Introduction: Making a Tahitian Ukulele
Hello, and welcome!
First of all, Thanks to Ken Russell for an awesome and inspiring project: How to build a tahitian ukulele
In this tutorial I will show you how to make a Tahitian type ukulele. This type is a little bit special since the sound hole is placed on the back, and the bridge is attached to a plate at the front. The resonance room inside is quite small compared to normal ukuleles, which gives it a sharp but beautiful sound. The Tahitian ukulele normally has 8 strings, 4 string pairs, but I chose to make a 4 string one.
There's also a youtube-video which shows the process roughly, where you can also hear how it sounds :)
Enjoy!
Step 1: Draw It
Develop a sketch to have a rough idea of where you want to go. This is the one I used as a template. You could also print it and cut it out to get the sketch over to your piece of wood when that time comes.
Choose the ukulele size you want to go for. It is crucial for the instrument that the dimensions are correct, especially the scale length. This is the length of the playable string, from the nut to the saddle. The concert ukulele has a scale length of 15 inches. Save the rest of your worry for later.
Step 2: Go Log Hunting
Get yourself a piece of wood you can work with. Luckily I found one lying around in my neighbor's backyard. Fresh wood changes during drying, so it should be relatively dry to keep it from cracking.
Step 3: Rough Shape It
At first, it could be smart to have a center line at which you can relate to all the way. Measure up the scale length so you know where to put the bridge, and then you can build your uke around that.
Cut out the basic shape of your uke. I first used a chainsaw on the log. I planned for my uke to be around 50mm (2 inches) thick, so i cut out a piece that was 70mm (2,8 inches) to get some margin. It's a bit difficult to get the surface completely straight, so you could for example build a chainsaw mill. I know there are some instructables for that out there.
Next use a jigsaw or a bandsaw on the outline. I would say a bandsaw is the best if you have access to one. Use the same tools to cut the thickness of the neck. My thickness is around 16mm (0,63 inches).
If you want some nice curves on it there are various saw tools you could use. Be careful not to overdo it! It's easy to get carried away...
Step 4: Sand Like There's No Tomorrow
Sand, sand, and then sand a bit more.
Use some kind of sanding machine you have lying around, or you may end up with oversized biceps. Gradually escalate to finer and finer sand paper. My final paper was P800. You will get excited when you touch it after that!
Step 5: Plate and Sound Hole
Jigsaw the plate. The thinner the plate, the more it moves and pumps out sound. Mine was 1,5mm (0,06 inches). The diameter i used was 140mm (5,5 inches).
Drill a small pilot hole through the whole piece, at the center of your marked circle, so you know where this is when you work your way through the sound hole.
Use something to cut a bowl into the front. Be creative! And make sure to leave a lip at which the plate can rest on. The looks of the bowl is not that important, as it will not be visible from the outside.
When the bowl is finished, drill the sound hole, around 2,5" in diameter.
Step 6: Cut-a-nut
Now this is important. The nut has to be perpendicular to the center line. Go look for your old protractor from your early school years!
Step 7: Glue Fretboard and Bridge
Again, the scale length is important, and is 15" on a concert ukulele.
Make sure to put the bridge so that the saddle is exactly this length from the nut.
It's completely possible to make the fretboard directly on your piece. Google a fret calculator and you will find the distance between each fret. Saw your frets and smash in some fret wire
Step 8: Drill Some Holes
Now as I said, I made a 4 string version.
Drill some pilot holes, and then some real holes in the dimensions of your tuners.
Step 9: If You Want Electronics
When you're at it, buy yourself a pickup as an extra touch to your new instrument.
I used a LR Baggs Five O, and it sounds great! Its a piezo based pickup with preamp. It also has a volume button and a battery pack that you can reach from outside, so everything is elegantly hidden inside.
I drilled a hole inside the body towards the fretboard, so I can plug the jack cable from outside while it's hidden when it's on my wall.
Step 10: Oil It Up
Now it's time to transform your smooth surface and give it some shine.
There's an own science field dedicated to finish on string instruments, so don't get lost. I used this finishing oil, which is an oil based on the chinese Tung tree. It penetrates and protects the wood with style, and really brings out the beauty in it.
Do some strokes, use some fine sand paper and finish it of with a polishing cloth. Don't worry. It gets beautiful in the end!
Step 11: Give Her a Place She Deserves
String it, play it and then hang it up on your wall where you can admire it and remind yourself of your beautiful creation!
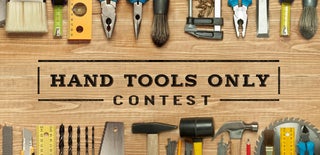
Runner Up in the
Hand Tools Only Contest 2017