Introduction: Numechron Digital Clock
My Numechron Digital Clock design was inspired by the Pennwood Model 1364 digital clock. Clocks of this type originated in the 1930s, and were built for many years by the Pennwood and Lawson companies in many different wood, metal, and plastic case styles.
I really liked the Art Deco style of the Model 1364 case and chose to emulate it, although my clock is considerably larger than the prototype. While mimicking the original style, I employed considerable open space in the case design so that the clock's internals would be visible.
A Pennwood employee, F. Greenewalt, patented the mechanism for this type of clock in 1935. He developed an ingenious set of wheels, cams, and levers to flip the numerals and operate the clock. I consulted the original patent to design the mechanism for this clock.
Here is a video of the clock: Numechron digital clock
Here is a video describing design and build: Making Numechron
Tools
- Carvewright CNC machine with carving bit and cutting bit
- bench disc sander
- drill press
- clamps
- screwdriver
Materials
- 1/4" Baltic birch plywood
- 1/4" aspen or poplar
- 3/4" oak and pine
- 1/8", 7/32" and 1/4" brass tubing
- brass wood screws
- small springs
- super glue
- wood glue
- stain
- polyurethane varnish
Step 1: Design
From the original patent we can see the parts of the clock that we will need to build and how they go together.
I used a Carvewright CNC to make all of the parts and the Carvewright Designer software to design the parts. I did cut some prototype parts and try them out on temporary jigs, then made design adjustments, to make sure that the mechanism would function and verify the design.
(Carvewright uses a proprietary file format, not standard STL or DXF formats, so the files cannot be used with other CNC machines. I do plan to make the files available in the Carvewright Pattern Depot in the future.)
You could also make these parts with a scroll saw (the digits would need to be painted on rather than carved). Some minor modification to the parts illustrated in my build would be required. Templates are provided for all of the major parts except for the case parts.
Step 2: Fabricate the Parts
Starting with the hours, tens of minutes, and minutes wheels pasts, make these using 1/4" Baltic birch. Baltic birch plywood is a quality material with many thin plies that are generally void free. All of my materials came from a local home center.
To make these parts without a Carvewright CNC, use the full-size templates attached below. Print the pdf file on 8.5" x 11" paper, and check to make sure that your printout scaled properly. Fasten the templates to the plywood and cut them out with a scroll saw. Sand.
I used 1/4" poplar for the hours and minutes numerals. The template contains a table of dimensions for these parts. Note that the top and bottom edges of each numeral must be mitered - cut at an angle - as specified by the chart. The seconds numerals can be cut on a band saw using the profile template provided.
Cut the frame parts and motor mount parts from 3/4" hardwood.
Attachments
Step 3: Assemble the Digits Wheels
Once the parts for the wheels are all cut out, assemble the digits to the wheels one at a time. The digits pieces are trimmed as needed for a tight fit - I used a bench disc sander with the table set at the appropriate angle for the mitered edges of each digit. Glue and clamp.
Note that the tens of minutes, minutes ones, and seconds wheels all have a peg on the left side of the wheel. (Left while facing the front of the digits.) I used a small piece of 1/8" brass tubing, sourced from Ave Hardware, for this.
Step 4: Seconds Wheel
Because the seconds wheel moves continuously, unlike the other wheels which lock into place, the seconds wheel is best made as a cylinder. I made mine in six sections. You could use a bandsaw to make sections like this, or possibly turn a complete cylinder on a lathe.
Step 5: Frame
The numerals wheels are supported on a frame made up of several pieces screwed together. I used 3/4" oak for my frame pieces.
7/32" brass tubing is used for shafts and 1/4" brass tubing for bushings. The larger tube slides over the smaller tube allowing the wheels to turn with little friction. I got my tubing at the local Ace hardware.
The tens of minutes wheel fits in between the two arms. The minutes ones wheel rides on a shaft protruding from the right arm. The hours wheel rides on a shaft protruding from the left arm.
Step 6: Spring Arms
Spring-loaded arms ride on cams on each of the hours, tens of minutes, and minute wheels to hold the digits in place after they move. I machined the arms and brackets out of oak. The small springs came from my local Ace hardware store. The arms are adjustable for both tension and position. Too much tension causes strain on the motor; to little causes the digits to be misaligned when at rest. The position adjustment allows the wheels to be rotated slightly so that faces of the visible digits are aligned.
To set the time, you just reach into the back of the clock and manually rotate the wheels.
Step 7: Motor
The clock is driven by a 1 rpm synchronous motor. These can be sourced from time clock parts suppliers. A separate motor mount is used to hold the motor and seconds drum in place. Electrical wires run through the mount to the underside of the clock's base and are hidden. A cover hides the motor. These motors run quite hot, so ventilation slots are needed. These parts were all machined from 3/4" oak and glued and screwed together.
Step 8: Case
A case and faceplate finish off the clock. A wide variety of case styles may be used. I emulated a classic case, but built one with ribbed top and sides so that the clock's mechanism remains visible.
A wide variety of stains and finishes may also be used. I used Minwax wood stain and Minwax clear satin polyurethane.
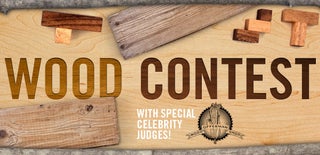
Fourth Prize in the
Wood Contest
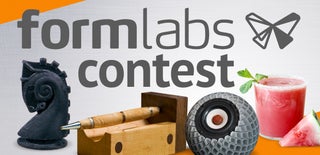
Finalist in the
Formlabs Contest
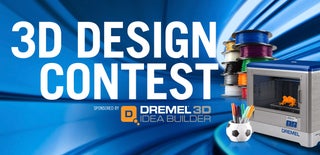
Participated in the
3D Design Contest