Introduction: Star Wars Rebel Pilot's Helmet Build
After reading how the original 1977 Star Wars Rebel Pilot helmets were made for "A New Hope," I decided to give it a shot. The prop shop had acquired a number of US Military Flight helmets as surplus from the Vietnam war having just ended in 1975. While there are many variants of helmets, the one they chose was an AP-6 that had a built in microphone connector near the cheek. This exact model drives the cost upwards to over $100 or more if you are willing to rework those beauties. I found a standard flight helmet - complete with working retractable sun visor and clear visor on eBay for $50.
I decided to make it my own design and not follow the squadron schemes as found in the Star Wars Saga. As in military circles, all pilots paint their unique to them so why not here? I also decided to create a Jedi Squadron logo on the cheek sides. I only retained the symbols for major battle awards (yellow V circles) and symbols on the comb / Mohawk crest.
Here is how I did it...
Step 1: Find and Prep a Real Flight Helmet
Materials Needed:
Pilot's Flight Helmet, EVA Foam, 3M Contact Cement, Sheet PVC, PVC Glue, Enamel Primer & Paint, Vinyl Star Wars Rebel stickers, Truck door Rubber edging (kind with metal inside to retain form when bent).
Tools: Tin snips to cut PVC, Manilla tagboard / folders for templating parts, painter's tape, clamps, sand paper
Getting Started...
Strip all the parts and screws, etc. off the helmet. Set them aside so they don't get lost. Get down to just the shell. Sand off all paint, primer, imperfections, glue residue to get down to the fiber glass. It's unhealthy to breathe this dust so wear a dust mask.
We will use fiberglass bonding putty to contour the seams, and fill them for smooth transitions. So to ensure it will stick, sand past the primer to the raw fiberglass.
Step 2: Establish Frames and Major Surface Pieces
Trace out the shapes as seen in pictures from the internet on helmets used in the movies. The actual AP-6 helmet used has CURVED visor retractor knobs, might flight helmet had them straight, so this was the first modification. Trace out the shape you need on the helmet in pencil. Not in the photos I trace the contact line to the helmet and how the visor retractor tapers up as it has thickness away from the helmet.
Cut pieces of manila tag board to match these shapes. Tape them together and keep cutting, taping, and cutting again until they are what you need. Transfer the manila templates to the PVC sheet material and cut them out with a tin snips or band saw. My PVC sheet material was approx. 2mm thick and worked fine.
Screw the Mohawk side pieces to the wood supports. Make a template from manila tag-board for the top of the Mohawk. Trace on PVC cut and screw it down to the wood supports as well. The sides of the Mohawk were somewhat wavy and I was afraid flexing would crack off the bonding putty. So I cut another piece of PVC and doubled up the side walls and glued them together covering the screw heads.
The curved - multi-angle pieces like for the visor retractor, are adjusted several times first with the tag board, then when correct, use the snips to cut them from PVC. Get some welding or heat resistant gloves and use a heat gun to soften those pieces. When pliable, form them to the locations on the helmet and hold in place until they cool and get stiff again.
Step 3: Fill in / Shape Transitions / Sand to Finish
Wipe off all sanding dust and once major pieces of PVC have been cut to shape, fitted and affixed to the helmet - time to putty in the seams for smooth transitions.
Use multiple thin passes for fast drying and smoothness of tapering. Use fiberglass putty with the glass strands for strength.
When built up, then sand until you have smooth transitions.
Step 4: Prime / Base Coat / Finish Coats
After sanding... wipe the dust completely off and prime with a good primer like Rustoleum. A good primer will fill in the voids. If you see variations that look bad, don't rush it, re-sand and re-prime - it will be worth it not to see bad bondo lines or cracks in the joints.
Mask off what you don't need painted and paint away on your scheme. I used templates printed out from my PC to sheet labels and then peeled them off - worked great.
Don't worry about pain imperfections because you will fatigue the paint in the last stage.
Stencil away and paint your scheme. There are a lot of great references on the net.
Step 5: Finish Wash
Once completely painted... now comes the hard emotional part... to beat it all up.
Take the helmet outside on some concrete curb or use a rasp / file and start grinding on the high spots. Go slow at first to get the jest of it, then bang it around on the high points. Once all knocked up... them wash it with a diluted mix of black, grays and or browns to get the dirty wash color.
Apply it and as quickly as it goes on, wipe it off. The wash fills all the knicks up. I even used a solvent on some spots as a cleaning agent would corrode the helmet finish as well. Be creative use whatever works.
Interior & Padding:
1. I hot melt glued ear muffs in the cheek areas to make up the dimension and assure a proper fit to what muffs used to be in there.
2. I added a small battery in the ear muff leading to 3 yellow leds glued into the front edges to creat a tint to the visors as ifin the cockpit in the movie. Notice I wanted to use the original visors - as I think the movie visors look really tacky and cheap with an elastic band. I also painted the sun visor to be my blast shield. Not the scrapes on my blast shield.
3. After the wiring was installed, I cut 1/2" eva foam in sections and glued them inside with 3 M contact cement.
Lastly put the truck hard rubber edging around the neck line.
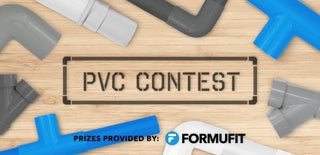
Runner Up in the
PVC Contest 2017
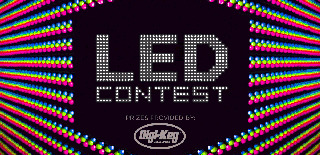
Participated in the
LED Contest 2017