Introduction: Multi-Tool Flip-Top Table
Building a flip-top table is great way to save shop space. Building 3 flip-tops as one long table is even better. This project started with an 7' long 2" diameter steel shaft I've had lying around the shop for years. Since I didn't want to cut the solid shaft (because that sounds like work), I simply built a longer table. Even if you don't need a table this big, it's a good excuse to buy more tools! This shop project is easy to build and only requires dimensional lumber and plywoood. I used the solid shaft I had, but steel pipe is all you will need. Let's get going!
Step 1: What Tools Do You Have?
I began by making a Sketchup drawing of possible tools I wanted to include and how best to arrange them. This allows you to determine the size of the flip-tops. If there are 2 tools you often use together try not to put them on opposite sides of the same flip-top. For instance, I use my planer and jointer together so I put them on different tables so both could be "up" at the same time. My mini-lathe I placed on the end due to it's length and the need to stand in front of it to work. This avoided needing a very wide flip-top. Give some thought to how and when you use your different tools when customizing your tops.
When measuring your tools make sure you include all the hand cranks, legs, knobs, cords, etc which stick out on the sides. They may be small, but they still count towards the total width when you flip the table.
Attachments
Step 2: Prepare the Vertical Divider Pieces
When I build shop projects I typically use what I've got lying around. Whether you consider this being economically resourceful or ecologically responsible, it's mainly because I'm cheap and don't care how it looks. It's not going in the living room after all. I had 4x4 cedar cutoffs and some 2x4's & 2x6's so that's what I used. The top and the bottom are 38" long and the legs are 24" long. You may need to adjust leg length depending on how tall you want the top and the size casters employed. The legs are simply two 2x4's screwed together with 3 pocket hole screws on each end. Toenailing 2 screws from one side and 1 screw from the other makes for a stronger joint. Use the long 2 1/2" pocket screws for joining the pieces. First, however, you will need to drill the holes for the shaft before assembling the dividers.
Attachments
Step 3: Drill Holes for the Main Shaft
Using a hole saw, drill holes through the four top cross pieces of a size appropriate to the pipe/shaft you are using. I'm not an engineer, but I think 1 1/2" pipe would work just as well and probably even 1" pipe depending on how wide the tops are and how heavy the tools. When in doubt, build stout! To prevent the shaft from turning I drilled and inserted 1/4" brass inserts over the shaft to accommodate 1"x1/4" bolts. Once the main shaft is in place the 1/4 hex bolts can be locked down to prevent turning. There are four bolts total; one in each top piece.
The simplest way I've found to get inserts installed straight is using the drill press. First drill your pilot hole for the insert. Then cut the head off of a 1/4" bolt, add 2 locking nuts and tighten it in your drill press chuck. With the insert screwed onto the bolt, turn the chuck by hand as you lower the chuck pressing down on the insert. Do not turn on your drill press! You are simply using the drill press to align the insert at 90 degrees while you turn the chuck by hand.
Step 4: Assemble the Dividers
Next you can screw the legs to the top and bottom pieces with your 2 1/2" pocket screws. The locking bolt goes on the bottom of the top cross piece. To prevent racking of the dividers, I added 1/4" thick plywood on 1 or both sides. The center 2 dividers have plywood on both side, whereas the end dividers received plywood on the inside only. This is because I planned to build shelves in the ends utilizing the extra space. Using a router and a rabbit bit, cut a rabbit around the inside of the frame as a recess to accept the plywood. After cutting the plywood to width and length, I also cut out a 1/2 circle under the pipe hole to access the locking bolt. To insure your dividers are square, measure both diagonals and the length should be the same. When both diagonals are the same the panel is square. Apply glue to the rabbit and nail the plywood in place.
Step 5: Whip Up Some Spacer Rings
My flip-tops ended up being 18", 24" and 30" wide. The space between the dividers is 18 1/4", 24 1/4" and 30 1/4". The 1/8" on both sides of the table tops is a little room for error so the tops flip easily. Using 1/8" acrylic scraps I made some spacers to fill those voids on each side. The spacers were made using a jig on the router table and a hole saw at the drill press. You could also cut these using a bandsaw or scrollsaw as they don't have to be precise. An alternative material would be to use a cheap plastic cutting boards. You will need 6 spacers.
Step 6: Time for Flip-top Frames
Determine the size flip-tops you plan to build and rip 2x4s down to 3" wide. Rip double the number of 2x4s you need as these will also be used for bracing inside the frames later. The top of my table frame is 38" wide and I made my tops 36 1/2" wide. The 3/4" recess on each side allows for mounting barrel locks to secure the tops. For the 3 tops, I build an 18"x36.5", a 24"x36.5" and a 30"x36.5" rectangle from 1.5" thick by 3" wide ripped pine.
To begin building the tops you'll need to drill more holes with your hole saw. Each of the 36 1/2" wide sides needs a hole centered vertically & horizontally for the pipe/shaft. Once all six holes are finished simply construct the frames using 2.5" pocket hole screws.
Step 7: Assemble the Base
Cut three pairs of 2x6s a 1/4" longer than the width of your flip-top ends. In my case this worked out to be 18 1/4", 24 1/4" and 30 1/4". Assemble the dividers, spacer rings, shaft and tops as demonstrated in picture 2 and secure the 2x6s using 2 1/2" pocket screws along the bottom. When all 6 of the 2x6s are installed square up the dividers to the 2x6s and tighten the 1/4" bolts against the shaft. I would recommend using "blue" Locktite on each bolt to prevent it loosening. The blue version is removal in case you need to readjust later. Measure diagonals on the sides and tops of your table as before and get it as square as possible.
Next turn the table over and cut two 2x6s the length of your table plus 8" or more for overhang on the ends. The extra 8" will give you 4" overhang on both ends but this can be longer if you want to add a shelf. If you're unsure make them longer and trim when you decide. Glue and screw the long 2x6s into the dividers and the short 2x6 spacers you already installed. Attach a short 2x6 block the length of the overhang to lock the end dividers in place. Add six 4" or larger casters but remember this will affect table height.
Flip your table over and install the barrel locks by drilling holes into the dividers and mount with screws. Use a level across the table top so your tops end up level and even with each other.
Step 8: Framing & Finishing the Tops
This part takes a bit of figuring since each top must be framed for mounting a tool on both sides. The position of the internal framing will be determined by the location of your tools' mounting holes. Plan for each 1.5" think piece to be centered under one of the mounting holes for your tool. In this way, the lag bolts or screws used to secure the tool will enter the frame on center. It's a good idea to take pictures for future references. Secure the 3" wide framing pieces using 2 1/2" pocket hole screws.
The tops don't have to be very thick since the internal framing is carrying the load and I used 1/8" Luan plywood. Once glued and nailed in place it creates a pseudo-torsion box which is strong. That said, I ended up adding another layer of plywood in some areas to glue Corian to and make a gluing station (next step). So there may instances where thicker tops are warranted depending on your planned use. Again, when in doubt, build stout.
Step 9: Fill in the Bare Spots
My center flip-top was tool-less on one side and I decided to make a gluing station using salvaged Corian and Kreg clamping tracks. To insure a stable base for the Corian and for mounting the T-track I added a layer of 3/4" plywood under it. The clamping tracks were secured to the plywood from the bottom before the plywood was attached. The plywood was glued and screwed over the 1/8" Luan plywood and the Corian attached with Liquid Nails. This gluing station has been very handy as wood glue easily peels off Corian after drying. Of course this top gets used for many things since the tracks allow me to clamp boards down to the table top.
Step 10: Accessorize Your Table!
The end of a table is a great area for organizing your stuff out of the way. In this case, a lathe workstation was in order. The swing out tool holders keep everything close and the recessed shelves store all the little stuff. Including shavings! This workstation is working well for me even when the jointer is up and in use (not that often frankly).
On the other end I added shelves for paint cans, junk, and the like.
Step 11: Go to Work!
I hope this instructable has given you some ideas for saving space in your shop. Give this project a try. It is well worth the time and effort. I am very happy with mine.
I look forward to your comments and suggestions for improvement!
Step 12: Video of Multi-Tool Flip Table
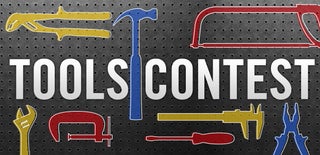
Third Prize in the
Tools Contest