Introduction: Give the Gift of Robot Love
When experimenting in building bobble head kissing dolls I came up with the idea of giving them a geeky twist.
Check out the video:
These robots are made with love and out of love …and the materials described below. They make a great Valentine gift to your true love or you can offer them to anyone deserving your robot love. You can however not sell them: love, even robot love is not for sale ;-)
I usually offer these as kits to be assembled by the recipient, as I love makers and I tend to encourage my “loved ones” into making. I prepare up until step 7 and refer to step 8 to 11 for the assembling. This way I bring Instructables to their attention (but of course my “loved ones” have heard of Instructables from me more than once). Making two complementary kits also allows offering a love robot to each individual in a couple.
The robots swing on an internal pivot point, with their weight distribution making them lean backwards, but only just. The attraction force of the magnets in their mouths overcomes this unbalance, making them lean forward on approach and kiss. Keeping all moving parts light helps to keep the movement back and forth smooth. Hence the idea of using ping-pong balls.
When using laser cutting it was easy to make the arms also serve as assembly tools (keys to M3 hex nuts), so no tools outside the kit are needed for assembly. I know that with laser cutting it is very feasible to make an assembly kit that doesn’t require any tools, but after a couple attempts to make a 2D cut pivot point I decided it was best to use a bolt for the main pivot axle. Furthermore, using bolts to keep the parts together also means the measurements are less critical and keeps open the option to contour saw the parts by hand.
The tittle is a tribute to the great Ible "Give the gift of Robot Invasion".
Note Februari 27th 2012: I corrected a large number of text errors, but there are probably quite a few still. English is not my native language. Please feel free to point out any mistakes.
Step 1: Materials
- 4 white or light coloured ping-pong balls (small yoghurt pots can be an alternative).
- About 10 by 10 cm of 3mm thick stiff sheet material, workable with your contour saw or a lasercutter. I choose 3mm birch plywood from the Ponoko Germany catalogue. I was actually a bit disappointed by the amount of sooth coming off, already staining the surface during transport. For my next order I’m planning on trying stiff thermoplastic sheet, like acrylic plate. As no interlocking is used, the design is not critical to the thickness of the sheet. However a thickness below 2 mm could make the "column/neck" part leaning to the sides to much. And material thicker than 3mm would require longer bolts and larger opening in the lower ping-pong balls.
- 4 M3x20 bolts and 16 M3 nuts. Hex head bolts allow for the robots' arms to be used as assembly tools.
- 2 neodymium magnets 4x8mm or similar, a third one comes in handy when building.
- A fine tip marker.
For two throbbing harts:
- 2 Blinking LEDs (red being the colour of love) operating on 3V. blinking LEDs are clearly underpowered on 3V. The ones from Opitec (n° 236135) work great.
- 4 strips of brass or bronze, 2 times 0.5 x 6 x 22 mm and to times 0.5 x 6 x 33 mm (roughly)
- Some thin gauge flexible electrical wire (6 pieces, each 10cm or longer). Thin gauge is key here, for sufficient flexibility. Think 0.15mm2 or smaller.
- 2 Button cell batteries, 3V each. I use two CR 2032 for my design. Other batteries with a different weight might need some trimming to get the mechanism in the right balance.
- Some way to hold and connect each battery. I used two times two small magnets (with a solderable coating) and a steel M4 nut glued in the back of each robot.
Optionally:
- Some double sided foam tape, about 3mm thick, 3 times 5x5mm.
Tools:
- A drill and a sharp 6 mm drill bit.
- A round file with a diameter smaller than 6 mm comes in handy.
- Scissors, preferably curved ones, either nail cutting scissors or Lexan scissors as used on RC car bodies.
- Soldering iron and solder.
- Hot melt glue gun and glue.
- A sheet of sanding paper, medium grit (150 to 220)
- Either a contour saw and a 3mm drill bit or access to a laser cutter (e.g. online service)
A template. The one attached below contains the parts for three robots on a Ponoko p1 template. I made it with Inkskape (freeware)
Attachments
Step 2: Opening Up the Ping-pong Balls
A 2 to 2.5 cm hole is made in each ping-pong ball. The inside diameter of a standard office tape roll is just the right diameter to mark it out.
Drill a hole well inside the marked circle, as a starting point for cutting out the marked area with curved scissors. Cut it out slightly small, to finish it with sanding paper: first put it on flat sanding paper on your work surface and sand by rotating it. Do this till the outside of the edge is smooth. Then make a roll out of the sanding paper and put it in the hole. Smoothen the inside of the edge by rotating the roll.
This usually takes only a couple of minutes, as the material the pin-pong balls are made out of is quite soft. The resulting diameter of the hole is not critical. It can deviate a couple of mm.
Step 3: Some More Holes in the Balls
Drill a 6 mm hole centred at each of those last markings, leaving just a small bridge in between. Use a really sharp drill bit and do not put too much force on it, in order not to dent the ball. It can help to pre-drill with a smaller diameter drill bit (e.g. 3mm). Remove excessive burring with a slim round file (diameter <6mm).
Cut the "bridge" in the middle as shown.
As the basis for the heads and the bodies are all the same, repeat this 4 times.
Step 4: Making the Switch
I did some test with Reed switches and SPDT switches, but ended up making switches myself. Reed contacts tend to stick to the magnet activating them, hindering the return to the off position when moving the robots back again. A SPDT switch on the other hand was complex to integrate and needed too much force. The robots should start moving towards each other at a couple of cm distance already, with still low magnetic attraction. Integrating a SPDT switch in the mechanism hindered that. So I came up with kind of inverse Reed switch, with the main magnet built in to it and activated by the approach of a ferromagnetic mass, or in this case another magnet with the correct polarity orientation.
Take two strips of brass or bronze, roughly 0.5 x 6 x 22 mm and 0.5 x 6 x 33 mm and bend them to the curvature of the ping-pong balls. Solder a 10 cm lead to each strip, sideways and leaving 5mm free at on end. Bend the longest one to a shape as shown, clamping one of the main magnets.
At the ends near de soldered leads, stick the two strips together with a gap of about 3mm, as shown. Some double side foam tape is handy. If you do not have that available you can use a drop of hot melt glue in which you insert a 3x3 mm piece of scrap material (e.g. the inside of a lasered 3 mm hole). Press together (taking care not to burn your fingers and let the glue set.
Clamp in the magnet and add hot melt glue to keep it in place. Use glue sparingly, as the underside needs to remain free to make electrical contact later on. Take care in the orientation of the magnets as the switches of the two robots need to attract one another, or your robots won’t show much love for each other.
Step 5: Mounting the Switch
Put the made switch in a ball that is to serve as a head. Keep it in place with a magnet on the outside, where the mouth will be. Align it with the top holes as shown. Glue the switch in place near the inner edge of the ball. Put glue only on the first half cm of the switch (where the 3mm spacer is), allowing the strip end with the magnet to move to make ore lose contact with the other strip.
Before removing the magnet, mark its position, for example with some tape. After removing the magnet draw a mouth at its position. It's a good idea to do a first drawing with some non permanent marker (pencil, washable marker...).
Step 6: LED and Battery Connection
Solder one of the leads coming from the switch to one of the LED’s legs, within 1 cm from the body of the LED. Keep the rest of the leg free and do NOT cut it (see step 7 for the reason). In the same way solder an unused lead to the other leg.
Solder the free ends of the leads coming from switch and LED to the battery holder solution of your choice (test to take in account the polarity of the LED). I used two smaller neodymium magnets with a solderable coating. Brass or gold coated ones solder well, some others dot to, while others don't (it is often not documented, so you will need to try it out). Soldering should to be done with minimum heat input (medium power, 25-40 W and working quickly), in order not to destroy the magnetisation. Some heavy pliers make a great sink and help keeping the solder from the sides of the magnets. Keeping the magnets' main surfaces flat gives a cleaner result when mounting the battery.
Repeat everything for the second "head ball". And test if a kiss switches on the LEDs. If the passion isn't there, first check the polarity of the batteries.
Step 7: The"body Ball"
As a last step before packaging as a kit, I add two sticky pads (foam tape, with the top cover layer kept on), where the arms are to be attached to each “body-ball”. As many types of glue do not stick well to the balls and neither does the double sided tape, I glued the pads in place with hot melt glue. An alternative is contact glue.
Step 8: Start Assembling (the Kit)
I kept to a minimalistic style for the robots, with just a suggestion of gender. The “male” robot has a forelock, while the same shape inverted suggests a high pony tail on the “female” robot. If you wish to follow this, carefully check the orientation of the top “lock” on the neck part versus the cut-out for the LED (the latter is always at the front side) when combining assembled mechanisms and heads.
As shown in the first picture below, take the LED and pass it, from outside to inside, through one of the top holes of a robot “body” (either one of the balls without a face and with sticky pads at the “shoulders”). Bring the LED through till it comes out of the large bottom hole of the ball.
Put the LED’s free leg ends through the small holes in the bottom end of the neck part. If you wish to mimic human anatomy put the LED at the left hand side of the neck part. Bend, without forcing a straight angle yet, to move the LED in the shaped cut-out. When the LED is in place push the legs further into the small holes to form a straight bend. Also bend the LED’s leg ends coming through at the other end, keeping it all in place.
Step 9: Bolting the Mechanism Together
Also on the top bolt, slide on the 3 mm hole of the neck part, with the LED pointing forwards. Add a nut and move it till it just touches the neck part, but do NOT tighten.
Add another nut and tighten these last two bolts against each other (so-called nut and check nut). The neck should still rotate freely. Add a nut to the bottom bolt and move it till it is at the same level as the last nut on the top bolt. Put on the second leg and fasten with a nut on each bolt.
Step 10: Mounting Body and Head
When putting the "body ball" on the mechanism, take care the glued-in nut comes at the back.
Bring the top of the neck part in the body ball and put it through the top holes from inside to outside. To do this you force the “bridge” ends between the holes to part. The botom hole might be a bit narrow for the LED and the mechanism to pass, but you can carfully deform the edge a little. Move the neck through till tthe "bridge" snaps into the second (bottom) hole.
Mount the head in the same way, snapping in the first hole.
Remove the protective paper from the foam tape and stick on the arms. Do not make them point forwards to much as it would disturb the balance.
Step 11: Putting on the Battery
Put one of the small magnets with a wire soldered to it on the back, there where it sticks because of the steel nut glued in. Put the battery on top and then the other small magnet+wire. Take care not to put the magnets near the edge of the battery, as on the minus side this could short circuit the battery, wasting its power.
Test with the head of the other robot. If a kiss does not activate the led, reverse the polarity of the battery.
Push any excess wire in the head.
Now repeat all for the other robot.
Love!
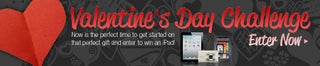
Grand Prize in the
Valentine's Day Challenge