Introduction: Pallet Shed
My wife and I moved into our new place a couple years ago knowing we would need to get a riding mower to keep up with the bigger yard. Between the riding mower and all the other stuff we discovered we'd need to keep up with the yard, we quickly lost half of the 2 car garage to yard equipment. We priced storage sheds, but ones that would be big enough to hold the mowers and be tall enough to keep me from cracking my head inside cost way too much; over $2300 for a 10'x10' shed at a local big box home improvement store.
We decided to build, but even low end building materials were going to add up quickly. We had been making shelves and small furniture pieces out of pallets for a couple months and started discussing using pallets as our building material. Then, one day, something really fortunate happened. There's a local printing company that occasionally sets their unwanted pallets out on the curb for who ever wants them. We happened to drive by and discovered about 5 of the biggest, stoutest pallets we'd ever seen. Each measured about 4 feet ab 6 feet. We had just found our shed. Well, most of it.
You can build one, too. These instructions show what we were able to cobble together based on what materials we had at hand. Using some of the techniques we learned, you can build your own
Step 1: Tools & Materials
Tools Needed:
Cordless drill/driver - drill holes / drive screws - Harbor Freight= $25
Phillips heads for screws
a 14" long 5/8" dill bit - for drilling all-thread bolt holes
Circular saw
Oscillating tool - used to cut the all-thread - Harbor Freight= $20
level (the bigger the better)
step ladder
2 pair of pliers
tape measure
Materials:
Dozens of pallets
2 - 5 foot lengths of 5/8" all-thread
about a pound of nuts and washers to go with the all-thread
5 pounds of 1-1/2 in screws
2 pounds of 3 in screws
assorted door hardware as you like
6 - 12x2 ft roofing tin
1 - 4x8 sheet of chipboard
Step 2: Build Your Base
We leveled out a 10' square area by means of digging into the ground and elevating with cement blocks. Start level and square to keep your building true and plumb later on. Once our site was prepped, I attached my first two 4'x6' pallets to ground contact rated 10' 2x4's using the 3" screws. These became he first corner of the building. The pallets walls were attached to each other by lining them up square, then drilling through with the long 5/8's drill bit. We then measured and cut a piece of allthread a couple inches longer than each hole needed. We bolted the pallets together top, bottom and center using the nuts and washes. It may have been overkill, but allthread is cheap and better safe than sorry!
Step 3: Working Your Way Around
We added another pallet to the back using screws on the bottom and allthread bolts on the sides, then did the same on the right side
Step 4: Keep Working Around
We put up the back left corner side wall using screws on the bottom, but used some pallet top boards to attach this side piece to the back wall. These were the last of the 4'x6' pallets.
Step 5: Working Up the Sides
We added smaller, regular sized (about 40"x48") pallets to complete the side walls. Again, we used screws to attach the pallets to the ground contact lumber, and allthread bolts to attach the pallets to each other side to side.
Step 6: Bring It Around the Front
We acquired some long, skinny pallets (about 3'x8') from a place a couple towns over that sold hot tubs. These weren't as stout as the 4'x6' we used for the back walls, so we used some 2x4 lumber that would frame the doorway to add structural integrity.
We then added three 12' 2x4's front to back to support a temporary plastic roof and framed in the doorway. Over night it looked like some kind of a weird greenhouse.
Step 7: Adding Doors & Roof
In the garage, we built a couple doors out of chip board and pallet tops, then hung them in the door frames. We made them plenty wide to accommodate the riding lawn mower that would soon be living there.
At this point, the 10' wide x 10' deep frame of the shed is done!
The temporary plastic roof was replaced with 7 - 12' 2x4's and 6 - 12 foot long sheets of corrugated tin. The shed is about 8 feet tall in the front, and about 6 feet tall in the back, so there's plenty of slant for the rain to run off.
This tin was by far the biggest expense for the shed, coming in at about $120 for the tin and self tapping screws that made up the roof
(We found out a week or so later that an aunt had had an old barn blow down on her property. We could have recycled the tin from her old barn at no cost.)
Step 8: Windows & Skin
Now the fun part! We left some spots in the front blank so we could let some light in. We did not want all the birds nesting inside, so the window coverings are made from plastic florescent light covers. With a heavy hand, they'll cut with a box knife. We cut slightly smaller than the frame and caulked them in place.
The shed 'skin' is pallet tops. They are very uniform in width, so the look nice stacked on top of each other horizontally. When we would get the the end of a row, we would measure carefully, then cut the last piece to the exact length needed. The left over bit from that board would be used to start the next row, just like hardwood floors. The variety of wood species and colors just adds to the look of the finished product. We completed the skin on front first, then went to the back and sides
Step 9: DONE!
Since the roof is angled to let the rain run off quickly, those side pieces needed a little more effort to cover and still look nice. Once the proper angle was measured, we were able the set it on the table saw and have a nice, uniform incline all the way up the roof line.
You, too, can build your own shed!
Take your time, measure carefully, don't let mistakes get you down, and have fun!
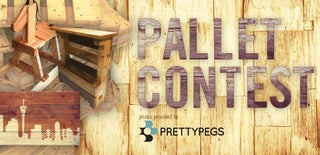
Second Prize in the
Pallet Contest