Introduction: Standing Desk Pulley Lamps
In this instructable I will walk you through the steps I took to build a pair of lamps that are mechanically coupled to my electric standing desk; as the desk rises or lowers, so do the lamps.
Background
I was looking for an artistic and creative way to light my new Jarvis desk for several weeks until I stumbled onto a picture of a pulley lamp on Etsy, then the project quickly took shape on the back of a napkin. The physicist inside me just couldn't resist the pulleys and the engineer in me loved the idea of a perfectly clear and well lit work-space for drafting. I used three pulleys for each lamp with their cord running from the lamp to the bottom of the table. As the table came up, it would pull the cord and cause the lamps to rise up by the same distance.
I had initially planned to use piping for the wall mounts, like in the photo, but had difficulty sourcing all the materials from Vintage Wire & Supply, so I decided to just use red oak; I think it turned out looking nicer, it just took about 20 hours longer to build. I had initially planned to light the table top with a roll of high CRI Flexfire LEDs, but loved the look, and color temperature, of the vintage bulbs, so I used both. The LEDs are my dimmable task lighting and the incandescent bulbs are my accent lighting.
In total the project took about 45 hours to build, minus design, prototyping, and replacing a burnt out drill press. The project will require basic carpentry and soldering skill and a great deal of patience if you copy my design directly; soldering the LEDs in the lamps was a 6 hour session and it took me the better part of a day to drill all the holes in the pulley arms without any tear-out. There are of course innumerable ways you could modify this instructable to meet your project requirements.
Step 1: List of Required Materials and Tools
PARTS
Flexfire makes the highest quality LED strips on the market. They are about an order of magnitude brighter than the LED strips you can find on Amazon, however they are about an order of magnitude more expensive. They offer 20% off coupons on occasion, if you subscribe to their newsletter, which is how I bought mine. I used a total of 16ft of LEDs in this project totaling 6,609 lumens.
Don't buy these from Flexfire, they are half the price on Amazon
Note, all the cheap dimmers, this one included, are PWM dimmers. If you ever plan to do any video work under these lights you will want to use a linear step down voltage regulator instead, so you don't get flicker in your video.
These niche bulbs can be found all over the place, I was already buying parts from Vintage Wire & Supply, so I ordered my bulbs from them. The spherical bulbs reflect the light from the LEDs beautifully.
Vintage Wire & Supply offers these in multiple sizes, metals and paint jobs. I Loved how the brass looks, but hate how it tarnishes so easily; you really must handle these with gloves if you don't want black finger prints all over them.
Buy the 4 pack to save a little money.
Make sure to buy the UNO sockets, those are the threaded ones.
MIL-W-22759/16 wire is commonly used by the home built aircraft community, it is rated up to 150 C it can carry up to 5A (for 22 awg) and 600V, it does not burn, it is highly resistant to abrasion and most importantly you can buy it by the foot. I had very demanding requirements for the wire in this project, and this wire met them perfectly:
- Be thin enough to slip 4 strands in the paracord
- Safely support 12VDC @ 4A for the LEDs
- Safely support 120VAC @ 0.33A,
- Tolerate a slightly dodgy wire run I needed to to to slip the LED wires past the bulb housing
While prototyping this project I did do one test with cheap PVC insulated 22AWG wire, and while it did work fine I was hesitant to use it due to its poor abrasion resistance and lack of a max voltage rating. There are a few location inside the lamp that are susceptible to shorting (on the 12VDC side) and I didn't want to deal with the pain of digging it open to fix it 6 months from now.
I am a very novice woodworker, this is only my second hardwood project, the first being the desk that it is illuminating, so I just pick up my wood at the local hardware store. There is no special requirement for the red oak, I just wanted it to match the desk.
You can pick this stuff up at your local hobby shop.
I had purchased this initially planning to use it for fabricating the entire arm assembly. I just cut it into pieces to mount the pulleys.
Any switches will do, but these from Vintage Wire & Supply looked pretty cool and fit the motif, especially with the matching knob and cover (below).
This is the magic double stick tape that they use on action camera mounts. I can not recommend this stuff highly enough, I use it more than duct tape. Refer this video by Jimmy DiResta for its many uses.
Minwax Pre-Stain Wood Conditioner
Wood screws or dowel pins and wood glue
24 AWG Solid core wire
Ring terminals
Safety wire
Drywall anchors and screws
Ziptie mounts & zipties
Terminal Strip (with protective cover)
Drywall anchors
TOOLS
Drill
Drill press
Wood cutting band-saw
Metal cutting band-saw (a hack-saw will work)
Soldering iron
Terminal crimpers
Helping hands
Wire cutter
Wire strippers
Scribe
Center punch
3/8" forstner bit
13/32" drill bit
Step 2: Polishing Lamp
My lamps arrived covered with finger prints and very tarnished, so I picked up a bottle of Brasso and polished them up. Alternatively you could put an antique finish on them.
After you polish the lamps wear gloves for the rest of the process, these things are finger print magnets.
Step 3: Mounting the LEDs to the Lamp
I was very concerned about shorting the LED strip to the conductive brass lamp, so I added a layer of Kapton tape on the inside of the shade where I would be making all my solder joints.
Here are the specs for the LED strips:
- 24 Strips per lamp
- 4 inches per strip
- Total length per lamp 8 Feet
- 402 lumens per foot (for high CRI warm white)
- Total output 3,216 lumens per lamp.
Place one strip every 15 degrees. The easiest way to do the layout is as follows:
- Place 4 strips at 90 degrees apart
- Place one strip in between each of those 4 strips (now you have 8 at 45 degrees apart)
- Now place 2 strips in between each of the strips.
Step 4: Soldering LEDs
All of the LED strips are connected in parallel with 24 awg solid core wire.
Alternatively, Flexfire LEDs does make connectors that are designed to slip onto the end of their LED strips (link), but I was concerned about how much bulk that would add to this rather cramped space, which is why I elected to solder it.
I am an electrical engineer by trade, so I have the best pair of helping hands on the market (link). If I did not have these helping hands I would have strongly considered using the Flexfire Connectors, because while not impossible, it would have been painfully tedious without them.
I was getting intermittent shorts to the brass lamp shade from the far ends on the LED strips, so I added a layer of Kapton tape under the end of the strips and this fixed the problem. The strips have a 3M adhesive backing that acts as an insulator between the copper contacts and what it is bonded to, however on the ends of the strips, where the mfg. has spliced them together (every few feet) , the insulation does not always cover the contacts, hence the shorts.
Step 5: Routing / Sleeving Wire
1. Take measurements for your desk configuration to determine how long your wires need to be. (I used 18ft, and had plenty of margin)
2. De-core the 550 paracord (remove the inner strands)
3. Feed the 4 strands of MIL-W-22759/16-22 wire into the paracord sheath and inch worm it through the housing. This is not a fast process, because it is a tight fit.
Step 6: Wiring the Lamp
My color code:
Purple - Hot
White - Neutral
Red - 12VDC Positive
Black - 12VDC Return
To get the 12VDC wires to the LEDs on the face of the shade I routed them between the socket and the socket's insulating housing. If an electrician saw this, they would probably wag their finger at me. I admit it is a little sketch, because the socket gets very hot and it is electrically live. I took two steps to make this a little safer, to a point where I am comfortable:
- I wrapped the socket in Kapton tape, which provides an insulating layer between the metal socket and the pair of 22 awg wires going to the LEDs
- I used Mil-Spec wire that is rated for up to 150 degrees centigrade
If this route makes you uncomfortable you can route the wire from before the strain relief through the holes in the shade holder to the LEDs, but the wire will be exposed.
Step 7: Shaping and Drilling the Arms
I am a novice carpenter, so this process took some trial and error.
My first attempt I tried to shape it without a flat pattern (mistake). I screwed two pieces of red oak together and band-sawed them, so their profile would match, which whey did, but it was no where close to a fair curve. I attempted to make the curve fair on the belt sander, but was not very successful. These scrap pieces came in handy later to make a MacGyvered drill press clamp.
This first piece did give me good practice on how not to drill holes into hardwood, I had tear-out all over the place.
Lessons learned:
- Always use a drill press. I started drilling the 13/32 in hole by hand after piloting and if I was not perfectly square it would tear out on the face of the board.
- Make sure your drill press is square. Haha, ya put a machinist square on there just make sure before you go drilling this many holes.
- Punching through a board using a Forstner bit without a backing board will blow-out the back of the board
- Punching through a board with a regular bit without a backing board is ok, if you go slowly.
- Clever clamping methods are required when drilling this many holes
- Don't overheat your cheap drill press motor by running it continuously, give it some time to cool off. Drill presses were harmed in the making of this instructable.
The final process that worked for me, with no tear-out, is as follows:
- Pilot with a very small drill bit to minimize how much it can walk out of the center punch hole
- Drill almost all the way through with a 3/8" Forstner bit
- Drill out to final dimensions, and all the way through, with a regular 13/32" bit, going slowly.
A more experience carpenter can likely provide a better procedure (please comment below), but this worked for me and I did not have tear-out of blow-out on any of the 60 holes.
All the extra holes I drilled in the arm were initially just for aesthetics, but by sizing them the same as the pulley mounting hole I am free to re-position the pulley on the length of the arm if I ever need to.
The flat pattern is a 24" x 36" PDF file, you should be able to take it to your local copy shop and have them print it for about $5, it is worth every penny. I used a light spray of 3M Super 77 to tack it down to the wood.
Attachments
Step 8: Adding Dowel Pins
Used a 3/8" dowel jig to drill out the holes.
You will want to put a tape depth gauge on the 3/8" drill bit to make sure you don't accidentally drill through to the last hole in the arm.
Step 9: Fabricating the Bases
These bases were a breeze to fab, here is the procedure
- Trace a quick 4" diameter circle (ghetto compass courtesy of Jimmy DiResta)
- Cut out the circle on the band saw, leaving a little bit of margin.
- Belt sand down to the final profile
- Round over the edge with the router bit of your choice
- To transfer the dowel hole location I centered the dowel jig on the base and used my 3/8" Forstner bit to put marks at each of the hole centers by putting it in the jig and pressing the bit down against the wood. The sharp tip of the Forstner bit leave a little mark on the wood.
- Tossing the base on the drill press I can then drill the 3/8" holes out at the marked locations.
Step 10: Gluing the Arms to the Base
I used dowel pins to attach the pulley mounts to the bases, but wood screws and glue would also work and would likely provide a stronger joint. I was not able to clamp up the long pulley arm to the base, so I could not apply pressure during the glue up, it still works fine, it just results in a weaker joint.
If I was doing this again I would simply use wood screw and glue.
Step 11: Fabricating Lower Pulley Mounts
Step 12: Finishing
Pretty standard finishing process here, just followed the instructions on the cans.
Only special thing I needed was to use small lint free wipes to get in all the holes along the length of the long pulley arms.
Step 13: Mounting the Pulleys
- Cut a piece of the 13/32" brass tube 1.5-2" long
- Chamfer one end on a belt sander
- Pound the chamfered end into the locations for the pulleys. It is ok if the brass rod does not go all the way to the other opening, as long as it is most of the way through.
- Trim down the brass tube (that is now press fit into the wood) with a band saw, so that it is sticking out about 1/4". This will act as a spacer between the pulley and the wood. The reason I trim it down to final dimensions after it is press fit is because it is easier to control in the band saw when you have a big wood handle on it.
- Cut the 3/8" OD tube down in a metal cutting band-saw to about 1.5"
- Chamfer both the the edges of the tube with a bench grinder.
- Pound the 3/8" tube into the 13/32" brass tube. Leave about 3/4" of the 3/8" tube extending beyond the brass tube.
- Put the pulley and do a fit check, you want to make sure that:
- The pulley is offset from the wood (it will wobble some and touch the wood when it as at an angle, this is ok)
- There is enough room in the end of the 3/8" tube, when the pulley is installed to drill a hole for a pin
- Center punch the hole for the pin and drill through both sides of the tube.
- Install the pulley
- Drop a piece of safety wire in the hole and bend over the edges.
My pulleys currently lack any safety catch to keep the wire from falling out, which would result in the lamp crashing down on my desk and shattering the bulb. I will likely add one eventually, but have yet to figure out an aesthetically pleasing way to do it.
Step 14: Mounting the Pulleys to the Wall
When mounting your drywall anchors make sure to drive them in all the way. Because the pulley bases have two mounting holes on the same horizontal center-line, they will wobble up and down if the anchors stick out. Even after pounding them in all the way I still used a double stack of VHB tape (with the outer film left on, I don't want to bond it to the wall) to eliminate any remaining up and down wobble.
Step 15: Wiring the Desk
The electrical system consist of two independent systems:
120VAC
- I cut a PC power cable down to size and put ring terminals on it so I could connect it to the terminal strip
- From the terminal strip the live wire is routed to the rotary switch on the desk, so I can turn the incandescent bulbs on and off.
- The live wire is routed back to the terminal strip from the rotary switch
- The White and purple wires that lead to to the socket are attached to the same terminal strip
12VDC
- The 12VDC power supply plugs into the powers strip I have attached underneath the table
- The output of the 12VDC supply connects to the inline dimmer
- The output of the inline dimmer goes to the terminal strip where it is spit to the two lamp LED inputs (the red and black wire)
Update: I have attached an electrical schematic for clarity.
Step 16: Summary
I was very pleased with how this build turned out, and am completing this instructable while sitting at my desk under these new lights.
Future upgrades
- Adding safety catches on each of the pulley wheels so if the cord slips out, the lamps will not come crashing down on my desk. I am thinking of taking a piece of brass and bending it over into a U and bolting / boding it through the pulley.
- Adding a 5A fuse to the the 12VDC bus to mitigate any concerns of a short in the dodgy route around the socket. I will likely use a simple inline fuse older that I can connect to the terminal strip below the desk.
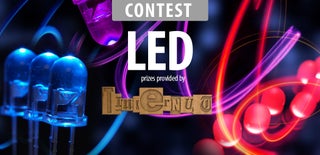
Participated in the
LED Contest