Introduction: Retro Shadow Box With Splined Mitres
I have always wanted to make a 50s / 60s inspired shadow box wall shelf to display various items I have collected from my travels. I decided to add some more complexity to the frame by using a spline joint, which adds strength but also gives it some visual appeal. I have used local hardwoods for the project, Jarrah for the frame and Sheoak for the splines to add some contrast. Each of the larger squares are 300mm in length and width.
Step 1: Cut the Frame Mitres
The closest Jarrah stock size I could find to the dimensions I wanted was 60mm x 19mm. I felt the thickness was too heavy for this type of design so I reduced it to 12mm using a thicknesser machine. I then sanded the jarrah boards using an orbital sander with 120, 240 and 360 grits to a fine finish. The reason for sanding prior to any cutting is so that you don’t inadvertently round the edges of your joints with a sander after they are cut. This will result in a less than perfect joint once assembled. Next step is to cut the 45 degrees mitre joints, there is a number of machines you could use to do this including a compound mitre saw or radial arm saw, I chose the table saw. I set the blade tilt to a 45⁰ angle, cut the first mitre and then moved the material up to an offset rip fence before flipping it over and cutting the second mitre. This process ensures that each of the eight pieces are exactly the same in length. Make sure your rip fence is set behind the blade, otherwise the material can jam between the rip fence and the blade causing a safety issue.
Step 2: Cut a Pair of Matching Grooves in the Mitred Faces
This is the tricky bit, the grooves have to match perfectly and must also be of a suitable position and depth. A good rule of thumb is not to extend the groove through more than half the thickness of the workpiece. Note: I cut a few practice joints on some scrap material before attempting with my actual lengths. I decided again to use the table saw set to a 45⁰ angle at the required depth. The only issue I had was the blade on the table saw only tilts in one direction, forcing me to cut the grooves on the other side of the mitre fence. My solution was to setup a sacrificial mitre fence using some MDF, clamped to the mitre fence. This in conjunction with the rip fence allowed me to cut perfect matching grooves on all 16 mitred faces.
Step 3: Cut the Cross-halving Joints
The next step is to measure, mark-out and cut the cross halving joints. Again I used the table saw with a sacrificial mitre fence and rip fence offset to correct length.
Step 4: Make a Spline That Fits the Grooves and Connects the Two Halves of the Join
When I researched this type of join, it is recommended to use crossgrain for your splines. This is so the spline doesn’t split along the grain and come apart. I decided against doing this for a couple of reasons;
1. The finished shelf will have very little load and unlikely to come apart
2. It is very difficult to cut small pieces of wood crossgrain
3. The she-oak material has a very nice end grain pattern.
I ended up milling some slivers of She-oak to the required dimensions - the spline is only as wide as the kerf of your saw blade (approx 3mm). The splines can have a little bit of movement in the grooves, the glue will tighten up the fit. I actually made the splines a bit too snug and ended up sanding them down by hand on a sanding board.
Step 5: Glue Frame and Splined Mitres Together
I used strap clamps and PVA wood glue to assemble the boxes. Always dry-clamp your work first to check for squareness and fit. I kept the splines slightly larger in length so they can be sanded flush once dry. Rub glue over all internal spaces of grooves, mitred faces and spline faces. Check for squareness by measuring internal diagonals.
Step 6: Finishing
The next step was to remove excess glue with a sharp chisel and sand protruding splines flush with a sanding board. I had the opportunity to put the squares through a drum sanding machine, which sped up the sanding time considerably. All other surfaces were sanded prior to assembling the two boxes together via the cross halving joint. I used a wax filler stick to fill in any small imperfections in the visible spline joints. Finally a number of coats of Spray Lacquer, sanding back between coats by hand with a worn piece of sandpaper. Once I was happy with the lacquer coat, I applied a finishing wax with steel wool to give the wood a low gloss lustre.
Step 7: Making Keyhole Hanger Plates and Mounting to Wall
This is the step which I had initially given the least amount of thought to when I started this project, but ended up being the biggest headache! I wanted the shadow box to be mounted flush on a wall and planned on using keyhole hanger plates. However, because I had reduced the thickness of the material, it was now too thin to accommodate any keyhole plate I could find. I ended up making the keyhole plates to match from some brass plate. I cut the brass sheet to size using a guillotine, then used a slot milling cutter on the milling machine to cut the slot and drill the hole for the screw to fit in. Some final finishing with needle files and wet & dry sandpaper. Mounting the plates onto the frame involved some careful l marking out, drilling and chiselling. I am aware there are keyhole router bits you can use for this purpose, but didn’t want to risk screwing up the entire project if I got it wrong. Lastly, I drilled wall plugs into the wall to position box, decorated it with ornaments, finished!
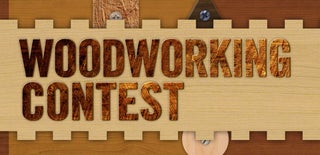
Participated in the
Woodworking Contest