Introduction: Multiple Raspberry PI 3D Scanner
UPDATE: Check out step 8 for the latest version of my scanner and a download link for the python scripts.
Hi,
I am a big Arduino and Raspberry PI fan and also love 3D printing. I wanted to be able to make a 3d model of my kids and started investigating how to build a 3d scanner. I found a lot of solutions out there, but the problem with most of them is that the subject would have to sit still for a while... well I think it would be easier for me to invent a spaceship that can fly to mars then inventing a solution for my 2-year old son to sit still :-( So none of those solutions where going to work.
I knew I had to come up with a way to instantly take many images at the same time. So I first started to research what cheap digital cameras exists. If I could find a cheap model, I probably could make an automated trigger system using arduinos. But then I would have all the images on many separate SD cards and I was not able to find a cheap good digital camera.
Then I noticed the Raspberry PI and PI camera combination. A "fairly" affordable module, that already is ethernet connected, so I could do the triggering of the cameras using the network and an easy way to download all the images to a centralized place. So my Project (and investment) started.
I bought for this project:
- 40 Raspberry Pies for this project and 40 PI cameras.
- 40 8Gb SD cards
- 1 single 60A 5v power supply to power all the raspberry Pies
- Led Strips and a powerful 12v power supply to power them on
As I am an impatient person I did not build the whole setup at once, I started of with 12 cameras, and was already seriously impressed with the results. So you DO NOT need 40 cameras, especially not if you just want to catch just the front of a persons face.
Here a result output:
UPDATE:
I have included a photo of Britt (the model in the video) being printed in full color by shapeways.
UPDATE2:
I finally was able to make a scan of my little son Hugo (2years old). It was made using 47 Raspberries and using my new softboxes with permanent lights. This allows me to shoot the images with no shadow. Can't wait to receive the printed model from shapeways :-)
Hugo - send for 3d printing
Step 1: Setting Up the Hardware
So I first needed a rig to hold the Raspberry Pies. I initially did some testing with a big round circle I made out of wood, but this was really impractical to work with and hard to walk in and out of. So after some testing, I went with an "individual pole" design. Most programs that turn images into a 3D model need the images to be shoot from different angles. So I settled for each pole to hold 3 Raspberry Pies cameras.
I made the poles out of fairly cheap multiplex wood using a 2mm cutting bit on my CNC machine. This allowed me to pre-drill 2mm mounting holes for the Raspberry, so I just needed 2.5mm screws that would instantly fix the raspberry to my frame.
For the PI Camera, I designed a small and easy to print bracket (as I need 40 of them, so it needed to be small) that can hold the camera securely and would easily allow me to change the angle the camera would be pointing at.
To fancy up the poles I also added a 1meter strip of 60 LEDs to each one, to provide some extra light for the photos and just because it looked cool :-)
Hugo - Almost ready for print
Step 2: Connecting Everything Up
Connecting 40 computers with ethernet and power was going to be messy, but I wanted to do it as efficient as possible. Unfortunately the Raspberry PI does not support Power-over-Ethernet, so I had to make this myself. I cut 40 ethernet cables, each 5 meters long. I kept all cables the same length so I know that what ever voltage I would lose over this distance would be equal for all and I would be able to adjust this on the power supply to get a very accurate 5v.
As 100mb ethernet only requires 4 of the 8 cables inside an ethernet cable, I could use 2 for providing the 5v to the raspberry. So I ended up putting 80 (2x 40) connectors on the cables using just 6 of the 8 wires (2 not being used). I would say this was one of the most boring and tedious elements of this project :-(
I bought a bunch of female jumper wires, cut them in half and soldered 2 on the end of each network cable, so I could easily just fit this on the ground and 5v pin of the Raspberry Pi.
On the other side, I build a "power distribution board" from my single 60A 5v power supply to where I could easily connect all the 5v and ground wires to coming from each ethernet cable.
Step 3: The Software
I am using Raspian OS, just the default download from the raspberry pi website.
To collect all the images, I am using a central file server (in my case I am using a Qnap). I configured the raspbian image to connect to the file server using cifs. This is done in the /etc/fstab file.
I am also using the central file server to store my software, so I can make modifications without having to update every raspberry on its own.
After I completed this image, I used dd (on my mac) to clone the SD card 40x for each raspberry.
I wanted to write a "listening" script that each raspberry would run, listening to a particular network broadcast package that would trigger the camera and then save the photo and copy it to the file server. As I want all the images to be stored in a single directory (one directory per shot), I am using the local IP address of each raspberry (the last 3 digits) for a prefix of the filename.
Here the python listening script I am using:
#!/usr/bin/python
import socket
import struct
import fcntl
import subprocess
import sys
MCAST_GRP = '224.1.1.1'
MCAST_PORT = 5007
sock = socket.socket(socket.AF_INET, socket.SOCK_DGRAM, socket.IPPROTO_UDP)
sock.setsockopt(socket.SOL_SOCKET, socket.SO_REUSEADDR, 1)
sock.bind(('', MCAST_PORT))
mreq = struct.pack("4sl", socket.inet_aton(MCAST_GRP), socket.INADDR_ANY)
sock.setsockopt(socket.IPPROTO_IP, socket.IP_ADD_MEMBERSHIP, mreq)
def get_ip_address(ifname):
s = socket.socket(socket.AF_INET, socket.SOCK_DGRAM)
return socket.inet_ntoa(fcntl.ioctl(
s.fileno(),
0x8915, # SIOCGIFADDR
struct.pack('256s', ifname[:15])
)[20:24])
id = get_ip_address('eth0')
ip1, ip2, ip3, ip4 = id.split('.')
print 'ID: ' + ip4
#create an options file, this file should containt the parameters for the raspistill image cmd
optionfile = open('/server/options.cfg','r')
options = optionfile.readline()
optionfile.close()
print "optons: " + options
while True:
data = sock.recv(10240)
data = data.strip()
if data == "reboot":
print "rebooting..."
cmd = 'sudo reboot'
pid = subprocess.call(cmd, shell=True)
else:
print "shooting " + data
cmd = 'raspistill -o /tmp/photo.jpg ' + options
pid = subprocess.call(cmd, shell=True)
print "creating directory"
cmd = 'mkdir /server/3dscan/' + data
pid = subprocess.call(cmd, shell=True)
print "copy image"
cmd = 'cp /tmp/photo.jpg /server/3dscan/' + data + "/" + data + "_" + ip4 + '.jpg'
pid = subprocess.call(cmd, shell=True)
print "photo uploaded"
To initiate all the raspberries to take a photo, I created a "send script". That would ask for a name. This name is send to the raspberries to include in the prefix of the filename. So I know who the images are from.
Here the python send script:
import socket
import sys
import time
print 'photo name:'
n = sys.stdin.readline()
n = n.strip('\n')
MCAST_GRP = '224.1.1.1'
MCAST_PORT = 5007
sock = socket.socket(socket.AF_INET, socket.SOCK_DGRAM, socket.IPPROTO_UDP)
sock.setsockopt(socket.IPPROTO_IP, socket.IP_MULTICAST_TTL, 2)
sock.sendto(n, (MCAST_GRP, MCAST_PORT))
The listening script checks the name received. If the name is reboot, reload or restart it does a special action, instead of shooting a photo.
To configure what options I want to use for raspistill (the default image capture software on the raspberry for the PI camera) I am using an options.cfg file to configure this. Again this is stored on the central file server, so I can easily change the options.
I did some testing to see how in-sync all the Raspberry Pies would take the photo. As they all receive the network broadcast package at the exactly same time, I found this worked great. I did a setup test with 12 units all taking a photo of my iPhone running the stopwatch app. Each photo captured he exact same 1/10th of a second.
Step 4: Processing the Images to a 3d Model
There are different ways how you can turn the photos into a 3d model. Personally I like autodesk’s recap the best.
Go to recap.autodesk.com. If you do not have an autodesk account yet, you can create one for free. It comes with 5Gb of storage, which is plenty enough to create your 3d model.
After you have logged in to recap, click on the new project button. Here you can select the quality of your 3d model (I always choose Ultra, why settle for lower). For the export format, most 3d printer software can directly work with .obj files, so at least select that one.
After that you can upload all your images by dragging them into your webbrowser, or by clicking you get a popup windows where you can select your photos.
Wait for the photos to be uploaded and click next 2 times. The autodesk cloud system will now start to do the hard work and turn your photos into a 3d model. This can take between 15 and 45 minutes. As this is happening “in the cloud”, you can do other things while waiting [:-)]
When the heavy computing is done you can click in the middle of the thumbnail (on the eye) to see the model in 3d on your webbrowser. Important: this requires the Chrome webbrowser!
When viewing your 3d model, you should see a thumbnail gallery of your images on the left. If all went well, you should NOT have many (or ideally none) in the list called “Not Stitched”. This would mean that those images where not detected. You can try to fix this by manually clicking marking points on the images. But as I said, hopefully the 3d scanner took good enough photos of you that this is not needed.
You can now download the .OBJ file to your local computer for further processing and clean up, like removing the background. The file you download is again a zip file. So you need to unzip this before moving on to the next step.
Cleaning up your 3d model.
There are many programs available to clean up your 3d model. The easiest program I have found to do this is also a free product from autodesk called “project memento”. You can download memento (Only for windows!) here: http://labs.autodesk.com/utilities/mementoAfter you have installed project memento, you can directly open up the downloaded .obj file, it should be called mesh.obj. The photos taken by the 3d scanner are 90degrees turned. This means that your model probably has an incorrect feeling for up and down. In the botton left you will get a message “did the orbiting feel off?”. Click on “feels off” to correct this.
You correct the orbit, click for instance on the top of your head, making sure that the arrow is pointing up. Try rotating the model (by keeping your right mouse button pressed). If it feels good now you can accept the setting.
As you can see, you where not only scanned, but also part of your environment. You probably want to cut those pieces away. This is very easy in memento. Just select with your mouse a region of unwanted stuff and then hit delete. By rotating the model around you should be able to easily select and remove all unwanted stuff.
Fix your model for 3d printing.
To be able to print your model on your 3d printer, you need to make sure you have a watertight model (no holes in it). Again this can easyly be fixed with memento. Click on the top middle of the memento window and you will see a popup to fix your model.Just walk thru the wizard and any hole issue it finds, click on fix. You need to select if you want a flat or smooth fix. For me usually the flat fix works best. Select “next” again to find more issues. The holes need to be fixed, everything else is optional.
After you have fixed all the holes, click done and now you can export the model as a new .obj file. You can do this by going to the top left corner of the mement program and click on the bended arrow.
You can now specify how detailed you want to save your model. Again here, why go for lower resolution?? move the slider all the way to the right to get the best quality.
You are somewhat done now. You have a printable 3d model. If you want to clean the model more up there are some programs that can help you with that.
Pixologic Sculptris (free): This is a great program to fix little details in your model, like smoothening out areas. it is like a photoshop, but then for the 3d world.
Meshmixer (free): An other free program from autodesk. Meshmixer is great to for instance make a flat bottom on your model.
Alternative software to make a 3d model
Besides Autodesk Recap there are more options to turn your photos into a 3d model.Autodesk 123d Catch (free): It works like recap (being a cloud service), it a bit better developed then recap, but does scale down your images. So the end result is a bit less resolution.
VisualSFM (free): This is local (and much more complicated) software to turn your images into a 3d model. You need a powerful graphics card (supporting cuda) to run this software.
Agisoft Photoscan Standard Edition ($179): Also for this software you need a powerful pc and so far I have not found that this produces better results that Recap or 123d catch.
Step 5: Results
Step 6: Design Files
Here are the design files I used. The "statief" is an 2d cad file for the poles that I cut out on my CNC.
The camera_mount files are the camera brackets I designed.
Step 7: Version 2
A few months doing the Makerfaire show, I was invited for another exhibit to demonstrate my 3d scanner. I wanted to make the set more portable and easier to adjust. So I redesigned the frame. instead of using only wood, I designed tripods from cheap radiator pipes. This allows me to easily move the cameras up and down. I already designed new 3d printed brackets for the raspberry and camera that slide over the radiator pipes (40mm).
You can already download the tripod design on thingiverse: http://www.thingiverse.com/anykey/designs and I will soon be adding the raspberry and camera mount to it as well.
I am currently using 47 camera units. This allows me to do full body scan of kids (up to 1.20m). I will need to add more cameras to do full body scan of an adult.
Daylin to 3d print
Step 8: Version 3 - 98 Cameras / Raspberry Pies and High Power LED Strips
Here is my latest setup. Using 98 Raspberry PI units on 19 poles (2 meters in height).
Between each pole is a 2 meter high power white LED strip (19.2watts per meter). On top is some extra LED lights (10 watts per meter) to provide some extra lighting on top of the head/hair
Python Scripts:
You can download the basic python scripts from my website: www.pi3dscan.com
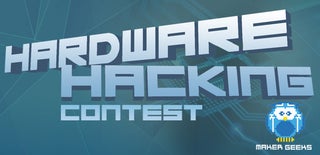
First Prize in the
Hardware Hacking
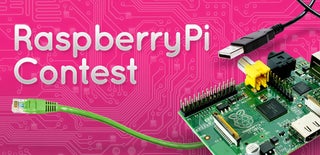
Grand Prize in the
Raspberry Pi Contest