Introduction: Plastic Shredder for Making 3D Printer Filament
While 3D printing continues to decrease in cost, it is still a large investment. Even after the initial purchase of a printer, purchasing plastic filament still remains a costly affair. One of the best goals now in the printing community is to allow the user to lower the cost by producing their own filament. Many companies and individuals are trying to fine-tune designs on filament extruders, including some excellent designs seen on this site. Eventually, the settings and methods for printing will allow for almost any type of plastic to be used, making any recyclable plastic a source of printing material!
One item that seems to be lacking is an efficient means of granulating plastic in order to feed into an extruder. Most designs use pre-formed plastic pellets, which are also expensive. If a person could shred waste plastic or failed prints to feed into an extruder, the cost of printing material would be greatly reduced. Searching the internet reveals some impressive and well-build plastic shredders, but the complexity and cost are significant. This Instructable will show a proof-of-concept of a simple, low-cost, hand-operated plastic shredder for starting the process of reusing waste plastic for printing.
Step 1: Concept
Two coaxial hollow cylinders (steel pipe in this case) are used as a cutting mechanism. The outer cylinder remains fixed in place, while the inner cylinder is free to rotate within. A slot is cut into both cylinders, such that when aligned, plastic from a hopper above is allowed to fall into the opening. The edges of the slot on the inner cylinder are sharpened to create a cutting edge. As the inner cylinder is turned, the plastic will be caught between the stationary outer cylinder and the rotating inner cylinder, and will be cut much like using a pair of scissors. The cut plastic will be contained within the cylinders, and by mounting the cylinders on an incline, the pieces will be able to fall through the cylinders and out to a collection container. By varying the size of the opening, larger pieces of plastic can be restricted from falling into the cylinders, giving control over the size of the plastic pieces produced.
Step 2: Materials and Cost, Tools Required
Depending on what tools and materials you have on hand, or your level of resourcefulness, this device can be built for anywhere from free, to about $30!
Cylinders: Any two pieces of pipe made of a hard material that can be sharpened and hold an edge can be used. One piece of pipe must be able to fit inside the other and rotate smoothly. For this proof-of-concept, I used one 1-1/4" and one 1" black steel nipple, both 6" long. While this worked, the gap between the two pipes proved to be inefficient, much like loose scissors.
Handle: I used a piece of 1/2" round steel rod
Hopper and Body: I used some scrap wood and screws for no other reason than because I felt like playing with it! This shredder works best mounting it in a vise, and it is perfectly suitable to simply clamp the outer cylinder directly in the vise, with no body required! Also, because the force is only exerted on the two cylinders, the hopper does not need to be made out of any rigid material, or be mounted rigidly. A plastic jug and duct tape would work just fine!
Retention pin: I first used a piece of all-thread rod, but ended up using a nail
Tools:
Angle grinder
Metal cutting disc
Drill
Drill bits
Tape measure
Marker
Rotary tool
Grinding stone
Safety glasses
Gloves
Other helpful tools:
Drill press or drilling guide tool
Center punch
Hammer
Square
Aluminum channel or angle iron to use as a straight edge
File
Reciprocating saw with metal blade
Piece of paper
Piece of pipe to help hold items being cut
Jigsaw for cutting wood (or scissors or utility knife if using plastic jug for hopper)
Hole saw bits
Step 3: Making the Cutting Cylinders: Outer Cylinder
The threads extend about 1" in from the ends on both pieces of pipe. Starting at the end of the threads on the larger pipe, measure 3" down the length of the pipe (4" from the end). Use a piece of paper to draw a line around the pipe at this spot. This line will be 2" from the opposite end of the pipe.
Use a straight edge to draw a 3" line from the circumferential mark up to the threads. Bend a tape measure around the pipe, and make a mark 1-1/2" from that line, and mark a parallel line. The threads will make the fourth line marking out the slot to be cut.
Wearing safety glasses and gloves, use the angle grinder to cut out the slot along the marks. You will probably need a vice or some creativity to hold the pipe while cutting. Keep your fingers intact. Since this was just a proof-of-concept, overcuts and lack of precision were acceptable.
From this point on, the end of the pipe that the slot touches the thread will be referred to as the short end, and the end that the slot is one inch away from the thread will be referred to as the long end.
Step 4: Making the Cutting Cylinders: Inner Cylinder
Insert the smaller pipe into the short end of the larger pipe, such that all of the thread of the smaller pipe sticks out. Use the marker to trace the slot onto the smaller pipe, then cut out the slot on the smaller pipe with the angle grinder. Both pipes should now have a short end and a long end.
Step 5: Making the Cutting Cylinders: Drilling the Hole for the Handle
Now to drill some holes for the handle, and to create a way to adjust the cutting size of the shredder. All the holes were drilled in the threaded areas of the pipes. Had I been smart, I would have filed or ground a smooth surface into the threads and used a center punch to mark the spot. Since I didn't, I broke several of my smaller drill bits trying to start a hole between the threads.
The handle for turning is attached to the smaller pipe. I aligned the holes such that the handle would be vertical when the slot of the smaller pipe was facing upward, as I liked the position this would give when the smaller pipe would start cutting the plastic. Measure in from the LONG end of the smaller pipe one inch minus half the diameter of your handle, and mark the location of the hole (in my case, 3/4" in for a 1/2" handle). This way, the handle will just touch the end of the threaded area. When the inner pipe is inserted into the larger pipe SHORT end first, the handle will keep the slots in both pipes aligned. Using a drill press or drill guide, and another pipe inserted into the small pipe to hold it still, drill a pilot hole into the smaller pipe. Let the bit pass all the way through the pipe and find its own resting point on the opposite wall, and continue the pilot hole through the other side. Increase the size of the bits used incrementally until the hole is the desired size for the handle.
Step 6: Making the Cutting Cylinders: Drilling the Cutting Size Adjustment Holes
Next, drill some holes into the thread on the LONG end of the larger pipe. I drilled 3 sets of holes passing through the pipe, spaced about 1/2" apart, and 1/2" in from the end, with the first set of holes being horizontal when the slot of the large pipe is facing upward. These holes will allow a pin to be inserted through the base and through the larger pipe, keeping the pipe stationary with respect to the base. By having a few sets of holes drilled, the larger pipe can be repositioned to decrease the size of the opening that the plastic falls into. I drilled these holes out to 1/4" because I planned on using a 1/4" rod for the pin, but I ended up using a nail for the pin instead.
Step 7: Making the Cutting Cylinders: Making the Cutting Edge
Using a rotary tool with a grinding stone, sharpen the long edges of the slot of the smaller pipe, such that the edge slants toward the inside of the pipe. If both edges are sharpened, the shredder will be able to cut in both directions. If desired, the larger pipe can also be sharpened with the edge slanting outward. Wear gloves. I didn't and ended up picking metal splinters out of my hands for 2 weeks.
Step 8: Making the Cutting Cylinders: Add the Handle
The last part of the cylinder assembly is the handle. A two-foot-long handle gives some good leverage for cutting thicker plastic. If the handle does not slide nicely into the holes in the smaller pipe, encourage it with a hammer. I used 1/2" diameter round steel rod.
Step 9: Building the Base: Inner Piece
As stated before, the base is not necessary if you are not planning on varying the size of the plastic shredding, but it does make operation easier. If not making a base, the cylinder assembly can simply be clamped in a vise.
Using a scrap of two-by lumber, I marked out and cut the inner portion of the base so that the cylinders would sit with the handle end tilted upward. This would allow for the shredded plastic to fall down through the pipes into a collection container. The only important part of the base design is that the base does not extend past the short end of the outer cylinder, so as not to interfere with the handle rotation.
Step 10: Building the Base: Outer Pieces
To make the sides, lay the inner portion of the base on the material to be used for the side, and use a square to make lines perpendicular to the direction the cylinders will be laying. I used some scrap on 1"-thick wood, but as this is not load-bearing, any size will suffice.
Cut out this shape using a jigsaw. I wanted a larger hopper on the system, so I planned on adding more wood to the outside. To allow plastic to be guided toward the cylinder slots, I cut the top of this piece at a 45-degree angle slanting inward.
Make a mirror-image of this piece for the other side, cutting the slant at a 45-degree angle in the opposite direction. Now, the larger pipe can be seated onto the inner base piece, and sandwiched between the outer pieces. Because the 1-1/4" of the larger pipe is the inside diameter, and because 2-inch lumber is closer to 1-1/2", there will be some gaps when everything is put together. Srcrews or nails will hold everything tightly.
Step 11: Building the Base: Adjustment Pin Hole
Now mark the location for a through-hole in the base for the pin. It is easiest to place the 3 parts of the base and the larger pipe together, and reach the marker in through the end of the pipe into the horizontal holes. Or, you can just measure onto the base itself. Drill these holes through the outer parts of the base.
Step 12: Building the Base: Eliminating Gaps
This next part is not necessary, but did allow for the hopper to be made without unwanted gaps. With the 3 parts of the base and the larger cylinder together, the location of the slot was marked onto the inner surface of the outer base pieces.
The sides were trimmed down in front of and behind the slot location in order to let the front and back of the hopper to sit snugly against the cylinder. The fancy notch was just a result of my using thin scraps of wood for the back of the hopper, as well as trying to stay away from the pin hole.
Step 13: Completing the Base
Now, the base parts can be assembled. First, insert the pin through the sides and the larger pipe to get everything aligned. Place the inner base piece underneath, and slide everything together tightly. Screw or nail the three base sections together. The pin and cylinder may need to be removed after the base is assembled in order to complete the hopper construction.
Step 14: Building the Hopper: Sides
For the sides of the hopper, cut two pieces of wood about the width of the cylinder slot, and of the height desired. Fasten these to the side of the base perpendicular to the cylinder orientation.
Step 15: Building the Hopper: Front and Back
The front and back were formed by cutting a piece of wood to width, and marking out the curvature of the pipe at the bottom. I used a hole saw to cut this rounded portion, but a jig saw would be suitable as well. Now that all the pieces have been cut, everything can be fastened by nails or screws.
Step 16: Final Assembly
Place the larger pipe into the base/hopper assembly, insert the pin, and insert the smaller pipe and handle into the larger pipe, and the plastic shredder is now completed!
Step 17: Adjusting the Cutting Size
To vary the size of the plastic shredding, remove the pin and rotate the larger pipe to one of the other sets of holes, and re-insert the pin. This decreases the size of the slot opening to the hopper, which restricts larger pieces of plastic from entering the cutting region.
Step 18: Shredding
Mount the shredder in a vise, and place a collection container under the rear of the cylinder assembly. Drop the plastic to be shredded into the hopper, and rotate the handle to begin shredding! Larger pieces may need to be cut so that they can fit into the slot. Or, you can just build a bigger shredder!
Once the plastic has been cut on one size setting, the opening can be decreased, and the plastic can be shredded to smaller-sized pieces
If the inside of the cylinders become clogged, push a rod in through the handle end of the shredder to push the shredded plastic through.
Step 19: Improvements
It was difficult to find suitable sizes of pipe at a hardware store that would fit together nicely. This left little choice as to the amount of gap between the cylinders. It rather was like trying to cut paper with loose scissors. Some pieces of plastic would fall into the slot, and the top would bend and get squeezed between the larger and smaller pipes rather than being cut. This is the most significant factor that could be improved upon.
Another possible improvement could be to make various-diameter inserts for the cylinders, so that the shredding size can also be adjusted by limiting the depth to which the plastic can fall into the cylinder.
Hopefully by presenting this design, someone can get an idea for an improvement, and in the future we can re-use waste plastic as a cheap source of 3D printing material!
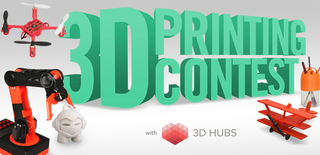
Participated in the
3D Printing Contest