Introduction: Make Your Own DIY CNC
This instructable outlines the assembly process of my 2nd generation CNC machine which I designed to be simple to build and quiet enough to be apartment friendly. I have included example projects that I have made in the first two weeks of using the machine to demonstrate its capabilities.
This is the second CNC machine that I have designed and built. My first machine was based off of oomlout’s instructable “How to make a Three Axis CNC Machine (Cheaply and Easily)” (by far my favorite instructable and the one that got me hooked on the site). It was moderately successful, cutting a number of parts from foam (a summary of parts made can be found on my abandoned blog here along with some build photos). The lack of overall stiffness and play in the linear mechanisms meant that plywood and plastics could not be cut effectively. The biggest downfall of the machine was the difficulty to setup and square the axes and lacked the ability to make fine adjustments once set up. The drive pulleys were sandwiched between the gantry sides and if a pulley loosened the entire gantry structure had to be disassembled and put back together and squared all over again (a couple evenings of work).
In reviewing published designs for a 2nd generation machine I revisited Joe’s CNC, a popular design but I questioned my ability to produce so many duplicate parts with enough accuracy. I came across buildyourcnc.com and their blueChick design . What caught my attention was their use of V-groove bearings and how it simplified the design and the ease of aligning the axes. I had previously discounted V-groove bearings due to their cost ($150/ set vs. $12 for skate bearings) but after my first build I had enough experience to fully understand their benefits and to realize they were well worth the investment. The blueChick was simpler than the Joe’s CNC design but was still a bit too intricate for my tastes so I set out to design a new machine based off of the new bearings. I came up with a new design with three main design features that solved shortcomings of my first machine:
1) All of the drive mechanics are exposed. If anything requires adjustment or tightening you can walk up with an Allen key, screw driver or wrench and access everything allowing the machine to be up and running again in a matter of minutes. The axes are easy to setup with the V-groove bearings and can be micro adjusted once installed.
2) The design has a low number of fabricated components and allows for low build tolerances. The precision is based off of the flatness of the plywood and the straightness of the aluminum extrusions. All of the fabricated components can be roughly cut (except two edges detailed in Step 3) and all holes are oversized to allow for slight inaccuracies in drilling. This allows for any inaccuracies in the building stage to be taken up during assembly without loosing any precision.
3) Low operational noise. The machine had to be quiet enough to use in an apartment or I couldn't use it. The rotary tool I used on my last machine worked well but when running at 20k rpm, it screamed too loudly for me to use in my new home. A custom spindle was built as a low noise solution with negligible reduction in performance.
Step 1: Terminology & Specs
The overall specs of the machine are as follows:
Cutting volume 22 1/2" x 18 1/4" x 2 1/4"
Axis drives:
X&Y: MXL timing belts w/ 40 groove pulley (pitch dia 1.019") maximum resolution 0.004 inch at 1/4 micro stepping
Z: 1/4" threaded rod. Theoretical resolution 0.00006 inches at 1/4 micro stepping
All axes powered by 130 oz-in stepper motors.
Cutting speed/depth are dependant on the material being cut and are limited by home made spindle power and router bit.
The terminology for the different components as I will refer to them is shown in the picture. I have the X&Y axes oriented as shown so that when sitting in front of the machine, the axes match a 3D CAD drawing as seen in a top view (X axis horizontal, Y vertical and Z out of the page/screen).
Step 2: Bill of Materials
Attached is a breakdown of the components and the cost of the machine. The hardware and aluminium were purchased in batches from local home improvement stores as a matter of convenience as the design progressed and those prices are shown. With a complete bill of materials these could be sourced from dedicated metal and fastener suppliers at a significant discount. All prices are in Canadian dollars; these items will be much cheaper off of the same shelves for my neighbours down in the US. Even though Canada is a metric country, all stock sizes of lumber, metals and hardware are imperial with a hefty mark-up on metric components if they are even available. Because of this all components are imperial sizes other than the plywood (I'd never seen metric plywood in a home improvement store before, which is probably why it was half the price of imperial stock of similar thickness).
The overall cost of the machine was above what I was expecting when I started my first machine but these costs have been spread out over the four years I have been working on the project. A comparison to entry level commercial products on the market shows that the DIY route is still a cheaper way to go. While these machines may have better performance than a home built wood framed design, there is no replacing the satisfaction of making a machine yourself. I am also unsure how flexible these are for running different driver software and overall flexibility on how you can use the machines.
ShopBot Desktop $4995 + Taxes + S&H + spindle
Laguana Swift $4900 + Taxes + S&H
Rockler CNC Shark Pro Plus $3800 + Taxes + S&H + spindle
General International i-Carver $2100 + Taxes
Lumenlab's M3 kit looks like a nice product but at $999+ S&H + software + driver the overall price will be over $1500 to get it up and running.
A note on designs titled CNC for less than $XXX dollars (usually under $200). There will always be a trade off between performance and price. Machines with very little forces on the tool can be made very cheaply (for drawing, cutting foam and 3d printing) but when cutting harder materials things have to be beefed up. These aren't bad machines but be clear with what you're building so you're not disappointed when the thing folds in half when it comes to cutting plywood. These prices also skip over several key parts, only including the major components in the price. Its amazing to see how quickly some 1/4" and 3/8" bolts add up and they certainly don't include software (or count trial versions as a permanent solution) and driver boards. Without these your $150 CNC is just an overkill paperweight.
BOM Summary:
Plywood & Metals: $158.25
Hardware: $107.77
Drive Line Components $261.46
Electronics $442.04
Software $522.26
Miscellaneous $11.19
Grand Total $1502.96
Step 3: Fabricated Parts
The list of fabricated parts required are as follows sorted by material. Attached at the bottom of the page are drawings for all the parts in pdf format.
18mm Plywood
-Base
-Gantry Side Right
-Gantry Side Left
-Gantry Assembly
-Trolley
1" x 1/8" Aluminum Flat
-2x Y rail
-2x Y rail angle
-Top X rail
-Bottom X rail
-2x Z-rail
3/4"x 1/8" Steel Flat
-4x Belt clamp
MDF
-Bearing block
-Stepper motor plate
3/8" Ply
-Spindle motor plate
-2x Spindle bearing clamp
-Z-axis bearing clamp
1 1/2" x 1 1/2" x 1/8" Aluminum Angle
-Stepper motor bracket
-Top spindle bracket
-Spindle motor bracket
-Bottom spindle bracket
The parts have been design to be as simple as possible to produce. I cut out everything using a jigsaw, drill press, disk sander and hacksaw. The disk sander greatly simplified the process as I was able to rough cut the parts using my jigsaw and sand to the line giving a very accurate and clean edge. As well as being as simple as possible the parts have been designed to allow for inaccuracies in manufacturing with all holes being oversized to take up any misalignment. The only part which needs to be made with a great amount of care is the Gantry Assembly. Once the pieces are cut and glued together the edges must be perfectly square to the front face or the machine will not be square. Using a disk sander made this easy to do as I held the front face flush against a miter gauge and sanded the edge until square. If you don't have a disk sander the edges will have to be squared using sandpaper or a block plane until true which will take longer but is feasible.
Unfortunately I do not have any pictures of the parts being cut as I wasn't thinking of making an Instructable at the time. A keen eye will be able to see that these parts have already been assembled. Assembling the machine the first time I ran into some unexpected interference issues. For example the location of the V-groove bearings for the Z-axis as well as the location of the anti backlash nut had to be modified leading to the trolley looking a lot like swish cheese in the end. The drawings attached show the modified hole locations and won't have as many holes as the parts shown in the photos.
Step 4: Base Assembly
Fabricated parts required:
Plywood base
2x Y-Rail
2x Y-Rail Angle
4x Belt Clamps
Hardware required:
8x 8-32 x ½ machine screw
6x 8-32 x 1 ¼ machine screw
28x #8 washer
14x 8-32 nut
8x 1” ¼” dia hex bolt
8x ¼” cross nut
25x ¼” x 11mm threaded insert
The base is the foundation of the machine and must provide a flat and stable support to mount the work piece and support the linear rails. 18mm birch ply was chosen to form the base as it was available at an affordable price, is easy to machine and can be expected to resist seasonal expansion and warping. Another benefit to using ply is that the overall dimensions aren’t limited by the material sizes available. I had an old children’s play table on hand that I used to support the base. The width of the machine (X axis) is such that the linear rails overhang the sides to have clearance on the underside. I do not have access to a table saw so the overhang was important as constructing a flat torsion box to provide adequate elevation would have been difficult. The length (Y axis) of the base was driven by the length of the timing belts I had purchased. The length of the base is determined to be the belt length plus the reach of the eye bolts less the length of the loop around the drive pulley (See Step 13).
The dimensions of the machine are not optimum for standard lengths of aluminum extrusions found at home centers (36”, 48” and 72”). By using different timing belts the machine could be redesigned to have rail lengths of 24” or 36” to use these materials more efficiently.
4.1 The first step is to find an adequate support for the machine. If a similar set up like mine with an overhang is not used, the base will have to be built up to provide 2" of clearance underneath the rails, measured from the top surface of the base. The best way to do this would be with a torsion box construction to provide the most ridged surface possible (http://www.thewoodwhisperer.com/videos/episode-18-assembly-table-torsion-box/) a simpler option would be to simply stack sheets of ply narrower than the base underneath.
4.2 Once the base is located on a suitable surface the Y rails can come together. Each Y rail and Y rail angle are attached using a 8-32 x ½” Machine screw, two washers and a nut in each of the 4 holes. The height of the rail was set by placing an offcut of the 1/8” aluminum flat bar on each end of the angle and bringing the flat flush with the top surface (photo #4) and then tightening the screws. These screws should be tightened securely to ensure the rail does not slip. The exact height of the rail isn't critical as long as it is greater than 1/16" to give the V-groove bearing clearance to sit on the edge of the flat bar and that the spacing is consistent down the length of the rail and between the two rails.
The photo #5 shows the finished cross section of the rail and #6 shows the entire rail.
4.3 With the rails assembled they can be attached to the base. This is done using three 8-32 x 1 ¼” machine screws per rail and two washers and a nut per screw (photo #7). Only tighten the nuts loosely so that the rail remains free to move over the base, these will be tightened in step 6.5 when it comes to matching the rail separation with the width of the gantry.
4.4 The belt clamps are to be attached next. There’s nothing fancy about putting the supports on, two 2 ¼” x 1” hex bolts into two cross nuts per corner, see photos #8 and #9 for all the information you’ll need. Make sure the tops are flush or below the base top so that oversized stock can be mounted overhanging the base. The hex bolts only have to be put on finger tight as the tension of the belt will provide preload. (***NOTE I have included this step here as they are related to the base, but leave them off until you install the gantry sides, otherwise you’ll just have to take one off per side to get the v-groove bearings onto the rails in step 5.3)
4.5 The final step in assembling the base is installing the threaded inserts for clamping down the work piece. These were chosen as they are simple to install. A couple routed dados in the base with t-channels would provide more flexibility for clamping but would add build complexity which as mentioned previously was avoided in the design. Be careful installing these as they can pull up the surface of the plywood making the surface uneven. The chamfers on these holes go a long way to prevent this so don’t skip these.
With the Y rails, belt supports and threaded inserts in place the base is complete and ready to support the gantry.
Step 5: Gantry Side Assembly
Fabricated parts required:
1x Gantry Side Left
1x Gantry Side Right
8x modified 5/16” washers
Hardware required:
8x 3/8 V-groove bearings
8x 3/8” washers
8x 3/8” nut
3/8” x 2” hex bolt
4x 8mm skate bearings
4x 5/16” x 1 ¼” hex bolt
4x 5/16” washer
8x ¼” washer
4x 5/16” nut
2x ¼” cross nut
2x ¼” x 1 ½” hex bolt
To build the gantry we will start with the sides that run along the Y rails. In this step we’ll see how amazing the v-groove bearings are and how easily they make the assembly process.
The gantry sides are similar but with differences between left and right for the idler bearing counter bores and limit switch counter bores. The limit switch counter bores are on the outside of the ends when installed and the idler bearing counter bores are on the inside. The features for the stepper motor mount are repeated on both side so that the stepper is reversible should you want to install it on the other side for whatever reason.
5.1 The 3/8” V-groove bearings are installed using the hardware shown in photo #3 with the 3/8” washer on the outside and a modified 5/16” washer on the inside. A modified 5/16” washer is a 5/16” washer bored to an ID of 3/8”. This is done because a regular 3/8” washer will rub against both the inner and outer races of the bearing but the OD of the 5/16” washer is such that only the inner race is supported allowing the bearing to spin. Tighten the top bearings securely but keep the bottom ones loose for now. The bolts should be tight enough that the bearings won’t shift under a reasonable amount of force, but don’t tighten them up so tight that the washers crush the plywood beneath them. The consequences of this are outlined in Note 2 later on.
5.2 Next item to install is the 8mm idler bearings for the timing belt. These have a 5/16” washer on the inside in the counter bore, and two ¼” washers on the outside to provide the required standoff. ¼” washers are used for the same reason as the modified 5/16” washers for the v-groove bearings. Photos #4,5,6,7 shows the setup.
5.3 The v-groove bearings can now be tightened against the rails. Start by sliding the bearings over the rails (Photo #9), hopefully you followed the note in step 4.4 and held off from putting on the belt supports, if not, remove one per side to get the bearings over the rails. The top bearings are already tightened so only the four bottom ones required attention. I don’t have any pictures of this step as it requires both hands to do. For each set of top and bottom bearings, squeeze the bearings together with your fingers while tightening the bolt. I wrapped the bearings in a towel as you’ll want to squeeze them together as tight as possible but they have rather sharp edges. Once you have completed this step for both bearings per side you should be able to grab the gantry side and twist it every which way without any noticeable play (hold down the rail when you test this as they should still be loose; we’ll get to tightening them up at the end of this step).
Note 1:
Up to this point everything should have gone together smoothly as long as the holes have been drilled within 1/16” of their indicated positions which should be do-able even with hand tools (its been designed to be forgiving like that).
There is a chance that you won’t be able to get enough separation between the bearings to get them on the aluminum flat if the holes haven’t been located within the specified tolerance. If this happens, re-tighten the top bearings making them sit as high up in the holes as possible and retry the assembly. If this still doesn’t solve the problem the bottom holes will have to be re-bored to a larger size. These holes haven’t been given the same amount of wiggle room as the others to keep as much material as possible under the washers to prevent crushing.
Note 2:
I have not mentioned aligning the gantry side to the vertical during this step (when I say vertical I mean when viewed from the side. With the bearings tight around the rail the gantry side will automatically align itself to be vertical to the base when viewed from the front. If it is not, the most likely culprit would be a washer that has crushed the plywood around it from tightening the bolt far too much. If this has happened you should remake the gantry side as it will be close to impossible to get all the bearings lined up in the same plane.) If the top bearing holes are drilled in line with each other and the bolts are registered on the same face (top or bottom of the hole) then the gantry side will sit within a degree or two from vertical. Any misalignment (angular and height above the base) will be taken up in the connection of the gantry side with the gantry assembly. Having this flexibility in the design later on allows for you to focus on getting one pair of bearings tight around the rail at a time instead of worrying about multiple things at once.
5.4 The last item for the gantry sides are the limit switch “bumpers” that trigger the limit switches. Shown in Photos #10 & 11 they only go on the side the limit switches are on and can be modified in length by using a different length of hex bolt. Tighten these by hand until the end of the bolt bottoms out on the plywood pushing against the cross nut. Do not use a wrench on these as you can easily over tighten and crush the plywood. The belt supports can finally be installed as per step 4.4 so go ahead and put them on now.
Step 6: Gantry Assembly
Fabricated parts required:
1x Gantry Assembly
1x X rail Top
1x X rail Bottom
Hardware required:
6x ¼” x 2 ¼” hex bolt
6x ¼” washer
6x ¼” cross nut
8x 8-32 x 1 ¼” machine screw
8x 8-32 nut
16x #8 washer
Once you’ve built the Gantry assembly you’ve already finished the hardest part of this step. The squareness and stiffness of the machine depends on how square the gantry assembly ends are. Take the time to double check these before proceeding.
6.1 Take the gantry assembly and loosely attach it with the ¼” bolts and cross nuts (6 of each) using a ¼” washer underneath the bolt head. Photos #1,2&3 show all the bits and pieces.
6.2 With the gantry assembly loosely in place, tighten the three 8-32 machine screws on one of the Y rails to lock it in place. Try to get the rail so that the bolts are roughly centered in their holes and the rail is parallel to the base side.
6.3 With one of the rails locked down, tighten the three ¼” hex bolts on that side. While you tighten the bolts, hold a square up to the front face of the gantry assembly to keep it square to the base and line up the bottom to be around 4" from the base (Photo #7). The actual distance you can get from the base surface will depend on the how the v-grove bearings were installed but shouldn’t be out by more than an eighth of an inch. The height isn’t terribly important but being square to the base is, focus on that when tightening the bolts.
6.4 You can now tighten the three ¼” hex bolts on the other side. Tighten the bolts evenly not one at once keeping an eye on how the gantry assembly comes together with the gantry side. Similar problems may be encountered as covered by Note 1 of Step 5. If everything goes together nicely there will be no gaps as in Photo #6 when the bolts are tightened loosely. Four issues in alignment could be encountered:
1) A gap anywhere and with the rails parallel to one another and the gantry sides vertical when viewed from the front is a sign that the gantry assembly sides aren’t square and flat.
2) A gap at the top bolt and with the gantry side leaning outwards when viewed from the front is a sign that the rails aren’t able to distance themselves far enough apart.
3) A gap at the bottom bolt and with the gantry side leaning inwards when viewed from the front is a sign that the rails aren’t able to distance themselves close enough together.
4) A gap at the middle/ back bolt and with the rails not parallel to one another when viewed from above is a sign that the gantry assembly ends aren’t square.
Issues 1 & 4 require modifications to the gantry assembly. Issues 2&3 may be resolved by adjusting the rail that was tightened down in step 6.2 In the case of #2, loosen the rail and retighten as far out as possible, or as far in as possible in the case of #3. Should this adjustment not be enough measure the distance between holes in the base and the length of the gantry assembly; drill the holes in the base larger to give more flexibility or reduce the length of the gantry assembly as required.
6.5 Once the gantry assembly is square and all six bolts are tightened, slide the gantry (now the gantry sides and gantry assembly are all attached I will simply refer to it as the gantry) to one end of the base. Side it back and forth an inch or two to make sure the rail has moved to the proper distance from the other rail and everything is smooth. Once you’re happy with it tighten the 8-32 machine screw on that end to tighten the second rail. Slide the gantry down to the other end and repeat the process of sliding the gantry back and forth. Tighten the middle machine screw and then the end one.
At this point both Y rails should be secured to the base, the front face of the gantry square to the base and the gantry free to slide the length of the rails with no play nor binding.
This process has come across as laborious and tedious but I had no problems assembling things on the first go which took under five minutes. Hopefully my success will be repeatable and if not the details provided will be enough to trouble shoot any problems.
6.6 Moving on to the X axis rails, attach the aluminum flats using washers on both sides and tightening finger tight. I put together a quick height gauge using a square of scrap of wood and a C-clamp to position the lower rail (Photo #10). Clamp the wood to a height that supports the aluminum rail with 1/8" clearance from the bottom of the Gantry (required to give the V-groove bearings room to seat). With the rail supported on the wood at one end, tighten the end machine screw. When tightening, try to keep the rail level, more on this in a second. Move to the other side and support the bottom rail on the wood and tighten.
If the rail was perfectly level after you tightened the first screw you will be done, however, if there was any misalignment, the rail would have rotated around the screw that was tightened first when you adjusted it at the other end and will not be even along its length. Go back and forth leveling it out, slowly honing in on making it snug against the wood block along the whole length. This took me 2-3 iterations to achieve. Make sure the wood block doesn’t shift while doing this! Really I should have used two C-clamps to hold it in place to stop it sliding down.
Take your time on this step to get it right. If the rail isn’t a consistent height along its length, your cutting tool will not run at a consistent height over the work piece. Once things are set up right, tighten the two inner bolts.
6.7 Once you’re happy with the bottom rail, set the top rail parallel to the bottom. The bottom rail is our datum and the top rail needs to be a consistent distance apart. If the distance isn’t consistent, the trolley will be smooth running without play in the middle, will have excessive play on one end and will bind on the other. I used a pair of digital calipers locked to the required length as a measuring tool. These are not necessary and are overkill, a trammel or a ruler with two pieces of wood clamped to it similar to that used previously will be more than adequate for the task. As usual, position the upper surface of the rail to be 1/8" inches clear of the top of the gantry to provide clearance for the V-groove bearing. The distance between rails is just shy of 5 ¼” (Note: I am doing a terrible job of measuring the distance in Photo #11, the edges of the rails should be an equal distance from the tips of the calipers). Adjust the height of the rail as in step 6.6 until consistent along the entire length.
Step 7: Y Axis Drive Train
Fabricated parts required:
Bearing block
¼” steel rod
Hardware Required:
Stepper motor
2x MXL timing belt pulley
¼” to ¼” spider coupling
¼” ID skate bearing
¼” shaft collar
3x 8-32 x 2” machine screw
3x 8-32 x 1 ¼” machine screw
9x #8 washer
6x #8 nut
This is my favorite step as it uses the fewest and most basic fabricated components, is simple to complete and gives you a sense of achievement without doing a whole lot.
7.1 Start by attaching one of the timing belt pulleys to the front shaft of the stepper motor. Dry fit the stepper to get the position of the pulley right so that it protrudes out the side and lines up with the idler bearings below (Photo #16).
Note: For all shaft accessories, line up the set screw with the flat on the shaft when tightening.
Design Note: The timing belt pulleys I purchased have annoyingly small set screws for a ¼” shaft, half the size of those on the ¼” shaft collar. When I initially assembled this machine and ran through the trials I found that if the machine had a catch the timing pulleys would come loose from the shafts. I was happy to see this as the failure mode as when something goes wrong something has to give and having to retighten a pair of set screw whenever I have an accident is far better than having to remake a component that bent or broke. The pulley on the far side of the stepper motor is exposed and you can just walk up with an Allen key to tighten it (after all, that was the point of this design) however the set screw on the stepper motor side is tucked away in the gantry side. Tightening this required removing the stepper motor and dismantling the shaft. To avoid taking the machine apart every time the tool catches I chose to install the pulley with some auto body filler on the flat of the shaft to prevent the pulley from coming loose (Photo #3). I kept the pulley on the other side as-is to act as the weakest link in the system and maintain the fail safe design.
7.2 Bolt the stepper motor onto the inside of one of the gantry sides (Photos #4-7). The face of the stepper will register snuggly in the 1 ½” hole. You only need three bolts to keep the motor in place saving you the trouble of getting into the upper corner with a screw driver to tighten the fourth one up. Washers are only required on the outer surface against the plywood.
7.3 Next position the bearing block on the opposite side (Photos #8,9). Measure the height of the stepper motor shaft from the base and try to get the center of the bearing block hole to match, Within 1/16” to 1/32” is good enough here. Use three 8-32 bolts to bolt it in place with washers on both sides. I used 2” bolts but 1 ½” would be ideal but I didn’t not have any on hand. The overhang from the 2” bolts does not cause an interference issues and is purely aesthetic. I may cut these down to size later if they still bother me down the road.
7.4 Attach the spider coupling to the back shaft of the stepper motor (Photo #10 &11).
7.5 With the ¼” ID skate bearing and ¼” shaft collar on the steel shaft, feed one end through the bearing block and one into the spider coupling. Tighten the setscrew on the spider coupling (Photo #12).
7.6 Slide the bearing into the recess in the bearing block and tighten the shaft coupling while pressing it into the bearing. (Photos #13,14).
7.7 The final step is to attach the second pulley on the steel shaft. Line up with the idle pulleys below (Photos #15,16).
Design note:
This arrangement works but can be improved. When the timing belts are highly tensioned they pull down on the pulleys. The pulley on the stepper motor side is very secure and does not deflect, but on the far side the bearing in the bearing block holds but the steel rod bows with up to an eighth of an inch deflection in the middle of its span. This can be counteracted in two ways, either installing another bearing block in the middle of the span or making the existing bearing block deeper so that it can hold two bearings.
Step 8: Trolley Assembly
Fabricated parts required:
Trolley
4x 5/16” modified washers
Hardware required:
MXL timing belt pulley
Stepper motor
4x #8-32 x 2 ½ machine screw
30x #8 washer
12x #8 nut
2x ¼” ID skate bearing
10x ¼” washer
2x ¼” x 1 ½” hex bolt
2x ¼” nut
4x 3/8” V-groove bearing
4x 3/8” washer
4x 3/8” nut
4x 3/8” x 2” hex bolt
4x 3/16” V-groove bearing
4x 3/16” x 1 ½” stove bolt
4x 3/16” nut
8x 5/16” washer
3x 10-24 x 4” stove bolt
6x 10-24 nut
The trolley piece I am using has been modified a few times to fix interference issues. There are seven extra holes where the 3/16” bearings and the anti backlash supports had to be relocated.
8.1 Attach the timing belt pulley to the stepper motor’s front shaft. Orient with the collar facing the motor and approximately 1/16” from the face plate.
8.2 Attach four 2” machine screws to the motor mounting holes with washers against the faceplate
8.3 Thread on a #8 nut and a washer to each machine screw.
8.4 Feed the machine screws through the mounting holes on the trolley.
8.5 Thread a #8 nut on each machine screw with a washer between the nut and the trolley. Adjust so that the nut face is flush with the end of the machine screw.
8.6 Tighten the middle nuts against the trolley to clamp the motor in place. The stepper motor is now fixed parallel to and offset from the trolley face. Photos #3&4
8.7 Install the ¼” idler bearings by stacking four ¼” washers and a ¼” skate bearing on the stepper motor side and sliding a ¼” x 1 ½” hex bolt with washer through the mounting hole on the trolley. Carefully slide a nut over the end of the bolt and tighten. The four ¼” washers bring the bearings into the same plane as the pulley which will eventually line up in plane with the X rail and timing belt. Photos #5&6
8.8 Mount the 3/8” V-groove bearings as done previously with the bearing and modified 5/16” washer on the stepper motor side and the 3/8” washer on the side of the bolt head. Tighten the top two bearings and leave the bottom two loose. Photos #7-9
8.9 Mount the 3/16” V-groove bearings by stacking a 5/16” washer, three #8 washers and the bearing on the front face of the trolley with a 5/16” washer under the nut on the stepper motor side. The goal is to have all four bearings offset the same distance from the trolley face. To achieve this use washers from the same box/batch and inspect them for imperfections that prevent them from sitting flat. The 5/16” washers are used as I had issues with crushing of the plywood when I first assembled the trolley. Photos #10-13
8.10 The final step until the sled is completed is to attach the anti backlash supports. These are bolted to the trolley as shown in Photos #14-16.
Step 9: Spindle Assembly
My custom spindle is made from an AC motor pulled from an old vacuum cleaner power head and parts from a rotary tool. The donor tool was the cheapest one I could find and was picked up for $10 on sale (Photos #1,2). Opening it up (Photo #3) you can see all the bits we're after: the spindle with shaft, bearings and collet and a nice speed control circuit on its own board. The parts not used are the plastic case, the brushes and field windings.
The spindle assembly has the commutator, laminated rotor core and cooling fan all built onto the shaft (Photo #4). The plastic cooling fan and the commutator came off easily using another rotary tool with a cut off disk but the rotor core was significantly more difficult. The alternating layers of iron laminations and varnish were bomb proof and I burnt through five cut off disks without making more than scratches on the surface. Using a hammer and chisel I managed chip away at the iron laminations layer by layer and got everything off (Photo # 8). Don't use a good chisel for this job, mine had large chunks removed from the cutting edge when I was done and required significant grinding to get a new edge.
Step 10: Sled Assembly Pt 1/2
Fabricated Parts Required:
1x Sled
1x Bottom spindle bracket
1x Spindle motor bracket
1x Top spindle bracket
1x Stepper motor bracket
1x Stepper motor plate
3x Bearing clamp
1x Spindle motor plate
1x Spindle
2x Z-axis rails
Auto body filler
1x shaft coupling
1x Z-axis drive rod
Hardware Required:
1x stepper motor
13x 8-32 x 1" machine screw
1x 8-32 x 1 1/4" machine screw
20x 8-32 nut
29x #8 washer
6x 8-32 x 3/4" machine screw
2x 6-32 x 1/2" machine screw
2x 6-32 nut
1x elastic band
1x Spindle Motor
2x set screws
1x 1/4" ID skate bearing
2x 1/4" nut
Building the sled and the custom spindle has a lot to it so I have broken it out into two parts. Part one with cover installing the components and part two covers making the belt pulleys, run-out and making a shaft coupling. All photos show the motor and spindle having pulleys made from auto body filler. This was from the first assembly of the machine and shouldn't have been done at this stage. They are made in the first parts of Step 11. Finding a small flat belt the right size to drive the spindle was difficult. Local stores didn't have anything sutable and I didn't want to go to the hassle and expense of purchasing one online. I tried to make one from a larger belt by cutting it to length and splicing it together but the join was too weak. At the grocery store one day I noticed the heavy duty elastic bands around bunches of broccoli and thought it would make the perfect belt. This turned out to be the right length and and has held up well so far.
10.1 Take the sled and put #8 washers in the counter bores on the back side. Photo #8
10.2 Install the Bottom spindle bracket with two 8-32 x 1" machine screws, washers and nuts. Photo #9. When installing the AL brackets, keep one edge a set distance from the edge of the sled so that they are all parallel and in line as shown in Photo #14.
10.3 Attach the motor to the motor plate using the mounting screws that held the motor to the part it was taken off of. You won't have the pulley on yet as shown in Photo #10. I salvaged this motor from an old vacuum power head but have also seen the same unit in a new paper shredder. They seem to be a generic item and a little digging should turn one up.
10.4 Attach the motor plate to the Spindle motor bracket using two 8-32 x 3/4" machine screws, washers and nuts. Photo #12
10.4 Attach the motor bracket to the sled using 8-32 x 1" machine screws. The spindle, elastic band and spindle bearing clamp all have to be assembled at this stage. The arrangement should look like Photo # 13. The bearing clamp has a 6-32 x 1/2" machine screw to secure the bearing with two #8 washers. The clamp is attached to the Bottom spindle bracket using two 8-32 x 1" machine screws, washers and nuts.
10.5 Attach a bearing clamp to the Top spindle bracket and attach the bracket to the sled with two 8-32 x 1" machine screws, washers and nuts. Photo #14.
10.6 Tighten the 6-32 machine screws on the bearing clamps to lock the spindle in place. Check that the spindle axis is parallel with the edge of the sled and square to the front face, adjusting if necessary.
Step 11: Sled Assembly Pt 2/2
Continued from Step 10
11.1 Apply auto body filler to the motor shaft and to the spindle in line with the motor shaft. This is best done in three or four layers or the weight of the filler will make it sag before it hardens. The elastic band cannot be removed but can be pulled out of the way. Photo #1
11.2 The pulley on the motor shaft was shaped by wiring up the motor and holding a sanding block up to it while the motor turned. The pulley should be shaped with a gentle crown to allow the belt to self centre while running. The pulley diameter is around 3/8" but would be better being the same diameter as that on the spindle (3/4") to run at a 1:1 ratio. Photo #2
11.3 To shape the pulley on the spindle I coupled the spindle to the flex shaft of another rotary tool using a piece of 1/8" rod and clamping both to the bench (Photo #3). The photo doesn't show the assembly at the same level of construction as this photo was taken the first time I assembled the machine. The pulley should be around 3/4" in diameter to have a good amount of surface contact with the belt to prevent slipping. As with the motor shaft a slight crown should be included to help tracking. Photo #4 shows the belt around the two pulleys.
Rotating the spindle by hand I was disappointed to see more run-out that I expected. Setting up a dial indicator I measured the run-out at the cutting bit to be 8 thousandths of an inch (Photo #5) and 6 thousandths at the collet (Photo #6). I hadn't taken any measurements of the tool as it came out of the box but being a cheap tool I expect this was how it came and not caused from the abuse of chiselling off the rotor. To get a baseline I measured my other rotary tool (Photo #7) and found the run-out to be 4 thousandths at the cutting bit on the tool itself and a comparable 6 thousandths when using the flex shaft. Doing a google search I found this site covering the same problem. Using the advice to only tighten the collet finger tight I found I could reduce the runout to a workable level.
11.4 The Z-axis rails (Photo #9) and stepper motor bracket can be installed next. The rails are attached at the bottom using 8-32 screws in the dedicated holes. At the top, the rails and stepper motor bracket are attached using the same holes in the sled (Photo #10,11). The aluminium brackets should have been positions parallel to one of the edges of the sled. The Z-axis rail should be offset from the same edge using the method used in step 4.2 using an off cut of aluminium extrusion. The other rail was positioned about 1/8" off the far edge using the same method as step 6.7
11.5 The stepper motor plate, stepper motor, Z-axis drive rod and bearing clamp can all be attached to complete the assembly (Photo #12). The stepper motor and stepper motor plate are attached to the bracket using three 8-32 x 3/4 screws and one 1 1/4". The longer screw goes on the back right corner of the stepper. A 3/4" screw needs to be used on the other back corner of the stepper motor to avoid interference with the nut attaching the Z-axis rail to the sled. The bearing clamp is attached to the bracket with a single 8x32 x 3/4" screw. Two 1/4" nuts are sinched together flush with the top of the inner bearing race.
The 1/4"x1/4" shaft coupler was custom made using recycled HPDE from milk jugs using the following sub steps.
11.5.1 Form a cylinder of HDPE. Photo #13,14. The method of forming the material is detailed in Step 21. A tomato paste can was used as a mould.
11.5.2 Mount the cylinder on a wood lathe using a scroll chuck. Photo #15
11.5.3 Turn the stock down to the desired diameter. Photo #16
11.5.4 Bore a 1/4" hole. Photo #17
11.5.5 Drill two holes to the set screw minor diameter. Photo #18
11.5.6 Tap the holes and the part is ready for set screw and assembly. Photo #18
If you don't have a wood lathe with a scroll chuck or you don't want to be melting milk jugs in your oven you can just go out an buy a shaft coupler for $10 or so, but what's the fun in that?
Step 12: Z Axis Assembly
Fabricated Components Required:
2 piece anti backlash nut
Hardware Required:
12x #8 washer
6x #8 spring nut
The trolley and sled assemblies are complete and need to be installed and squared to the gantry.
12.1 Start by tightening the V-groove bearings on the trolley around the X-rails. The trolley should be as square to the base as possible but can be a degree or two out. All four bearings should be running on the rails so that the trolley slides smoothly without any play.
12.2 Put two flat washers and one spring washer on each of the 4" bolts attached to the trolley with the spring washer between the flat ones. Slide one half of the anti-backlash nut over the 4" bolts
12.3 Slide the sled between the 3/16" V-groove bearings. Put the other half of the anti-backlash nut, two flat washers, one spring washer and a nut on the 4" bolts. Keep the anti-backlash nut clear of the threaded rod as in Photo #5.
12.4 The spindle should be square to the bottom of the Bottom spindle bracket. Rest the bracket on something parallel to the base, I used a piece of 1x3 (Photo #4), to support the sled and hold it square to the base. With the sled supported, squeeze the v-groove bearings together around the Z-rails and tighten while keeping the sled square to the base. A flat wrench will be needed to hold the nuts at the back of the trolley. The spindle wrench from my rotary tool is 3/16" and was just long enough to reach the nuts. Do not over tighten the bolts or you will crush the plywood and it will be impossible to have the axis run smoothly without play.
12.5 With the Z-axis running smoothly it is time to form the anti-backlash nut. The nut has been shown preformed as I did this step the first time I assembled the machine. The nut is made from recycled HDPE like the coupling. HDPE is an ideal material for this part as it forms perfectly around the rod giving no play and has a low coefficient of friction so the motor can spin. To form the nut around the threaded rod use a pencil torch or equivalent (I used this style) to heat the rod pointing the flame on the rod just below the nut. When the rod has heated up, press the two halves together being careful not to touch the hot metal. Hold the nut in place for a couple of minutes to allow the plastic to cool. If you move it away before it has solidified around the threads it will pull away like melted mozzarella cheese and won't take a crisp outline of the threads. To protect the machine I covered the nearby areas with tinfoil to disipate the heat from any stray movements with the torch. I tried to angle the torch away from any parts behind the rod but managed to catch the end of the Spindle motor plate leaving it a little bit singed (Photo #8).
12.6 Tighten the nuts on both sides of the anti-backlash nut so the spring washers press the nut into the threaded rod (Photos #6,7). Play around with how much force is required to lock the axis in place but not too much to bind the axis. The support under the sled can be removed and the machine will support itself (Photo #9).
Step 13: Timing Belts
Hardware required:
3x MXL timing belt
6x 3/16" x 2" eye bolts
12x 3/16" nuts
24x #8 washers
6x 6-32 x 5/8" machine screw
6x 6-32 nuts
The timing belts are what converts the rotary motion of the stepper motors into precise linear motion along the axis. The belts are clamped onto eye bolts and the tension is adjusted by tightening the nuts on the eye bolts.
13.1 The first step to assembling the timing belts is to locate the two holes per end needed to clamp the belts in a loop. Test fit the components and mark where holes should be located if looped around the eye as in Photo #1. I purchased closed loop belts and simply cut them open using an utility knife.
13.2 Drill/punch the holes into the timing belts at the points marked. Use a 1/8" drill or an awl to form the holes. The material will be flexible and the resulting hole will be smaller than the bit diameter. The holes should be similar to those in Photo #3.
13.3 Assemble the timing belt anchors by looping the ends of the timing belt around the eye bolts and closing the loop using 6-32 machine screws (Photos #2,3). The holes will be smaller than the screws but twisting them while pushing will get them though the hole. The grooves should be on the inside of the loop and clamped shut making sure the grooves are meshed. The completed assembly should look similar to Photo #5.
13.4 For the Y-axis, loop the belts around the pulley and idler bearings and then bolt the eye bolts to the steel belt clamps (Photos #7-9). The Y-axis was designed to be the correct length for the belts used so there is no excess. The slots in the belt clamps are oversized to allow for adjustments in the belt positioning; adjust them so that the belt lines up with the idler bearings and the eye is far enough away from the base that it clears the gantry side when it is at the extent of its travel.
13.5 For the X-axis there is excess length in the belt. Instead of cutting the belt to length I tied the excess out of the way as shown in Photo #10 in case I wanted to make the axis wider in the future. It is a tight squeeze to get the belt around the idler bearings and motor mounting bolts and onto the pulley. Don't try and snake the eye bolt through because it wont fit. Make a loop in the middle of the belt and feed it up past the idler bearings and over the pulley. Position the eye bolts so that the belt is in line with the idler bearings which should also be close to in-line with the X rail. Photos #10,11.
13.6 Finally tension the belts by tightening the outside nuts on the eye bolts. Try to apply equal tension on the belts. Once you are satisfied with set-up, tighten the inner nuts to prevent the eye bolt from rotating.
Step 14: Squaring the Gantry
The gantry should be square before the timing belts were installed but by tightening then to different tensions they will try to pull the machine out of alignment. The machine can be brought back into alignment in three easy steps:
14.1 Tape down some scrap paper and using a square, draw a line perpendicular to one of the Y axis rails. Photo #1
14.2 Loosen the set screw on the spider coupling so that the two sides are uncoupled. Move the gantry so that when a strait edge is held flat against the X rails its forward edge is in line with the line drawn in step 14.1 Photo #2.
14.3 Take a similar measurement on the other side of the gantry (Photo #3). If the line is further forward than your measurement, tighten the front eye bolt; if it is further back, tighten the back back one. When a measurement taken on both sides of the gantry has the strait edge landing flush with the line the gantry is square and you can tighten the set screw on the spider coupling.
Step 15: Limit Switches
Hardware Required:
5x nominally closed momentary push button switch (3 red, 2 black)
15.1 Solder two conductor 26 gauge wire to each limit switch. Determine the length of wire required to reach the desired location of the controller box. I have chosen to place mine below the table at the back. I do not have a cable management system in place but will implement one once I gain some experience using the machine and get a feel for what will work best.
15.2 Attach a red limit switch (Y home) on the front belt support on the side the limit switch “bumpers” were installed in step 5.4. A black one (Y limit) goes on the same side at the back. Red limit switches designate home positions and black, extents of travel. Photos #2-4 show how the limit switch interfaces with the limit switch “bumper”. The wire for the home switch is run under the table to the controller box and the switch at the back simply drops strait down into the box.
15.3 Attach a red limit switch to the left side of gantry (X home) and a black one (X limit) on the right hand side (Photos #5-6). Feed the wire from the home switch through the hole next to the belt clamp and run the wire down the back of the gantry. Threading #8 nuts on the bolts protruding from the top X rail and gently clamping the wire keeps the wire in place. Feed the wire through the hole on the opposite side and bundle it with the wire from the switch on the right hand side. Photos #7-9
15.4 Attach the Z-home switch to the bearing clamping block under the anti backlash nut. Hot glue was used to position the switch as required. Photos #10-11
The machine is now fully assembled and ready to hook up to the driver board.
Step 16: Foam
Foam board (Extruded polystyrene rigid insulation) is the perfect prototyping material for the CNC. High feed rates and aggressive cutting depths can be used allowing prototype parts to be machined quickly and at $20 for a 2' x 9' x1" board you can afford to make mistakes without hurting your wallet.
Multiple fluted high speed cutting bits (similar to this one) work better than double fluted router bits. When using sharp tools the finish can be quite good (such as this done on my first machine). Using the cutting bit on harder materials causes it to loose its edge and it will leave a fuzzy finish on the foam. The lesson here is to segregate your cutting bits based on material which lead to me building the bit holder in Step 18.
The first thing I like to do when machining a new material or after making adjustment to the machine is to cut out calibration shapes to see how well the machine is performing. A 2" square and circle are shown in Photo #1 with dimensions shown as measured using a pair of digital callipers. Before cutting these make a strait cut in the material and measure the width of the groove. A 1/8" bit won't cut out a perfect 0.125" because the cutting bit isn't likely to be exactly 1/8" and there will be some spindle runout. Because there is very little force on the tool when cutting foam this test shows the performance of the drive train and not the stiffness of the machine. When taking measurements I keep in mind that the machine has a resolution of 0.004" which is smaller than the error from my cheap pair of digital callipers. Measurements to look for on these shapes are as follows:
-the square is a square and not a rectangle. If one side is shorter than 2" it shows that the corresponding axis is loosing steps/slipping.
-The circle has a consistent diameter when measured at various angles. If this doesn't check out but the edges of the square were correct it shows that the X and Y axes aren't square and the square was actually a parallelogram.
With a maximum resolution of 0.004" on the X and Y axes I was more than happy with the results.
Next I did the CamBam drilling tutorial using a 1/16" drill bit.
Testing 3D shapes I cut a miter gear and a sprocket using CAD files downloaded from sdp-si.com. CamBam files for all parts are attached.
Step 17: Plywood
Calibration cuts in plywood yielded good results. The shapes were accurate and had very good surface finish. All photos show the surface finish strait off the tool.
The feed rate was limited by the spindle power and the noise level. I have no reason to believe the machine would't be able to make more aggressive cuts if a palm router/laminate trimmer was installed.
Step 18: Bit Holder
My local tool store happened to have their off-brand rotary tool bits on sale so I got a good selection of different styles to try at a fraction of the price for name brand bits of a similar quality. Any rotary tool bits you can buy at tool stores will be marginal in terms of the quality of cutting edge they are shipped with and their ability to hold an edge when sharpened. In order to get the best possible performance and cut quality you'll have to look at purchasing speciality 1/8" shank cutters from suppliers on the internet or upgrade to a 1/4" spindle so that you can use the much higher quality standard router bits. To maximize their cutting life I've built a tool holder to separate the cutting bits based on the material they are to be used on. The piece was cut out of a piece of 1x4 using the following steps:
1) The letters were engraved using a 3/32" end mill. Letter depth is 1/16"
2) Two rows of 1/8" holes were drilled with 7 holes per material.
3) Four 3/16" holes were cut per material.
4) The lettering was lightly sanded using a flat sanding block to clean up any rough edges. When cutting with the grain or on a down hill cut the cutting bit gave a crisp edge. When cutting across the grain or on a climbing cut the tool left fibers on the upper edge. A down spiral cutting bit would solve this problem and give a crisp edge all around the lettering.
5) The engraved lettering was painted being careful to stay within the lines.
6) The excess paint was sanded away giving a clean edge to the lettering. The tool bit holder is complete and ready to be filled with rotary tools of all sizes.
Attachments
Step 19: Propeller Pt 1/5 - Mould
For my first real project I wanted to make something that demonstrated the advantage of using a cnc machine and its capabilities. I originally was going to build a model sailboat but decided it didn't quite fit the bill as it is possible to construct one using traditional methods (but must slower and a bit less precise). I had recently been reading articles on propeller design for human powered vehicles from the great archive available on the International Human Power vehicle Association’s website. Of particular interest is Eugene Larrabee’s article in the 1984 Volume 3 Issue 2 detailing the process of designing propellers using the minimum induced loss method.
I have attached a spreadsheet that performs the calculations and outputs the propeller particulars when given the power, speed, rpm and radius as inputs.
(Edit 29/4/2012, calculation spreadsheet now attached)
For my propeller I used the parameters
P=200W
Speed = 3 m/sec
RPM= 200
Radius = 22cm
Number of blades=3 (Ooops! didn't realize this mistake until I was finished making the propellers)
I put the information into Rhino3D, a 3D CAD program that is very good for creating complex surfaces (a trial version is available here) and generated a line for the leading and trailing edges using the chord and pitch distribution from the spreadsheet. To generate the propeller surface I used the Sweep2 command using section profiles between the edges. The propeller has both geometric twist (change in angle of attack over its length) and aerodynamic twist (change in airfoil cross section). The propeller has a constantly changing cross section going from a heavily modified NACA 4418 cross section at the root to house the bossing, transitioning to a 4415 at the 1/3 radius mark, 4412 at roughly the 2/3 point and blends into a point at the tip. To produce a two part mold I split the propeller in half at its widest point to avoid any undercuts and created a box around both sides to create top and bottom molds. The resulting parts have very complex curvature and would be extremely difficult if not impossible to make by hand with a reasonable amount of precision, making it the perfect project for a cnc machine. To make an assembly I sketched out an end cone and two piece hub to bring everything together. The geometries are attached in iges format.
I wanted to find out how suitable polystyrene foam would be for a single use composite mould. A two piece mould was machined and used to layup two carbon fiber propellers.
The two mould halves were cut out using a 0.075” rouging cut (Photos #7&11), 0.05” finish water line cut (Photo #8) and a vertical scan line pass (Photos #9,10 &12) taking around an hour per side. The 3/32” bit used for the finishing passes did not leave as crisp a surface as the larger bit leaving a fuzzy surface. As soon as the moulds had been removed from the machine I realized that I had not included holes for indexing pins; luckily I didn’t have any issues aligning the two sides without them.
The first step to preparing the mould was to give them a quick once over with 400 grit sand paper (Photo #15). The goal was not to shape the material and remove the remaining scan lines but to take off as much of the fuzz as possible.
The moulds were then given two coats of thinned latex paint (Photo #16,17). Using thinned paint prevents build-up that would change the profile. The purpose of these coats is to give the foam a better surface to sand against to take off the remaining “fuzzies”. With the paint fully dry I used 200 grit wet/dry sanding paper and sanded with a bit of water (Photo #18). A final coat of paint may be required to fill any thin areas after sanding.
When I was happy with the surface quality of the mould I applied 6 coats of mould release wax according to manufacturer’s directions. Because I wanted to get two parts out of this mound I followed up with a precautionary layer of PVA applying it in two thin coats.
I had only prepped the top surface of the moulds but to protect the mould from epoxy seeping out from the joint I spread a layer of Vaseline around the edge to prevent the mould from being glued shut.
Step 20: Propeller Pt 2/5 - Carbon Fiber Layup
With the moulds prepared they are ready for laying up the carbon fiber. Before I began this step I got all the tools and materials I required and cleaned my work area. Working with composites is much cleaner and more enjoyable when things are set up properly before you begin. All my work with epoxy and spray paint was done out on my balcony to avoid breathing in fumes.
Will all the items in Photo #1 on hand I started by cutting out strips of carbon fiber to the rough shape of the propeller. Photo #2
Next I mixed up the resin and hardener. I ended up needing 30ml of epoxy which can all be mixed at once as it has a working time of over an hour. I applied a coat of epoxy to the mould surface and laid down the first strip of carbon fiber (Photo#3). I wetted out the fiber making sure it was fully saturated and repeated the procedure of laying down a new layer and wetting out. Each new layer was narrower than the previous building up thickness in the middle but not at the trailing edge where the profile tapers off. Progress was gauged using a popsicle stick laid across the mould as in Photo #4 showing which areas require more fiber. A 2" long section of 1/8" key stock was embedded in the propeller with 1" protruding. Small offcuts were used to pack in around the shaft. When one side of the mould was built up to the required thickness the second half was laid up in the same manner. With both halves completed the moulds were brought together and lined up (Photo#5). With the mould lined up a stack of text books (I knew they would come in handy one day) was placed on top compressing it together. A good amount of epoxy and carbon fiber came out at the seam making me glad I had applied that layer of Vaseline to the sides. Photo #6-8. The end of the mould at the propeller tip had a tendency to slide apart due to the slanted surface. A C-clamp kept the mould aligned on this end.
After twelve hours the epoxy had jelled but had not hardened completely. I had a utility knife around the seam and popped the mould apart with little difficulty (Photo#9-11) I was pleased to see that the mould release has done its job and the mould had survived with little to no damage. Using a utility knife I trimmed away the swarf on the propeller as it is much easier to do before the epoxy hardens (Photo #12). With the excess trimmed off I put the propeller back into the mould to keep its shape until finished curing.
Once the propeller had sat for 24 hours I repeated the process for the second one.
After the second propeller had sat for 30 hours the epoxy had fully set and was ready for sanding. I used 120 grit sand paper from a sanding belt and 220 grit wet dry paper. Wet sanding is more efficient than dry and eliminates the nasty carbon dust that would be produced otherwise. After cleaning up the leading and trailing edges as well as sanding away minor surface flaws the propellers looked as shown in Photo #14. They are smooth but dull. To finish the propellers I applied four light coats of clear gloss finish (Photo #15). Light coats are important here; I got excited and laid down too much finish causing runs that had to be removed using 600 grit paper.
Step 21: Propeller Pt 4/5 - Hub
This step covers my process of recycling platic milk jugs into billets and machining them into the hubs for the propeller. This process was also used to make the shaft coupler and anti backlash nut.
HDPE (or High Density Polypropylene) is a great material to work with as it is hard, easy to machine and has a low coefficient of friction. This site has a good breakdown of how it compares to other engineering plastics. When bought in sheet form it is fairly expensive but it is laying around your house in a variety of forms, milk jugs, other food grade containers, cutting boards etc.
The process I use has been refined after many trials and represents the best method I have tried so far. I started by searching instructables and the web to find what others had done and found this one. I tried this method several times changing different parameters each time but melting the plastic in oil didn't give the final consistency I was after. My next idea was to melt the platic in a tin can that was submerged in oil. I neglected the effect of bouyancy and had problems keeping the can submerged. My first thought was to place a weight on top of the can but this made it too top heavy and prone to tipping over, not something you want when it is in hot oil. I thought I found the perfect solution by attaching the can to the bottom of the pan using magnets but when the oil gets up to temperature the heat is enough to break down the magnetism of the rare earth magnets I used. The next step of the evolution of this process was to melt the plastic in the oven and is the method I used here.
The first step is to clean out some milk jugs, take off the labels and reduce them into flakes. I do this with a pair of scissors while watching tv. I can only do about four jugs at a time which takes around an hour before I start to get blisters from using the scissors. The flakes should be as small as you have the patience for, as reducing the size in half requires four times the cutting time. The smaller the flakes are the easier it will be to eliminate voids in the plastic. Cutting the milk jugs up by hand is very tedious and I have tried to come up with better methods. I can tell you one that doesn't work is using a paper shredder. HPDE is used in tick tac lids as it is very flexible and won't break due to fatigue when flexed. This property means that it will not shred in the paper shredder but will deform enough to go in half way and get stuck. I cut up four milk jugs aiming for flakes 3/4" x 1/8" in size (Photos #1,2).
I cleaned up three tuna tins for use as moulds. I have made billets from all sizes of cans from tomato paste for the shaft collar and larger tomato cans depending on what I want to use the plastic for. (Photo #3)
Next I filled the tins up with flakes. When melted these will compress and the tins will have to be topped up. (Photo #4)
With the oven preheated to 350 degrees Fahrenheit I put the tins in for half an hour. HPDE has a melting temperature of 266 F and an extrusion temperature of 350-500F. With a household oven the temperature can be expected to swing +/- 25 F as the heating element cycles on and off. Trying different temperature settings I fould that at 375F and over the plastic would burn and give off an unpleasant smell. I've settled on 350F as the best temperature to use taking longer to melt the plastic but avoiding overheating issues.
After the half hour I removed the tins from the oven and press down the partially melted flakes with an old spoon to compress the material and try to remove any voids (Photo #5). If the tins are out of the oven for over a minute or so the extremities will begin to cool and transition from opaque to white.
I kept putting in the tins in for half hour stints and after two hours they were fully melted. I gave them one last press with a spoon to try and get the surface as even as possible to minimize machining afterwards. Photo #6. When fully melted they are fully opaque. The material is not runny but has a sticky gooey consistency.
I have tried many different methods of heat cycling the plastic to minimize internal stresses. If the pieces are thin enough and taken out of the oven at this point and left to cool, they will warp. The easiest way to minimize the heat stess is to just turn off the oven and walk away. The plastic will retain heat remarkably well and will be too hot to handle even after several hours. I leave them overnight to be sure everything has cooled down slowly. There is enough shrinkage when cooled that the parts come out easily from the tins even when there is a slight lip on the inside. Photo #7.
After cooling the recycled plastic is ready to be machined into propeller hubs. Starting with the top hub the top surface is machined flat (Photo #8). The excess plastic is cut away using a hack saw (Photo #9). The piece is then flipped over and the bottom surface is machined flat (Photo #10). Next the five holes are machined with an end mill (Photo #11), and then the recess for the bolt head (Photo #12). A 1/8" groove is cut for the propeller shafts (Photo #13). The last step for this side is to cut out the circular profile. The part is now flipped over and recesses cut for the nuts (Photo #14).
The bottom hub is similar with the top surface of the piece machined flat (Photo #16,17) and then flipped over and flattened again (Photo #18,19). Holes and a 1/8" groove are machined next (Photo #20) and finally the profile cut out (Photo #21,22). Not shown, but the final step is to flip the piece over one more time and machine the recesses for the bolt heads.
As I progressed through the steps I tried different cutting speeds and depths. I discovered by the end that I was not taking deep enough cuts which resulted in the bit chattering on the surface. The facing cuts would have been much cleaner such the recess in Photo #8 had I taken off twice as much material per pass.
Drawings for the hubs are attached.
(Edit 29/4/2012, propeller hub drawing now attached)
Attachments
Step 22: Propeller Pt 3/4 - End Cone
The end cone is the attachment to the hub that makes the assembly more aerodynamic (or hydrodynamic) when travelling through a fluid. The base diameter is 2" to match the hub diameter and the height is 2" chosen to give a streamlined surface without being too long. The overall shape is a parabola what has been reloved around a central axis.
To build it a plug was machined from 1" polystyrene foam in two halves (Photo #1). 0.05" was left at the bottom to stop the parts coming loose on the last pass (Photo #2, I need to learn how to use the holding tabs feature in CamBam when I get the time). The two havles were then glued together using a thin layer of white glue after the swarf was removed with a utility knif and some 220 grit sandpaper (Photo #3).
To give the endcone a hard durable shell I covered it in a layer of fiberglass using the vacuum bag method using the following steps:
-I assembled the materials in Photo#4. I was working outside with good ventilation to protect myself from the fumes.
-I measure out the epoxy in to 2:1 ration of resin to hardener using the measuring cups. Shown in Photo #5 is 15ml of mixed epoxy, I ended up using 30ml.
-Starting the fiberglassing I wetted out a piece of fiberglass cloth 3"x3" (larger than the cone's base) onto the piece of waxed MDF. Photo #6
-Next I placed the foam endcone plug in the middle of the wetted fiberglass. Photo #7
-and draped a piece of fiberglass cloth over it. Photo #8
-I wetted out the cloth until all areas were saturated with resin. In Photo #9 I still have creases in the cloth. These will not lay flush even after vacuum bagging so small slits will have to be cut in the fiberglass overlapping the edges to smooth the material out.
-Next an oversized piece of peel ply is layed over the fiberglass. Photo #10
-And then a layer of breather cloth (Photo #11). I put an elastic band around everything at this stage to hold it all together while I made the bag. Photo #12
-I placed everything on one side of the vapour barrier (Photo #13) and doubled the plastic over sealing the edges with duct tape while inserting an air line from underneath the breather cloth and out a corner (Photo #14)
-The exit point of the air line is the hardest place to seal. I used plasticine around the airline as shown in Photo #15. This takes a long time to get right an is quite frustrating. The next time I vacuum bag something I will take the time to make a proper sealed connection using brass fittings.
- A vacuum is now applied using a pump made from this instructable. With this setup I can pull up to 25" Hg.
-After 24 hours to let the epoxy cure the part was taken out (sorry, forgot to snap a picture of this step), the excess glass cutoff around the bottom, a coat of primer applied and sanded to be flush with the propeller hub. Photo #16
-When I was happy with the fairing (more a function of the time I had available than the results, it could have been a lot better) I gave it a couple more coats of primer. Photo #17
-I cut out a recess on the bottom and using autobody filler attached a #6-32 nut and washer. I covered a 1/2" long #6-32 machine screw in Vaseline to prevent the autobody filler from sticking to it and assembled it through the mounting hole in the propeller hub (Photo #18). This makes it possible to remove the endcone from the top side of the hub. I later decided that removing it wouldn't be necessary so I faired the hub and endcone together with drywall compound and made them one piece.
-Using metalic autobody spray paint I had on hand (Photo#19) I gave the endcone/top hub assembly and the bottom hub three coats of paint followed by a layer of clear coat. Photo #20
Step 23: Propeller Pt 5/5 - Assembly
So here it is, the final assembled propeller. The parts are assembled as shown in the exploded view in Step 19.
The main purpose of this project was to demonstrate the feasibility of making a mould from expanded polystyrene to create an accurate composite part. This process has been a resounding success with the cnc machine successfully machining a complex surface and imparting that geometry to the composite part. With this process a piece can be created in three evenings worth of work:
Day 1: Mould machined (1-2 hours depending on complexity)
Mould painted and sanded (1 1/2 hours give warm enough temperatures and thin coats being applied)
Mould prepared with release wax and PVC (1 hour for 5 coats of wax drying for 10 min between applications and a coat of PVA left to dry overnight)
Day 2: Layup of composite (1 hr)
Day 3: Sanding and finishing of part (1-5 hrs depending on many factors)
The HDPE hub turned out alright but shows a lot of promise for using the material in the future. As mentioned in Step 21, more practice is required to get the optimum feeds speed and depth to achieve the best surface quality possible with my set-up. A few voids can be seen in the material but these are nothing compared to what I was getting when I first started. With a bit more refinement I am confident I can make consistently void free blocks.
The weakest part of the lot is the end cone which comes down to not spending enough time fairing the surface before painting. In the future I will try vacuum bagging parts like this one in a female mould so, like the propeller blades, the final shape can be as accurate as the cnc machined part.
Step 24: Follow Up / Improvements
The machine has been up and running for nearly a month now and has logged around 7-8 hours of cutting time without any major problems. At around the 3-4 hour mark I had to re-tighten the V-groove bearings on the X & Z axes but these have not loosened since then. The following are a few observations I have made while using the machine.
The pulleys on the Y axis have come loose more often that I liked. The problem wasn't the time require to re-tighten them but that they would have to be checked before each use to make sure they were secure. I had cut out a propeller end cone to find out it was circular because I hadn't noticed the pulleys had come loose. To solve this problem I attached 1/4" shaft collars to the pulleys using 10 minute epoxy as shown in Photo #1. All of the HDPE parts were cut using this setup without the pulleys loosening. When running at less than 30 inches per minute the movement of the machine is slightly jittery as the discrete steps of the stepper motors is magnified. In the future I will be replacing the 40 tooth pulleys with 20-30 tooth versions to increase the resolution of the machine and make it;s movement smoother. I imagine these will come with the same size set screws as before so I will take the time to bore out the threads and re-tap them to accept 8-32 set screws as are on the shaft collars.
I had expected the aluminum rails to show signs of wear from the contact with the V-groove bearings as this was experienced on my first machine. The rails have worn a little bit as shown in Photo #2 but shouldn't require replacing any time soon. I will make a concious effort to use different parts of the machine when cutting smaller items so that the wear isn't concentrated in a particular area. If this becomes a problem I might consider making my own V-groove bearings from HDPE and fitting them around a skate bearing. The HDPE against aluminum should have very low friction and good wear characteristics.
The part I was the most concerned about was the elastic band driving the spindle. This had taken a bit of damage during the construction process and I didn't know how quickly it would wear if it was slipping over the pulleys. Photo #3 shows the elastic band in good conditions with minor wear that as taken off the lettering. The pulleys in Photo #4 show a bit more wear but is mostly cosmetic.
The home-made spindle has performed well and as been quiet enough to use in an apartment but I would like a bit more power and the ability to use higher quality 1/4" shank router bits. I will be looking out for garage sales to pick up a 1/3 HP induction motor (similar to the one in this) and trim router to make a beefier hight powered version of the current spindle.
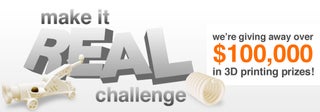
First Prize in the
Make It Real Challenge