Introduction: Portable Solar Tracker Project - Circuit Design and Breadboarding
In theory solar energy is awesome. It is clean, free, and plentiful. The drawback is that to directly convert light to electrical energy requires a solar transducer such as a solar panel. The current state of this technology leaves more than a little to be desired in durability, efficiency, and cost. In order to power a home or a car requires large arrays of panels and even then only certain geographic regions provide sufficient periods of direct sunlight.
While solar energy technology is not yet mature enough to be widely accepted as a primary energy source for the general population, it does have some unique advantages. For instance, it can provide a remote energy supply which is great for trickle charging small devices such as cell phones or GPS when traveling, hiking, or camping, or just hanging out at the pool. It can also provide a source of emergency energy for periods when the main power grid is offline.
One way to make the solar panel more effective at harvesting energy is to ensure that it is always pointed directly at the sun. Panels are more efficient at converting electromagnetic radiation which has a direct rather than glancing incidence. Therefore it is desirable for a panel to have the ability to track the sun as it moves across the sky.
This series of instructables will follow my design and construction of a small, portable solar tracking device that can be taken on camping trips or stored in your trunk for emergencies. Along the way I will demonstrate various design and construction techniques which can be used in other projects. In this, the first installment of my Solar Tracker Project series, I will show the circuit I designed and explain its principle of operation. I will also provide a component list and a video of the circuit in operation. For now the circuit will be operated using a 9V battery but in the final device it will draw parasitic energy from the solar panel it will be connected to.
Enough talk. Let's make.
Step 1: Circuit Design and Theory of Operation
When considering options for the design of this circuit one criteria which was important to me was a very low idle current. That is to say that when the solar panel was pointed in the correct direction I wanted the circuit to use as little power a possible since any energy consumed here will be subtracted from the total energy that the solar cell can provide to any connected devices and reduce the overall efficiency of solar harvesting.
With this in mind I chose to use an inverted LED array sensor. When light falls on the P-N junction in an LED, a voltage is produced which is proportional to the intensity of the radiation. By having two LEDs connected anode to cathode, one LED will produce a positive voltage in response to the light and one will produce a negative voltage. When the amount of light falling on the two LEDs is equal these voltages will sum to zero. However, if one LED gets more light on it then a net voltage will exist and can be output. Depending on whether the output voltage is positive or negative we will know which LED is getting the higher incident light intensity.
Since this design relies on a voltage and not a current it will have not power consumption in the sensor stage. This is in contract to a light sensitive resistor or transistor which will have a power draw. Another advantage of the LED sensor is that we can increase the sensitivity by connecting multiple LEDs in series at both polarity locations. Our final design will use 5 to 10 LEDs connected in series for both the forward and reverse polarity locations in order to improve the responsiveness. For now I will just use one in each location as I have shown in the schematic.
The output of the sensor stage will first be connected to an op amp set up as a buffer. This will prevent any small current draw in the downstream circuit from causing changes to the voltage in the sensor array. The output of this buffer will feed two other op amps used as amplifiers: one non-inverting and one inverting. The complementary inputs to these op amps will be set by a series of potentiometers and the the op amp output will be sent to the H-bridge to drive the motor.
The user input and calibration stage is made up of three potentiometers and one resistor. This setup is essentially an adjustable voltage divider. The resistor (470kohm. Sorry, I forgot to label it when I drew the schematic) brings down to voltage going into the potentiometers and prohibits the system from ever having a low resistance path from the anode to cathode. The first potentiometer develops a voltage gap between the two leads going to the op amp stage. Adjusting this expands or contracts the range of stable values in the system which allows some disparity to exist between the intensity of light at the LED without automatically driving the motor. The other two potentiometers adjust the balance point of the system. These must be set such that the motor does not turn when equal illumination is provided to the LEDs.
I should point out that current will constantly be drawn through the input and calibration stage. In order to limit the current to a very low value I have selected reasonably high resistor values (the highest I had on hand for breadboarding). Before I make the PCB prototype I will measure the idle power dissipation of the circuit using two multimeters, one for current and one for voltage, and optimize this stage for minimum parasitic power draw. Power (P) is equal to current (I) times voltage (E), or P=I*E.
The output of the processing stage will control which transistors are open in the H-bridge. When A goes to high, the PNP transistor will close and the NPN transistor will open. When it goes low the opposite will occur. The proceeding circuit is designed such that when A is high, B is low and visa versa. With A high and B low, a current will pass through the motor from right to left as shown in the schematic. If B is high and A is low, the current will go through the motor from left to right. This will cause the motor to turn in different directions depending on the input state and eventually allow the solar panel to align to directly face the sun.
The diodes in the H-bridge, called flyback diodes, are there to prevent damage to the circuit. When driving an inductive load such as a motor large voltage spikes can occur when changing current. A sudden drop in current will induce a large voltage spike and by connecting diodes as shown the current is given a path to travel though which will not fry our electronics.
Step 2: Parts List
Based on the schematic I drew up, the listed components will be needed to construct the circuit. A total of 6 op amps will be present but only 5 will be used based on the current design. However, extra op amps are always a plus at this stage in the game since we can still use the extras as buffers or amps for any additional features that may be added as development proceeds. The BC457 and BC557 are general purpose NPN and PNP transistors, respectively. The 1N4148 diodes are standard 100V diodes and should suffice nicely for the current purposes.
Step 3: Breadboarding the Circuit
As I built and tested each stage of the circuit, I made it into a plug in module for my breadboard. This reduced clutter and freed up room on my board. It also made each module reusable for other projects I may attempt in the future. The design I use for these modules allows the to be plugged directly into the board and power rail.The layout and method for making these invaluable devices is documented in a separate instructable that can be found here: https://www.instructables.com/id/Techniques-for-Beefing-Up-Your-Breadboard/. In order to aid visualization of the motors rotation I wrapper the rotor will a piece of wire.
Step 4: Proof of Operating Principal
In this video I demonstrate the operation of the solar tracker circuit prototype and explain some of it's operating principal. There are ~7 seconds at the beginning of the video before I start talking so don't adjust your set, just stick with it.
Step 5: Next Steps...
There you have it. A functioning solar tracker circuit ready to be optimized. In the next instalment of this series I will fabricate a PCB of the circuit and build the solar panel mount and rotation stage. After testing that the entire mechanism works when run on a 9V battery I will add a solar panel, rechargeable battery pack, and charging circuitry. Until then, hack the planet!
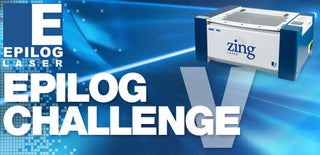
Participated in the
Epilog Challenge V
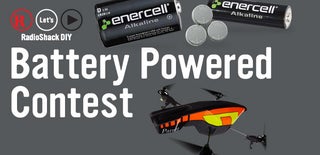
Participated in the
Battery Powered Contest