Introduction: Screen Printing With Vinyl
In this instructable Im going to show you how to screen print without the expensive, time consuming, dark room needing, messy photo emulsion!
So here is what you need.
1: A vector image to screen print.
2: A blank screen
3: A sign squeegee, or credit card.
4: A vinyl decal or access to a vinyl cutter.
5: Masking/transfer tape.
Step 1: The Image to Decal
If you dont have a vinyl cutter (odd are you dont) this is still a useful technique as most high-street Printers/sign-makers/universities will have one, and more importantly if you proved them with the image will make you a decal up for very little as it will probably fit onto a scrap of sign vinyl.... but what ever they charge it will be considerably less then getting a screen made up!
1: Find the image you want to screen print, and if necessary convert to a vector image.
(It will need to be vector due to the vinyl cutting stage only working with vectored images.)
2: Cut the image, or get it cut for you!
(its very important that you ask for it to be a negative of the image, or if your weeding the vinyl yourself you need to weed the line-work from the vinyl)
Step 2: Setting Up the Screen
Once you have you vinyl decal sticker, your ready to apply it to your screen.
Your decal will have a wax paper backing sheet and a transfer tape front, you need to peel off the wax backing sheet to expose the sticky vinyl.
Place the decal sticky side down on the screen and rub it all over with a credit card or sign squeegee.
Now peel off the layer of transfer tape to expose the no sticky side of your vinyl decal.
Step 3: Mask and Print!
Now you have your vinyl decal stuck down to the screen you just need to mask off the rest of the screen and your ready to go!
you can easy remove the vinyl with a little white spirit, and reuse the screen with a new design........this makes it a lot cleaner and more practical for small print runs.
Why not use glow in the dark paint, so i qualify to enter in the Make It Glow contest! ;)
Now I will take this chance to preempt a couple of question, but if iv missed something just ask below.
Q: Wont the squeegee jut rip up the vinyl
A: No, well its not done that to any of my ones, the lubrication of the paint, and the industrial adhesive quality of sign vinyl stop this from happening. (if you were doing heavy detailed work you could always flip the image and stick it to the underside of the screen)
Q: I dont have spare £200+ for a vinyl cutter, just to screen pint 10 T-shrits!
A: Any sign printers should do you a vinyl decal for less the the price of a blank Tshirt! (compare that to the price of getting a photo emulsion screen made up!)
Q: Is it true you have many leather-bound books and your apartment smells of rich mahogany?
A: Yes.
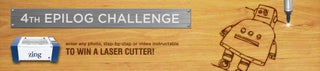
Participated in the
4th Epilog Challenge