Introduction: Recycling Aluminum (Aluminium) - Make Your Own Al Foundry.
It has always been a very fascinating thing to see the things that we as humans have been able to accomplish through time. How we were able to build amazing things, utilizing only our imaginations and the resources around us.
This project is no stranger to these feelings I have and can teach a lot of things to anyone attempting it. We gave it a try at our hackerspace H3 Laboratories
There are various ways that you can do this project of course, so you can take ideas and go melt some aluminum at your house or hackerspace. Invite some people over and melt Aluminum together. It may look simple but it is very enjoyable and camaraderie forming.
Have fun
Keep in mind, that you should do this outside, and stay safe. Get some goggles, welding gloves or better, and closed shoes or boots.
If you choose to follow these recommendations, I or anyone or anything mentioned in this instructable are not responsible or liable, under any circumstances for any personal injuries, accidents. death or bad things that might occur whilst the melting is underway or anything related to the actions you might take by following this instructable. Please use common sense and be safe.
Step 1: What You Need
Aluminum is quite easy to melt, it does not require much heat. Based on what we have here, you can get ideas and adapt to what you have on hand. It is also very interesting to attempt to make this project as low cost as possible.
- Decent speed air source. We used an old ShopVac with a divergent nozzle and clothes drier duct to reduce the speed and increase the flow of air per unit area.
- Safety gear (Dial 911 if something major occurs! Their safety gear is always better than yours) - You will need big gloves, welding gloves can work fine. A first aid kit, and some proper eye protection. Face shields are better, but get at least some goggles.
- Fire Bricks, Granite Stones, or Brick pieces - You need some way to contain your fire. It is best to use Firebricks, you can use any material that does not have water inside and is in general non-porous and therefore cannot absorb water. You can use very dry bricks, but there is always a chance that they might have water inside, in which case they can explode in a variety of ways.
- Sand. - Any sand can do the trick, just make a mound and arrange your fire pit as show in the pictures.
- Steel Tongs - You need some way of feeding your crucible.
- Crucible - This is where the actual metal will be heated, melted, and contained. Any stainless steel container will do, just make sure it fits.
- Bread Pan - You can make very nice looking ingots with a bread pan, the more used the better, because the resin in brand new ones when burned will produce dark coloration on the surface of your solid ingot and decomposition byproducts of Teflon. Do not breathe the fumes produced by this, just to stay safe. Or better yet, just get a cast iron mold or another plain stainless steel mold.
- Scrap Aluminum - You can get this from anywhere, just collect as much as possible so you can have a good amount to melt. Some sources are heat exchangers, heat sinks, cans, hard drive chassis. Try to pre-heat, and dry the aluminum scrap before melting as some water in the metal may cause unexpected reactions, which can be scary or dangerous due to violent failure of a vessel or container. The more solid the aluminum the better such as the aluminum in heatsinks.
Step 2: Put Everything Together
There really is no specific way that you should arrange all the components, you can experiment here and try different approaches to see what gives you the best results.
The only thing to consider for good heat transfer is: make sure that you have good air flow from underneath the coals so that they light up really good and increase their temperature. Remember the brighter the hotter. Also make sure that you have coals high up the length of the crucible, as this will insure the best heat transfer.
You can use the Blackbody radiation temperature color chart to estimate the temperature, or if you have a thermocouple, use that.
http://en.wikipedia.org/wiki/Black-body_radiation#Explanation
Step 3: Time to Pour Your Aluminum!
Now all you have to do is pour your aluminum and let it cool, you can experimenting with cooling rates to change the crystal structure as well, but that would be for another Instructable.
Before pouring you might need to remove the slag that accumulates at the surface of the molten aluminum. In our case most of the slag stayed behind. So we didn't have to, anyways.
Thank you for reading! Post pictures of your melt! Let's Recycle!
This instructables was created by Guillermo Vargas et alia, at H3 Laboratories in El Paso, Texas for the sponsored Instructables challenge.
Any entity or individuals mentioned in this text are not liable or responsible under any circumstances for any injuries, damage, loss , including personal injury or death, resulting from the guide or the execution of these steps.
Stay Safe!
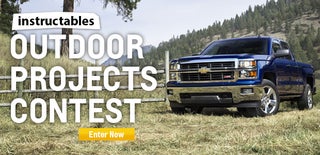
Participated in the
Instructables Outdoor Projects Contest
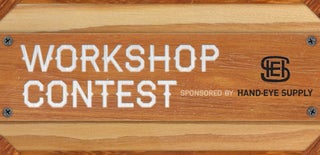
Participated in the
Workshop Contest