Introduction: Making a One-part Rubber Mold and Casting an Object
This Instructable is connected to Arlene Shechet’s exhibition Meissen Recast currently on view at the RISD Museum.
Meissen Recast plays with the idea of molds, the casings that shape an object’s final form. Shechet reinterprets plaster molds by casting them in porcelain and calling attention to their usually unseen details. The process of mold-making and casting invites creative experimentation, but follows rules of precise timing and size.
Taking us through the steps involved in casting objects, Marisa Marofske (RISD BFA Painting, 2014) uses the form of a dog toy to create an array of iconic, colorful donuts.
Read the full article on our website and explore other objects made with molds on Pinterest.
Step 1: Create a Mold Sized to Your Object.
This could be an elaborate form made out of acrylic, but for some materials it works just as well to create a mold out of cardboard.
“I started by tracing out the shape of the object. You want the walls of the mold to be [higher than the original object]. You would want to score, and then obviously you’d want to cut.
And then what happens is this becomes a really simple box.”
Step 2: Tape and Seal Off the Cardboard Mold.
It’s essential that none of the material escapes the box.
“You can just use any kind of masking tape, anything. You’re not going to have any leaks, which is enemy number one in casting. You could [also] use packing tape on the inside.”
Step 3: Glue the Original Object Down.
This way, the object won’t rise when the casting material is poured around it.
“Since the bottom is flat like this, the way I’m going to do it is glue it down flat on the surface of the mold itself and fill it above. And then [the flat bottom] will become the top of the mold.
You just want to make sure you have a decent amount of rubber between the object part of the cast and the top of the mold.”
Step 4: Carefully Prepare Your Casting Material.
Marofske chose Dragon Skin, Medium Set, a kind of silicone rubber. Both parts are individually mixed in a ratio of 1:1, then carefully mixed together. For this part, it’s important to wear gloves and mix in a well-ventilated area. The tools you use also matter—wooden paint stirrers work better than makeshift stir sticks. The rule of thumb: mix well, but carefully.
“So you have Part A and Part B, it’s one to one. The thing that’s great about Dragon Skin is it’s super stretchy. When you’re casting, you want to do soft mold for hard object, hard mold for soft object.
The stuff we got, the medium set, the pot life is just around 8 minutes, so that means you only have 8 minutes before it starts setting up. So this takes about 5 hours, between 5 and 7 hours to fully set up, but you, it’s I think worth it for the extra time you have in mixing it, because you want to get all the bubbles out, so it’s nice to not be racing the clock.
Having the right mixing tools makes your life a lot easier. And then when you’re mixing them, you want to use separate stirrers, just cause if you mix one and then you’re stir the other one, it’s going to start to set.
So again I’m just going to stir this and make sure it’s mixed. So you can see some bubbles have risen to the top. It’s impossible not to have some.”
Step 5: Pour the Mixture Into the Mold.
Start pouring in the corner, and as the material fills up the mold, make sure it covers the entire object. Because the dog toy is rubber, Marofske didn’t spray it with a mold-release agent—she felt sure the mold material would separate from the rubber without sticking. For other materials, it’s best to cover the object with mold-release spray.
Step 6: Tap the Mold to Help Bubbles Rise to the Surface.
“You can just kind of tap the sides, to get some of the bubbles. You can even pick it up and tap it. But you can see this is totally fine, nothing’s going to seep out. And then, since it’s a waste mold, we’ll just rip it off and it’ll go right into the trash.”
Step 7: After the Mold Has Fully Set, Remove the Cardboard Waste Mold and Discard.
“It looks like it did stick a little bit, but it should be fine. If I were going to do it again I might just put tape on the inside of the box.”
Q: “Could you use Vaseline?”
“Yeah, you could, Vaseline is a pretty common casting material. It’s just horrible. I hate Vaseline so much. But if you’re casting plaster into plaster you have to use Vaseline. It acts as a resist.”
Step 8: Remove the Dog Toy From the Dragon Skin Material.
Some of this had crept over the top, so Marofske used a knife to cut a clean line around the open bottom of the mold. “And now I’m just going to trim this, just so when you pour the casting it doesn’t dip into the material.”
Step 9: Spray the Inside With Mold Release, and Mix the Casting Material.
“And since I’ve done so many of these, I actually know the exact amount to mix, but one way you can do it if you wanted was you could fill it with rice or water and then pour it into a thing with volume, so you could find out how much you needed. I know that it’s just around five ounces, which is the volume of . . . the object itself.
And this works just like the rubber. So you’re going to want to stir them individually before combining them. And again, try to not add any air into the liquid.”
Step 10: Mix the Casting Material and Pour Into the Mold.
We are using Smooth-Cast 300. The mixture needs to poured soon after its parts are combined, before it begins to harden.
“So I’m going to stir them together and almost immediately pour them into the mold. And then you’ll see that they’re both pretty transparent but it’ll cloud up and become opaque white. And it also gets pretty hot when it happens because it’s a crazy chemical reaction.
And then you just tap the sides to get some of the bubbles from pouring it to come to the surface.”
“It takes about five minutes. This one is the fast-setting, so there’s medium set for this kind of stuff too. But since it’s such a small cast you don’t really need the time. Sometimes you’ll even see the vapor coming off it once it starts reacting, so you definitely want to do this is a well-ventilated area. It almost looks like it’s smoking or something, but it’s subtle. Again, you don’t need a respirator, but you don’t want your face in it.”
Step 11: Pop the Plaster Object Out of the Mold.
Step 12: Things to Keep in Mind.
Finally, we asked Marofske about things to keep in mind when casting and making molds. Below are her top five considerations for the process.
1. Mix well, but carefully.
2. Having the right mixing tools makes things a lot easier. For example, it makes a difference to buy paint stirrers. You can just use anything, obviously, but this makes it super simple.
3. Try not to get it on you because it’s horrible and gross.
4. A good way to think about casting is to choose your casting method based on the object, not the other way around. So if you wanted to cast a rubber duckie, for example, you’d probably do that in plaster. But soft molds are always easier. The thing is if, this doesn’t require another mold, because it’s not big enough and there’s also just enough space around it for it to hold its shape.
5. Also I think the mantra of casting is: expect to fail. Because it happens. It’ll leak out the side and then that’s it.
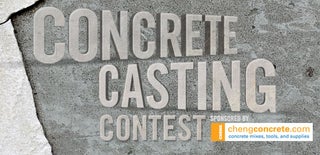
Participated in the
Concrete & Casting Contest