Introduction: Plywood Floor Lamp
I have finally got something to post.
Here is something I worked on last summer. ( well not really, it is a rendering I did last night ) Keep looking, you'll see.
The challenge, make something out of one piece of 4'x8' - 3/4" Plywood. Sounds simple enough,,,one thing I added to that was I wanted to see if I could do it without mechanical fasteners.
Challenge on.
I have included a PDF of a drawing package that I made for this instructable. It has some of my original design revised with "as built" modifications.
Also included, DWG and DXF files of the profiles for anyone with a CNC mill or router. (I just noticed a rib profile missing, i'll fix that soon and replace the files here soon. Till then, if you know your way around a DWG editor you can "copy/paste" one of the other ribs and modify it very easily to reproduce the missing part.
Finally, STL files of a simpler but still articulating version of this. Available for those of you who are lucky enough to have a 3D printer and want to play around with this.
I if you download these and find issues, let me know I will be happy to try and resolve them
NEW!
Just added for hand cutting DIYers, a PDF of all the profiles 1:6 scale for 1/8" thick material of your choice. Just stick it down and cut away. Use mill board, fun foam, balsa wood, ply...the list goes on and on. enjoy!
Attachments
JA-Plywood Lamp- Instructables.PDF
Lamp- 1-6 SCALE Instructables.PDF
JA-Plywood Lamp- Instructables Metric Dims.PDF
John Allen- Lamp- Profiles- instructables .DXF
John Allen- missing parts - Lamp- Profiles- instructables- .DXF
John Allen- Lamp- Profiles- instructables .DWG
John Allen- missing parts - Lamp- Profiles- instructables- .DWG
STL files.zip
Step 1:
I first sketched out some ideas and modeled some parts on the computer.
But then I really just started cutting.
The straight parts were cut simply with a table saw and jigs.
I printed out "size as" (1:1) drawings of some of the profiles for cutting. I spray glued my 1:1 drawings on to some 1/4" M.D.F. to make templates for flush trimming with a router.
For the circular parts, all outside cuts were made on a band saw with a circle jig, inside cuts with a jig saw. I did a few tests with a jig but found cutting free hand worked better for me.
Step 2:
Now here is the best thing I figured out building this thing
The angled notches in the lamp shade ring were done on the table saw. (Those of you who spend more time on a table saw may say duh, or even have a better way to do it.) But for me it made my day.
I placed one of the rings flat on my table saw and set it up as if I were going to cut it right down the middle into two halves. I then raised the blade till the radius of the blade matched the angle on the ring I was cutting into. With my paper drawing spay glued onto the ring to show me the material to take away I did it by eye just using the 1/8" kerf of my saw blade. Of course a dado blade, fence and stop may have been more accurate, but i was done in the time it would take to set that up. Besides, you see the pictures, can you tell?
Step 3:
Easy parts first
These parts were just ripped on my table saw, cross cut to length and with an extra wide dovetailing jig I made some cuts.
Forstner bit for the holes.
The round parts that look like pucks were solution number one for avoiding mechanical fasteners. I ripped two pieces of ply (about 1.5"X24" with the blade tilted at 30 degrees) and glued them together. ( which was a bit of a hard pill to swallow because I was trying to do this with out glue too) but it made these parts more structurally sound. This made a longish stick that was a hexagon in cross section. Long story short...I turned it on my lathe to be a snug fit into holes I drilled with the forstner bit and cut it up into 0.75" pucks.
Step 4:
Optical illusion alert
The rectangular holes on the disks are the same size...they have to be in order for this to work. check out simultaneous contrast for an explanation.
Since I gave in and used glue on the other parts I used it to make the wedges as well. I could have made them with out glue but I thought the design I came up with is the strongest I could think of. A lot of forces are applied to this simple part. The notch or hook I put on the wedge was to make it easy to disassemble.
Step 5:
Okay here is proof that I am a hack.
This "stepped notch" foot design comes from of the fact that I did not want to put notches into both disks. Reason being, I wanted this to go together any way or orientation and to get the notches to line up in all instances is very difficult to do by hand and by eye. As it turned out when these feet slip in they really lock in nicely....ahem, just like I planed it...right from the start.
Step 6:
Beware pets and small children
Largely due to the fact that I wanted to get all cute and fancy with the no mechanical fasteners idea, this design needs some help.
To defy gravity this lamp relies on friction to stand up. If I were to use some hefty spin on lugs to connect the side plate to the arms I would have enough clamping force to confidently leave this standing and know it won't wreak havoc and terrorize my two schnauzers. There is also way a to use spring force to counter the effects of gravity.
All that being said, whacking those little wedges into the trestle connector works quite well, certainly does the job.
I am curious and would like to stress test these joints some time. Maybe when i get sick of it hanging around.
Step 7:
Well there you have it.
That's all I got for now folks.
If you made it this far I would like to think you enjoyed it. Thanks for looking.
I am happy to answer any questions you might have about this project.
In addition to anyone with CNC router you want to keep busy, maybe we can talk.
So long for now,
John
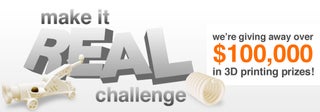
Participated in the
Make It Real Challenge