Introduction: Perfect (3d Printed) Hinge
In a project budget, hardware regulary takes an important part of the budget. Making your hardware by yourself achieve the dual goal to get a suitable piece of hardware and to reduces the overall cost. Hinges made out of metal or wood are not easy to make and a good hinge will probably take you a lot of time. Through, not anyone is skill enough or tooled properly to succeed.
As the local store is not that close to my home, I was regulary tempted to 3D print pieces of hardware for my projects. If you need a knob, a cleat or a handle, plastic might be strong enough. But hinges should bend without flex, and hold a good amount of weight. I tryed a lot of printed hinge designs, but I was regulary desapointed.
Most of printable hinges are not heavy duty, even if it uses screws as axis. I mean especialy those which uses screws as axis. Because steel is stronger than plastics and always contributes to make the hinge fail. Ins some cases, the screw thread grinds the plastic on the barrel side. The hinge get some play quickly and gets fragile.
The full plastic hinges are not better. Plastic is a reasonalbly weak material, and you need oversize dimensions to get some stiffness and some strenght. As nobody wants to add a big Fisher Price alike piece of hardware to his project, most designs are small hinges with consequently a small shaft and a small bushing. So the 3d printed hinges fails to hold more than small pannels, like plexiglass or so. Unfortunately, even with light weight materials to move, 3D printed plastic hinges breakes easily. The main reason is the way they are printed.
The weakest hinges are those printed in three parts : two leaves and a printed axis. In most cases, that hinges needs to be mounted verticaly or the shaft can get out. Then there's the two parts hinges, mostly ball jointed, and obviously it cant hold a lot. Then comes the single print intricated ones. And there's a dilema. If your hinge lay on the printbed, you will get a good shaft and barrel strenght, but it won't be round enough for a good motion. If your hinge is printed standing up, you will get a good motion, but the shaft or the barrel will not have enough material to get a good cohesion between the layers and will be weak. ..
Step 1: A Design That Solves the Problems.
The idea was to get a strong shaft and a strong barrel in a reduced area. The only way to get this, is to draw a variable diameter shaft and barrel.
The shaft needs strenght especialy at its attachement points, but as you get far from theses points, you don't need much strenght. On the contrary, the barrel will be stronger at the centre. So the overall hinge will be stronger than a constant diameter axis and barrel in the same build volume. As the gap between the axis and the barrel is small and constant, the variable diameter don't brings extra play.
After a lot of trys, the best ratio was fifty support fifty hinge, spared as 2+4+2 = support/hinge/support. The profile of the hinge gets larger smoothly until the barrel area. The countersunk screw holes makes the screws as discreet as possible while pushing strongly the hinge to its support. I added teardrops holes to avoid overang trickle on the holes while printing.
I rounded all horizontal sharp corners to get the smoothest possible motion on the printer. So the print runs faster and is consistantly more quiet !
Step 2: Printing !
At its original size, the perfect hinge is 40x40mm (1-37⁄64in or 1,57") It is reasonably scalable. I printed it at 150% with no noticeable extra play. Joshua downloaded the hinge from thingiverse and printed it out at 75% with no issue.
Of course, the hinge is meant to be printed verticaly to get a very smooth motion. If your printer is a bit out of calibration you may have to breake the hinge for its first opening. You can do it by hand, holding one leaf of the hinge firmly on a table hedge from one hand and pushing down with the other hand. My 10 years old child manage to do it.
I recommend PLA or PETG as printing material, because ABS and Nylon bends too easily.
You can get the last version of the hinge and read printing specifications on the perfect hinge thingiverse page. (and see my face too, if that matters uh...)
Note, the Perfect Hinge is actualy my most downloaded part ever.
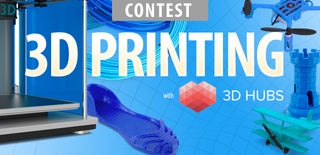
Runner Up in the
3D Printing Contest 2016