Introduction: Pocket Lathe
Sometimes building small items requires small tools. This pocket lathe is 8 inches wide, 3 inches deep and 4.5 inches tall. Yes it does fit completely in my jacket pocket and cargo pants pocket.
Please note that there are some ideas for improvement posted at the end of this Instructable. This started as a desire to make a miniature chess set
Step 1: Order Parts
I disassembled an inkjet printer to get the motor that drives the print head. This motor has enough power for turning pine and other light woods. It is too weak for working with aluminum or copper.
The bearings and support blocks are from vxb.com
The gears are from sdp-si.com
I used some scrap pieces of ¼ inch hard board to make a base stand.
You will need 2 of the ¾ inch shaft supports part number WH12A
You will need 2 skateboard wheel bearings 608ZZ type
You will need drive gears or belt system. This is completely dependent upon your motor selection.
I used nylon bevel gears for a reduction in the motor speed 1:2 (24/48).
Step 2: Assemble the Rotating Parts
Begin by enlarging the opening in the shaft supports. These started out at ¾ inch and needed to be 7/8 inch. I used standard drill bits to accomplish this. You only need to enlarge the hole about half way through the thickness of the support.
At this time you install the bearings and tighten the support.
The bearings go towards the inside of the working area.
Step 3: Make the Holders
Select another 5/16 X 2 inch bolt and perform the same tooth cutting procedure.
Put the 1 inch bolt through the bearing and support, use several spacer washers and tighten down with a 5/16 nylon lock nut. The bolt should rotate freely but not wobble.Place the 2 inch bolt through the drive gear with the bevel facing he bolt head. Then use 9 spacer washers then put the bolt through the support block and bearing then use another spacer washer and a nylon lock nut. Again tighten until the drive mechanism rotates freely but does not bind. The drive gear should not slip on the shaft.
Step 4: Make a Chuck
This step is optional and will require you to know how to braze or weld. When you are completed you will have a 4 jaw chuck. I cover a 3-Jaw chuck in my mini metal lathe Instructable.
You will need a ¼ inch fender washer and 5 5/16 regular nuts. Along with 4 5/16 set screws.
Thread one of the set screws into one of the nuts with the bevel of the screw protruding through the back enough to center the nut in the fender washer hole. The nut must sit flush to the washer. Braze the nut to the washer then remove the set screw.
Turn the washer over so that the nut is on the bottom.
Thread 2 nuts onto a 5/16 2 inch bolt and space them apart enough so that the outer edges of the nuts are at the edges of the fender washer. Lay the assembly across the washer center and braze the nuts in place.
Repeat this step one more time and braze the nuts at 90 degrees to the first set.
Clean the piece and finish as desired, I primed and painted it flat black.
You might want to use some thread locker on the set screws. Make sure all screws are tight before turning on the lathe.
The nut on the back threads onto the drive shaft as shown in the main picture.
Step 5: Make a Base
The base is 2.5 inches wide by 8 inches long. Using the motor and gear drive block, mark the position if the desired holes. Drill the holes for the drive motor and drive support.
Using the tail support block mark the holes for mounting at both the farthest and closest points on the base. Using a ruler mark off the slide holes that are needed for the work piece support block. These long holes will allow for adjusting the work area for work piece size and will also be used as a manual clamp for the work piece.
Drill and cut all the holes then build the base using additional pieces of hardboard that are cut to size. I 4 pieces the same dimensions then cut one of these in 2.5 inch sections for use as end pieces. Assemble the base then glue to hold together. I used super glue but wood glue would also work. Finish the base as required. I primed and painted it flat black.
The motor mount is made from a 2.25 inch piece of 1 inch aluminum angle.
This was visually aligned to the drive support block and the existing motor support. This was then marked, drilled and tapped to create the support clamp.
The motor is attached first then the support is places in the base and the drive block is bolted to it. Align the block so that it is square to the base.
The tailpiece slide lock is made from 1/2X1/4 in aluminum bar stock that is slightly narrower than the base of the support block. Visually align the two then drill and tap, I used 10-24 socket head bolts due to the fact that the Allen key needed to tighten is the exact same size as the set screws used in the 4 jaw chuck. Place the slide lock under the base and bolt the tailpiece support down.
Step 6: Assemble and Test
The wiring is quite simple, you will need a switch and a power supply. I chose a 12V 1A wall wart as mine and it seems to have enough power. It is also small enough to store in the base of the lathe when not in use. The socket for the wall war was located at the back and the power switch was located at the top near the drive gears. The power is connected directly to the motor with a switch in series.
The red wire goes to the + motor terminal and the black goes to the -. These were soldered in place.
The power of this unit is quite low so accidentally coming in contact with the gears or chuck will typically give no injury. I ran my cutting tool into the chuck while testing the lathe, the tool did not break and the rotation stopped immediately. Also if you try to take too much material off at once the tool will bog down
Make sure that the drive shaft turns counter-clockwise otherwise the chuck will not stay on the shaft. If it does not reverse the polarity of the motor wires.
Step 7: Make a Cover
The hollow base is used for power supply and tool storage.
I decided to make a vinyl wrap to secure all the components. I rough measured then used a spray adhesive to keep teh halves from rubbing. Then folded in half, cut to the correct dimensions then stitched along the long edge. I cut one end square then stitched the edge. I wrapped the lathe with the vinyl to get the proper length then cut it square and stitched the remaining edge.
It unwraps towards the front so that when you rest your hands down it secures the lathe from moving. I used Velcro for the closing flaps and a small strip was sewn near the back flap for attachment into the base. I glued the center flap onto the inside of the base with hot glue. The flap that is closest to the user has the soft Velcro side to prevent scratching and snagging on clothing.
I had some scrap vinyl left over and made a tool pouch to hold the Allen keys and cutting tools.
My sewing machine is not working correctly, please forgive the unprofessional stitching.Step 8: Final Thoughts
While this can be run on batteries it seems to be a little bit of a power hog so it is advisable to use an external power source.
Since this is a single speed lathe running at ½ the RPM of the motor that used, a PWM motor controller might be nice to give variable speed.
A larger motor from a power drill will be a nice change and would afford more power for working with light metals. I am currently working on this for use with copper and aluminum. The current design is direct drive with variable speed control. I will post it when complete.
Using a belt drive will allow for a size reduction as the motor could be mounted horizontally instead of vertically.
The base could be made from acrylic or plywood
A cover for the rotating parts could be added for safety.
I am in the process of creating a miniature chess set. A rook and a king are shown.
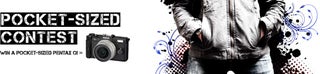
Runner Up in the
Pocket-Sized Contest
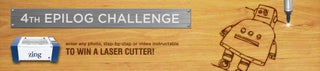
Participated in the
4th Epilog Challenge
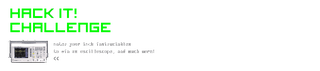
Participated in the
Hack It! Challenge