rarely getting much more than a couple hours in one go. While mildly frustrating at times, I think this was for the best ultimately as I had plenty of time to think about what I would do next or work out mistakes I had made that I might otherwise have hurried and made worse.
There were a couple, relatively minor, things I buggered up such as getting inexplicably carried away and gluing dowel into batons before having drilled the corresponding holes or cutting, drilling and gluing part of the landing gear lever system at completely the wrong height, but nothing irreversible or particularly infuriating.
A good portion of what appealed to me about using pallet wood was that I wouldn't have to obsess over it being perfect in certain areas. Don't get me wrong; I wanted to do the best I could, but making the best of used wood and its idiosyncrasies was quite relaxing as any minor errors would not look as glaring as on something designed to be flawless, if that makes sense. I am tempted to build another - essentially the same - from scratch next year with nice timber, nice joints and focussing more on aesthetics and really build on what I learned from this project.
So for now, I consider what I've made to be a rolling prototype. But one I'm very pleased with and had a lot of fun and satisfaction making.
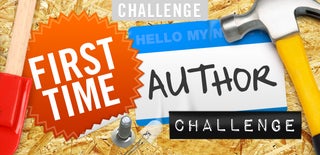
First Prize in the
First Time Author Challenge
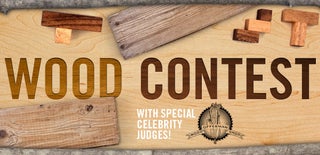
Fourth Prize in the
Wood Contest