Introduction: Make Modular, Pocket-Sized Solar Panels
Have you ever been outside and had your phone die? Have you ever wanted to make your own solar panels for charging a cell phone or electronics project? Now you can!
Each panel costs $1.25 in materials and provides 0 - 0.5V at 400-1000mA depending on load and lighting. The panels are linkable by magnets, and can be reconfigured on the fly to provide different voltages and currents
This is a cheap, portable device that can be used to charge your cell phone when you're camping or on a grassy knoll somewhere.
It is easy for anyone to make, with tools that you might have around the house.
For an alternate guide, check out the project's github page.
Step 1: Tools and Materials
Tools
- Office Laminator
- Scissors
- Ruler
- Non-stick parchment paper (bakery/baking/butter paper)
Materials
- Polycarbonate sheet .01" thick - This will be the rigid, protective layer that surrounds our solar panel. I bought mine from mcmaster.com.
- EVA (Ethylene-Vinyl Acetate) film encapsulant - This should come with a smooth and a bumpy side. It's made as a film for solar panels, and will cushion the cells to keep them from cracking. I found mine with this Ebay search.
- Copper tape with conductive adhesive - It's important to make sure that the adhesive is conductive (most aren't). I found my tape on adafruit.com
- Solar Cells - I recommend 52x76mm multicrystalline or polycrystalline solar cells. These will give us 0.55V open-circuit voltage, and 1A short-circuit current. I found mine with this Ebay search.
- Small neodymium magnets (1/4" x 1/8" x 1/32") - You will need 2 for each panel you want to make. I got mine from KJ Magnetics.
For a price breakdown, see this project's github page on materials.
Disclaimer: Solar cells are extremely thin and crackable. Always handle with care.
Step 2: Cut Sheets to Size
For 52x76mm solar cells, cut your sheets to 65 x 90 mm (6.5 x 9 cm). For each solar panel you plan to make, cut two 65x90mm rectangles of polycarbonate, and two rectangles of EVA.
Step 3: Apply Tape to Front
Cut a strip of copper tape 7cm long. Apply it, sticky side down, on the white line.
Be sure that there is a gap between the end of the tape and the end of the cell (seen here at the bottom of the image)
Step 4: Apply Tape to the Back
Flip the solar cell over. Repeat for the back of the solar cell.
Be sure that there is a gap between the end of the tape and the end of the cell (seen here at the bottom of the solar cell)
Step 5: Place Plastic Backing
Take one piece of polycarbonate and remove both pieces of protective film from the plastic. Remove the protective paper from one EVA sheet. Put a sheet of EVA exactly on top of the polycarbonate with the bumps facing up. Then place the solar cell assembly on top of that.
Carefully position the solar cell to be in the center on top of the polycarbonate/EVA sheets.
Step 6: Place Plastic Fronting
Remove the backings from the remaining polycarbonate and EVA sheets.
Now place an EVA sheet with the bumps facing down on the assembly. Place the remaining polycarbonate sheet on top of the EVA.
Step 7: Laminate Your Solar Panel
Check that your solar panel is in this order from bottom to top: polycarbonate, EVA (bumps up), solar cell, EVA (bumps down), polycarbonate. Also make sure that your copper tape is sticking straight out of both sides of the panel.
Place the assembly between pieces of parchment paper to keep the laminator's rollers clean from melted EVA, and copper tape adhesive.
Without disturbing the position of the solar cell in the assembly, carefully put the assembly into the laminator in the direction shown.
Step 8: Preparing the Magnets
When working with these magnets it's important for them to be the right direction. Mark one side of a magnet. Now do it on the rest, so that when you stick two magnets together, the marked side always attracts the blank side.
Step 9: Add Magnet to the Front
Put a magnet with the marked side facing up on the panel as shown here.
Now fold the copper tape over. Make sure it tightly contours to the 90 degree angles of the magnet.
Step 10: Add a Magnet to the Back
Now turn the panel over and add another magnet where shown. This magnet should have the marked side facing down.
Now fold the copper tape over. Make sure it tightly contours to the 90 degree angles of the magnet.
Step 11: Check Your New Solar Panel
If you have a multimeter, check the voltage and current output of your new solar panel. Make sure there is a bright light shining on your solar panel. It should have a voltage of 0.55V, and a current between 0.4A and 1.0A depending on how bright your light is.
Step 12: Stack Your New Solar Panels
Because of the design, these solar panels can be stacked for easy transportation. Your panels are approximately the size of a deck of trading cards. I bought this card carrying case at tap plastics.
Step 13: Powering Electronics
If you want to charge your cell phone at 5V with USB, you have a number of options:
With 6-12 panels (3-6V) you can use a board like the Minty Boost or another 3V to 5V boost converter to charge your phone.
With 12 panels (6V), you can use Adafruit's solar lithium polymer charger to very efficiently charge a battery and your phone (may need a 5V LDO Linear Regulator).
With 12-46 panels(6V-23V), you can use a buck converter and my other guide to efficiently charge your devices.
You can run an Arduino by wiring the positive and negative leads of 12 solar panels in series into the barrel-jack of the Arduino.
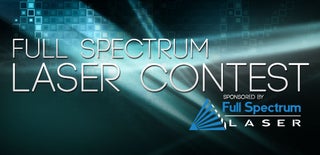
Participated in the
Full Spectrum Laser Contest
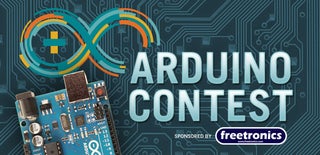
Participated in the
Arduino Contest