Introduction: Reanimating Grandpas Old DIY WWII Compressor
I have to paint several parts on my car and therefore I wanted to use one of the old compressors which stand around in the cellar since my grandfather died According to my dad hey build them out of old airplane compressors from planes which where shot during WWII. He drove round the villages and collected this stuff. Must be genetic somehow ;) At first I had to choose one of the two compressors. I`m a pretty lazy guy, so I choose the complete one with a motor in it. Disassemble, clean, reassemble => use... I thought :D
Step 1: Shock No.1
As you can see on the pictures the compressor was totally rotten inside. Everything was covered or nearly eaten up by the rust. But after disassembling, cleaning and reassembling ( everything with metric tools on inch bolts) the compressor really worked. the Problem is the rustparticles comming out of the tank and the lack of power... so of to the next one.
Step 2: Compressor No. 2 => Nice Surprise
This compressor had no motor, but when I turned the wheel it seemed to work. I opened up the head and was lucky to find nearly no rust at all. After a little cleaning and finding out how it works I put on new liquid gasket and reassembled it. Next step was the motor
Step 3: Choosing the Right Motor
By looking at grandpas old electric motors I soon found one which exactly fitted the mount points on the compressor cart. Less work for me :) I placed it and wired it. Good to know for this old electric stuff: groung is red, not green and yellow as nowadays ;)
Step 4: Shock No.2
After about 30 sec of compressing there was white smoke everywhere. The condenser had aged ( it's about 40 years old) and couldn't stand the high voltage. In order to get the compressor working the same day and start spraypainting I decided to attach the motor from the first compressor which was much quieter, consumes less power and which is better transmitted due the the larger belt pulley on the motor. For this purpose I had to make an alloy plate to attach the motor on so I have not to change the mountpoints on the compressor itsself. By this I also could attach some rubber buffers to make the compressor even more silent
Step 5: Testing the Compressor / Shock No. 3
After assembling everything, I decided to test the compressor. Everything worked out well, until at about 10 bar I heard a silent noise of air flowing which got louder and louder. As you can see the adjustment unit which turns the compressor of at a certain pressure just broke in 4 parts. I guess this happed before, because the knob could only be turned with lots of force. But the high pressure of 10 bars gave it the rest. To turn the compressor off at n high pressure the spring inside the unit must be squeezed very strong which causes a constand pressure on the bakelit part above the gasket. when the air pressure gets bigger than the spring pressure the switch on top turnes "off" So I had to disassemble everything, clean it, glue it, reassemble and hope. If the glue is strong enough or the old plastic ( T least I guess its bakelt => old brown plastic part ;) ) breaks again I will make a matching alloy part on the turning lathe...
Step 6: Test It Again
reassemble all the parts (also used new screws so I could tighten them a little easier) and plug it in...Seems to work. I was a little worried because of my new rubber gasket because its a little different from the original one, but it seems to be elastic enough to work. The switch turn the compressor of at a specific pressure... ready to role. Next step is to attach a oiled air filter to prevent the compressor to rust inside because from now it will be outside in my shed where my workbench stands :)
Step 7: Final Shock No.3
After about halb an hour I had the same problem I had before. The glue wasn't strong enough. Because I found no alloy block which was big enough I had to improvise with a block of hart rubber which I normally use when punching holes in gaskets etc. After remaking the part which pushes the switch to shut the compressor off at a certain pressure I used the angle grinder to remove the sharp spike on the adjustment screw. And finally it works :) .... Lets go painting!!!
Step 8: Lets Go Painting
Finally I started painting. Because of the little volume J can paint only one piece in about 5 minutes then I have to wait for the compressor to work again, but it works pretty well :)
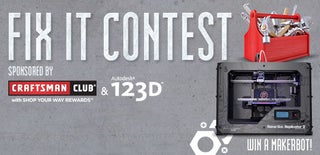
Participated in the
Fix It Contest