Introduction: Make an Adjustable Knitting Loom
This multi-tasking loom is my DIY version of the commercial All 'n one knitting board It seemed like an easy wood-work project and looms in general are expensive and fairly hard to come by down my side of the woods.
Using the 2 small spacer blocks it is possible to use it as a knitting board, either single knit or double knit and using the pegged spacers it is a variable peg round loom.
Step 1: Materials and Tools
I had some left over pallet planks and decided to use that, which in hindsight wasn't really a good idea, the DE-HT (Denmark- heat treated) pine is soft and all the pulling and tugging tends to loosen the pegs.
I used:
- 2 x 20mm² x 406mm (16inch) lengths of pine that I jig sawed out of a pallet plank.
- 2 x 90mm long M6 stove bolts and wing-nuts.
- 2 small spacer blocks 20mm² x 20mm long.
- 2 larger pegged blocks 20mm² x 37mm long.
- 2m of 5mm dia dowel for the pegs.
- a pack (300) of plastic beads 8mm OD 4.4mm ID
- 2 x M6 fender washers which I squared off to use as the metal sliders on the sliding block.
Rather use a hard wood for the dowel, bamboo skewers tend to splinter very easily and pine is too soft and easily damaged by the metal loom hook.
Tools
- Drill press is a must for the vertical peg holes.
- Jigsaw if you are using a larger plank and need to cut the frame pieces out.
- 5mm drill bit.
- Tape measure
- a small length of broken hacksaw blade to cut the slots in the frame and pegs.
- Optionally, a router with a small bit is another less labour intensive way of grooving the side rails
The usual cautions apply when using power tools, eye n ear protection.
A drill press can slap you wide awake with a 16inch pine batten if you're sleeping and forgot to clamp the work piece down.
Step 2: The Making of the Pegs
The plastic beads had a 4.4mm ID so I used a 5mm dowel and sanded it down after failing to drill the tiny beads wider for the 5mm dowel.
I used 2 fender washers for the sliding part but suitably worked pieces of hacksaw blade would work just as well.
I started by scoring the dowels with a makeshift jig to have a suitable guide for the hacksaw blade.
I used a 30mm peg length with 10mm sunk into the frame, it makes for a good 20mm workable peg length.
Step 3: The Frame Pieces
I decided on a 66 peg loom with the 2 header pieces being 3peg sections, the spacing was to be 12,7mm (1/2 inch) which meant the side rails needed to be 406mm long (16 inch).
The groove was cut with a hacksaw blade piece which turned out a bit on the small side, so it was enlarged with a jigsaw blade held in a visegrips. I see the commercial version has a routed groove in the side rails which might be a less labour intensive route if you have such a power tool. The grooving of the side rails and the pegs was easily where the bulk of the project time was spent.
The spacing is a bit on the small side for these size beads and I'll probably increase it to 15mm in the future.
The whole project took about 8 hours over 2 days and cost about $5, $3 for the beads and $2 for the stove bolts, the rest was lying about the garage.
Step 4: Alternate Method
This is how I should have done it the first time around, hardwood rails and routed grooves. I'm using 13mm x 19mm meranti and 5mm oak sliders to fit the 5mm routed groove.
Once again I'm doing a 66 peg loom but with 15mm peg spacing this time,this means a longer 472mm loom instead of the previous 406mm version.
I used this project as a reason to upgrade my drill press, theres nothing nicer than working with the proper tools for the job. I started out by printing templates to scale to tape to the wood, the cross-hair laser and fence stop made it a quick 5min job.
The routed 5mm groove took a bit longer due to the need for 2 passes per rail to stop the bit from burning the wood, 15min and all was done.
The pegs were recycled from the pine version 1, nothing was glued on both occasions, once again small spacer blocks can be used to convert this loom into a 60 peg knitting board.
Step 5: Loom Hook
Its tricky using the loom without the loom hook and after a sore palm using the short commercial version I decided to make my own longer one.
The shorter plastic version that's included with a commercial loom is a bit on the short side and digs into my palm.
I dug out a 5cm length of 2.5mm steel and after sharpening it on the bench grinder, gave it a little heat treatment with a lighter. Next it was sanded smooth with 800 grit wet and dry paper and forced into a length of 10mm dia hard wood dowel. The dowel received a 2mm pilot hole for the metal hook and a good sanding all round.
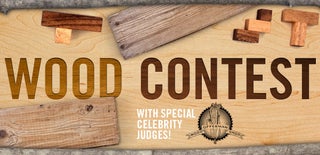
Participated in the
Wood Contest