Introduction: Rustic Bed Frame - Queen Size
It started about a year ago. My wife and I were looking at hand made furniture and fell in love with a bed frame made of cedar. It was sanded and "rustic" meaning log form. We wanted to get it but it cost $1,000. So I told my wife that I could make it. And so, six months later, I started the project.
This Adirondack Style AKA Rustic bed frame can be made all with hand tools (power drill was used). The rest was hammer, chisel and hand saw. A lot of hard work, but can be made for roughly $50 give or take. If you choose to put polyurethane and stain it, the will be a bit more as you have to buy those. The one you see here, the finished product, was stained "Golden Oak" and Clear Gloss polyurethane.
This bed is a queen size bed, but am sure it can be adjusted to any size as long as you know the dimensions. Just looked online. The inside of a Queen Bed cannot be any shorter than 60x80 inches. I went about an inch or two extra on each side encase of my own human error.
Step 1: Tools You Will Need
Luckily, you will need very few tools. Just a lot of time and work. Your skill of using a chisel will greatly increase by the end.
-Rubber Mallet (for hitting chisel)
-Chisel (1 inch, 1/2 inch) - new and sharp ones will save you a lot of time
-Saw (I used a hand saw as I did not have a chain saw, but that would make it much easier)
-Power drill (actually is optional, but putting screws in later for support will make it more sturdy and easier in some places). Will also need it for drilling out peg holes
-5 2x4 boards (make sure they are very straight)
-Wood Glue
-Clamps - at least two
- Draw knife (for removing bark)
-Hatchet - used it for removing limbs on the tree
-Lots of sand paper - 60, 120, 220
-Measuring tape
-Level
Optional Tools:
Electric Sander - most likely will save you a lot of time. However, the draw knife gets things pretty smooth so you might not need it as much as you think.
Step 2: Finding the Trees
You will need about 2-3 white pine trees. Each should be smaller in size (large, medium, small). Try to make sure they get relatively thin at the top, and not to thick at the bottom.
Remember while searching for your trees. Your "Medium Tree" base, and "Large Tree" base are the beams for you head and foot board. Try not to get anything that will be too heavy to move as a bed.
The "Small" tree and rest of the other two trees become the rails and spindles for the remainder of the bed. You will need more than you think, so get enough from the start or you will need to spend time waiting later for pieces to dry.
In my bed, used a tree that split at the base as my "medium" tree so it wasn't that thick and didn't kill the tree (seen in the picture). I had to cut it with a hatchet as the angle would not allow me to get my saw from the backside.
As for my "large" tree I found one the was a "Y" split not too far up. It was perfect because the bottom section was large enough to be the head board main beams, and the tops of the "Y" were thinner. Sorry I have no pictures here as I didn't bring my phone and it was a hard section of woods to get the tree.
Before transporting, chop off all the limbs. I used a hatchet as it makes quick work of it. However, looking back, cutting them with the saw might have made for easier sanding later as the hatchet left sharp points.
Step 3: Cutting - Still in the Woods
Since you cut the trees down, it's easiest to transport them by cutting them. You would recommend cutting them to needed lengths now to save a step later. Lengths are as follows (Queen Bed).
2 x Head Board Beam - 5 feet (thickest beam)
2 x Foot Board Beam - 4 feet
4 x Rails - 88 inches
4 x Connecting rails - 68 inches
10 x Foot and Head Spindles - size varies
8 x Rails Spindles - size varies, ~ 10 inches
As long as you don't cut things too short, you can always estimate or get close and cut them later. Shorter limbs (spindles) are hard to remove bark sometimes, so keep them longer until you know their exact size, which is much later.
Step 4: Removing Bark and Drying
Use your draw knife to remove all the bark. I learned the deeper you pull into the wood, the better the wood grain will show up after sanding.
After you remove all bark, let it dry. I left them in my barn for about 3 weeks and did the job. If you don't let it dry you will have shrinkage in the wood and your measurements will change, joints could loosen, and stain/polyurethane will not take as well. LET IT DRY!!!!
Leaving it out in the sun during the day does help, but don't set it in the grass.
Step 5: The Big Four - Pieces Your Are Building
Keep in mind when you are done building, the bedframe will be 4 main pieces (not including the 2x4 slats). See Pictures above for the four main finished pieces. This will allow you to transport the bed.
2 sides are rails
-Lay out all four of you 88 inch logs. Each side should have a thicker (bottom) and a thinner (top) one. If they are all the same size, not a big deal, but the bottom will be taking all the weight of the bed, so it should be thicker.
Remember, the showing length will be 80 inches, so make sure whatever length you end up making it, you can have 80 inches showing.
-The spindles we will build later, so don't worry about them now.
Head Board Rail
Thicker lower, thinner top (68 inches long)
-if you happen to make these shorter, which you can (64 inches) just make sure they only go 2 inches inside the Main Beams on each side. Remember, the showing length needs to be 60 inches.
-These too should be thicker than the ones used on the Footboard as it is bigger.
Foot Board Rails
Thicker Lower, Thinner top (68 inches). Both will probably be thinner the "Head Board Rails" as it is smaller.
Once you have them all paired, I recommend labeling them. I used a Red Sharpy for "Right", a Blue Sharpy for "Left". I chose left and right as if I were laying in bed (which means facing the footboard). I would then write on the ends, "Top Head", "Bottom Head". Colors told me left or right and I could tell the size difference for Head Rails and Main Rails.
Step 6: Chisel Time - the Rails
Main Rails: - The 88 Inch Beams
Right now your Main Rails should look like plain pieces of wood. Measure 4 inches in from both ends and mark all the way around.
Now make a mark at 2 inches in from both ends.
Chisel out the rails so that they form a rectangle from the end to the 2 inch mark. Size of rectangle should be about 1.5 inches wide, and 2 inches long.
IMPORTANT!!!! Make sure that your squares are facing the same direction!
Now the remaining two inches should be chiseled as a taper. See image.
Head and Footboard Rails
You can do these as the same as above.
I did a 1 inch square that was 2 inch long. I actually make the square insert go all the way to the end of the rail. I tapered 1 inch from the end to the rail. The taper in this one did not go into the Head/Foot Beams. This is one reason you might want to make these rails 66 or 64 inches so you don't have to chisel in as deep.
Head Board and Foot Board Beams (The Tops of Them)
I chiseled the top to make them look better. You can choose to do this or not. Look at picture to see what I mean.
Step 7: Chisel Out Slots
This is something you will get faster at as you have more practice.
I wanted my bottom rail to be 9 inches off the ground. So I made a mark on all four Head and Foot board Beams. Then, to account for error in my chisel work, I traced the rail ends around the spot I need to chisel. After that, it is just hammer and chisel time.
Make sure you keep it square as you chisel down.
Do a lot of checking.
Remember, the main rails need to go in 4 inches, with a wider taper at the two inch mark (this will give it a move of a funnel like entrance with a square hole at the bottom).
For each one, you will need to do a lot of checking, fixing, checking, fixing, until it can go in and out smoothly.
The Head and Foot Rails only need to go in 2 inches, without any taper (maybe a quarter inch just the make it fit better. These ones should be a tighter fit as at some point they will be glued and screwed into place.
Total time for this (16 holes you will be doing) is about 8-14 hours. Towards the end I got fast enough to do in in about 30 minutes, but the first couple took me about an hour each.
Step 8: Measurements
Just so you have a few more measurements in chiseling out the slots, here they are.
Sorry for the bad drawing, hopefully it is not too confusing.
Main Rails
Ground to first(First Main Rail)- 9 inches
Second Main Rail (Ground to Second) starts at 22 inches from the ground.
Head and Foot Board Bottom Rails
Bottom Rail - 14 or 15 inches (depends how close it is to the Main Rails) Make sure they will not connect or your Main Beams will be compromised)
Head Board Top Rail
As high as you want. I went about 4 feet.
Foot Board Top Rail
As high as you want. I went about 35 inches.
Step 9: Sanding
Sand, Sand, and more sand. Pictures above show before and after sanding. At the time of this picture, most of the sanding was done here but not all. Head Board spindles are not done yet either.
By the time you are done, you will be so sick of sanding, you will want to never see sand paper again.
IMPORTANT: If you have an electric sander, I highly recommend you use it as I am sure it will save you a lot of time.
Also, I learned halfway through that taking the draw knife over your wood again before sanding makes it a little easier, as the drying process sometimes makes the wood a little rough.
60 grit, 120 grit, 220 grit.
Total time here 40+ hours
Good news is, here you can jump around to other steps and come back to other sections. You can do thins such as, build the entire footboard before you even start to chisel out the head board pieces. Jumping around here so the sanding doesn't make you want to quit is a good way to go.
Step 10: Rail Spindles
These guys are annoying.
Because the rails change width down the run of a rail, so must your spindles change in size. I kind of did estimations.
You need to cut the spindles about 10 inches long (depending how wide apart you made your Main Rails). You will need to measure these yourself.
Chisel out spindles. I made female and male parts of the spindles round, square would have been easier.
Sand these too.
Chisel out the holes in the Main Rails also. Again, trial and error to make them all fit. Make sure you measure where to place these as they need to be equal distance on bottom and top rails.
Step 11: Head and Footboard Spindles
These ones are a bit tricky also.
For the Sunray design like I did, you need to find the middle of the Bottom Beams. Place on straight one there, which is to equal to the distance High and Low of the two beams.
The next two spindles (left and right of that), need to be cut at 22.5 degree angles and opposite directions. Refer to my terrible drawing from a few steps ago. These also need to be measured both where to put them and length to make them. I cannot tell you as each bed will be different.
The last piece needs to be at 45 degree angles. These pieces can be the same length.
I chiseled out underneath them a "U" shape so they hugged the log underneath them better for gluing and screwing.
Step 12: Attaching Head and Foot Board Spindles
I chose to screw them in as I was not sure how to chisel at angles.
First I wood glued all the spindle in place and let them dry. Then I went ahead and screwed them in (for the head board my wife help hold them in place and screwed them in while the wood glue was still wet).
Do a larger drill bit at first so the screws can be hidden.
Pre-drill the holes with a small drilled bit to prevent splitting the wood.
Try and put the screws in a location (inside the bed) where they will less likely be seen. Sometimes this cannot be avoided though.
When you are done, fill with wood puddy to hide them.
Note: I slid little slivers of the chisel wastes into gaps with glue and sanded anything left later. I just though this would help with stability, bot really sure though.
Step 13: Slats - 2x4 and Chisel
You will need 5 or more 2x4. I chose just to use 5 as they fit among the Main Beam Spindles the best.
They will need to be 65 inches give or take a half an inch.
Because the main rails change width, the length of each one will be slightly different. Make sure you label your boards as each on will always go in the same place.
Measure where each on goes in each side. I chose to only go about 3 inches from the Foot Board and Head Board as I want to make sure the Box Spring of the bed didn't want to drop down on the ends.
The other locations were in between the spindles on either side.
You will need to chisel out so the 2x4 drops into the Main Rail and is flushed with surface.
After that is all done, make sure the rails are all level. Then sand them down inside.
Step 14: Stain and Gloss
If you chose, you main stain and gloss the entire thing. We did. We did two coats of Gloss. I am sure I will get a lot of complaints or questions about more details. I will be happy to answer questions.
For those critics out there.
I made this up in my head as I was life guarding. I am sure there are easier ways. I did not have the tools to make this easier though, and just committed a lot of time.
If anyone makes one, please share it as I would like to see. This was my first big project and had not really any prior experience beforehand so this is possible for any skill level. Just take you time and think about your steps before you move on.
Enjoy!
Step 15: Stability
I realized that if the bed gets motion to it, the Main Rails might eventually slide out. Not a good thing.
What you will need:
-1/2 Poplar Wood Dowel
-1/2 Drill Bit
Drill through the Head/Foot Board Beams so that the drills drills through the middle of the chiseled section of the Main Beams. Then you can slide the wood dowel through those holes to lock them in place. Make sure that you will be able to take them out in the future or you might never get your bed apart!
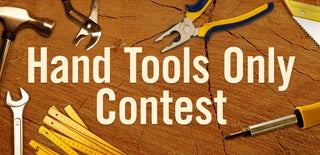
Second Prize in the
Hand Tools Only Contest