Introduction: Soldering Tiny SMD Components the Easy and Fast Way (with a Hotplate)
I've being doing electronics for a little while and while SMD components seemed to provide a lot of advantages, I was intimidated by their small size; "how the hell do I solder that?" But as I wanted to use a specific tiny accelerometer for my project, which only came in the minuscule 2x2mm (about 150 of these fit into an M&M!) I was forced to learn it. And to my surprise, it was even more easy an foolproof than normal soldering! This Instructable shows you step by step the process of soldering a small SMD PCB. Total time of doing it is under 5 minutes, even less when you get some practice.
For this Instructable I skip the part of designing the PCB and sourcing the parts, just to focus on the soldering part. If you have any questions on design, manufacture or sourcing, don't fret to ask! And if this Instructable helped you, don't forget to vote ;)
Step 1: Gather Parts
- A hotplate that can be set to a temperature of 150-300ºC (I was very lucky to have access to a Weller station, but anything with an adjustable temperature range will work)
- Solder paste
- (Flux is not necessary as its already in the paste, but it can make fixing mistakes a lot easier)
- Precision tweezers
- An object to apply the solder paste with, this can be anything thin and rigid, I chose to use a jumper wire
- All of your components
- The PCB to put everything on
Step 2: Dispense Some Solder Paste
Now find a (discardable) piece of plastic and put a little blob of solder paste on it. A blob the size of a 3mm LED was enough for my board.
Step 3: Apply Paste
Use your 'applicator' of choice (the jumper wire in my case) to grab a tiny bit of solder any apply it to one of the solder pads on your PCB. To make things a bit easier, I chose to start from the centre of the board outwards and with the biggest parts before the smallest. The amount of solder paste needed is very little, but make sure there definitely is a little blob standing up on the pad.
Step 4: Add the First Component
Now grab your tweezers, grab the component for you pad you just applied solder paste to and drop it into place. Gently push it into the paste to be sure it won't move. Be careful that you oriented the component right!
Step 5: Repeat
Now simply repeat the previous steps for all the other components. Whether your apply all the solder paste first and then place all the components at the same time or apply and place for each component individually is up to you. To keep things interesting, I like to take a group of components of a similar size and place those at the same time. I work from the largest to the smallest components, which allows me to gradually increase precision and concentration; when I arrive at the really small components, I've already practiced on the large ones!
Step 6: For the Really Tiny Parts
One of the components on my board is a 2x2mm accelerometer with 10 pins. The pins were so small that I was not able to individually dip the pads. After some trial and error of having to little or too much solder I figured out an (almost) fail-proof method. You take a tiny bit of solderpaste and apply it in between and on the sides of the pad. The capillary action when soldering will make sure that all the solder is pulled onto the pads and you're sure that you didn't add too much solder. To help this action, I like to apply a little extra droplet of flux. This really makes the component float and pull towards the right pads.
When the solder and flux is in place, simply put the tiny part in place and you're ready to do the actual soldering!
Step 7: Soldering
Everybody who has ever tediously soldered a complex strip-board design will love this step. Set your hot plate to the right temperature, I chose 270ºC, but depending on you components and solder paste you might want to use a different temperature.
Carefully put your board on the hotplate with tweezers, making sure the components don't move. Now the magic happens! After a little while you can see the solder paste becoming fluid and really grabbing the parts into place. Check if all the components are in the right place while the solder is still fluid, and if they're not (like with the tiny parts being just one pin offset) push them into place with your tweezers.
Once you're sure everything is in place, carefully take your board with tweezers and put it on a heat resistant surface.
Step 8: Test and Cheer!
After the board has been cooled, test it! If everything went right and the board programs and/or the LEDs light up, you'll be very happy! If it does not work immediately, take a good look at all the solder pad and use a multimeter to figure out if any connections shorted or didn't connect at all. If this happened you can simply put the board on the hotplate again and add/remove some solder on the place an error occurred. Something you need to look out for is that the PCBs will slightly warp from the heat, this means that the second time you put a PCB on the hotplate, the edges might not touch the plate and it will take longer for the solder to heat up in those areas.
I was very happily please with how easy and error-free this process went and I hope this Instructable will help you as well!
Edit:
As some of you have noted, the Weller soldering station and hotplate I used in the photo's, is not really in the price range of most hobbyists. But there is no need for such fancy equipment. Sparkfun swears by their skillet, Hobbytronics makes use of an electric stove and at Reprap they use a cheap cooking hotplate.
Also, I don't have a clue on what makes a good solder paste/flux and which one you should buy. Some of them have a syringe attached for easy application. Maybe an expert could chip in on this part?
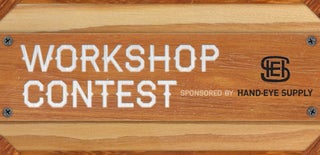
Participated in the
Workshop Contest
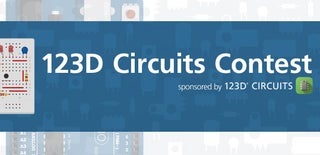
Participated in the
123D Circuits Contest
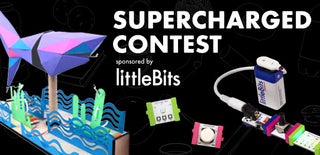
Participated in the
Supercharged Contest