Introduction: Plunge Router Base for a Fixed Router
For many beginning woodworkers, the dilemma of whether to buy a fixed or plunge router (and when/why to use one over the other) can be confusing. For most projects, a fixed router will take care of the job handily, but there are times when a plunge router is helpful or necessary. Purchasing a combo router kit can sometimes be prohibitively expensive, and for those who already own a fixed router but find themselves in need of a plunge router for a particular project, it isn't always possible or reasonably affordable to find a manufacturer-produced plunge base for their specific model.
I found myself in the latter situation - unable to find a plunge router base for my Ryobi fixed router available separately - and wasn't particularly thrilled about buying a whole new plunge router that I would only find the need for occasionally.
Thus, the inspiration for this project was born, and I found that with minimal cost and effort, I was able to fabricate a perfectly functional plunge router base that I can easily attach and remove from my fixed router. This design can be slightly altered to accommodate nearly every model of fixed router that you might own, and can be done for the right price (already owning some of the mats, the parts needed cost me under $30) and with tools that even the most novice woodworkers will own.
______________________________________________________________
Tools Needed:
Router
Hacksaw
Power Drill & Bits
Ruler or Measuring Tape
File
Dremel (not necessary but came in handy)
Safety Gear (eye protection, gloves, respiration mask, etc)
______________________________________________________________
Materials Needed (I'll specifically address the parts that I used for my design later in this instructable, but many of these will need to suit your particular router model):
Lexan Acrylic Sheet (this is what I used for the body of my plunge base, but this could be made using wood/metal/plastic/hard rubber/etc)
Cardboard (for mocking up your design shape)
Copper Tubing & Caps
Aluminum Round Rod
Threaded Rod
Compression Springs (the limited selection at my local hardware store influenced the dimensions of the rest of my design)
Epoxy / Cold Welding Mixture (I used JB Weld epoxy but anything with a high PSI rating will do)
Assorted Bolts, Screws, Washers, etc. (depending on how you want to attach your plunge base attachment to your fixed router)
Step 1: Imagine Your Design
Inventor Nikola Tesla was famously able to create entire complex designs for his inventions solely in his mind, test-run and troubleshoot any potential mechanical issues to redesign his idea, and even measure out parts using nothing but his imagination. When he sat down to finally build his creation, it had been so thoroughly examined and vetted that it was usually assembled and operated without issue - this includes very complex mechanisms like the modern motor.
It's fairly safe to say that his skill surpassed even the best builders here on instructables, but I find this process to be very helpful nevertheless. I encountered a few well-defined problems with my original design before ever putting pen to paper (or cardboard, in this case), and though I certainly didn't account for every detail of my idea prior to building it, I saved a lot of time and frustration simply by carefully imagining and visualizing how this mechanism would work.
The idea is fairly simple: Build two parallel plates (again, I used acrylic sheeting, but this could be substituted with a number of different materials) that are separated by an enclosed compression spring mechanism, design a way to attach the top of these plates to the bottom of your fixed router, and find a way to control how deep your router bit can plunge into your cutting surface.
I began by examining the base of my fixed router. Most routers have a removable plastic ring on the bottom of their router base, and this can be used to gauge the necessary size of your plunge router base as well as to determine how best to attach your plunge base. For the first issue, I traced out this plastic ring onto a sheet of cardboard and drew out the shape of my base while keeping in mind the four rods that would be incorporated into the bottom sheet of the plunge base.
In order to have the two parallel acrylic sheets of my router base compress to as small of a distance as possible during use, I realized that both the springs and the aluminum rods used to compress them had to sit almost entirely within the copper tubing when fully compressed. This required me to extend the copper tubing well above the top of this plunge base, which was an important design consideration as I had to avoid any conflict with the body of my fixed router.
Now that the idea has a form, it's time to get cutting.
Step 2: Cut Your Lexan (part 1)
With the cardboard sheet cut to the necessary size, I traced it onto a block of 3/4" MDF that I would use as a jig for cutting the Lexan sheets. Lexan is a common hard acrylic sheeting available at any of your large hardware retailers. It comes in a variety of dimensions including thickness. In my case, I had some acrylic sheeting left over from my Cheap Picture Frame build. This sheeting was only about 1/10" thick, and though Lexan is supposedly much stronger and less brittle than glass of equivalent thickness, I knew that this was too thin for my purposes. Thicker acrylic sheeting can become exponentially more expensive, so I decided to superglue two sheets together to increase strength and rigidity.
After cutting my wood block jig out with a jigsaw and sanding down the edges to my desired shape, I covered it on both sides with a few strips of double sided tape to hold both the wood jig and the acrylic in place while I routed out the edges. With a 1/4" flush trimming router bit, I followed along the edges of my jig, cutting out four identical Lexan plates. Making sure that they were lined up exactly, I then covered one plate with superglue and attached another, clamping them down for a few minutes to dry.
With my two pairs of plates now intact, I needed to cut out a circle in the middle of each to allow for router bits to penetrate through them when plunging. This doesn't have to match the base of your router exactly and, as you can see, my end product left plenty to be desired in terms of aesthetic. I just drilled a hole in each plate large enough to insert a router bit (if only I had a plunge router...) and then cut out a circle freeform. It might help to use a Dremel with a sanding attachment to clean up the edges of these circles as well.
Step 3: Cut Your Lexan (part 2)
Now that the edges and center hole are cut, it's time to drill out the slots for our aluminum shafts and copper tubing. The way I envisioned this design was to have the aluminum shafts seated firmly in the top of the bottom base plate. These would then protrude into the copper tubing on the top plate, compressing the springs in the process. It's up to you to decide where to position these holes for your shafts and tubing, but consider the existing design of your fixed router to avoid any conflicts. When looking at my router in the normal upright position, I decided to have the copper shafts positioned on the top and bottom of the edges of the base while the router handles protrude from the two sides (see pictures of the finished product if this is confusing).
As a general note for this build, I recommend using forstner bits whenever you are drilling holes through your Lexan. I was lucky enough to learn this during the last step in which I drilled out the center hole. When using a standard twist drill bit, it can be very easy to apply too much pressure or torque and crack your acrylic. I found that forstner bits seemed to do this job much better without taking the chance of cracking your recently machined acrylic plates. That being said, keep an eye on your forstner bit while drilling, as I found the need to scrape away any acrylic that ended up accumulating on the tip of my bit. This acrylic heats up during the drilling process and invariably seems to melt and dry on to the tip of the forstner bit, as evidenced in the picture above. Take your time with the following steps, as you don't want to ruin one of your plates in the process of hastily drilling your last hole.
Bottom Plate:
You are going to cut two sets of holes in this plate: two for the aluminum shafts, and two for the threaded guide rods. I used 1/2" aluminum round rods for the shafts, and a 1/2" forstner bit allowed these to fit snugly. I drilled only about half way into my bottom plate for these two holes. The forster bit accomplishes this task with no trouble at all, and it ensures that the shafts are seated firmly in place and that the base of my plunge router is perfectly flat on the bottom. I then used a 3/8" bit for my guide rod holes in the same fashion.
Top Plate:
You want to make sure that you are as precise as possible when drilling your holes for the top plate, as there wont be much wiggle room for your two pieces to assemble together. After carefully marking the center of my corresponding holes on the top plate, I used a 5/8" forstner bit to drill out the holes that my 1/2" copper tubing will sit in. Since the diameter of my copper tubing is listed for the interior dimension of the tube, I needed a slightly larger hole. Once again, I drilled 3/8" holes for my threaded guide rods in the same place as the bottom plate. On this plate, you want to drill all of the way through for all four holes.
The last step is to figure out how you want to attach your plunge base to the bottom of your fixed router. Most modern routers feature several ways of affixing your router to a router table, and the most common way is using some bolts with the pre-threaded holes in the bottom of your router base. Find the corresponding bolt size for your router, measure out the location of these holes onto your top plate, and drill the corresponding holes. Make sure to test out attaching the top plate to your router base before you move on to the next step.
Step 4: Cut Your Rods & Tubes
With your holes cut and standing by, you can begin the process of cutting all of your rods and tubes to size. For this step I used a miter box and hack saw (clamps will help you keep your rods in place). The lengths of each of these pieces is largely dependent on the exact dimensions of your router as well as how much plunge you want to get out of your attachment. For me, the process of designing and cutting all of these rods started with the springs. I went in assuming that there would be a decent selection at my local hardware store. I found this not to be the case. There was really only one size of compression spring that would suit this project, so this influenced how I decided upon the size of my aluminum rods and copper tubes.
The springs I used were 2.5" long and 3/8" wide, and I stacked two of these into each copper tube. This seemed to supply sufficient tension to hold my router up all of the way when sitting on the plunge base, but didn't require too much pressure to compress them all of the way during use. Using an uncut aluminum rod and copper tube, I marked out how much I could compress the two springs stacked on top of one another in the tube, and used this to determine the necessary lengths of the rod and tube.
As such, I then cut my 1/2" aluminum rod into two 2 7/8" shafts, and cut my 1/2" copper tubing into 5" long lengths. This allowed for the aluminum shafts and two fully compressed springs to sit completely inside the copper tube, and provide about 2" of plunge for my router bit when fully assembled (and when using the longest bit I own with the router depth set to maximum). This is plenty of plunge for nearly any job that I'm going to encounter, and was the best that I could do with the springs that I found available.
As for the threaded guide rods, I determined that 3 3/4" was a sufficient length. This could have ended up being slightly longer or shorter, but this size offered plenty of room on either side. The purpose of these threaded guide rods is twofold: 1) They provide more lateral stability for the plunge base, diminishing the amount of wiggle that the base would have if it only used the two shaft/tube components for support. 2) Using a threaded rod allows the user to control the amount of plunge the router can accomplish with the help of two sets of nuts. If I only want to plunge 1/2" into my cutting surface as opposed to 2", I need only to compress the plunge base, measure out the necessary depth of my router bit, screw the nut to this distance and it's ready to go. Also, using another set of nuts on the ends of the threaded rods ensures that the plunge base stays intact when not compressed. Otherwise, shafts in the bottom plate of the base would fall right out of the copper tubing.
Once your rods and tubes are cut, make sure that the cut ends are nice and smooth. You'll no doubt encounter some sharp jagged edges and burrs after cutting this metal. I used a file to smooth out the outer edges of my rods and a Dremel grinding bit to clean out the inner edge of the copper tubing. Be aware that filing down the edges of your threaded rod requires some detailed attention, as disturbing the nature of the thread may make it difficult or impossible to screw on a nut. Take your time here and ensure that both ends of both threaded rods can receive a nut before moving on to the next step...
Step 5: Epoxy and Assemble
I'll begin this step by saying that the first epoxy I used did not suit my project well, and I ended up having to backtrack slightly and administer a different epoxy. As I had some left over from a different project, I decided to give JB Weld Steel-Reinforced Epoxy a try. Though the PSI rating was sufficient for my needs, I found this particular A/B mixture to be particularly hard to work with, and quite messy. I ended up having to scrape off a good amount of excess dried epoxy on the plates, aluminum shafts, and threaded rods. Also, I wasn't able to be precise enough when applying it to my copper tubing, and ended up having to pull the tubes out and re-adhere them using a different epoxy.
After a little research, I ended up buying some JB Weld ClearWeld epoxy. This was much easier to work with, set very quickly, and better yet dried completely clear. So with all that being said, do your research when finding the right adhesive for your job and save yourself the time and trouble that I didn't manage to avoid.
In addition to gluing your rods and tubes into your two base plates, you'll need to epoxy your copper caps on to your tubing. This will serve as the point of your plunge router attachment that receives the most amount of pressure in the whole assembly, so make sure to apply a liberal amount of epoxy with a high enough PSI to ensure your safety.
Once the rods and tubes are glued in place, I recommend finding a way to let them set and harden that ensures all of the pieces dry in a perfectly upright position. If you leave these to set and one or more of the rods hardens leaning slightly to the side, the whole apparatus will be unusable and you'll have to backtrack. I found the best method was to place a loose block of wood in between the two bases and utilize each base to keep the other in position. After waiting the amount of time designated for full hardening with the epoxy that you choose, hopefully you'll find all of your rods and tubes in a perfectly upright position and ready for assembly.
Take the top plate and align it with the holes in the bottom of your fixed router's base plate. Use some bolts to secure the top plate to the bottom of your router. Insert your springs into the copper tubes, screw a nut onto each of the threaded rods all the way to the bottom plate, insert your rods into the appropriate holes and add another nut on to the end of each threaded rod. You now have a fully assembled, (hopefully) fully functioning plunge router attachment for your fixed router! There's only one thing left to do:
Step 6: Try It Out!
Fully decked out in your safety gear, give the plunge base router attachment a test drive on a piece of scrap wood. There will naturally be a little bit of lateral wiggle room in the base due to the nature of the adaptive design, but with a slow depression into your wood you should have no trouble controlling the bit's progression into your cutting surface. With this attachment, you should be able to accomplish nearly any task that requires a plunge router, and at a fraction of the cost.
This project met a lot of my needs: it was cheap, gave one of my favorite tools new capabilities, challenged my ability to design, and - more than anything - it produced a product that doesn't exist in the market: a fully adaptable plunge base that can accommodate nearly any fixed router available. I appreciate you reading all the way through, and good luck with your future builds using this attachment! If you end up building one of your own, please share your results below. I'm sure our woodworking community can come up with some awesome ways to improve this design.
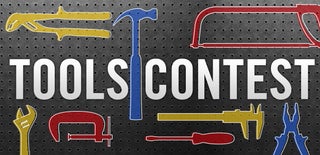
Participated in the
Tools Contest
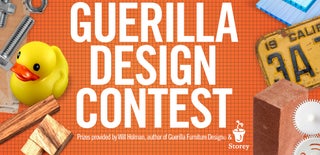
Participated in the
Guerilla Design Contest