Introduction: Low-Cost Standing Workbench - No Screws Needed!
When we upgraded our electronics bench setup, we wanted a new table that was cheap and incredibly easy to assemble (and disassemble / transport for moving).
Our solution? Turn two 4'x8' sheets of 23/32" plywood into a slot-assembly, no-screws-needed project bench, that can be assembled and disassembled in under two minutes. Let's get started!
Like this Instructable? Don't forget to follow us, favorite it, and check us out on Facebook!
Cutting Time: ~3 hours
Assembly Time: 2 minutes
Cost: $65 for plywood, $70 for optional enhancements
Materials:
- Two 4'x8' sheets of 23/32" sanded plywood. If you need to cut it down to transport it (as we did), you can get by with four sheets cut to 24"x74", but it'll be a pretty close cut to the edge.
- Recommended upgrades: 20-outlet, 60" power strip and LED work lighting
Tools:
- Shopbot Alpha CNC cutting machine (we made it at TechShop Pittsburgh)
- 1/4" HSS 2-flute center cutting end mill (>0.75" flute length)
- Brad nailer and plastic brads to nail your parts to the spoilboard
- Dead blow hammer to knock your nailed boards free
Experience:
- Must know how to operate a CNC milling machine (like the ShopBot Alpha)
Step 1: Parts and Toolpaths
We've provided the solidworks parts/assembly, the vector DXF files, and the VCarve Pro project files, so feel free to take them open and have a look at how everything fits together. We didn't include the toolpaths, as those will likely change depending on the dimensions of the board you're cutting and the specs for your mill.
When you're ready, open up your toolpath creator of choice (we used VCarve Pro) and lay out your parts. If you haven't done toolpath creation before, we recommend taking the TechShop CAD/CAM course or looking at some online tutorials to help speed the learning process.
If you're not using the provided VCarve Pro project files and want to work directly from the DXF files, be sure to join the imported vectors and apply dogbone fillets to the corners so that your parts will fit together without sanding. We've attached pictures on the next step showing the dogboned vectors, so match against this to make sure you get every corner.
Our bit was configured as a 1/4" 2-flute HSS end mill, at 12000 RPM, 288 IPM feed rate and with a 30 IPM plunge rate. We used profile toolpaths exclusively, 6 passes with climb milling. Make sure you're milling Outside/Right for the outer perimeter and Inside/Left for all cuts inside the part, or things may not fit together!
Attachments
Step 2: Cutting
The lengthiest part of the project is the CNC work. When cutting out your parts, we recommend the following:
- Leave at least 1" of clearance on all edges of your stock. You can use a brad nailer or jig with these edges to keep your parts from shifting.
- When cutting the legs, table top, and shelf, cut the inside/left paths first, and remove the scraps before cutting the outer profile. This keeps your part from shifting around when cutting the interior.
- We recommend doing an "air cut" (cutting with a Z-zero at least 1" above the top surface of the part) with the outer profiles to make sure you have your part centered the first time.
For a first attempt (such as ours), it'll take a couple hours to get everything cut. Here's the cool part: since you don't need fasteners, you can actually assemble the table as each part comes off the bed, and re-cut or modify parts that don't quite fit while you still have access to your CNC mill.
While the table is assembled, we recommend going around the edges with a sander to remove the burrs and sharp corners. When you're happy with the results, simply follow the assembly steps in reverse and you'll have a few flat parts that you can easily transport to your hack space or evil laboratory.
Step 3: Assembly
Now that you've seen and CNC'ed all of the parts, assembly should be pretty intuitive. If you're ever confused, check out the intro animated image for a quick guide to assembling your new table. This thing literally takes less than two minutes to set up, and requires no fasteners at all.
- Lay one of the long horizontal support pieces on the ground, slots facing up.
- Fit the bottom slot of each side piece to each of the upward facing slots of the horizontal support piece.
- Insert the two triangular rear supports into the slots on the sides of the side pieces. One side of this support piece has its tab closer to the right-angle corner of the triangle; this side should be flush to the side piece.
- Slide the second long horizontal support, tab side down, into the vertical slots of the sides towards the front.
- Slide the table surface in from the front so the leg pieces go into the long slots, then push the table straight down so that the four tab holes receive tabs from the legs and rear triangular supports. The rear supports might take a little fiddling to get them to fit in place.
- Slot the top shelf board into the tabs at the top of the legs.
- Take a step back and bask in the glory of your new project bench!
Step 4: Improvements
We hope you've enjoyed this Instructable, and that you're currently enjoying a sweet DIY plywood standing table. We've found that an all-plywood bench makes mounting power strips and tool hooks a snap; just drill straight through the wood and use a zip tie, or screw it directly to the bench.
After using this table for a few weeks, we found a few upgrades that could take this project to the next level:
- The table surface's slot holes in the sides and back are flush, but they do interrupt the smooth top face. We imagine this could be fixed by shortening the tabs on the side pieces by ~1/4", then using a profile cut for the tab holes that doesn't punch all the way through the material.
- The length and depth of this project table is easily adjustable via Solidworks, so you could modify the parts and get a precise fit for your needs.
- Never underestimate the power of outlets... a 20-outlet, 60" power strip mounted to the rear of the table surface ensures you'll never be lacking for a place to plug in.
- It takes a bit of soldering and a 12V power source, but these bright white LED lights can be mounted underneath the upper shelf to evenly illuminate your work surface.
This project also creates a lot of scrap, particularly when cutting the large rectangular section out of the leg. We're working on an Instructable that'll turn these scraps into something useful, so stay tuned - don't forget to like this Instructable, favorite it, and follow us on Facebook!
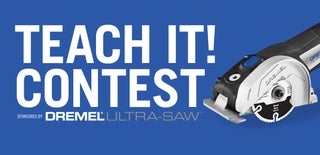
Second Prize in the
Teach It! Contest Sponsored by Dremel
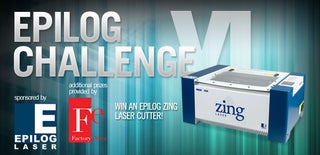
Participated in the
Epilog Challenge VI