Introduction: Spot Weld Anything (Even Copper)!
There's hundreds of welding Instructables around, many of them quite good. I'm writing this one here to share a technique I've developed that works quite well, even on copper tabs (for which it was designed).
The theory is simple- I've got a handful of ultra-capacitors (2.5 Volts, 2600 Farads) wired in series, then discharged through the material. The devil is, as always, in the details.
Anyone who's tried will tell you copper is a pain to weld- for many of the same reasons you probably *want* to be using it in your project. It's got about five times the thermal conductivity of iron, which basically means you need to pump in a lot more heat to overcome heatsinking. When it comes to resistance welding (which is how spot welding works, unlike other electric welders, which use arcs), you've got even more pain coming- the conductivity is another 5 or 6 times higher. So your welder needs to output 5 times more current just to create the same amount of heat.
Put all this together, and it means you probably need a welder that's over 20 times more powerful than a typical steel spot welder.
Step 1: Bill of Materials
I'll hardly claim that I've got the best setup here- but it does work, so this is probably a good place to start. To replicate my setup, you'll need:
* 4 ultra capacitors.
-I used Maxwell "Boostcap"'s, rated for 2.5V at 2600F. I believe mine are surplus from electric buses regenerative braking systems. I got mine for about $10 each from the Electronics Goldmine (http://www.goldmine-elec.com/), but it seems they're sold out at the moment. You can find them on eBay, too. Make sure they're rated to have low series resistance (in other words, they should be able to provide a lot of current- mine should do 600 amps).
* 3 lengths of heavy gauge wire, with suitable ring terminals on each end. I used scrap I had around- I think it's about 6 gauge, roughly 2 feet long. Each is a different color in my setup.
* thick copper tubing, about 3/8" ID, 1/2" OD. You need two pieces, each about 3 inches long.
* a graphite block(s), enough to yield two pieces about 0.5"x0.5"x3.0"
* two big hunks of copper. I used a 1/2" plate roughly 5"x5", and a cube about 3" to a side. It's not critical.
* Some sort of DC power supply- I used a standard benchtop variable DC supply. It's limited to 3 amps, so charging takes a long time. You could do much better.
* Some means of clamping your electrodes: I used some G-10 fiberglass stock (not the best choice, but fairly temperature resistant and non-conductive), with holes drilled for the electrodes, and a rudimentary hinge. Again, you could do better than my quick-and-dirty solution.
Step 2: Make the Electrodes
I think the key to my system is in the electrode design. Seems like most spot welders use copper electrodes (no good here!), and DIY solutions use more unusual metals, like tungsten. Mine use graphite. It's got great heat resistance, and decent electrical conductivity. I think my system actually works better because the sharp tips of the graphite electrodes (remember kids, conductivity is proportional to area of the cross-section) have higher resistance, so they heat up and help melt the copper.
Basically, I took my piece of copper tubing, tried to sharpen one side as best I could, and then used it to 'cut' into a block of graphite, getting as much wedged in as I could. The copper tubing is there to provide a good electrical path as close to the tip as possible, as well as a good contact to the graphite. I did this on a lathe, but I don't think it's necessary. Once you cant go any farther (mine got firmly wedged in -as I had hoped- after I had about 1.5" in), cut the remaining graphite off to leave you with a roughly 0.5"-0.75" tip protruding from the end of the tube. File it to a blunt point. As you use the electrodes, this point will have to be cleaned up from time to time.
The last step is to hammer flat the end of the copper tube, and drill a hole so you can use a screw to attach your cables.
Step 3: Run the Electrical Connections
I had 4 capacitors, which I wired in series. My caps had screw terminals on the end, and came with ready-made bus-bars, which made this process easier- you may have to come up with something more involved. Make sure you've wired the caps correctly- plus to minus, plus to minus,.... These things will die if you plug 'em in backwards.
As a 'switch', I use two big blocks of copper; I get the material and the electrodes set up the way I want, then bash the two blocks against each other to do the weld. It's extremely crude, but remarkably effective. You may also find it cathartic, after a rough day. I wouldn't know...
With your three cables, you'll want to attach one side of the capacitors to one of the copper blocks (I drilled and tapped a hole in each to make these connections), the other block to one of the electrodes, and the other electrode to the heretofore (I don't get enough opportunities to use that word) unconnected capacitor terminal. Polarity doesn't matter.
BEWARE! the voltages you're dealing with here are not enough to hurt you via electrocution, but will cause serious burns if you accidentally short the terminals with a metal tool. You are building a welder after all. Avoid working on the electrical connections when the caps are charged. I made a shorting wire out of a power resistor, some wire, and alligator clips; when I was finished welding, I used it to slowly and safely drain the capacitor bank.
Step 4: Ready, Get Set, GO!
Once you've got the whole thing assembled, you should use some sort of DC power supply to charge the capacitors. I used my variable DC power supply, a common piece of electrical test equipment. You could probably get away with using a "wall-wart" style dc power supply.
A few words of warning: these capacitors will die if you over-volt them. Be sure to check with a voltmeter to make sure you won't over-charge them. wall-warts generally put out more volts than they claim. Regardless of your charging system, be sure to monitor charge balancing- each cap can have a different amount of capacitance, which means that one will have a higher voltage than the rest, even when you charge them in series. If I took my 4 capacitor bank (each rated for 2.5 volts) and naively tried to charged the system to 10 volts, I'd probably kill a capacitor- one will be at 2.6V, another at 2.4V... you get the idea.
I machined two blocks of fiberglass stock into a 'pliers' style tool, where I can squeeze on one end and thereby press the two electrodes into my work. I then use the other hand to bash one piece of copper against the other (which sits on my NON-CONDUCTIVE table).
Step 5: Performance, Reflections
All in all, this system works quite well to join sheets of copper up to around 25 mils (For everyone who lives outside the USA, a "mil" is 0.001 inches, or .0254 mm) thick (so 50 mils total). From my early experimentations with bank voltage, I believe the welding capacity (i.e. thickness of stock possible) would only increase with more capacitors (and thereby a higher voltage and current limit). For my purposes, this is fine. After all, a strip of copper 25 mils thick and 1 inch wide has nearly the same effective cross-section as 5 gauge wire- pretty serious stuff!
I suppose you could have used car batteries for this- although I feel like ultra-caps are more durable, cheaper, and lighter- at the cost of taking a while to charge before you can start working. My lousy 2.5 amp charging system requires nearly 20 minutes to do a full charge, and a few minutes after every few welds to recoup the charge levels.
According to my performance measurements, my system will provide a peak power of roughly 5 kilowatts (10 volts at 500 amps)- roughly 4 times the average amount a typical American household uses, and far more than any hobbiest-class transformer based welders can do (As far as I know, you'd be hard pressed to pull more than 30 amps -3kW- from a standard american 110 volt outlet). You need every bit of that for this job.
My system is still very much a work in progress; It was intended as a super bare-bones proof-of-concept, not a finished tool. If you intended to use such a device extensively, you'd be crazy not to have an enclosure for the electronics, an integrated charger (with automatic cell balancing), and a built in shorting resistor to drain the bank when not in use. An alternative to the banging method of switching the power would be to use a bank of MOSFET's as a DC solid state relay. Not as fun, but probably better.
One quick note: This write-up was done after the project was completed. I can't seem to find many pieces of welded copper (I gave them all away, or ripped them apart to test the weld strength), so I'll make some more and upload them (and maybe some action shots!) in the coming of days.
I hope you've enjoyed reading this, and maybe learned a thing or two. I'll be checking the comments periodically over the next couple weeks (at least) and answering any questions you may have.
I've also entered myself in the laser giveaway contest, so please vote for me if you feel I've earned it! As a university student, I'd probably end up unofficially donating it to the university, and help other students use it for their projects at (or below) cost.
Step 6: Addendum: Some Specific Results.
New as of Nov. 4 2011:
I fired up my prototype welder, and I've got some pictures and descriptions of the results. I made two welded pieces, and I took another photo of the whole setup, which may help clarify the electrical connections. Each piece is a stack of copper foil- I'm guessing each sheet was about 2 or 3 mils thick.
The first was a stack of eight relatively larger sheets (2"x5"), with roughly 20 mils total thickness. I welded 14 times, each time for maybe half a second or less. I went about as fast as I could (trickle charging the whole time), and when I was done the bank had dropped by about 1 volt.
The second piece is a stack of 16 identical sheets with about 0.040" total thickness. these sheets were smaller (about 0.75"x2"), and I welded them in 3 places. It took about 1 or 2 seconds to do each of these welds, so the bank was drained a fairly similar amount once I had done all three.
Step 7: Improvements (in Progress)
As is readily obvious, this system could use some improvements. In my limited spare time, I'll be trying to develop them. I'll be updating this section as I go, with my prototypes, and thoughts on improvements. I'll do my best, but I make no guarantees that my "here's where to go next" suggestions will actually work. If you want to pass me in development, be prepared to roll up your sleeves and do some (a lot) of testing before you trust it. Not that you should totally trust what I've done, either. Caveat emptor.
Overvoltage protection
First off, you'd want an overvoltage protection circuit to stop your power supply from overloading the capacitors (which will kill them). I developed two possibilities (see the first picture); the first using readily available parts I had knocking around, and the second using an uncommon IC chip (the TC54) which would do a better job.
The first uses a zener diode (you can also use regular diodes- which cut on around 0.7V- in series to create a poor man's zener; I used two in my first prototype, to get a turn-on at around 1.4V) and a resistor to selectively activate a transistor, which discharges the capacitor. Since the voltage on the gate of the transistor is basically going to be the voltage on the cap. minus the threshhold voltage of the zener, the transistor will turn on quite slow- not so good.
The second uses a specialized chip designed to shut off circuits when the voltage droops too low (typically because the battery is dying). BEAM robotics people use these frequently, along with it's cousin the 1381. This guy is better than the zener, since it applies a much higher voltage to the gate of the transistor (Cap voltage-0.3 V), which makes it sharper.
In both cases, you want the sum of your trigger voltage (either the zener or the TC54) plus the turn-on voltage of the transistor (for a typical silicon transistor, this should be about 0.7 V) to be just below the max voltage of the capacitor- I'd test this out before relying on it. You also need a transistor rated (and properly heat-sunk) to handle the amount of power you'll be seeing. You also want a fairly high hfe rating (a.k.a. current gain); I used a 2n3055 (hfe around 50) which was OK, especially since I was using normal diodes as the voltage trigger; however, zeners and TC54's have much lower current ratings, so a higher hfe transistor is probably much better- I did a bit of poking around on digikey, and it looks like the TIP140 (hfe =1000) will do much nicer.
Consistent, tunable, non-caveman switching
While fun, the "bashing two rocks together" switching technique has many obvious drawbacks. The thing to do here is probably to rig up a 555 timer as a "one-shot" with a potentiometer to change the pulse duration. You can then use that fixed pulse to trigger a bank of mosfets (which are happily parallel-izable for higher current handling capability) to discharge through your electrodes. A possible circuit diagram is the second image on this page. You'd want to pick R3 to vary around whatever point you want- I'd say from 200k to about 2M ohms (giving a pulse ranging from about 0.3 to 3 seconds). I've got some big honking mosfets (FDA032N08 which can hopefully handle around 200A each) on their way; I'll be able to give this a try soon.
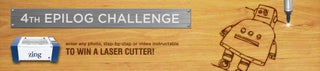
Participated in the
4th Epilog Challenge