Introduction: Make a Playable Laser-Cut Gramophone Record From Bioshock Infinite
Presenting a genuine Albert Fink's Magical Melodies recording playable on any gramophone of your household!
Sounds of Columbia by our very own genius composer! His many songs subjugate the charts!
Hear the Music of Tomorrow Today!
WARNING: This instructable may contain mild spoilers about the plot of Bioshock Infinite.
I've always loved the music of the Bioshock series and, partly to convince myself that Rapture and Columbia could exist, I've been slowly building up a collection of records as people could have listened to them in the first half of the 20th century.
Naturally, I was excited/dismayed when Infinite came out as it meant I would have more soundtrack to explore/locate and collect. However, although I was pleased at the ingenuity of re-recording period-style anachronistic covers, I was disheartened by the fact that there would never be a way to listen to them on a phonograph as they play in-game.
So I decided to make my own. I'm still working out the kinks and testing cutting 78s on acrylic using a laser cutter. But it's something else to hear music that's never existed before on a record come out of 100-year-old phonograph.
Without further ado, Albert Fink presents "God Only Knows"
Step 1: Why 78 Rpm?
Unlike Mister Albert Fink, I give credit where credit is due.
I modified amandaghassaei's wonderfully documented instructable and adapted it for 78 rpm. In fact, it's probably best to read hers first. The instructable is meant for cutting records out of various materials at 33.3 and 45 rpm, the most common record speeds. The author only makes one passing reference to 78s.
However, there are several advantages to cutting at 78 rpm
1) Gramophones are 78-exclusive: Old-fashioned crank phonographs can only play at this speed. However, very early records prior to the formation of the RIAA standard and poor pressing quality at the turn of the century meant that records could have variable speeds from 60-130 rpm. Labels would sometimes display the speed required, but often it was left up to the listener. Many phonograph have speed adjuster for this reason.
This was standardized to 78 rpm in 1925.
2) Mono sound: The laser cutter can only handle cutting grooves with monophonic sound; separate left and right channels are impossible. When the laser cuts the record, it follows a line path which creates a groove with two identical walls. In order to fit two channels on audio on one groove, stereo sound, the two groove walls have to be cut with different lateral and vertical modulations.
78s and early vinyl records were exclusively mono, hence the single speaker, perfect for the time period I'm going for.
3) Laterally cut grooves: The depth of the laser can be adjusted prior to cutting, but not on-the-fly during the cut. So any grooves made by the laser cutter will have to go back and forth and not up and down.
Most 78s and mono vinyl records had laterally cut grooves which is still the norm nowadays. Some Pathé and Edison Diamond Discs were vertically cut (also known as hill and dale recording), but record companies pushed in favor of the lateral cut. amandaghassaei mentions that it's best to 3D print a record with vertically cut grooves as the vertical axis is most precise. Perhaps these two instructables can be combined to make a record playable on an Edison Diamond Disc machine.
See here for a great visual explanation on how the record needle extracts sounds from the grooves.
4) Wider grooves: As amandaghassaei noted in her 3D Printed Record instructable, 78s use a wider needle (2.2-3.6 mil or 0.0022"- 0.0036") to fit into the wider grooves. By contrast, "microgroove" LPs require a 0.7 to 1.0 mil (0.0007" - 0.001") needle.
The laser cutter I'm using has a minimum kerf of 0.006", so it's more appropriate to make a 78 style record and then use a stylus made for 78s to ensure the needle is making full contact with the groove walls.
I'll go into more detail on the laser cutter specs page.
5) One Sided: Very early records were one-sided until technology improved that could press both sides of a record at the same time. Most of the time, the blank side was just blank, but sometimes the back was nicely embossed with the company logo.
Records are typically pressed with two molds pressing into a biscuit of vinyl or shellac at the same time. I haven't been able to make a proper two-sided record on the laser cutter. Basically, it entails flipping the record over and cutting in the exact same position. Most of the time, I have significant wow on the second side since the grooves are slightly off-center from the spindle hole.
6) Better Sound Quality: If you can get more data passing by the needle per second, you'll have better sound.
I modified amandaghassaei's original equations to prove this. Everything else is constant except for the speed.
At 78 RPM
(78.26 rpm for 60Hz countries, 78.92 for 50Hz countries)
revolutions per second = (revolutions per minute)/(seconds per minute)
revolutions per second = 78.26/60 = 1.30
inches per revolution = 2*pi*(radius of needle)max inches per revolution = 2*pi*5.75 =~ 36
min inches per revolution = 2*pi*2.35 =~ 15
sampling frequency = (resolution per inch)*(inches per revolution)*(revolutions per second)
max sampling frequency at 78 rpm = 1200*36*1.30 =~ 56200 = 56.2kHz
min sampling frequency at 78 rpm = 1200*15*1.30 =~ 23400 = 23.4kHz
At 45 RPM
max sampling frequency at 45 rpm = 1200*36*0.75 =~ 32400 = 32.4kHz
min sampling frequency at 45 rpm = 1200*15*0.75 =~ 13500 = 13.5kHz
At 33 RPM
max sampling frequency at 33 rpm = 1200*36*0.5 =~ 21600 = 21.6kHz
min sampling frequency at 33 rpm = 1200*15*0.5 =~ 9000 = 9kHz
From amandaghassaei's instructable:
"Sampling rate is the amount of samples per second in a song. Usually the sampling rate is 44.1kHz (or 44,100 samples a second). When the sampling rate drops below about 40kHz the higher frequencies of a song start losing their detail, but depending on the song you can go down to 20 or even 10kHz sampling rate without too much of a problem."
Ideally, 78 rpm should be able to provide a higher possible sampling rate with better sound.
Some caveats: Unfortunately, I do not know the resolution (dpi) for my machine just the precision, so I've left that unchanged in the equations.
Additionally, most 78s exist on 10" singles, 12" was usually reserved for longer operatic and classical pieces.
However, the RIAA standards also dictate 78 rpm standards and the equations are left up to the reader.
The main disadvantage of cutting at 78 rpm is that more grooves are required which correlates into a longer cutting time. So a 2-3 minute song takes up an entire 10" record side while a 12" LP can hold 20 minutes of uninterrupted music. I'm still working out the kinks, but I'd like to find a way to reduce the cutting process; it currently takes 10 hours to cut an entire record.
Step 2: A Brief History of Records
I want to set a few things straight about records. Some people may be unfamiliar with older records and I'd like to explain some terminology. You can skip ahead if you're not interested.
In the pre-CD and cassette world, records were how music was recorded and delivered to the masses. The basic mechanics are deceptively simple and have remained virtually unchanged for 100 years. A medium, nowadays typically vinyl, would have grooves pressed into it which would vibrate a needle to deliver sound.
Many of you are probably familiar with vinyl records, the most common; 12" LP records that spin at 33.3 rpm and 7" 45 rpm singles with the big hole in the center. These were the dominant form of recorded music from the 60s to the 80s before being supplanted by the aforementioned cassette and CD.
Prior to this, close to the invention of recorded sound at turn of the century, and the setting of Infinite, shellac discs were the norm and spun at 78 rpm. The high speed is partly due to the poor sound fidelity of this early era; if more music data passes by the needle per second, you'd get better sound. It's also partly derived from momentum coming from earlier cylinder recordings which spun at about 90 rpm.
78s are the type of discs that you'd see in old Tom and Jerry and Looney Tunes cartoons. If you remember your high school English class, Holden Caulfield purchases one in a record store.
However, they highlight one of their defining characteristics; if thrown against a wall or dropped, they would shatter like plates (vinyl, being a type of plastic would bend or warp). These are also the type of records that you would play on old wind-up phonographs/gramophones.
In addition, shellac could not handle highly compressed sound without encountering a significant drop in audio quality. However some 33s did exist which were made out of a softer version of shellac such as Vitaphone's movie soundtracks.
16 rpm was intended for use by the blind for "talking books" which compressed as much as possible on one disc. This practice continued even until the 1970s which is why you'll sometimes encounter a 4-speed record player.
There are two main types of phonographs; the showy ones with the large acoustic horns that's imprinted in the public conscious and the more sedate ones with the internal horns. You see them both in Bioshock Infinite. Funnily enough, the ones with the big horns were considered big, unattractive, and enormous dust-collectors. The horn was awkwardly shaped and did not store well which has led to missing or banged-up old horns. Fittingly, the Luteces have one with an internal horn in their laboratory.
Before you try, vinyl records cannot be played on a phonograph since speeds were not adjustable from 78 (so everyone sounds like chipmunks) and that vinyl is much softer than shellac and has much smaller grooves (so the needle will gouge out whatever remains of your record).
Although 78s were fragile and could only hold 2-3 minutes of music per side (typical singles were 10", longer operatic works were on 12" records) they were extremely popular (as recorded music had never existed before; all music was "live") and continued to be produced until the 60s.
Bioshock 1 and 2 take place in the very heart of the "war of the speeds" from the 40s to the 60s. Technology had improved so that records could be made at a slower speed while maintaining and improving audio fidelity. Columbia records (yes, Columbia records is a real and one of the oldest record labels that still exists today; one of their latest releases was Random Access Memories) introduced the new "microgroove" 33.3 rpm 12" record. They were called LPs (long-playing) since they could play up to 20 minutes per side. The use of vinyl also allowed more grooves to be compacted per inch allowing longer playing times and more durable discs (many were advertised as "non-breakable" compared to the fragile 78s). However RCA Victor, marketed the 7" 45 rpm single which offered cheap popular music for teenagers. This is why 45s traditionally have the large center hole which allowed for easier handling by jukeboxes.
Much of Bioshock's soundtrack can be found on 78 and 45 singles as a result of this, though older songs were originally released on 78s. LPs featuring these songs are typically compilation albums of older reissues or new re-recordings.
During this time, many record players and labels offered 3 speeds to see who would win out. Additionally, in relation to the LP, 78s became known as SPs (standard play). 10" 33s were known as EPs (extended play) as they contained less music than full albums, but more than a single.
The large number of phonographs lying about in Bioshock 1 and 2 mean that the music probably was on 78s. There are a couple of jukeboxes, but there were available versions that could play 45s and 78s. Bioshock 2 also has some additional examples of different record players.
RCA Victor and Columbia eventually reconciled and started manufacturing each other's speeds, 45s were good for singles of popular music and LPs allowed for soundtracks and longer albums. 78s eventually died out, though some still were produced in 3rd world countries such as Africa, India, and the Philippines. Artists from the 60s such as the Beatles on 78s are very rare and highly collectible.
I already have a very eclectic (and growing) record collection which inspired my to do this project. I'm currently curating it at www.rapturerecordssonorousinc.tumblr.com
Step 3: Laser Cutter Specs
I currently have access to a LaserCAMM Model No. 2305. It uses a CO2 laser and can cut or score materials such as paper, acrylic, balsa etc. The laser can be manually focused up an down by the adjustment screw. It only reads AutoCAD 2000 .dxf files in inches. Apologies if the photos are blurry; they have to be shot through the protective cover.
The kerf of the laser is 0.006". The specifications from the company indicate that the leadscrew resolution is within (+/-) 0.005"/ft. I do not have this information in DPI
I will explain how it works for my machine. You may need to adapt these instructions for your laser cutter. I highly recommend that you read her instructable first.
amandaghassaei had the foresight to make the music groove data available on a vector pdf. Here I will demonstrate how I got from pdf to LaserCAMM file (.dmc). Her Epilog seems to be able to cut from pdf, but I have to go through the following conversion process.
1) Translate from PDF to AutoCAD using Illustrator (pfd to dwg): I ran into a lot of problems with missing grooves. I would open up the pdf in Illustrator to find that grooves became lost during the conversion. It seems that there's a cap on how much data Illustrator can take. It seems to be about 180 kB per file. You can adjust your Processing sketch to output several pdfs based on how many grooves per file. 8 grooves was the maximum I could do without losing data. Unfortunately, I got 40 pdfs to sift through.
Be sure to scrutinize the pdfs versus what you get from Illustrator.
Illustrator is able to export DWG files for use in AutoCAD. When exporting, under DXF/DWG Options, be sure to change the Artwork Scale to "1 in = 1 Units" (or your preference) so you don't need to rescale the object again in AutoCAD.
2) Convert from DWG to DXF in AutoCAD: The LaserCAMM software as I've said is rather old and only reads DXF files from 2000. Once you've opened your DWG file, EXPLODE the object and delete the bounding area lines. You can move the object, but be sure to do the same for every other file. The LaserCAMM only reads data made in the 1st Quadrant of the coordinate plane so I had to made sure the eventual record didn't cross the axes.
I was here that I also realized that separating the grooves into smaller files was an extremely good idea. AutoCAD is memory intensive and the large number of data points sometimes caused my computer to freeze. The smaller files help to reduce this. Unfortunately, I still had 40 files to feed into the machine later.
The LaserCAMM also recognizes layers. So for the last file with the spindle hole and the record outline, I can save them to separate layers from the grooves as Inner and Outer so the LaserCAMM can recognize them as different cuts.
The last step is to save as a DXF (2000).
3) Converting to LaserCAMM format (dxf to dmc): The computers in the laser cutter room have the software to do this. In the dialog you can choose OPERATION, MATERIAL, THICKNESS, and POWER.
The OPERATION settings has several options such as CUT, which completely cuts the material, and SCORE which etches the material. The LaserCAMM can recognize different cut settings for each layer and proceed accordingly.
I contacted the LaserCAMM engineer and he recommended the following setting for a CUSTOM cut.
Power: 2% (I found that this made the cut too shallow; 5% works better; deeper scoring results in longer cut times)
Speed: 80 inch per minute speed (increasing the speed seems to decrease cut times, but the cut becomes shallower)
Width: 30 microsecond pulse (this apparently controls the time for the laser to turn on and off as it moves from point to point)
I need to further experiment with these settings to reduce cut times.
This will output a dmc file. The LaserCAMM program also has a useful ability to merge several dmcs into one dmc. Then send it out to the machine and wait for the laser cutter to do its work.
Step 4: Cutting the Record
Choosing the Songs
There were several choices that seemed appropriate for this project. The period songs were already available on records (and some on wax cylinders). The classical music and the Scott Joplin songs are probably modern recordings, but similar versions could possibly be found on records.
So my main focus was on the period-sounding anachronistic covers which have never existed on a record.
"Everybody Wants to Rule The World"
"God Only Knows"
"Girls Just Want to Have Fun"
"Fortunate Son"
"Shiny Happy People"
"Tainted Love"
Additionally, there were some actual period songs re-recorded for the game.
"After You've Gone"
"Will the Circle Be Unbroken" (choral and duet versions)
"Wild Prairie Rose" is a modern song sung by Jessy Carolina (who is the vocalist in some of the previous songs) and her band "Ommie Wise". It was a nice touch in-game.
Unfortunately, test-cuts of the songs that apparently have been run through vintage filters with artificial pops and crackling don't come out too great. I would like to have access to the original recorded takes to possibly get these to sound great on records (with their own actual pops and clicks)
So I settled with "God Only Knows" and "Will the Circle be Unbroken" both since they were "live" without filters and they were the most recognizable songs from the game.
I also realized that the titles were appropriate descriptions as I sat in the laser cutter room for several hours on end trying to figure out if this will work.
Material
First I had to make sure that the material choice was feasible. Vinyl is much softer than shellac and can readily take impressions with finer detail. However, it is much more prone to dust, static, and scratches.
According to this hardness scale PVC has a Shore Hardness of about 75 while acrylic is slightly higher at about 85.
Shellac records could have up to 75% of filler and abrasives in an attempt to grind the record needle to the shape of the grooves. I found little documentation of the hardness of shellac to acrylic. The closest I came was this page for testing the hardness of varnishes. The technique is to use a set of drawing pencils with varying hardness (9H - 9B) and attempting to scratch the finish (9H is hardest). The shellac finishes have a hardness of 3B while acrylic varies from 4H - 2H - 3B. So theoretically, acrylic is harder than shellac so using a heavy phonograph reproducer on the material shouldn't pose a problem.
I attempted to mimic the thickness of actual records. I ended up using 0.125" acrylic sheets (clear was all they had). If I go thinner, I would be concerned that the etches on each side would blend into each other.
Creating the Cut Files
There are basically 3 steps here.
1) Using Audacity to modify the sound file
2) Running the sound file through python to create a text file with the sound data
3) Using Processing to convert the text file into a set of vector pdfs with the grooves
Again, I highly recommend that you review how amandaghassaei laid out her files and programs to create the record.
Also I'm not sure how to insert a block of scroll-able code like in amandaghassaei's instructable. It may be a PRO feature. I'll include a link to my githud repository.
https://github.com/UpgradeTech/LaserCutGramophoneRecord-78RPM
First things first, make the sine test record. Just run the file through Processing to create the pdf. This is to make sure that your laser cutter is able to cut records in the first place
If you're impatient like me, here's how I made the record files:
It's best to create a folder such as "Gramophone Record". Inside, put the wavtotext-78test.py Python file. Then you should have the "LaserCutRecord_78test" folder with the LaserCutRecord_78test.pde Processing file inside.
Audacity
I didn't have as much of a problem getting the grooves to play the non-amplified original sound file. Still it's something to look into to try to get better sound from the record.
Equalization is definitely something to apply. All modern record players automatically apply the RIAA equalization standard to dampen bass and boost treble. This helps improve the mastering process as high frequency tones are difficult to mold correctly and play back. Since I'm testing on a modern record player, I have to apply and invert the RIAA equalization curve so the record player will play it back correctly.
However, windup phonographs work acoustically and adding equalization will cause a tinny sound. Most recordings were not designed for acoustic playback. From Wikipedia:
- The maximum sound level achievable was quite limited, being limited to the physical amplification effects of the horn.
- The energy needed to generate such sound levels as were obtainable had to come directly from the stylus tracing the groove. This required very high tracking forces that rapidly wore out both the stylus and the record on lateral cut 78 rpm records.
- Because bass sounds have a higher amplitude than high frequency sounds (for the same perceived loudness), the space taken in the groove by low frequency sounds needed to be large (limiting playback time per side of the record) to accommodate the bass notes, yet the high frequencies required only tiny variations in the groove, which were easily affected by noise from irregularities (wear, contaminates, etc.) in the disc itself.
Keep this in mind if the end product is meant for windup phonographs.
"Go to Effect>Equalization and select RIAA. Hit inverse and apply, you should now hear the higher frequencies of your track boosted."
However, something else to look into is that prior to the adaption of the RIAA standard, different record companies had their own equalization standard. Sometimes you'd even see record labels advising you to use the company's own needles and phonographs for "perfect tone". The Audacity wiki has a plugin and a table for recreating various 78 equalization curves. This may be something to look into when trying obtain the best results when playing on an antique phonograph.
Regarding amandaghassaei's advice to add 2 sec of blank audio to the beginning and the end of the track, this is less necessary for 78 rpm as any silence will be stretched out and create several grooves of essentially blank data.
Be sure to export as a wav file in your "LaserCutRecord_78" test folder with the Python file.
Python
I had the strangest bug that I isolated to the Python file. Even though I set the Processing file to output at 78 rpm, the record cut from the file played at 45 rpm.
The sampling rate of the wav file was 22.05 kHz (you can check in Audacity). The sampling rate variable in the Python file was also set to 44.1 kHz.
Initially, I fiddled around with the settings in the Processing file, but they made little difference in the pdfs they outputted.
Eventually, I halved the sampling rate in the Python file to 22.05kHz. The pdfs immediately showed less compressed sound waves. I cut out a test record and played it at 78 rpm. Oddly, it sounded really slow even at 78 rpm.
I recorded it on my computer and sped it up in Audacity. I eventually figured out that it needed to be played at 90 rpm; twice as fast as 45 rpm.
I theorized that there was a relationship between the sampling rate and the RPM. I knew that the sampling rate that corresponded with 78 rpm must have been between 22 and 44 kHz.
If you recall your high-school algebra, knowing that sampling at 22.05 kHz plays at 90 RPM and 44.1 kHz plays at 45 RPM, the equation is as follows:
Assuming x is RPM and y is Hz
y = - 490*x + 66150
Plugging in 78.26 RPM for y (I live in a 60 Hz country)
y = 27802.6 Hz
I plugged this back into the Python file with frate = 27802.6
It worked perfectly at 78 rpm.
I'm not sure exactly where the problem is in the code, but if the sampling rate of your wav file is 22050Hz, your Python file should have the 28702.6 set as the frate in order for the record to play correctly at 78 rpm.
Test record cuts, therefore, are essential to see if your grooves are sketched correctly. As far as I know, there's no way to figure out whether your grooves are at the correct speed other than playing it. You can judge slightly by observing how compressed the sound waves are on the pdf from Processing.
Be sure to copy the name of the wav file to the line
fileName = "yourfilename.wav" #file to be imported (change this)
Hit Run > RunModule and you should have the .txt file saved to the same folder as the Python file after a minute or so.
Processing
Now open up the "LaserCutRecord_78test" folder with the Processing file inside. Copy the .txt file you just made to this folder.
Open up the Processing sketch. Don't forget to change the name of the file to be imported in the Processing sketch to your txt file name made in the previous step:
String filename = "yourfilenamehere.txt";
Run the Processing sketch by Sketch > Run. The Processing sketch will output several pdf files each containing the grooves for your record. The last file will contain the runout groove, spindle hole, and record outline.
I will focus on the "parameters" section as they pertain to this record.
You can modify the file sizes of each pdf file under "numGroovesPerFile". As previously explained, I had to limit it to 5 otherwise I would lose groove data during the transfer process and crash my computer due to the sheer number of data points. I also find it helpful to set it to a high number, such as 500, so a can examine the entire record at once. This can be useful to observe if the waves have been stretched out and are consistent with 78 rpm.
As previously explained, the samplingRate should be set to 27802.6.
cutterWidth and cutterHeight all depend on your cutting bed size.
Regarding record size, I modified it from the 12" record specifications to a 10" record. "diameter" is the record diameter while "innerRad" and "outRad" are the radii of innermost and outermost grooves. Confirm these against the RIAA standards page.
It's best to leave the "innerHole" alone and not make it any smaller. Acrylic is less forgiving than vinyl and shellac and it may get stuck on the spindle.
The main focus is getting the grooves to be a close as possible both to replicate 78 records and not to have the increased number grooves extend into the label area. Some record players have an auto return which makes it impossible to play the record past the label area due. The tonearm will automatically raise and return to the resting position.
The above pictures are test records in which I was attempting to move the grooves closer together. The last picture is a rather amusing test record that demonstrates how far the grooves would have extended towards the center if it had been completed.
The "spacing" variable was the main one that I modified. I currently have it to 2. "amplitude" also helps to reduce the space each groove takes up as it moves back and forth.
Many 78s and early vinyl records have a eccentric run out groove which would have activated the auto-return and disc-changer. It's probably easiest to recreate in your vector program.
A thing to note is that all the grooves should ideally be cut in one session. Shutting off the machine misaligns the grooves ever so slightly. It still plays, but can possibly mistrack.
Step 5: Testing
Numark PT-01
This record player is a sturdy little bugger and has the ability to play 3 speeds. Record stores typically use this model to let customers test out records.
amandaghassaei in her instructable appears to use an Audio Technica LP-120 in some videos and an Audio Technica LP60 in others. She experienced a lot of trouble with skipping and tracking during her tests. She probably used a needle meant for LPs during the tests. As I have previously demonstrated, the laser cut records have grooves that more approximate wider-grooved 78 shellac records. Since the needle sizes for 78s vs LPs vary by a factor as much as 4 to 1, having a small needle can cause it to ride at the very bottom of the groove or bounce around.
This particular turntable appears to have what is known as a ceramic cartridge with a diamond tip compared to the Audio Technica's magnetic cartridge. It tends to get a lot of flak because many cheaper turntables use it for its low-cost. Its response curve is much lower than a magnetic cartridge. In addition, the Numark uses a spring and a weight to regulate its tracking force which cannot be adjusted.
All this actually points in favor to getting sound out of this record. The needle tracks at a higher pressure which allows for the needle to stay in the groove and not skip.
For the following tests I used the stock needle that came with it as well as a needle advertised for 78s.
This is the stock needle that came with the record player. It did skip for quite a bit before the excess acrylic dust cleaned itself out. There seems to be a lot of high frequency background noise probably due to the "bumps" in Fig. 3. In this closeup of the underside of the grooves there's a sawtooth pattern visible due to the laser pulsing as it moves from point to point. I'm attempting to minimize this, but you can still hear them, but the smaller needle is probably sinking into the bottom of the groove and picking up the bumps as noise.The noise may also be partly exacerbated due to the fact that I'm using a point and shoot with the built-in microphone to film this.
The Numark appears to have a built-in safety feature where if the signal-to-noise ratio is too low, the turntable will slow down to prevent excess noise being sent to the speaker. The LP needle will demonstrate this phenomenon when the Volume knob is turned up and the record will slow down dramatically. Adjusting the Tone knob helps slightly to reduce noise which I fiddle with at the beginning of the video.
This is a needle that was marketed for 78s The audio here seems to be much cleaner since the needle is wider. In addition, I can turn up the volume and the record will not slow down.
Victor Talking Machine Phonograph Model No. VV-80
I was fortunate enough to find a working phonograph in a thrift shop and the shopkeeper was generous enough to let me record this test. I initially had problems with the needle catching on the acrylic which slowed down the record. I try to gingerly lift the tonearm so it settles in the correct position. You can see me fiddling with the speed control as the dial didn't correctly display the RPM. I mostly went by ear until it sounded correct.
This particular model is an internal horn phonograph. The horn is "hidden" by some swing doors in the front right below the top of the phonograph. You can open and close the doors to modulate how much sound you want. The doors are closed during this recording.
You can see the needle turning white from acrylic dust. I'm not sure if this is caused by the heavy reproducer gouging out the grooves or if the needle is cleaning out the dust that collected in the grooves during the cutting process. I tested the record later on the Numark again and I heard no audible difference.
Unfortunately, the camera ran out memory at this point, but I continued on my iPhone.
As you can hear, the phonograph is not picking up the high-frequency noise caused by the bumps on at the bottom of the grooves. This is probably due to the heavy reproducer which forcibly presses the needle to against a mica sheet to acoustically recreate the sound rather than electrically amplify it. Prior to RIAA equalization standards, many records have a lot of bass and little treble.
It is for this reason why old-fashioned phonographs are very hard on old records as they have very high tracking forces. In addition, the tip of the steel needle is ground away on the grooves (Fig. 5). Typical shellac records are mostly filler with abrasives to grind the needle into a correct shape. Because of this, needles ideally should be replaced after every play on a record (you can order them in packs of 50).
Step 6: The Record Label
My first inspiration to embark on this project was the appearance of a grainy black and white vision of Albert Fink's record sleeve. I already had access to the record label that played in the phonograph. (Figs. 1-2)
However, I realized that this was an exact replica of an actual record label. (Fig. 3)
It's literally adapted from a scan of a specific record label similar to the one on this page. Even the marks around the spindle hole are identical.
The E. Berliner was what gave it away. Emile Berliner was the pioneer of making flat-disc records. Edison had already come out with his phonograph that first made recorded music available to the masses on wax cylinders, confusingly called "records" at the time (some of Infinite's soundtrack comes on cylinders). Berliner's "gramophone" proved that music can be made on flat discs, allowing faster replication and easier storage. Although, cylinders technically had better sound fidelity, since the grooves were of a fixed diameter compared to a flat record's ever decreasing spiral, flat records won out since they were cheaper to produce.
Partly due to circumvent copyright, Berliner called his invention the "gramophone" in contrast to Edison's already established cylinder "phonograph". In the past, gramophone was used specifically to refer to Berliner's disc record player and phonograph for Edison's cylinder player. Now it seems that phonograph and gramophone are somewhat interchangeable similar to the American "elevator" and the British "lift". Typically the use of the names refer to the old crank models, however many audio receivers have a "phono" input. What seems to be in vogue nowadays is "turntable", but "record player" is a good umbrella term.
Edison, as you probably know, was a genius for having introduced recorded sound, but a terrible businessman. He stubbornly held onto the cylinder business. Eventually he gave in and created Edison Diamond Discs. He marketed them as being unbreakable since they were obscenely thick compared to a thinner shellac records. Also, probably partially due to pique, he made the records vertically cut and manufactured phonographs than could only play his discs and while other discs could not be played on his machine and vice versa. Again, the vertically-cut records had arguably better sound, but the record company only lasted 17 years partly due to Edison's stubbornness to include popular artists in his discography, preferring to choose those which suited him. (I'm slightly relieved that Infinite's soundtrack does not have a Diamond Disc recording)
Back on topic, the two record labels are identical save for the "Albert Fink's Magical Melodies" and the "Improved Berliner Gram-o-Phone". It's a pity since the other record information makes no sense in Columbia. "E. Berliner" is still visible and every record in Infinite proclaims that it is a recording of "Ah! La Femme Il N'y A Que Ça" sung by a "Mons. A. Fertinel".
However, I tried to match fonts and made two versions, the original in a vectored form (Fig 4), and an adaptable one more suited for Columbia. Assuming Albert Fink also stole Berliner's technology (Gettit? "A. Fink") I have versions for every anachronistic cover in-game and I modified what would be the catalog number into the year of the original recording.
Getting the label to stick to the slick acrylic surface is somewhat of a problem. Labels were never glued on records. They were pressed directly into the shellac/vinyl when the record was formed. I ended up cutting out the label and the spindle hole with an X-ACTO. I placed the record on a record player and aligned the label on the spindle. I've tried spray glue to make it stick, but it peels eventually with rough handling. Rubber cement and school glue seem okay. Once in place, I piled some books on the label to get it to dry flat. Next time I might try etching lines in the dead wax area to get the label to stick with more traction.
Step 7: The Paper Record Sleeve
This was one of the more elusive bits of my research. I knew that shellac records usually came in paper sleeves that advertised the company name (a far cry from the catchy album art of LPs that proclaimed the artist). I was disappointed that Magical Melodies in Emporia did not seem to have any records, apart from the one on the phonograph.
Then when Clash in the Clouds DLC came out, I noticed one in the foreground of the “Magical Melodies Sweep Columbia!” unlockable kinetoscope at 1:49
Fig. 1 is an "enhanced" version
This was little to go on, but I attempted to make an early mockup based on elements from the game and sampling colors from the logo. (Fig 2-4)
I knew that something was off since typical 78 rpm record sleeves from the time period were made from brownish kraft paper with few colors.
http://home.earthlink.net/~gnordenstam/RecordColle...
http://www.nfsa.gov.au/collection/sound/art-early-...
But there was little I could do since it was in black and white.
Then I was looking through some early gameplay teasers and found it.
http://www.ign.com/articles/2013/03/12/the-music-o...
There's a record stand in front of the float where the barbershop quartet sings. This seems to be rather late in the development phase as the location is identical except for that record stand. The sign still advertises the "BEE Sharps" instead of "Albert Fink presents". This was probably dropped due to a Simpsons reference.
Figs. 5-6 are stills from the video:
It's a bright pink and the difference is startling, so I updated my mockup. (Fig. 7)
I also realized that it appears to be directly inspired by the UK version of a period Columbia Record sleeve. Note the "Britain, Éire, Australia, and New Zealand" at the bottom and the "Manufactured in England". (Fig. 8) Oddly, this record company seems to come up again and again.
I realized the blank space at the bottom was for copyright info so I modified that to fit into Columbia.
Finding the paper similar to this was a bit difficult. I ended up using a brown kraft paper similar to that used in paper grocery bags. I got some at an office supply store as "craft paper". You may find it as packing paper.
Finding a printer (since record sleeves are a non-standard size of 10"x10") who would print on this stock was also difficult as they wouldn't take mine and they didn't have any similar stock. I eventually found a mom-and-pop print shop that would and they did a great job. Note, FedEx and Kinko's only like really straightforward stuff.
The sleeve pattern is really simple. Essentially, it's a 10" X 20" sheet that's folded in half. The sides of the sleeve have flaps to form an envelope.
I think it came out pretty well compared to what evidence I have. (Fig 9)
I was not able to find the texture in the game's files, odd since there are a ton of unused assets like the Gibson Girl Elizabeth and a Resurrection Device. I would love to get access to this texture file to confirm details. Additionally, the record label appears to be slightly different from the Berliner label, but the details are too vague to make out. I can just see "Magical Melodies" whereas the Berliner label has "Albert Fink's Magical Melodies".
Step 8: Further Thoughts, Improvements, and Criticisms
1) Get some black acrylic: Clear was the only stock that the shop had. Or perhaps Delrin so the needle doesn't catch as much.
Although I did not experience severe warping like amandaghassaei, I observed some cupping when some records were finished. I'm not sure if this is due to the grooves slightly collapsing through the sheer ablation of material or because I cut some grooves out of order. Thicker material may help to resolve this
2) Improve signal-to-noise: This is probably fixed by fiddling with the parameters in the Processing sketch. Additionally, I'll try to minimize the sawtooth pattern caused by the pulsing laser.
3) Decrease cutting time: No-one wants to wait 10 hours.
4) Possibly gain access to the clean versions of the anachronistic songs and the sleeve texture? Maybe in Burial at Sea Part 2?
5) Experiment with non-RIAA equalization: As previously mentioned, for best results Columbia records sound best with Columbia needles.
I would like to be able to make better and more gramophone records. I'm currently saving up money to purchase my own phonograph, but the Numark will do for now.
For this reason, if there were to be another record of the Bioshock soundtrack, possibly with the Albert Fink's Magical Melodies record label), it would be inappropriate to the time period of Infinite not to make it a 78 rpm record at least. Shellac is a nice touch, but few companies still make them. Cylinders would be awesome though.
This instructable could easily be adapted to make any gramophone record. Once I'm finally able to purchase an actual phonograph, I can begin testing in earnest and find the ideal settings
Additional possibilities:
Make songs available on 78 RPM
Some songs in Bioshock were never released commercially on records during the artists' lifetime. Django Reinhardt's and Stéphane Grappelli's "La Mer" (one of the major themes from the game) was only recorded in Rome in 1949 for radio broadcast (Reinhardt died in 1953). Mario Lanza's "Danny Boy" was part of a larger radio broadcast.
In Fallout, Bob Crosby (not to be confused with his more famous brother Bing) recorded "Dears Hearts and Gentle People", but again it only exists on a 16" radio transcription record and was lost until the transcription was discovered.
So I hope to bring these songs into existence on an actual record again.
Cardboard records
Do you think that amandaghassaei was the first to think of cutting records on paper? Think again.
Records were pressed as early as 1930 on cardboard-like stock (technically resin on cardboard) for very cheap (they sold on newstands for 15 cents a pop)
Take a peek at Sam Lanin pressed on a Hit of the Week cardboard record.
Cylinders
Edison's first cylinder phonographs recorded on sheets of tinfoil wrapped around a cylinder. Unfortunately, the tinfoil had to stay on the cylinder for playback. Once taken off, the tinfoil couldn't be played again. This gave way to the more permanent "wax cylinder" would could be mass-produced (the wax eventually gave way to celluloid, but the name endures).
Although most cylinder phonographs had a recording function and a playback function (you reduced the amount of weight on the needle to playback), you could possible adapt the tinfoil technique to laser cut some songs. The grooves have to be arranged in lines rather than a continuous spiral. Unfortunately, as far as I know, it's not possible to make my machine cut on a continuously rotating cylinder.
Other Unusual Records
Some early records were made out of exotic materials such as rubber, glass, and even chocolate. Only some materials can be cut on a laser cutter.
The run out groove could possible by cut to have a infinitely repeating sound bite.
Intertwined grooves: Puzzle records existed which had 4 songs hidden on one record. Other novelty records included a horse-racing record which would announce different results depending on where the needle was dropped. this could be replicated with some clever spacing and rotation of the grooves.
Other Bioshock Records
Rapture Records
Although there was a record store in Bioshock 1, no records actually were present on the phonographs. For some reason, the needle still "scratched" when they were picked up with Telekinesis. We did see some wonderfully generic record sleeves in the store.
Bioshock 2 had a pretty nice version of the Rapture Records label. Some are found in Grace Holloway's room.
Infinite had a Rapture Records Easter egg hidden in the phonographs in the Lutece Labs and in Comstock House. Naturally it's also present in the Rapture Records in Burial at Sea.
It's different from the one in Bioshock 2. Unlike Bioshock 2's, Infinite's has no place to put record information such as artist name and song title.
Strangely, the Magical Melodies label from Columbia can be seen on the phonograph and in the display case in the Rapture Records store in the Burial at Sea DLC.
Audio-Log: Fink Industries
There's also a record label on the Voxophones. Funnily enough, it has a very large center hole. This may be a reference to how unscrupulous turn-of-the-century record companies would sell a record for really cheap, but with large center holes. They would then sell the adapters so the record could fit onto regular sized spindles at absurd markups. Otherwise, the consumer would have to purchase record players made by the company, but could only play that company's records.
Seems right up Fink's alley
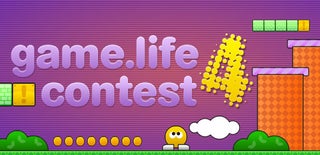
Participated in the
Game.Life 4 Contest