Introduction: Segmented Turning Blank (for Bowls and Cups)
Decorative cups and bowls can be made on a woodturning lathe, and are often made out of a single block of wood (or a straightforward laminated block of wood). For a more complex appearance, try a segmented wood turning. In a segmented turning, the turning blank is made out of a series of stacked wooden rings. Each of these rings is made from a group of small, precisely cut pieces of wood often of different wood species. Each piece must be cut at an exact angle, or the resulting ring will have small gaps between adjacent pieces. This is challenging enough that people make or buy special jigs for cutting these pieces very accurately.
This instructable shows an alternative way to make these rings which greatly simplifies the cutting and assembly of the pieces. Using a laser cutter, each piece is created to resemble a jigsaw piece. This not only provides the precise angle needed between pieces, but eliminates the need to clamp the pieces when gluing them together to create each ring.
This instructable shows how to make the segmented turning blank itself, but not the process of turning it on a lathe to make the final piece. That is a likely topic for a future instructable...
I made this at TechShop www.techshop.ws
Step 1: Materials and Equipment
Vector drawing software (I used CorelDRAW)
Laser cutter (my TechShop has a Trotec Speedy 300)
150 grit sandpaper
Wood glue
Hammer
~24 square inches of 1/4" thick light wood (poplar)
~24 square inches of 1/4" thick dark wood (walnut)
This instructable assumes some basic familiarity with CorelDRAW and a laser cutter.
Step 2: Establishing the Basic Diameter
Start by drawing two concentric circles which represent the coarse inner and outer diameters of the turning blank. Remember that a small amount of material will end up being removed during the turning process, so you need to make these a little oversized. I picked an outer diameter of 3"and an inner diameter of 2.2", and am assuming that I will end up removing about 0.05" of material from both the inside and outside during turning.
Make sure that you set the line width to hairline so that the laser cutter knows that you want to cut these lines and not just engrave them.
Step 3: Making the Basic Key Shape
Now we are going to make the puzzle-like key shape. Start by drawing a horizontal line joining the two rings. Next, draw a 0.125" diameter circle adjacent to the horizontal line. Then, join the circle to the line with two short arc segments. Finally, use the virtual segment delete tool to remove the short arc and line segment leaving you with the basic key shape.
Step 4: Setting the Segment Size
Select the basic key shape, then go to the transformations menu and choose the rotate option. Set the rotation angle to 36 degrees, the number of copies to 9, and the center of rotation to match the center of the two main circles. This will create a total of 10 segments. You can adjust the angle and number of copies to create more or less segments as you would like.
Step 5: Individual Segment
We don't want to start laser cutting yet. First, cutting out the segments in their original ring configuration will waste a lot of wood. Second, as is the segments won't actually hold tightly together when gluing. This is because the laser kerf (the width of the cut made by the laser) is about 0.013". While it doesn't seem like much this results in the keyhole being a little oversized and the key portion being a little undersized. Rather than trying to precisely size each of these and attempt to make an overall perfect fit, we will add an interference fit feature to the key side of each segment. Start by deleting all but one of the segments.
Step 6: Modify Key to Account for Laser Kerf
To help hold adjacent segments together snugly, we add two bumps towards the back side of the key. By making them large enough to cause a slight interference fit, the segments get wedged together. At the same time they need to be small enough that they can crush slightly when assembled rather than blocking the key from fitting into the keyhole.
Draw a 0.035" diameter circle towards the back of each side, then delete the arc segments that protrude into the key. To avoid an interference fit at the tip of the key, we need to flatten the end of the key slightly. Draw a shallower arc across the end, then delete the original end of the circle.
Step 7: Final Segment
The segment is now complete. Since we plan to alternate light and dark segments, we will need five of each type of wood per ring. To make the cutting of the segments a little faster, make four copies of the segment with the step and repeat function. Now you can cut a ring's worth of segments with each pass. Obviously you could just make a large array of these matching the total number of segments you need for a whole bowl, but I found this easier to manage.
Step 8: Laser Cut the Segments
Now cut the segments out on the laser cutter. Since I plan to use six rings in my segmented turning blank, I need to cut six rows in each type of wood. The poplar cut very easily with the first settings I tried on the laser cutter (100% power, 0.7% speed). However, you can see that those settings badly charred the walnut. What eventually worked out well was to increase the speed of the laser cutter (so it couldn't sit and burn the wood) but have it make multiple passes for each segment (since it wouldn't cut very deep on any given pass). The final settings for the walnut were 100% power, 2% speed, and 7 passes. You will have to experiment with your laser cutter and materials to find the right combination of settings.
Step 9: Sand the Segments
Now lightly sand the flats of each of the segments. This will help remove any fibers along the edges of the wood that might have been left by the cutting process, and will help ensure that the ring is as flat as possible when being assembled.
Step 10: Assemble the Rings
Assembling the rings can become tedious, so to help avoid making any mistakes I first lay out the segments for one ring in the correct order. I then add glue to the keyhole of one segment, place it over the key of the adjacent segment, then gently tap it down into place with a hammer. The hammer is necessary to make sure the segments fully mate due to the interference fit of the key design. Repeat with each segment until the ring is complete. Now assemble all of the remaining rings.
Step 11: Sand the Rings
Once the rings are dry, there will be some amount of glue and possibly wood fibers poking up from the joints. Sand both sides of every ring flat. If you get tired of the hand sanding, you could use a palm sander or similar to speed up the process.
Step 12: Glue the Rings Together
Here is where you can be creative and decide what kind of pattern you want to create when stacking the rings. Once you pick a pattern, start gluing the rings together one at a time. Spread a thin layer of glue on the flat of one ring, set another on top of it, finely adjust its rotation, then place something heavy on top to hold them tightly together until the glue sets. You could obviously use a set of clamps if you have them, but I just happened to have a small anvil nearby that worked perfectly. Repeat until you have glued the entire stack together.
Step 13: Turning the Final Bowl
You now have a segmented turning blank that you can incorporate into a wide variety of bowl or cup designs. Various bases, rims, and lids can be added to create your one of a kind woodturning. Here you can see the blank on its way to becoming a new holder of knickknacks; first being mounted to the lathe faceplate then after roughing out the basic design.
Happy turning!
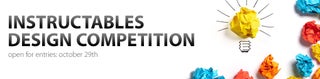
Participated in the
Instructables Design Competition
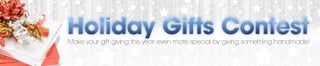
Participated in the
Holiday Gifts Contest