Introduction: Semi-Auto Longshot 2
- Raw materials you'll need:
- 3/8" thick acrylic sheet (Mcmaster P/N-8774K41)
- 5/8 Diameter metal rod, I'll explain later
- #10-32 Soc Hd cap screws (Mcmaster P/N-90128A940)
- 1/4-20 Soc Hd set scr (Mcmaster P/N-91375A533)
- #5-40 Soc Hd cap screws (Mcmaster P/N-91251A130)
- 0.5" DIA X 12" Lg PVC pipe (98 cents at Home depot)
- .5" x .5" x 1" piece of aluminum/CRS
- .25 x .25 x 2" piece of aluminum/CRS
This is all necessary to begin the mechanical fabrication, feel free to substitute any or all the fasteners to suit whatever you have on hand as these are just the sizes I used on mine. Just to give you an idea of what we will be constructing see the images below. Next up, manufacturing!
Oh and to give you a taste of the firing rate check this video out, it misfired a few times but that is just because the stepper motor limit switches weren't wired up yet.
Step 1: Flywheel Assembly
Below you will find a zipped folder containing bother .iges files as well as 1:1 PDFs. All you really have to do is print them out, stick them on, and start cutting/drilling. But DON'T FORGET THE SAFETY GLASSES.... seriously, hot plastic/metal will permanently injure your eyes.
You will NEED the following tools:
- A cutting device (Ie. Table saw, band saw, dremel, hacksaw... etc)
- A drill press or drill (drill press is preferred)
- #10-32 tap and tap drill
- 1/4-20 tap and tap drill
- Sand paper
- Band saw
- Standard 3 axis manual milling machine
- Standard engine lathe
- Dremel
- #10-32 tap and tap drill
- 1/4-20 tap and tap drill
- 1/2 DIA drill bit
- 27/32 DIA drill bit
- Sand paper
- Begin by cutting out all your blanks, Check the drawings provided. Make sure to make everything as accurate as possible, this will drastically reduce your headaches later on. See the images below of assembly and reference. The PVC breech was cut by hand using a Dremel (Abrasive cutoff wheel and grinding wheel) and adjusted to fit the magazine and flywheels. The pockets in the carrier plate were designed for these motors (Tamiya Torque tuned motor) but any small rc motor will do. I would suggest that you drill and tap all the holes in the barrel mounts (with the exclusion of the hole for the barrel). Next, drill and counterbore the holes in the main carrier plate.Once everything is drilled and lined up, screw the assembly together and drill/cut the main bore for the barrel to sit in.
- The second phase is to manufacture the flywheels, the reason they are metallic is because you will need to install set screws to keep the shaft of the motor from spinning freely, and unless you are careful you will strip the threads out. I used #3-48 set screws, you could also glue the wheels on if you don't feel comfortable working with small taps. If you do not have access to a lathe you can use the 5/8" diameter rod as it is, and simply use a drill press to drill the hole (It won't be accurate, but it will work). The only issue with using the rod without turning it down is that you will have to alter the barrel more. You don't really need to rough the wheels up or add any e-tape/rubber, they will grab the dart just fine.
- The third step is to make the loading mechanism. This will be slightly more tricky as you will need to machine the OD of the rod down to properly fit inside of the barrel, or simply scrounge for material that fits. The crank and linkage are very simple to manufacture, but the entire assembly will need to be sanded to ensure that all the parts slide freely. Once again, these parts are most easily made from aluminum, but plastic could be used if you can't get your hands on anything else.
Step 2: Modifying the Shell
I get a LOT of flak from people for what they deem "destroying" a Long Shot, however I respectively disagree and i would even go as far to say that i'm doing a SERVICE to the Long shot. Who else can say that they have a LS that has a 120' range? Or one with a 4 round per second firing rate? Well.... besides me =).
So if you don't want to "ruin" a longshot, go break open a recon, alpha trooper, deploy, or raider and get this working in that shell instead. For those of us who would rather take one of the best looking NERF blasters out there and turn it into something amazing, keep reading!
Okay, so grab your longshot and open it up. Remove EVERYTHING, I decided to cut the front of the blaster off to make it more HvZ friendly; Start cutting strait down at the end of the tactical rail. Take a look at the pictures to see what you will need to remove, honestly it's not much.... well compared to the last build I did at least.
It's easer to watch the video in the next step to figure out where to modify the shell. I promise it will be easy.
Step 3: Align the Assembly.
- Stepper motor installation depends on which you are using. I had mine laying around from a former project, but any bipolar stepper motor with a reasonable torque will do. You can simply bolt the stepper motor to the plastic LS shell, or even glue it on; I opted to make a plate to increase the rigitidy of that area out of 1/8" thick 6061 aluminum plate.
- I decided to cut out the back of the shell and fix the stock in the closed position to increase the handling of the blaster. I attached the stock to the LS shell with one bolt and a bunch of epoxy puddly.
- The next thing is to clear the area around the crank, it will depend on where you mounted the stepper motor. As you can see I got lazy with the crank after I realized no one would see it once the blaster is closed.
Step 4: Electronics
THIS PAGE WILL CHANGE, as I finish up the electronics I'll update this section to reflect everything i'm doing. I'm sorry the instructable isn't complete; but even if you started working on this thing right now i'd have the electronics/programming up by the time you got here.
What you will need:
- Microcontroller of your choice (I used an arduino)
- Stepper motor controller or servo (I used the easydriver)
- 3 micro switches, you can get them at radioshack but i suggest e-bay.
- one SPST switch for power on/off
- One LED for status
- Multi-position switch if you want select-fire
- Resistors
- Batteries (This will be discussed more in the next step)
- Boost converter (see next step)
- Motor controller (see next step)
- wire... wire... and more wire
- Patience
Step 5: Electronics Continued
-
Boost Converter: This circuit is required to give the stepper motor the maximum possible power through the easydriver circuit. The easydriver is capable of providing a maximum of 750mA per step, so to overcome this power limitation we must give the circuit the maximum voltage it can handle in order to achieve the maximum torque from the stepper motor.
My first few attempts failed in one way or another, I'm going to try a third time using a new layout which will give me more room to work with on the proto-board. You can see an image of my second attempt below. More to come!! - Motor controller: This will be a simple MOSFET driver for the motors to trigger them from the arduino.
That's pretty much it for the electronics, stay tuned for the programming tutorial once it is finished!
Here is a video showing off the loading mechanism operating at 30v, which will be close to the output of the final boost converter.
Step 6: Epilog Contest
A little about myself:
My name Is Philip Haasnoot and I am currently a senior level mechanical engineering student at Stony Brook Univerisity. I am the president of the SBU Solar Boat Team and represent the university on the board of directors for the SBPLI FIRST robotics regional. I am a huge supporter of open source and collaborative projects. My field of interest is medical robotics and prosthetics, to date I have designed several prototype prosthetic arms and dexterous hands that are in various stages of development. I also have constructed two Robo-ONE style robots, even going so far as to design my own servos to fit the form factor better.
So what would I do with a Zing laser cutter?
It would be easier to ask me what I wouldn't do with a Zing laser cutter. The answer to that question is not much. I've seen videos on youtube of people using laser cutters to slice pizza, or give themselves tatoos; I would never use a laser cutter for these types of silly actions. Some things I would use a laser cutter for :
- Manufacture parts for my Robo-One style bipeds
- Develop the prototypes for my prosthetics
- produce assistive devices for the handicapped
- Repair things that require unusual parts
- Assist local FIRST robotics teams with more complex acrylic parts
- customize pretty much anything
- Etch circuit boards
- Finish my open source servos
- Begin a plethora of collaborative projects
There really isn't much I wont use this laser cutter for. Hope you ya'll find me worthy of your votes!!
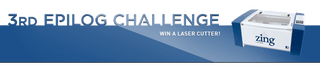
Participated in the
3rd Epilog Challenge
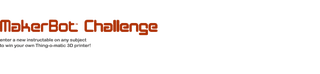
Participated in the
MakerBot Challenge