Introduction: Building a "Pintail" Duckboat Pt 1
******Please Note: The woodworking part of this project is complete. Pt. 2 will be on Prepping and Painting the boat.
My name is Greg and I am a wood scavenger. I was trained as a 6093 Aircraft sheet metalsmith In the Marine Corps, Most of my lifetime ago. When I got out of the Corps I spent a couple of years working for Lockheed Ga. on C5's and C130's. Then I moved to Florida and went to work for a Yacht manufacturer fitting aluminum panels on 100'+ yachts. But every time I walked past the woodworking shop I loved my job less and less. So I studied and bought old hand tools from flea markets and thrift stores and now I am a Certified Wood Butcher. I can't stand to see good wood in a dumpster or a scrap bin. My motto is, "It's not scrap until I say it's scrap."
So one day I was walking across the 9' boards I had recently saved from the landfill and decided that a boat would be a good project for them. So began the internet search for a suitable design. I wanted something to travel the canals around my house and take photographs. So I wanted something lite and stable. I decided on a design called Pintail. Drawn by William D. Jackson in the 1940's. and published in a book on small boat building called the "Boat Builders Handbook". The viewers at home can follow along by downloading the Pdf for free at Svensons. That is what I did and that is what I am building from. It's a simple yet challenging boat to build and it has all of the features I was looking for. So let's get started shall we.
Step 1: Tools Needed
Always keep in mind when you are working with sharp edged tools and especially power tools, that they will cut flesh and bone as easily as wood. Even the Ryoba hand saw will give you a nasty wound if you get your body parts in it's way. Make sure that all of your tools are razor sharp so they are able to do what you intend them to do without forcing. Do not push tools towards any part of your body including and especially your hands. Also be very careful of bystanders as they may not be aware of what you are about to do. Always wear safety goggles, dust masks and other protective gear when appropriate.
Most importantly If you have never used a Table saw, give the dimensions and wood to someone who has experience and let them cut the long parts. Please read all directions and have good understanding of what needs to be done before starting a project like this. And don't forget to change the batteries in your smoke alarm on your birthday.
Power tools
Table saw (only in the beginning to cut the long parts. You really should not attempt to cut these pieces with a circular saw)
Circular saw (Skillsaw)
Jigsaw or Bandsaw
Screw gun
Sander
Hand Tools
Hand plane (or a belt sander or grinder)
Tape measure
small try square
All of your clamps (most of them anyway)
Chisels
Adjustable angle "Boat square"
Small Hammer
Japanese "Ryoba" Saw
Battens
The materials list is in the plans.
Step 2: Make Patterns
I guess you could just layout the parts right on the wood but I decided to do a full scale drawing of the frames and make patterns for the Inner and Outer Stem (bow) Pieces and the side Cockpit Knees and just trace them onto the wood and cut out with a jigsaw. I used the inside of a frozen pizza box to draw the frame halves and other bits of thin cardboard for the other parts. I drew the curves by marking the pertinent measurements and using a batten to draw the lines. I also used a long batten to draw the curve of the form board, which would eventually become the bottom curve of the boat. I glued up the frames and cut out the parts. It rains a lot where I live and I would be building outside so I wanted to minimize the exposure to the elements.
I went with only one piece of plywood between the frame pieces instead of two because it minimized the areas where water might collect. Plus it just looked cooler. I saw this design on a Lightning sailboat so I am not worried about it being strong enough.
Cut the ends of the form to match your stem pieces. But first....
Step 3: Cut the Long Pieces.
The longest pieces are the Clamps (gunwales or "gunnels") at 11' long. Instead of buying a 2x10x10' for the form board, I got a 2x12x12' so that I could cut these parts off first and then cut the form out of the remainder. I used my skillsaw with a guide board clamped to the base at 3/4" to make these two cuts. I later took those pieces and a 2x8x10' to my my old boss's shop to cut them out on the table Saw. I laid out the keel with a long batten and then cut the shallow curves with the skillsaw.
Note: It's usually easier to find clear, knot free wood in larger dimensions than smaller. So if you have to buy wood, get the biggest dim's possible and take your parts out of them. Unfortunately I was not able to use the wood I had found in the remodel dumpster for the long pieces but I did use it for the frames and smaller parts. So those 9' boards will go into a future 'ible. But the 2x12x12' was only about $15 and it was straight grain and practically knot free.
Step 4: Set Up the Form.
I built a simple set of legs for the form out of 2x4's. I went with a three legged design but I actually should have gone ahead and added the second foot since that side is kinda wobbly.
Step 5: Set Up the Frames
The center frame is actually part of the form and isn't attached to the boat, giving it an open cockpit between the #1 and #3 frames. I notched the stem pieces and attached them to the form with a couple of pieces of ply on each side. Then I trimmed the keel to length and started on the chines. Southern Yellow Pine is a pretty stout wood and these pieces are 3/4 x 1 3/8 so I laid the pieces between my bench and chair and hung a bucket of sand on them to put some pre bend into the wood. This worked like a charm. the bucket was a good 8" off the ground when I first hung it there. By morning it was on the ground.
Step 6: Trim the Chines
OK. The easy part is over. Now we start to build a boat. I used Clothesline to pull the chines in so I could mark them and cut the ends to fit against the stem pieces. You do this little bit at a time. You can't just pull them in one at a time or nothing will line up right. So I tied off one end just enough to keep it from spreading while I used the Clothesline to pull the other side in.
After trimming all four ends I loosened everything up and glued it all in place.
Step 7: Add Bilge Battens
This part was pretty easy. Just lay your pieces across the frames and make sure everything is even. Then mark where you will notch the frames and cut the notches. Notch the center frame a bit loose so that it doesn't get stuck when you try to pull it off the form. Then mark the angles and cut. Glue and screw to the frames(Not the middle frame). And put a couple of screws from the outside into the ends of the BB's.
Then install Clamps pretty much the same way as you did the chines. Don't forget to pre-bend them first.
Step 8: Adding the Clamps
I know it may be confusing but the top outside frame of a wooden boat is called a "clamp" Or a Sheer Clamp. No, it's not see-thru, but the "sheer line" is another name for the continuous line from the transom to the bow. Or in this case, from the bow to the bow and back to the other bow. This design is called a "Double ender" for reasons that are hopefully more obvious that the reason for calling that frame piece a "sheer clamp".
In the process of adding these parts I figured out a neater way to cut the ends. A lot of this is just done by eye, but I found that I could clamp the Clamp (sorry) to a 2x4 and use it as a lever to hold the piece in place and mark the top and bottom, then connect the lines to get my cut line. Check the pictures they can show it better than I am doing here.
Step 9: Adding the Bottom. But First, a Bit of Controversy and a Minor Disaster.
This is where the controversy comes in, "Hey Greg, What kind of plywood did you use?" Well I used 5mm underlayment from The Big Orange Place. It costs 11 bucks a sheet. I have used it before and I have taken strips of it and soaked them in water for days and they did not de-laminate. In fact you may be able to see a little bench in some of the photos. There are small scraps of this ply on that table that have sat out in the rain for days and haven't de-lam'd So I am quite confident in using it.
Another point that I am sure to hear about, I will not be using epoxy or any fiberglass on this boat either. Believe it or not people built boats before epoxy was invented. Some that have lasted for decades. I won't go into my reasoning too much here because I 'm sure it will be discussed in the comments section.
I am, however using one Modern Miracle. I am gluing it together with 3M 5200, If you have never used it before, let me tell you it's some awesome stuff. It sticks to pretty much anything and it's the only adhesive/sealant that should be used below the waterline. When you glue something together with this stuff, fasteners are redundant. They are only there to hold things in place til the 5200 dries. You could also use resorcinol glue but I couldn't find it in my area. I admit I didn't look that hard though. =)
Now on to the minor Disaster. In the first photo you can see where my frame has come apart. This was not the fault of the glue. (I used Elmer's Wood Glue MAX.) But I glued the plywood pieces to painted wood. Big No-No. But I just took everything apart and sanded off the paint and glued it back together. I also added a couple of screws for safety. I moved ahead with marking and cutting the plywood for the bottom without reattaching the sheer clamps to the stem to give the frame some time to set before putting any stress back on it. I re attached them before I buttoned up for the nite..
The plans said to start the bottom at one end and scarf in a piece at the other end. But I instead centered the piece and added a small piece at each end. Check the photos for the deets.
Step 10: Attaching the Sides
I decided to start the side planks in the middle, The same way I did the bottom. Instead of starting at one end and scarfing a piece in at the other, I would be putting a smaller piece at each end on both sides of the boat. I won't have the plywood to do this until I cut the deck pieces and side deck pieces out of the other sheet of ply. So you may see holes in the bows over the next couple of steps.
I will use the pieces that I trimmed from the side planks to patch the missing bit at the sheer line. But with the sides already on, the boat can come off of the form.
Step 11: Turning the Hull
I need to take the hull off it's form but first I need somewhere to put it. The only cradle I ever build for a boat was for my model sailboat. It's just a simple folding X with straps across the top that the sailboat sits in. So I though I would try to make something like that, only bigger. 2x4s and 1x4s and a big dowel. I'm not sure I Really needed the dowel but at least I will be able to fold it up when I am done.
I also had to erect a shelter from the rain in my backyard. I didn't want to have to pour water out of the now upright boat every morning. Thanks to jaaaaayyyyy and his excellent instructable. I kept trying to do it my way and it wouldn't work until I finally did it his way and success!!
Step 12: Installing the Cockpit Floor and Knees
At this point I had planned to install the floor, so I wouldn't be working over the coamings. But I decided to wait until the boat was complete and the inside was primed. So I worked on the side Knees. This is a part that supports the side decks instead of the middle frame that we took out when moving the boat off of the form. I cut these out of the offcuts from the form itself. I wanted them to be sturdy enough to use as lifting handles for the boat.
Step 13: Deck Beams, Carlins and Other Framing
The deck beams were pretty straightforward. Cut them to the pattern and notch around the sheer clamps. Then thru bolt with a #10/24 x 2" Stainless bolt and nut at each end of both frames. I used countersunk bolts and finish washers because they dont pull into the wood. Definitely put washers under the nuts.
Once the deck frames and side knees are in, and the deck battens are in, we can start on the carlins. These are pieces that run fore and aft on the boat, they support the side decks and, along with the deck frames, define the cockpit. They are curved to somewhat follow the sheer clamp. but they do have their own curve.
They were pretty tricky to fit. The way I did it was to mark each of the beams where I wanted the Carlins to land, and screwed a small block there to hold it. Then I used a bar clamp to pull the center in to the side knee so that I could mark everything. I cut the notches in the knee and the deck beams and then installed them the opposite way. I put two screws into the knee, and a clamp for safety, then went to the other side of the boat and grabbed each end of the carlin and pulled towards me, evenly. They dropped into the notches and I was able to glue and screw everything into place.
Step 14: Fore and Aft Decks
I thought I should get some primer in this hull before installing the decks. But I did have to cut the pieces out so that I could get the bow planks out of what was left. I installed these pieces and primed the entire inside of the boat. Next I painted the underside of the deck pieces and installed them.
Here is how I did it. I had a bit of trouble on the first one because of the arch of the deck. So I will show how I did the second one. As shown in the photos, I clamped a couple of sticks to hold down the sides so that I could get some screws into the wood and hold it down It did not want to stay there. so I used countersunk screws with washers and I ran the screws down slowly so they wouldn't simply pull right thru the wood. Yes, The Force was strong in these decks. (sorry)
After the adhesive sets I will take the screws out one by one and remove the washers and reset the screws flush to the decks.
Now on to the side decks.
Step 15: Side Decks
First clamp the side deck in place with the corners flush with the carlins and the ends overlapping the fore decks. Mark one end with a straightedge, cut, butt it into place and mark and cut the second one. I recommend doing these one end at a time so that you can "sneak up" on the proper fit. You want it tight as possible with no gaps. You would be surprised how small a difference there is between "Just right", and "Big Gap". I always say that the major difference between a rough carpenter and a fine carpenter is knowing which side of the line to cut.
Even though the ends were pretty well supported by the sheer clamps and the carlins, I still put a small support block in there to make sure.
Once the ends were fitted I clamped it back in place and reached under to trace the carlin onto the side deck. I cut this line away from the boat with a jigsaw. Once this cut was sanded, it was ready to go back in permanently. Lay a bead of adhesive along the frames and place the piece and nail it into place.
So now I am looking at 22' of excess plywood that needs trimming. It made me tired just to think about doing all this with the Dozuki Saw. So I flipped the boat over and cut it with the jigsaw, up side down pressed up against the deck with my thumb on the trigger. This worked well Mostly. But in a few spots where I got in a hurry I tore up the top layer of the plywood. Just more work for the finisher. (me)
Step 16: Coamings
Coamings are vertical pieces that surround the cockpit. They usually stand proud of the deck, in this case by about 1 inch, to keep water out of the cockpit should it come over the deck. I used 3/8ths exterior ply wood. You want to do the long pieces first . I started with 6 inch strips. After fitting all of the pieces and holding them in place with a couple of screws, I used the T shaped part of my quick square to mark all the way around. You could also use piece of wood that is the proper dimension. What is the proper dimension? That's up to you. I really don't use a tape measure that much. I prefer to put pieces in place and mark them. I find that to be more accurate. Anyway if you are able to cut these parts in place, do so. If not, remove, cut and replace. I removed the short pieces and cut the long ones in place with the Dozuki saw. I then went around the outside of the coaming and the inside corners with 5200.
And that about wraps up the woodworking portion of our program. Tune in next time for "Prepping and Painting".
Thanks for checking out my 'ible on building Pintail. I hope you will vote for me in the contests I have entered and if you enjoyed this and would like to see more, don't be afraid to follow me so you can be notified of my next one.
Cheers!
Greg
ArtisanEclectic
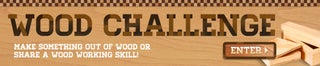
Participated in the
Woodworking Challenge
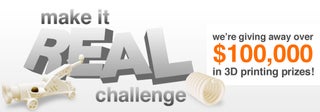
Participated in the
Make It Real Challenge