Introduction: Self on a Shelf: a Shelf Built From Junk
“We have a wall. It’s a nice wall. I painted it grey last year.” Hardly an exciting conversation starter is it? My wife and I had been staring at the painted wall for some time trying to work out what we should do to make it a bit more interesting for us as well as for any friends and family who might come and visit. As I love making things I suggested that we put up a shelf to display some of the stuff I’d made – almost like my own mini-museum (hence the name Self-on-a-Shelf). Contrary to tradition, the wife agreed with me and so after picking myself up off the floor, I set about planning how to build the shelf from scratch. Of course, I couldn’t display all of the things I’d made using a shelf bought from a shop now could I?
The rest of this instructable explains how I went about making the shelf, the brackets and how I mounted it all to a rather awkward plasterboard wall. Enjoy!
Step 1: Planning
First of all I needed to decide where the shelf was going; it’s height, length and position on the wall. As this shelf was to be mounted above chairs I wanted to make sure that it was high enough that it did not make it inconvenient for people trying to get to their seat. However, I also knew that I wanted to put a couple of tall ornaments on the shelf and so it had to be mounted a suitable distance from the ceiling to ensure that the ornaments would fit.
I also knew I wanted something rustic that would fit in with the rest of the room and the ornaments I planned to display but I wanted it to be unique and unusual so that the shelf and brackets were a feature in their own right. Additionally, I like making stuff out of reclaimed materials and re-purposing things so wanted to continue with this trend. In the end I opted to make the shelf out of a 3.2m (10.5ft) long reclaimed pine joist, and I made the brackets from some metal bar offcuts and an old motorcycle sprocket. In fact, the only thing I had to buy from new were the 8 mounting bolts! Due to the length and weight of the shelf I opted to use 4 brackets to support the shelf. I made sure that there was an even spacing between the brackets and a similar overhang at each end of the shelf to make it look symmetrical. I’ve included a quick sketch of this as attached.
Step 2: Tools and Materials
Materials
1 x metal motorcycle sprocket
3.5m x reclaimed pine joist - cut down to 3.2m/10.5ft). It's 215mm (8.5") wide and 50mm (5") thick.
1.6m of 3mm metal bar, 40mm (1.6") wide - cut to 4 x 400mm (16") lengths
Mounting bolts/screws (in my case these were suited for a drywall)
Safety Equipment
Latex gloves for handling oils/cleaning products
Dust Mask for sanding
Ear defenders and goggles for power tools
Basic Tools
Scraper for getting gunk off the sprocket
Screwdriver (though a drill would be easier!)
Metal clamps (or vice)
Drill (with metal and masonry bits as well as screwdriver bits)
Spirit Level for making sure your shelf is straight
Rags for cleaning as well as for applying wax/oils if required
Hacksaw (if you don't have an angle grinder)
Hammer - for tapping the wall plugs into the wall
Pencil (and metal scribe if you have one) for marking out
Set-square (or something that can be used to mark a right-angle)
Wire brush for cleaning the metal
Consumables:
Sandpaper, Brake Cleaner, Wax/Oil/Paint, Screws and wall plugs.
Specialist Tools
Welding equipment (Arc/MIG/TIG/Gas) and associated safety gear (mask and gloves as a minimum)
Optional Extras
Angle Grinder (I would consider this an essential tool if you plan on doing lots of metalwork)
1mm metal cutting disc for the grinder (as shown in the photo.) These are great for making quick, clean cuts
Electric Sander (If you plan on doing a lot of woodwork these are well worth the investment)
Hammer Drill (for making holes in brick/concrete walls)
Vice (for clamping things in place while cutting/grinding)
Step 3: Making the Brackets - Preparing the Sprocket
Sourcing the Sprocket
The chain and sprocket on my motorcycle needed changing. Rather than chuck the old bits in the bin, I decided to do some up-cycling (poor pun intended). As the sprocket was steel I knew it could be welded easily and certainly looked thick enough to be used to support a shelf! And don’t panic –the chain has been put to good use too but not on this project. If you want to get hold of a sprocket it’s worth speaking to a local motorcycle mechanic as these parts are often just thrown away after a service. Keep in mind that I’ve used a steel sprocket. Motocross bikes tend to use aluminium sprockets but unfortunately these cannot be welded to steel bar and aluminium is more difficult to weld than steel. If you’re not sure what metal you’ve got, test with a magnet. The magnet will stick to steel but not to aluminium.
Preparing the Sprocket
After 22,000 miles of rotating on my back wheel, the sprocket was looking a little worse for wear. I scraped off most of the oil and dirt with a metal scraper. I then sprayed brake cleaner (also known as carburettor cleaner) directly onto the sprocket and then used an old rag to rub the rest of the grime off. Remember to wear gloves for this bit and also bear in mind that the spray is *very* flammable!
Next it was time to cut the sprocket into sections. I started out by drawing/scribing lines across the sprocket to divide it into 4 equal pieces. I used a ruler for a straight edge and then used the holes on the sprocket as a guide to work out where to cut. Clamping the sprocket in place and using a 1mm cutting disc on an angle grinder, the sprocket was cut into 4 equal sized sections.
Step 4: Making the Brackets - Preparing the Metal Bar
I needed some metal bar to form the main shape of the bracket, however as I didn’t have any metal bar I had to improvise. I made some straight, flat bar sections out of some 3mm angled steel I had lying around by simply using the angle grinder to cut the angled bar into 400mm (15.75") strips. By all means, you can use this approach too but it takes time to clean up the cut edges and make them perfectly straight. It’s definitely easier just to buy some metal bar so that you are starting out with some nice, straight metal! I would advise against using anything less than 2mm thick steel as it’s likely to flex with any significant loads on it.
The next step was to drill the holes in the bar for the screws. I would advise doing this before bending the bar to avoid the bent bar fouling on the drill or getting in the way… and yes, unfortunately I am speaking from experience!
Mark the centre of the holes using a scribe or pencil. I opted for two holes for the wall mounting and two for holding the wood in place. You certainly don’t want to use less than this otherwise you could end up with a shelf that is at best, wobbly and at worst, quite dangerous. The holes are spaced approximately 13cm (5") apart. Ideally, use a centre-punch to mark the centre of the hole prior to drilling as it helps the drill bit to ‘bite’ in the right spot. If you don’t have a punch then it would be best to start off with a smaller drill bit so that you can make an accurate start before moving up to the desired diameter drill bit. As the bolts I’m using are M6 size (6mm) I’ve gone with a 6.2mm hole size although the hole size is dependent on what fixings you’re using. Also, make sure you drill the holes well away from where the sprocket sections are due to be welded on otherwise you’ll struggle to get a screw/screwdriver in there later on!
It’s at this point that the bar will be bent at 90degrees to form the basis of the bracket. I started by marking a line about half way along each length. Now, on my first attempt I figured the best way to do this would be to clamp the bar in a vice, and use a few blows of my trusted persuader (a big hammer) to bend the bar. I soon realised that due to the thickness of the steel, the bar was not bending easily or uniformly. I quickly changed my approach and instead used the angle grinder to cut a notch along the width of the bar, being careful not to cut right through it. The bar could then be bent very easily and accurately by hand. Use a set-square to ensure that the bar is bent to the desired 90 degree angle.
Step 5: Making the Brackets - Welding and Finishing
The next step prior to welding everything up is to clean it to make sure the surfaces are free from rust, dirt and oil. Wire wool or a wire brush on a drill attachment are useful aids for this step.
I appreciate that welding equipment is not available to everyone. If you don’t have your own kit, then so long as you’ve prepared the materials as described above, it shouldn’t take long for someone to weld the bits up for you (around an hour for all 4 brackets depending on their experience). Worth asking at a local engineering firm or at a garage for assistance if you need some welding doing. For relatively small jobs like this, most of the welder’s time is spent setting up the equipment and preparing the metal so whatever you can do to make life easier for them should help to keep costs down… I don’t mean make them a cup of tea and massage their shoulders, I mean make sure you’ve cleaned the metal and explained/marked where you want the sprocket sections to be welded on! : P
If you do have your own welding gear then my advice would be to tack weld the sprockets in place before welding fully. I found that the sprockets and bar would move around as the tack welds cooled so it’s essential to realign everything before tack welding the next section. Once it’s all nicely tacked in place, fully weld everything, being careful not to overheat the bar as this is prone to warping if it gets too hot.
Firstly weld up the slot that was cut to bend the bar so that this is strengthened again. Then weld on the sprocket sections ensuring that they are aligned with the middle of the bar. Finally, with a stiff brush remove any spatter and dirt that may have stuck to the brackets during the welding process.
Now it’s time to give the brackets a final finish. You can leave them as they are but being
steel, they will rust over time - even indoors. I left mine without a finish as I wanted to keep the industrial, rustic look but you might want to consider coating them with a clear wax or even spray painting them if you want to make them more colourful - just remember to use primer before applying a colour coat.
Step 6: Making the Shelf
I found the piece of wood at a local reclamation yard. It was sat outside getting wet and looked very sorry for itself as it was split at either end and was full of nails. However, with a bit of TLC I knew I could get it looking its best again.
Here I should point out that whether you’re using new wood or used wood, be sure to check it’s straight. No one wants a wonky shelf! Hold one end up to your eye and look along the length of the wood. It should be obvious if the wood is twisted or warped anywhere. If it is, pick a different piece of wood!
Once you’ve chosen your piece of wood, let it dry out if it’s been sat out in the rain for ages. Also, if you’re using reclaimed wood then be careful to ensure that any old screws or nails are either removed or screwed/hammered below the surface of the wood. This is for two reasons: one is the obvious safety element of not having sharp, pointy bits sticking out of your furniture! Secondly, these sharp protrusions will wreck your saw blade and sandpaper. Next use the set-square to mark where you want to cut the board to length and then use your best saw to cut it to the desired length. I deliberately bought a piece of wood longer than I needed so that I could cut both of the split ends off.
So now the wood is cut to size we can move onto sanding. Electric sanders make this bit much easier and quicker. If you don't have an electric sander then get yourself a sanding block, or an old piece of wood that can be used as a sanding block (as pictured).
I wanted my reclaimed wood to feel smooth but still look rough and I found 80 grit paper gave this exact finish. One quick blast with the palm sander and it was ready for waxing. However, if you want a really smooth finish then start with 80 grit paper and then move on to 120, 150 or even 200 grit paper, just remember that you will start to lose some of the rustic characteristics of the wood if you sand too much off. Really it’s worth trying on a piece of scrap to check the finish you want. In order to achieve an aged look, I also sanded down all of the corners and edges on the wood to round them off and give the wood a bit more character. I also left some of the old nails in situ to show off its reclaimed roots!
To finish it off I used a clear wax which helps to clean the wood, bring out its natural colour and give it a matt finish. This was a mixture of beeswax and turpentine and can be bought from most DIY stores. I had considered staining the wood with oil but on previous projects I have found that even some clear oils/stains have reacted with the reclaimed wood I was using and have really darkened the wood more than I wanted. Again, worth experimenting on some scrap wood before trying it out on your shelf. To be clear, I said your shelf, not yourself. If you coat yourself in wood stain, don't blame me!
Step 7: Mounting the Brackets and Shelf
With the shelf and brackets finished it’s now time to mount the brackets. On the wall, use a spirit level to draw a straight, level pencil line across where you want the top of the brackets to sit. Remember that you are not marking the top of the shelf, you are marking the top of the bracket. The thickness of the wood will determine the shelf height. This might sound obvious but it’s important to keep it in mind if you are building to a specific height. Also, when you’re deciding where holes are to be drilled into your wall you’ll need to consider what you’re drilling into. Pipes and cables are often hidden behind walls and aren’t always obvious to identify. Tools are available to find metal pipes and cables but don’t forget that these won’t help you find plastic pipes which are becoming more common in modern houses.
Hold one of the brackets up against the pencil line you drew, ensure the bracket is straight and then mark the centre of the holes on the wall. Now, unless you’ve made each bracket perfectly, they are not going to be identical. Therefore, when you mark your holes make sure you use each bracket in turn and don't assume that you can mark all of the holes with one bracket because there is a good chance the holes won't line up if you do. Also remember which bracket corresponds to which holes on the wall. I numbered mine 1 to 4 and also marked the wall so I knew where each one needed to go.
I had to mount these brackets onto a brick wall that’s been lined with plasterboard (aka drywall). I was worried that the plasterboard would not be able to support the weight of a solid wood shelf and all the stuff I wanted to put on top of it. I was also concerned that, due to the large airgap between the wall and the plasterboard, using conventional wall plugs in the brick might not be enough to prevent the screws sagging slightly once they have a load on them which could risk cracking the plasterboard. In the end I found some great bolts online which are designed to overcome this problem. They make use of large bolts which fix solidly into the brick wall and then sit flush with the front of the plasterboard. A separate screw then tightens into the bolt to clamp the bracket to the wall. I’ve added a few photos and sketch for more info on this as it’s difficult to describe in words!
With the brackets mounted on the wall, slide the shelf into place, checking that you have the overhang you want at either end and that the shelf sits snugly against the wall. Then simply screw through the brackets into the wood. All that’s left to do is put loads of stuff on your shelf, stand back and admire your hard work.
Step 8: Final Words
It has cost me less to build this shelf than buying new brackets and new wood from a store. Admittedly, it has taken more time to make than buying something pre-built from a shop, but this shelf is far more durable than a shop bought item, it won’t sag over time, it’s environmentally friendly, unique and it’s actually much safer. In fact, it's so strong that my new party trick is to hang off the end of the shelf with my feet off the floor! Ok, ok, so perhaps some could say I’ve over engineered it but I’m glad it’s strong and will be able to stand up to years of use and it's much more interesting than talking about the plain grey wall that was there before. : )
Thanks for reading. Any questions or comments please fire away. Also, I have one shelfish request (sorry!)... if you think this is a worthy entry for the Shelf competition please don't forget to vote for it. Thanks!
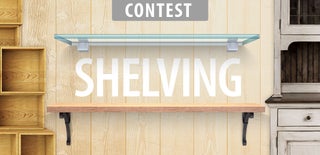
Participated in the
Shelving Contest 2016