Introduction: Make a Plywood Portrait Monitor Stand
Working with a lot of PDFs, Word and Publisher documents and various IDEs can be difficult on landscape monitors, however mounting a monitor in portrait orientation can be expensive when you don't want to drill into the wall as the cheapest desk mounting VESA mount I found was still around £40-50, which was a little over my budget.
So I designed a simple stand which was easy to make using parts left over from one of my other projects.
Step 1: Prepare Your Monitor
Firstly, this works best with monitors which have the VESA mount directly in the centre, if it is towards the top of your monitor then it is likely the manufacturer doesn't want you to use it in portrait (I'm guessing cooling related as the monitors I have seen like this produce a lot of heat, and using a monitor in portrait orientation reduces the convectional airflow through the monitor, as the vents are on the top and bottom).
Next you want to remove the stand from your monitor, this can take a lot of brute force, but it's always best to check with the manual in case there are some little catches you may have missed, in my case even after I had removed the stand there was still a part of the hinge sticking out from the side, but I think I can live with it.
I am lead to believe that some monitors will also allow you to rotate the on screen display for using it as a portrait monitor, I haven't been able to find this option on my monitor, but it isn't often I use the OSD on my monitors anyway.
Step 2: Design Your Stand
You will want to check what VESA spacing you have, usually it will be 75x75mm for monitors smaller than 22", but could also be 100x100mm on larger panels, this is important as this will determine how the screw holes will be spaced out on the panel that will hold the monitor, the monitor I used had a 75x75mm VESA mount.
You will also want to determine the hight from the desk to the VESA mount, this will vary depending on what size of monitor you have, how high your desk is and various other ergonomic stuff, but it's easier just to hold the monitor portrait and see what hight feels right.
You can then use this information to design any style of stand you like.
Step 3: Cut Plywood Panels
Once I had designed each of the panels needed, the original plan was to use a CNC router to cut them out, however I decided to use up the spare materials from other projects I would laser cur a router template and use a router in a router table (essentially a spindle moulder) to cut the parts.
I used a staring bearing guided cutter to cut each of the parts, and held the template onto the plywood using double sided tape.
Step 4: Cut Aluminium Tube
I cut each of the Aluminium tubes to length on a metal turning lath using a parting tool and the digital readout on the lathe, removed the sharp edges using wet/dry paper and finally polished them on a buffing machine.
I also cut some small lengths of Acrylic tube to be pushed inside the Aluminium tube, this would help the 10mm Aluminium tube sit centrally on the 6mm threaded bar.
Step 5: Assemble
The final step is to assemble the stand, to do this I first used PVA glue and some small nails to fix the square which holds the VESA mounts to the two side panels, using the Aluminium tubes as a guide to ensure the spacing is correct.
Once that was set I added the Aluminium tubes, this was done using a penny washer on each side of the side panels and a dome nut on each end of the M6 threaded bar.
Then the base was attached using wood screws through the base and into the two side panels, take care here not to split the side panels or miss them completely when drilling pilot holes through to them.
The last step is to take some M4 screws and shorten them so they can be used to hold the monitor in place, then the monitor can be screwed on to the stand using a single washer at the back and a few on the front to ensure the monitor can stay cool.
Ill go on to the base of the stand in the next step, as this had to be changed due to a design flaw.
Step 6: Further Modifications
When I assembled the stand and tried to use it with my monitor for the first time I found that the fact that the two foam "feet" protrude mainly in the centre of the base meant that it was very unstable, so I modified the base by drilling four 40mm holes in each corner and placing an extra foam disc in each one, protruding slightly more from the base than the two in the middle of the base, this helped to solve this problem.
The foam discs were cut using a laser cutter and held in place using double sided tape.
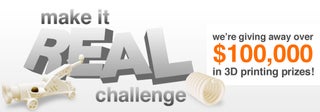
Participated in the
Make It Real Challenge
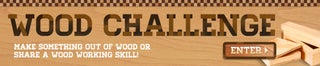
Participated in the
Woodworking Challenge