Introduction: Star Trek Enterprise Composite Shelf
On the Enterprise - D there is a wall of model ships which are all named Enterprise. As a display of lineage and scale, I always thought that the design element would be cool to accent any room or office. Kinda like having a display of all the manned rockets from Mercury to Saturn V when I was a kid.
Those wall models were all scaled down to fit the wall space and looked like a simple form for molding with no real detail. They were also painted gold and hence are referred to as the "golden starships".
The models looked like they morphed out of the wall so that was inspiration to make it a functional shelf.
It would be nice to have a laser cutter to fabricate the parts for this build but I am going to show you how to make this project old school style with cardboard and wood popsicle sticks.
Step 1: Somewhere in the Universe...
There exists blueprints for the starship Enterprise. The original series NCC-1701 is the one I want to model.
It is not hard to ask your computer to go find a high resolution graphic drawing of the Enterprise.
I used rasterbator.net to enlarge the graphic to fill 4 sheets of paper. You can scale it up to any size you want and print it out. You can use any poster size printing utility program or app. I had flipped the original graphic in GIMP so it would be facing to the right like the real golden starships.
When the drawing is put together as one sheet, we will mount it on a piece of cardboard so we can work right on the drawing itself.
I laminated two layers of cardboard salvaged from empty shipping boxes and glued them together to make it a stiff board.
I then covered the layout board with plastic wrap because I knew I would be getting glue and paint on it.
Now all you need is cardboard, lots of glue and about 150 wood popsicle sticks(craft sticks/tongue depressors).
Have a pair of heavy duty shears to cut the wood sticks or use a sharp utility knife(score and snap).
CAUTION: Tools that cut will cut. Keep your work area tidy and protect yourself from dust, wood splinters and paint/glue fumes.
Step 2: 3D Model Slice and Stack...
Once you have your set of plans, you can interpolate your 3D model from it.
Read up on my technical drawing primer to get an idea of how to read the diameter and visualize it in space.
We want to make a cardboard core and veneer with wood popsicle sticks.
Like all 3D models, you take slices representing different depths and cut or stack them up to get the full volume. The more slices you make, the more accurate the model will be.
I cut out cardboard pieces and overlaid them on the drawing. Note that we are just making one half or the starboard side of the starship. You can make a whole model and slice it in half for two shelves.
The cardboard slices can go in any direction since we do not need it for strength.
If you had a laser cutter or CNC router you can straight away make a stacked acrylic, metal, cardboard or plywood model.
Step 3: Walk the Plank...
You can pick any pattern to lay with your wood popsicle sticks to cover the cardboard.
I had to trim the rounded ends of popsicle sticks so they could butt up against each other.
When I used a lot of glue to stick the popsicle sticks, some of them warped as they absorbed the liquid from the glue on one side. They curled up lengthwise and thus I had a ripply deck. I was hoping for a basketball court like floor - maybe that is why they are made with tongue and groove joints.
If you have any gaps, use real wood filler to pack into the voids. I thought the carpenter's glue I was using would be good to fill the gaps but it makes for work in the end.
Step 4: Are You Board Yet?
There is a lot of open space to cover. Also, there are a lot of curved cuts and odd shapes to veneer. I like how the shuttle bay door, the cigar shape main hull, and the warp engine nacelle turned out.
I had intended to have a smooth curve or transition to the bulbous parts of the saucer section but popsicle sticks are made from a stiff wood that is hard to cut and is not pliable. I had used a set of heavy duty shears but that often splintered the wood. It is easy to crack the stick lengthwise along the grain so you can better fit it to a curved surface
I built up the curved sections with a shingle technique of going around filling in all the flat spots first and covering the gaps with a cut piece.
Cover the back of the model with popsicle sticks too.
When all done, the entire model should be encased in wood.
Step 5: Shelf and Support...
I still have a bunch of MDF wainscoting scraps to use.
I had a piece that would make a perfect shelf.
I lined the edges with some 1/2 inch square stock cut and glued to form a rim around the perimeter just like the Instructables Robot shelf.
When the glue dries you can sand or plane the outside edges to make them seamless where it transitions. You can also use a thick board or piece of plywood
You could also make the shelf a cardboard core and veneer with the popsicle sticks.
Step 6: Rough It Up...
When all the glue dries...
Sand, sand, sand.
Use a mini-plane, chisel, utility knife, rasp, file, saw, or whatever to trim off any big pieces that need to be trimmed.
Sand, sand, sand.
Two things I learned today:
1. Sandpaper from the dollar store is really cheap. And doesn't work too well.
2. Don't use carpenter's glue as a filler. It dries extremely hard and it is sandable...with a power sander.
so make it three,
3. Don't attempt to sand something like this by hand. It is a chore.
Step 7: Drydock...
Here is where things start to come together.
You can dry fit all the pieces together to see how they will fit.
Prop up your shelf and align it with the center of the warp engine nacelle.
Glue on the warp engine nacelle to the edge of the shelf.
If you have the shelf lined up perpendicular to the attached wall or flat surface, check the length of the warp engine support.
The warp engine support should catch the inner lip of the shelf and keep the shelf level when in use. Trim or modify to fit.
You can glue in two side alignment blocks to the shelf edge so that the warp engine support will fit right in to a recess.
Glue the the bottom of the warp engine support into the main body of the starship.
Step 8: The Prime Directive...
At this point, do a final sanding to get rid of any dirt marks or excess glue.
Use a tack rag or just a slightly damp paper towel to wipe off any sanding dust.
Prime with paint primer if you are painting this shelf in a solid color.
I wanted a clear finish to show off that this is made of wood, or at least look like it...
I used a combination stain and polyurethane finish. It was water based so no bad fumes. This was a "traditional cherry" wood color applied with a foam brush.
I gave it three coats of the finish allowing each coat to dry followed with a light sanding to smooth it out.
Step 9: Secure All Stations...
Drill two pilot mounting holes in the back edge of the shelf near each end.
Drill two pilot mounting holes right under the saucer section in the saucer support section.
Since the width of the shelf is not greater than 16 inches on center, it will probably miss the studs in the wall. I will need to use some drywall shields/toggles when I drill the screw holes in the wall.
Pick a nice spot on the wall to display your model. Have a mirror backing on the wall to get that full 3D effect or have an infinity mirror running as the background.
Mount the shelf level on the wall.
Place the warp engine support into the recess on the shelf. You can add glue for a stronger support.
Align the rest of the ship and drill through the pilot holes to mark mounting holes in the wall You might need longer screws to go through the saucer support section..
Secure to the wall with screws. Use transparent aluminum screws to be less noticeable.
Look, a complete set of the TOS dvds materialized on the shelf!
Enjoy!
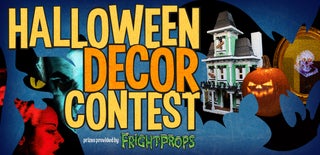
Participated in the
Halloween Decor Contest 2015
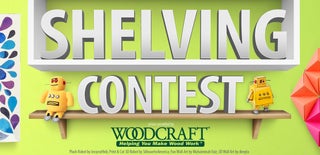
Participated in the
Shelving Contest
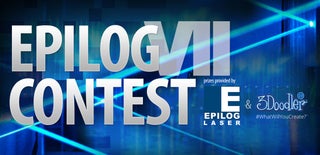
Participated in the
Epilog Contest VII