Introduction: Maker Station: the Portable Reconfigurable Work Station for All Makers
In this Instructable I will be teaching you how to build a maker station of your own, I'll cover The various tools and materials you will need, I'll discuss the concepts and designs that influenced the final product, and then I'll walk you through the build process so that you'll have all the information needed to successfully tackle this project. Along the way I'll share tips and tricks I learned during the build so that you can hopefully avoid some of the obstacles I tackled while building my Maker Station.
Features of the Maker Station
-Interchangeable center table sections that can be customized to the task at hand.
-Built in floor that is attached to the Maker Station so your body weight holds the station firmly in place while you work.
-33" high work surface which is an great working height for both standing and seated tasks.
-Internal storage space for tools and materials.
-Custom tool storage racks that can be mounted on the out side of the Maker Station for easy access to your tools, and on the inside for easy storage and transportation.
-The Maker Station collapses into a 30" X 33" X 12" rectangle for easy storage and transport, (small enough to fit in the trunk of most standard sized cars.)
-Built in wheels for easy transport.
-Built in collapsible super bright LED work light .
-6 Outlet Power Strip.
-Made from hard wearing maple faced plywood for strength and durability.
-Total weight is a sturdy 80.5 lbs (36.5kg.)
Step 1: How It Works
The steps from closed to open
- Unfold the front and back panels
- Fold the back panel underneath the Maker Station
- Flip the Marker Station over onto the floor
- Fold up the table leaves and lock them into place
- Unfold the leg supports
- Unfold the light and use the hand screw to fix it in place
- Attach the tool racks and add a chair.
- make something awesome.
Step 2: Tools and Materials
Qty | Material Description | Unit Price | Total |
Wood | |||
1 | ¾” Plywood (4’ X 8’ Sheet) | $53 | $53 |
1 | ½” Plywood (2’ X 2’ Sheet) | $7.50 | $7.50 |
3 | 2” X 4” (8 Feet Long) | $2.50 | $7.50 |
Hardware | |||
4 | 3” Butt Hinge | $3 | $12 |
8 | 2” Butt Hinge (sold in packs of 2) | $2 | $16 |
2 | ¾” Cabinet Hinge | $3 | $6 |
1 | Cabinet Handle | $1 | $1 |
4 | 3” Rubber Casters | $3 | $12 |
2 | Spring Toggle Clamps (sold in packs of 2) | $3 | $6 |
1 | Lid Support | $6 | $6 |
Fasteners | |||
1 | #8 - 1 ¼” Wood Screws (Box of 50) | $6 | $6 |
1 | #8 - 2” Wood Screws (Box of 50) | $6 | $6 |
8 | ¼” X ¾” Lag Screws | $0.15 | $1.20 |
8 | ¼” X 2” Lag Screws | $0.20 | $1.60 |
8 | ¼” X 1” Fender Washers | $0.10 | $0.80 |
1 | 1/4"-20 4 Prong Tee Nut | $2 | $2 |
1 | ¼” X 2” bolt | $1 | $1 |
1 | ¼” Plastic Screw Handle | $3 | $3 |
1 | Screw On D Ring Picture Hangers (4 per pack) | $3 | $3 |
1 | Medium Screw Hooks (10 per pack) | $3 | $3 |
Other | |||
1 | 13” Low Profile Under Cabinet Light | $24 | $24 |
1 | Adhesive Velcro | $8 | $8 |
1 | Normal Velcro | $4 | $4 |
1 | 6 Outlet Surge Protector | $10 | $10 |
1 | 1 Bucket Tool Organizer | $7 | $7 |
1 | Wood Glue | $3 | $3 |
1 | Masking Tape | $2 | $2 |
1 | Wood Finish (Linseed Oil) | $8 | $8 |
Total | $220.60 |
Tools
Table Saw
Dado Blade Set
Power Drill
Phillips Driver Bit
1/4" Forstner Bit
1/4" Plug Cutter
1" Forstner Bit
Countersinking Drill bit
Plunge Router
1/4" Straight/Plunge Router bit
Wood Chisels
Flush Cut Hand Saw
12" Clamps
Power Sander/Sand Paper
Measuring Tape
Combination Square
Cloth for Applying Finish
Step 3: Design
Design was definitely the most difficult part of this project. As stated in step 1, I wanted to create a mobile work station that could be useful for a variety of different tasks and and useful to a variety of different artisans/makers, so there was a great deal of consideration put into things like the height of the work station and the ability to switch out the middle section of the table so that the work space can be customized to the needs of the maker and the job at hand. I also spent a good bit of time on considerations like how to incorporate lighting, which we all know is one of the most important parts of any good work space, (you can't make if you can't see what you're making right?) Lastly, once I had figured out how to incorporate all the necessary attributes, and how to make it customizable I had the task of making it collapse into a nice neat package so that it would be easy to transport whether you're moving it around the house, or loading it into a car to take to an arts festival or demonstration.
To work through the design issues listed above, as well as some others such as how the front and back would fold and join to create the floor so that your body weight will hold the table firmly in place, I created a series of drawings and doodles which I then turned into 3D models via Google Sketchup. Creating models of the maker station was very beneficial as it allowed me to see my finished product and to make adjustments before I ever started actually building the thing. By creating the models I was able trouble shoot errors before they were made so that I wouldn't waste time and materials needlessly. As an added bonus I built the models to scale meaning that I was able to pull all of my part measurements directly from them.
Check out the Google Sketch Up model here:
SketchUp: Maker Station
As an added bonus, once I had the finished models I was then able to arrange the parts in such a way that the entire maker station could be cut from a single sheet of 3/4" plywood and three 2 by 4's leaving very little scrap material, check out the parts diagrams in the next step.
Step 4: Cutting the Parts
Three 8' long 2X4's
The first step in building the Maker Station is to cut the various parts from the 3/4" plywood and 2X4's. Pictured above are diagrams of the various parts that need cut and their measurements, these are the same diagrams I used when creating my Maker Station and I am happy to report that all the parts lined up well and worked out perfectly. (I included a metric version of the parts list for all you lucky people out there who didn't grow up with Imperial measurement system).
Tip: If you're like me and don't have a vehicle large enough to haul a full 4' X 8' sheet of plywood fear not. I designed the plywood parts layout so that you can have the sheet of plywood cut into four sections at the hardware/home improvement store without damaging any of the parts. See the picture above for an example of how the sheet can be broken down for easy transport.
Step 5: Building the 2X4 Frame: Cutting Half Lap Joints
Two 30" 2X4 cross beams
With all the parts cut, the first step of building the Maker Station is to create the 2X4 frame that all the other parts attach to. Start by cutting a half lap joint into one end of each of the legs and into both ends of the cross beams as shown in the picture. To make these cuts, install a dado blade set into your table saw and set your blade height so that it is exactly half the thickness of a 2X4 (roughly 3/4" because a 2 X 4 is actually 1.5 inches thick). Next set your rip fence so the distance from the outside edge of the dado set to the fence is exactly equal to the width of a 2X4, (roughly 3.5"). With everything set, use your miter gauge to pass the boards over the saw blade while one end is butted against the fence, This will establish the back of your half lap joint. After the back of your half lap joint is created, continue running the boards back and forth over the dado set until you have created each of the half lap joints.
Once all of the half lap joints have been cut the next step is to join the legs and cross beams together to make the front and back of the Maker Station frame. Consult the pictures to see how the pieces should be assembled, and use the wood glue and 1" wood screws to fix everything in place.
Step 6: Building the 2X4 Frame: Assembling
Two 30" 2X4 cross beams
Wood Screws
Nine 4" long 2X4 Spacers
How you position the spacers is important as their placement determines how and where the LED light and casters will be installed later on. Consult the included picture for an idea of where the spacers should be placed.
Lastly, once everything is in place, you will be using the 2" wood screws to attach the spacers to the two U shaped leg and cross beam pieces. When I built my Maker Station I didn't want all of these screw heads to be visible so before I screwed the spacer in place I used a 1/4" Forstner bit to create counter bores on the faces of the U shaped pieces where the screws would go through. I made the counter bores about 3/16" deep so that later on I could insert wooden plugs over the screws to hide them from view, (check out step 19 for information on creating and installing the wooden plugs.)
Step 7: Attaching the Bottom to the 2 by 4 Frame
3/4" Bottom (30" X 8.5")
1/4" X 2" Lag Bolts
1/4" X 1' Fender Washer
After you have finished building the 2x4 frame of the Maker Station, the next step is to attach the 3/4 plywood bottom (30" X 8.5). This bottom should be attached using the 2" long 1/4" lag screw and fender washers. Because this bottom will be what the Maker Station sits on you want to make sure that the heads of the lag screws don't stick out, so use a 1" Forstner bit to create counter bores deep enough to house the lag screw heads and washers. Once the counter bores are created, pre-drill holes for the lag screws so that the legs don't split when you're screwing them in place.
Note that the Maker Station frame should be exactly 7" wide and that the bottom is 8.5" wide. The additional with of the bottom will provide room for the leg supports that will be added later on, so for now make sure that the bottom over hangs each of the sides 3/4" (see picture).
Step 8: Attaching the Center Table Top to the 2 by 4 Frame
3/4" Plywood Center Table Top (30" X 7")
3 Toggle Clamps
Step 9: Attaching the Table Leaves
Two 3/4" Plywood Table Leaves (30" X 12")
Four 3" Hinges and Screws for Attachment
Step 10: Adding Cross Braces and Table Leaf Supports
Two 3/4" Plywood Cross Braces (26" X 3")
Two small scraps of 3/4" Plywood (at least 3"X 1.5")
Wood Screws
Two 3/4" Table Leaf Supports (18"X 3")
Two 3/4" Cabinet Hinges
Start this process by affixing a block of 3/4" plywood to the center of each of the cross braces. the block should be approximately 3" long and about 1.5" high; this block will be what the leaf supports rest against to hold the table leaves in the extended position.
Next, with the Maker Station still sitting upside down on a flat surface measure up from the underside of the table leaves 13" and make a mark on each of the four 2X4 legs. These marks are where the cross beams should be installed, (see the picture for a visual representation). Use the 1" screws to fix the cross beams in place.
Once the cross braces are screwed in the next step is build the leaf supports. the leave supports consist of the plywood part you cut earlier (18" X 3") and a 3/4" cabinet hinge. The plywood leaf supports get a 45 degree cut on one end and the hinge installed on the other. They are installed as shown in the picture, ( to determine where they need to be installed push the 45 degree end of the leaf support firmly up against the block you attached to the cross brace and position the end with the hinge against the underside of the table leaf. Mark the hinge installation holes and screw the hinge in place. because the table surface of the Maker Station is registered against the flat work surface the table leaves should be perfectly level with the center of the table after leaf support installation is complete.)
Step 11: Making the Back Panel
3/4" Plywood Back Panel B (30" X 9.5")
Two 2" Hinges
Step 12: Attaching the Back Panel
Maker Station Assembly
Two 2" Hinges
Note: up until this point the Maker Station hasn't had a determined front or back, when attached the back panel assembly determines what will be the front and back of the Maker Station so if you have one side that you want to be the front for a particular reason make sure you take that into consideration when you attach the back panel assembly.
Step 13: Making the Front Panel
All of the 2" Trim boards
Wood Screws
Wood Glue
Note: I didn't want the screws that hold the trim pieces to the front panel to be visible, so I counter bored the screw holes using a 1/4" drill bit, (just like I did for the screw holes in the frame,) in preparation for wooden plugs that will be inserted at a later time.
Step 14: Attaching the Front Panel
Front Panel Assembly
Two 2" Hinges
Note that it is easier to attach the front panel if you have folded the back panel underneath the Maker Station (again, as shown in the picture.) Flipping the back panel under the Maker Station raises the height of the station's bottom so that the the front panel lines up perfectly with the bottom.
Note: Once the front and back panels are attached there will be nothing to hold them in the closed position (later on, after finishing, industrial strength Velcro will be installed to accomplish keep the panels held closed.) Until then the panels can flop around and can potentially come down with enough force that they could cause injury or rip the hinges out that hold them in place. To remedy this problem, use clamps to hold the front and back panels to the legs of the Maker Station. The clamps will securely hold the panels allowing you to flip and turn the station while doing things like installing the wheels or the LED light.
Step 15: Adding the Leg Supports
Four 3/4" Plywood Leg Supports ( Triangular 18" X 8")
Eight 2" Hinges
First, remember back to the step where the bottom was attached to the Maker Station (Step 7). when the bottom was attached there was 3/4" overhang on each side; this overhand will be where the leg supports sit when they are in the closed position. the problem is that the 3/4" leg supports plus the thickness of the hinges will be to thick and will cause issues when trying to fold everything up. The solution is to mortise the hinges into the leg supports so that the supports sit flush with the legs when they are folded closed; (see the pictures for information on cutting the mortises and installing the hinges).
Second, as the leg supports swing out into place they can catch on the hinges that attach the front and back panels to the bottom of the Maker Station, to keep this from happening I routed the bottoms of the leg supports to provide clearance so that they can easily clear the hinges. To create this clearance I used a router with a 1/2" straight bit to cut a 1/4" deep gap in the middle of the bottom of the leg supports. See pictures for a visual representation.
Step 16: Adding the Wheels
Two 3/4" Plywood Wheel Supports (12" X 4")
Eight 2" Lag Screws
4 Casters
Sixteen 1" Lag Screws
Start by affixing the casters to the wheel supports (12" X 4") as shown in the pictures. Note that I added 1/2" plywood spacers to the wheel supports because the lag screws I bought for installing the wheels were a bit to long and would have poked out through the top of the 3/4" thick wheel supports. Once you have the casters attached to the wheel supports use the 2" long lag screws to attach the wheel supports to the Maker Station frame. As you can see from the pictures the wheel supports are installed a few inches from the top and bottom of the Maker Station, this was to help with stability and the process of rolling the station off of the wheels and onto the bottom when you are ready to set it up for work.
Note: Remember that there is a specific side for the wheels and a specific side for the light, make sure you attach the wheels to the right side, if you can't remember which side is which take a look back at the pictures on step 1.
Step 17: Building the Light
3/4" Plywood Light Arm #2 (26" X 3.5")
3/4" Plywood Light Arm #3 (22" X 3.5")
Two 2" Hinges
Utilitech 13" LED Under Cabinet Light
Rockler Trunk Lid Support
Making the light can be a bit of a confusing process because you are going to be switching back and forth between the various light arm parts to make sure everything fits together perfectly. Here are the main things you need to know before we get started.
- The light gets mounted onto Light Arm #3 (the 22" long one).
- Light Arm #3 gets a shallow channel cut into one end to accept the cord from the light.
- Light Arm #2 (26" Long) gets cut apart and reassembled so that there is a rectangular shaped hole in the middle of it. (This hole is where the light goes when everything is folded up.)
- Once Light Arm #2 has been cut apart and reassembled Light arm #1 (3.5") gets glued to one end of it.
- The first step in building the light is to cut apart light arm #2. Start by cutting a 1" wide strip from each of the long sides so that you have two 1"X26" long strips. This will leave you with a middle section that is about 1.5" wide and 26" long.
- Now take that middle section and cut it apart so that you have a piece that's roughly 4" long and another piece that's about 8" long. With those two pieces cut you can add whatever is left to your scrap bin.
- Now glue the four pieces you just made together as shown in the picture to reassemble light arm "2.
- glue light arm #1 to the end of light arm #2 where you used the 8" long middle piece.
- While the other pieces are drying, take light arm #3 and cut a 1/4" wide groove that's about 1/4 deep in the middle of it. Note that this groove doesn't extend across the entire length of the board; instead it only goes in about 5 or 6 inches. This is done by running the board over the table saw blade and stopping after you've cut roughly 5 inches in, (check out the picture to see what I mean.) After you've made one cut back the board off the blade, more your fence over slightly and make another pass to increase the width of the gap, to make sure that all of my cuts ended at the same place I used a stop block clamped to the fence, again, check out the picture to see what I mean.
- Next, install the light onto light arm #3 so that it is centered and so that fits in the open area created in light arm #2. Remember to install the light so that the cord is on the side with the groove.
- Now use a 2" hinge to attach the end of light arm three that is grooved to the end of light arm #2 that isn't glued to light arm #1. Tip: make sure the cord is in the groove in light arm #3 before you screw the hinge in place, otherwise you will have to remove the hinge to install the cord.
- Good job so far, with all the light arm pieces attached the only thing left to do is to attach the lid support to one side of the assembly. This support will be what holds the light up when it is in the open position, (kind of like the hinge that holds the legs of a step ladder apart).
With the light assembly built, the next step is to attach it to the Maker Station, continue on to step 18 to learn how to do so.
Step 18: Installing the Light
Light Assembly
One 2" Hinge
One Threaded Insert
One Hand Knob Screw
Alright, With the light built, the next step is to attach it to the Maker Station. Thankfully attaching the light is a much simpler task than building the light.
Start by locating the side of the Maker Station where the light will be installed, you can reference the pictures on the first step to help with this. Once you've found the correct side, install a 2" hinge as shown in the picture, note that the hinge is mortised deep, similar to how the hinges were mortised on the leg supports. With one side of the hinge attached to the Maker Station, attach the other side to the light assembly as shown in the picture.
Next, flip the light up (like how it would be if it were in use) and drill a 1/4" hole through the light assembly so that you tag the Maker Station with the tip of the drill bit, this hole will be used to installed the 4 prong T nut thread insert and hand knob screw that holds the light in place while in the up position. Note, make sure that you drill the hole high enough so that you don't come in contact with the hinge plate that holds the light assembly to the Maker Station.
With the hole drilled, install the 4 prong T nut threaded insert, pass the hand knob screw through the light assembly and give it a few turns to lock the light into place. when you want to close the light simply unscrew the hand knob and allow the light to swing into place between the legs of the Maker Station.
Note: After finish has been applied, double sided Velcro will be added where the light folds closed so that it doesn't inadvertently swing open. Also, a Velcro strap will to the small space left at the bottom of the cavity that the light folds into so that the light cord can be wrapped up for storage. Check it out on step 21.
With the light installed the major construction of the Maker Station is complete, from here on out I'll be covering finishing touches, applying finish, and making accessories for the Maker Station.
Step 19: Finishing: Plugging the Screw Holes
Wood Glue
Plug Cutter
Flush Cutting Saw
Sand Paper
With the major assembly of the Maker Station complete it's time to shift focus to finishing. If you remember back to steps 6 and 13, I discussed how I counter bored the screws holes I drilled so that wooden plugs could be installed later on to cover up the screw heads. Well now it's time to talk about those plugs, how they are made, and how they are installed.
To make the plugs you need a plug cutter that cuts plugs the same size as the diameter of the counter bores you drilled, (in this case 1/4"). Plug cutters can be bought from retailers like Sears, Amazon, Woodcraft, etc.
Chuck the plug cutter into your drill just as you would a drill bit. Next position the plug cutter on whatever material you wish to use to make your plugs, in this case I chose to use a scrap of red paduke, an exotic hardwood with a beautiful bright red color. Start your drill and apply gentle downward pressure until the plug cutter has cut 1/8" to 3/16" into the wood.
Next use a saw from the side to cut underneath the plug freeing it from the stock wood.
Now do this about 60 times.
Note: The speed and accuracy of this process can be greatly increased if you substitute a drill press for the hand drill and a band saw for the hand saw.
Once you have all the plugs cut installing them is a simple matter of squeezing some wood glue into the counter bored holes and then inserting the plugs with a bit help from a soft faced hammer. When the glue has dried you can cut the plugs flush with a flush cut saw and then you can use sand paper to sand them smooth.
Step 20: Finishing: Applying Stain and Linseed Oil
With the plugs installed you're ready for the last big step of this build, applying the finish. Generally I like polyurethane finishes but for this project I decided to stick with a traditional boiled linseed oil finish. Linseed is a wonderful finish for a project like the Maker Station because it is very easy to apply, can be applied in multiple coats to build up luster, is very protective, dries hard, and is most importantly easy to repair when the inevitable mishap occurs, (The Maker Station is essentially a mobile work bench after all so you're going to ding it up at some point).
Before applying the linseed oil finish I applied walnut oil-based stain to the work surfaces of the Maker Station and to the front trim boards, this was an aesthetic choice as I thought contrasting colors would look nice in these areas.
As for applying the linseed finish, the process is very simple and almost fool proof which is fantastic if you're someone like me who hates finishing wood projects because of issues like drips, sags, and shiny spots. Linseed oil won't leave drips or sags because it's a penetrating oil finish that you wipe on and wipe off after a few minutes, and it creates a nice soft luster that looks very professional on all types of wood projects. To apply, simply use a cloth to thoroughly rub the linseed oil all over the project making sure to coat all surfaces, edges and corners. Allow the oil to set for 10 to 15 minutes and then wipe off any excess.
Generally two to three coats of linseed oil will yield a nice finish, however if you're looking for a nicer finish more coats of linseed oil can be applied to build up the luster, (for my Maker Station I applied two coats to the entire station and then 2 additional coats to areas like the floor and work surface, areas where I wanted a bit of additional wear resistance.
Tip: to make finishing easier I removed the light assembly and middle section of the work surface; I finished these components separately and then re-installed them into the Maker Station.
Tip: After finishing the exposed edges of the plywood parts looked pretty terrible. To hide these unsightly edges I used black acrylic paint which created a very sharp finish with nice contrast.
Step 21: Finishing Touches
Normal Velcro Strips
Power Strip
Once you've finished with the hook and loop, you can install a power strip onto the inside of the Maker Station to give your work area a few more outlets for those times when you need to run the light, a rotary tool, a soldering iron, and a panini maker all at the same time.
Step 22: Creating the Tool Racks
1/2" sheet of plywood
Screw on Picture Hangers
Thread and Needle
Screw in Hooks
How to make the Tool Racks
- The bucket organizer should be build in such as way that it can easily be separated into two equal sections so use a seam ripper or good old fashioned scissors to to break it down as shown in the picture.
- With the bucket organizer separated you should now have two pieces, each of which should have a front flap (the part of the organizer that goes on the outside of the bucket), and a back flap (the part of the organizer that goes inside the bucket).
- Fold the back flaps underneath the front flaps and stitch them together to create a pocket, (note: if you don't want your seam to be visible, sow the fronts and backs together inside out and then turn the whole thing inside out once you've finished sowing to move the seams to the inside).
- Next cut a piece of 1/2" plywood large enough to fit inside the pocket that was created when the fronts and backs were sown together, (note: the plywood panel should fit tightly inside the pocket.
- With the 1/2" plywood panels inserted into the the bucket organizer pockets, install the hangers onto the backsides of these assemblies as shown in the picture. (Note: pay attention to how far apart you mount the hangers, about 8" apart should be good.
- With the hangers mounted your tool racks are ready to go, the only thing left to do is to mount screw hooks for the tool hangers to hang on. Mount hooks underneath the upper most wheel support as shown in the picture, and then mount hooks inside the maker station, again as shown in the picture. Mounting hooks in these areas will allow you to hang the tool racks when the Maker Station is in the closed and open positions. (Tip: remember to mount the hooks the same distance apart as the hangers you installed on the tool racks).
Step 23: Load It Full of Tools
Alright, after a good bit of work we're finally at the fun part, loading it full of tools and getting ready to put the Maker Station to work. In terms of tool storage you have a lot of options; you can store your hand tools in the tool racks that were made back on step 22, and for bigger things like power tool cases and small tool boxes there is plenty of room on the inside of the Maker Station when it is folded up, (see picture).
Step 24: Optional Specialized Table Top #1 the Work Holder
The Work Holder
The work holder is a specialized table insert that utilizes hold down clamps and "T" slots to create a clamping surface for a variety of projects.
How to make the Work Holder Table Insert
Materials
- Start by cutting a 30" X 7" rectangle from a piece of 3/4" plywood (exactly as you did to create the original center table top)
- Next determine what side of the table insert you want to be the top and then use your table saw to cut two 1/4" deep grooves into that side as shown in the picture. (Note these grooves are approximately 1.5" in from the edges of the table insert). The reason for cutting these grooves is to remove most of the material from the areas where you will be routing the "T" slots so that your router doesn't have to work as hard to remove the extra material.
- Once you have cut the grooves with your table saw, the next step is to use your router equipped with the "T" slot cutting bit to create the "T" slots. Clamp a straight edge in place to ensure that your slots end up straight and then start routing the slots. While routing take your time and back your router off every few inches to give it a break and to clear out some of the saw dust and chips that may be trapped in the slot.
- When you have both slots cut, use some sand paper to smooth our any rough areas created during routing.
- After the work holder table insert has been sanded, apply your finish of choice. (I chose a matte finish black paint.)
- Lastly install toggle clamp catches just as you did for the original table center so that the work holder table insert can be locked into place.
With the work holder insert complete you can add on the hold down clamps by sliding them into the T slots and you're ready to go.
Step 25: Optional Specialized Table Top #2: the Jeweler
The jewelry making insert includes:
-Storage for 30 Rotary Tool Bits
-Bench Pin
-Contoured Sanding Surfaces
-File Storage for 12 Needle Files
Just like the Work Holder insert, the Jewelry insert was finished with a protective coat of black paint.
Step 26: Finished
Thank you for taking the time to check out my Instructable on building the Maker Station. I hope you found the information presented here to be useful and interesting. If you have any questions or comments please feel free to post them in the comments section and I will do my best to get back to you as soon as possible, and I really enjoy hearing your thoughts and opinions so please don't be shy about posting!
Also, If you enjoyed this Instructable please consider voting for me in the Portable Work Station, Wood Working, and Full Spectrum Laser Contests
Best Regards!
Step 27: Bonus!
One of the unexpected benefits of the Maker Station design is the fact that the work light is stored on the top of the station when it is in the closed (portable) configuration. I noticed this and saw the potential to add a bit of utility to the Maker Station by turning it into a floor lamp via a simple fixture made from a scrap of 2x4 and a 4 prong T nut (like the one used to fix the light in place when the Maker Station is set up for work.
To make this piece simply cut a piece of 2x4 that is roughly 4" long and while holding the light in the upright position, butt the piece of 2x4 up against the light and use a pencil to make the location of the screw hole that was drilled in the arm. With the location of the screw hole marked, install the 4 prong T nut into the piece of 2x4 just as you did when you installed the first one into the Maker Station. With the T nut installed the light modification is now complete, simply use the hand screw to screw the piece of 2x4 against the light which will hold it open for use as a floor lamp.
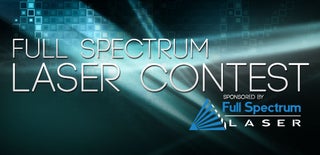
Third Prize in the
Full Spectrum Laser Contest
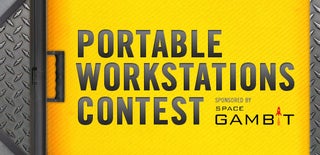
Grand Prize in the
Portable Workstations Contest
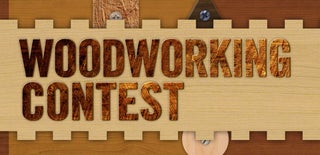
Participated in the
Woodworking Contest