Introduction: Rocking Speeder Bike
I have built my son lots of projects but with my daughter's first birthday coming up I felt it was her turn to get some project love and what better way than with her own Speeder Bike?!
The 74-Z Speeder Bike is best known for its appearance in the 1983 movie, Star Wars: Episode VI: Return of the Jedi. In which Imperial Scout Troopers, on the forest moon of Endor, engage in a vicious chase with Luke Skywalker and Princess Leia Organa after the Rebels commandeered the speeder bikes to pursue their foes.
I have to say though, when the design first came to mind, I had no idea the time and thought that would be involved....
Step 1: Design
For the most part, the facade of the speeder is based on the original concept drawing for the movie prop I found on the net, while using photos of ultra high quality scale models to fill in the gaps. Customizing the design to suit its purpose as a child's rocker (sturdy with no small breakable parts).
I see the overall design as three main parts, firstly the speeder bike its self (the hull etc); secondly the rocker arms/frame and thirdly the electronics.
- My first consideration was strength and stability for the safety of the little ones, as though this project is for my 1y/o, I also have a 5y/o who no doubt will want a turn. The need to be strong enough to handle a beating led me to the first part of my design, a rigid backbone with a solid plywood top for the seat platform. This gave me a good foundation for things like the handles and outrigger to mount from, and somewhere to fix the 3D printed hull shell.
- The rocker arms were the source of great deliberation (as you can tell by the multiple sketches above) as the effects of the weight of the speeder bike and a toddler over a guessed center of gravity was quite a challenge. My solution was to use the two center rocker arms to clamp either side of the speeder bike's timber backbone but still have clearance to slide the rockers back and forth 50mm or so to find the center of balance. This design also has scope to easily replace the rocker arms with maybe a (motorized?) rolling mobile base..... I'm just thinking out load.... stay tuned....
- In terms of the electronics I am not going to go into too much detail as I feel it is a little out of the scope of this instructable and I would recommend doing an Arduino setup (where as I used bits and pieces I had laying around).I wanted to end up with an LED blaster canon with the sound of the blaster and another button on the control panel that spun the turbine on the power cell. My initial idea was to use the guts from a toy blaster but it turned out the circuitry in the toy blasters were very fragile and I managed to damage the sound chip while assembling. So I ended up using a simple 555 timer flashing LED for the blaster and a sound recording/playback module I had laying around from another project. The power cell turbine is a simple circuit and I just used a small DC motor I found from a car windscreen washer pump.
Materials:
The main materials I chose to use are practical and some of my favorite to work with:
Plywood: Super strong, easy to cut and can look quite classy if finished off correctly. Low cost.
3D Printing: Great for the technical curved parts like the hull and detailed small parts. Low material cost.
PVC Tube: Light, easy to work with. Low cost.
Screws: G2 and G4 countersunk screws in a range of lengths
Bolts: Mostly M3 and M4 bolts
Attachments
Step 2: Timber Backbone and Plywood Templates
First, print out all the templates, some will require a large format printer like the rocker arms, or you could print them in sections and stick back together. Most templates are a simple process:
- Trace template onto plywood with mechanical pencil.
- Mark hole centers through template using a brad awl.
- Cut out plywood parts using a jig saw or a band saw.
- Finish each part by sanding and comparing each part to its template.
Some parts like the outrigger mount require shaping in two directions, in these cases:
- Cut out each part requiring secondary profiling.
- Screw parts together (if required)
- Shape parts in secondary profile using disk or belt sender.
Step 3: 3D Printing
I would suggest to get the 3D printing underway asap as some of the main hull pieces could take 10 hours+ to print. I printed in fairly low resolution as I knew the parts would be painted and also to save some time.
I printed using a Makerbot Rep 2
Infill 10%
Layer Height 0.3mm
Number of shells 2
Feedrate 90 mm/s
Travel Feedrate 150 mm/s
Print Temperature 230c
Material: Solid grey 1.75mm PLA
*Note: The main hull parts will need supports.
Attachments
Hul Nose L.stl
Hul Nose R.stl
Hul R Mid.stl
Hul L R Mid.stl
Hul L Mid.stl
Hul R R Mid.stl
Hul L Rear.stl
Hul R Rear.stl
Hul Vents.stl
Pod L Rear.stl
Pod L Front.stl
Pod R Front.stl
Seat Back.stl
Pod R Rear.stl
Blaster Body.stl
Steering Nose Rear.stl
Steering Nose Cone.stl
Control Panel.stl
Blaster Tip.stl
Engine Panels.stl
Engine Tube angles.stl
Engine Tube Connections.stl
Stabliser lugs.stl
Stabliser connectors.stl
Stabliser Centres.stl
Jet Rear.stl
Jet Prop.stl
Jet Front Shroud.stl
Handle Grips.stl
Handle Brace Brac.stl
Handle Brace Lugs.stl
Range Finder.stl
Exhaust Panel.stl
Strap Clips.stl
Step 4: Assembly
Once at the stage where you have 3D printed all components and profile cut all timber parts you will be ready to assemble some of the parts, bearing in mind some parts will need to be left separated for painting as they may be a different color like the steering vanes and their mounts for example. Having said that it is a good idea to do an assemble then disassemble to make sure everything is coming together ok and not fouling on other parts etc.
Refer to PDF drawings in each step for each components assembly process.
Step 5: Rocker Arms
The rocker arms are a very strong 18mm plywood spaced using 32mm stainless steel CHS tube and clamped together with M10 thread bar, washers and dome nuts.
The two middle arms are actually 10mm shorter in height which brings them off the ground so only the two outer arms rock on the floor surface.
Be sure to take a high level of care while drilling the holes for the thread bar cross members to ensure they will line up perfectly upon assembly. Unfortunately this is one of the components you will need to assemble -> check -> disassemble for painting.
When counterboring the holes for the spacer tubes to seat into, use a forstner bit in a drill press to ensure the seating area is dead square. Also use a depth gauge to ensure each bore is exactly the same (most drill presses have these built in).
Remember not to bolt the rocker arms into position through the timber backbone until you have temporally clamped them into position to try them out during the dry run.
Step 6: Handle Assembly
The biggest challenge with the handles was giving them lateral strength. My solution was to craft the arms from a stiff 12mm marine ply and install rigid steel brackets that fix right back to the timber backbone. Also use some nice big o/d washers to spread the load.
It is important to install the washer that is sandwiched between the plywood arm and the hull shell, this separates the arm from the hull shell and clamps the handle to the mounting bracket ONLY. If this washer was omitted the little lateral flex there is in the handle arms would get transferred to the 3D printed shell and eventually crack. Refer to drawing No.:14016 - 08.
Be sure to use dome nuts on all exposed nuts to avoid injury to the younglings.
Attachments
Step 7: Power Cell
As a novelty for the younglings I decided to make the power cell turbine spin. I found a small DC motor from an old car windscreen washer pump and incorporated it into the design which is mostly 3D printing and PVC tube. Refer to Drawing No.:14016 - 09.
The construction sequence is important with this part and is as follows:
- Install mounting thread bar with curved washers onto PVC housing.
- Bolt motor front shroud / mount.
- Attach wire tales to motor (long enough to get to electronics junction box)
- Install front shroud with motor attached to PVC housing & fix in place with blind rivets.
- Insert wires through the inside of the rear body spigot.
- Push rear body into position and fix in place with blind rivets.
I would suggest to do the above assembly after paining but you just need to touch up the heads of the rivets as they will still be raw.
Attachments
Step 8: Outrigger Assembly
Mounting plates
The outrigger adapter plates were the source of a great deal of deliberation as they needed to mount the outrigger tubes in a solid fashion but there was not a lot of meat (timber) below where the tubes land on the plywood outrigger mount due to the large radius fillet on the underside of the mount. My solution was to run the plates right across and offset the mounting screws inboard where there is more meat to fix to. Thrown into the mix is the stabilizer lugs that needed to hang out in roughly the same location so it made sense to incorporate all the above into one mounting plate.
Blaster Wiring Path
Be sure to drill the hole through the outrigger mount for the baster LED wire at angle toward the electronics junction box and not vertical as it will run into the under side of the timber backbone. Refer to section image above.
Step 9: Engine Cover
The engine I designed to not only replicate the original speeder bike look but to also double as a removable shroud over the rocker arm to backbone connection. It can be easily removed with 2 small screws at each of the 3 angle bracket connections.
Attachments
Step 10: Rear Pod and Thrusters
The construction sequence I would suggest for this part is as follows:
- Bolt the front and back halves of the rear pods together.
- Fix the pods to the underside of the rear top panel.
- Now with the pods in place you can hold the rear panel in position and check its profile to be sure its flush all the way around and sand off any excess prior to fixing in place.
- Install exhaust panel.
- Install thruster flaps with small hinges.
Attachments
Step 11: Foot Rest
- Use a piece of 38x38 SHS tube to fabricate a mounting bracket for the foot rest frame.
- First drill the 12mm hole that will be the connection to the 12mm round bar frame.
- Use a butane torch or oxy acetylene to heat the round bar to ensure a nice tight radius bend. I would suggest setting up a quick jig to check the angle and the two arms are parallel. Refer to drawing 14016 - 10 for dimensions.
- Weld round bar frame to bracket at an angle of 20 degrees from parallel to backbone.
In hindsight I would either weld a small piece of flat bar on top of the round bar under the timber foot rest or machine a flat on top of the round bar at the foot rest to avoid the timber foot rest rolling on the round bar with wear over time. I guess I'll see how it goes.
Attachments
Step 12: Seat
I selected 7mm ply for the seat base to ensure the staples would not protrude into the foam.
- Use the 7mm plywood seat base as a template to mark the medium density foam and cut out the profile with a sharp knife.
- Use a little hot melt glue to hold the foam in position while you cover the seat with vinyl.
- Work your way around the seat base with the staple gun, pleating the vinyl as necessary.
- Trim off the excess vinyl.
- Install the seat with a 2" wide strip of self adhesive velcro.
Velcro is used to mount the seat as the seat will need to be removed to access the screws in the seat back and one of the screws holding the top main panel to the backbone.
Step 13: Swag Assembly
Use some coat hanger wire to bend up some loops using long nose pliers then push the loops into the 3D printed base making sure the join in the wire loop is hidden inside the clip.
Paint the completed clips prior to installing straps.
Use your sewing skills to stitch some material strapping to one of the tie down clips and stitch some velcro dots to the other end that will thread through the other tie down clip. Be sure to check the length by laying strap over the hessian swag.
Step 14: Dry Run
Clamp the timber backbone to the upper rocker arms and ensure the rocker is sitting and rocking how you would like before fixing in place with M6 coach bolts as shown on drawing No.:14016 - 03.
Step 15: Electronics
As I said in the intro section I wont be going into too much detail with the electronics as I feel it's not in the scope of this instructable. I also feel there are better options like an Arduino or Intel Edison setup.
The first 9 or 10 images above showing my initial ideas / attempts using the guts from a toy blaster which unfortunately failed due to a fried sound module during construction. My solution was to use a recording / playback module for the blaster sound & build a flashing LED module using a 555 timer. The next issue I ran into was switching both the sound playback & flasher with the handle mounted SPST N/O momentary switch. My solution to that was to incorporate a dual relay setup to actuate both circuits simultaneously.
If there is enough interest I may do a schematic of my final circuit.
Step 16: Painting
As anyone with experience painting will tell you "preparation is key" and the same goes here. Spend the time to sit down and use a few grades of sandpaper working your way from course to fine on each piece.
Be sure to give the PVC tubes a good rough up as paint struggles to stick to an unprepared PVC surface.
For the primer I just used a cheap etch primer pressure pack can you can buy from any hardware or automotive store. Start with very light coats and work up to an even solid coat.
The main hull is two coats of Dulux A103 "Pookie Bear" with one quick light coat of pressure pack mat black to finish to give its weathered look. The brown paint is purchased in a liquid form so I used a low pressure spray gun to apply this color.
To achieve the "gun metal grey" I laid down 2 coats of pressure pack mat black & finished with one light coat of metallic charcoal grey.
The engine, power cell and rear panel has two coats of Hammertone charcoal grey.
I wanted to leave the rocker arms a natural timber to give a hand crafted feel to the job. So I used an acrylic clear with a satin finish pressure pack can. As there is no sealer going on first, the plywood rocker arms will totally soak up the first 2-3 coats of clear so be prepared to use 2-3 cans of clear to complete the rockers. Between each and every coat of clear go over the rocker arms with fine sand paper and you will end up with a beautiful satin finish.
Step 17: Completion
I hope you've enjoyed reading the instructable! I did put a lot more time and thought into this design than I anticipated but I am happy with the end result and judging by the smiles on the younglings faces, they are too.
Thanks for taking the time :)
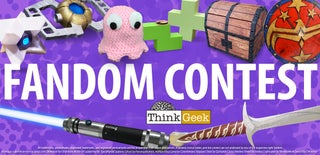
Grand Prize in the
Fandom Contest