Introduction: Mustache Mascot Costume
The Mustache Dache, a mustache themed 5k, commissioned me to build a mascot. Based on my previous costume work, it only took about a day. I'm sure there aren't thousands of people building mustache costumes out there, but hopefully the techniques will help make your build a success. http://mustachedache.com/
If you like the costume, please vote in the upper right corner. Thanks!
Step 1: Materials/Techniques
For this project I used a foam rubber substructure upholstered in a furry black fabric.
You can use either EVA Y-20 foam (ethylene vinyl acetate) or XLPE (Cross-linked polyethylene foam). Both are similar to yoga mat material, suitable for use with hot glue or contact cement, come in a big range of thicknesses for stiffness, and after sealing can be painted if needed. For the strongest permanent bond always use contact cement. Follow the instructions and allow it to dry to a dull finish for ~15 minutes to get maximum grab.
You can cut the foam rubber one of three ways depending on the type of cut:
Scissors: Better on thick material but may leave a rough serrated edge.
Long box cutter: gives a clean edge.
Hot knife: Works well on thin material with very tight contours.
I've price shopped the entire internet. Cheapest foam: http://www.thefoamfactory.com/closedcellfoam/cross-linked-polyethylene-foam.html. My local fabric store, Joann's Fabrics, always has a weekly 50% off coupon that cuts cost on the fur which is $20/yrd.
Step 2: Foam Substructure
Creating the foam rubber outline to be upholstered is very easy.
You can see the standard sheet width is the middle portion and that an extra portion had to be added to hit the 7 foot width. The foam was cut with a fresh very sharp razor blade. In general I recommend buying a pack of 50 blades so you don't tear and pull at the rubber with a dull edge.
Contact cement was spread around the rim of each side except for the lower central bottom since that is where you'll get in the costume. The contact cement is allowed to dry at least 15 minutes and then the surfaces are pressed together with firm pressure for several seconds. I then created foam tubing from foam pipe insulation to add to the 3D shape of the costume. It was then glued into place.
Step 3: Upholstery
Fabric requirement is based on your costume size. Standard fabric comes in a 54" width and is sold by the yard. Mine required 3 yards on the front and back. For me it was worth the extra cost to use one large piece rather than piece scraps together on the tips. Spray adhesive (Elmers or Spray 77) on both surfaces. Allow to dry to a tacky finish and then slowly apply pushing out wrinkles as you go. Try not to stretch the fabric as you apply because it will warp the costume when you actually put it on.
Step 4: How to Wear It?
The person wearing the costume had to have their hands free. I decided to use lacrosse shoulder pads as my mounting solution ($10 on craigslist). I attached plastic tubing to the back so that two rods stuck up. These rods would slide into the slit on the foam pipe insulation we put in earlier.
Slits were cut in the area where nostrils would be found and a flap of fabric was added to hide the cutout. That way you can hide the arms to give a clean mustache profile or put them out for a cartoon character feel.
An eye hole was cut and black mesh was added to the back.
Step 5: Finishing Details
To give the finishing touches, the wearer wore white cartoon gloves, a jogging outfit, and googly eyes were attached with wire for durability.
If you have any questions on how to build your own costume, feel free to ask in the comments and I'll do my best to help.
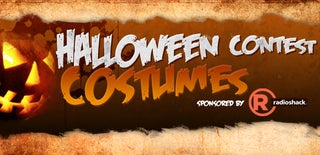
Participated in the
Halloween Costume Contest
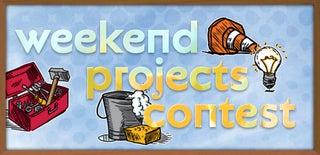
Participated in the
Weekend Projects Contest