Introduction: Steampunk Mechanical Heart Chest Piece
I wanted to make a costume for a Steampunk themed party, but wanted to do a bit more than just use some cogs as decoration. I thought it would be fun to make it move!
Materials:
- Lid of a swimming pool chlorinator with clear lens
- MDF backing
- Slow RPM 90deg angle motor from ebay
- Cheap plastic cogs (ebay)
- copper and gold stray paint and primer
- printed backdrop on simple paper
- wiring, glues etc
- nails
- Green wall plugs
Step 1: Planning, Planning and More Planning
It took quite a while to figure out how to make the cogs sit at the right height, rotate evenly and still be firmly secured. The other tricky bit was making the whole setup fit under the lens between the chlorinator lid and the timber backing.
For the cogs, I drilled a hole in the timber the size of the nails I was using. Then I had to cut the wall plugs to the right height so that the cogs would be able to rotate help up by the wall plug, and help down by the nail head. I then put superglue in the drilled hole, pushed/hammered the entire assembly (nail, wall plug and cog) into the hole, and trimmed the tip of the nail on the other side.
The hardest bit was getting the wall plug cuts flat and even so that the cogs would rotate evenly over the top.
To sit the motor, I had to use the router to cut a cavity to the right size and shape, then I glued and strapped the engine down with wire. I needed to trim the clear lens as shown to allow the lens and timber to sit flush.
I made 3 holes in the timber to take the 3 legs of the chlorinator lens, and where they stick out of the back, I secured them with a safety pin through a drilled hole, to prevent the whole thing falling apart...
Step 2: Layout and Assembly
When I had figured out who I wanted to layout the cogs in the assembly, I glued the backing paper down, installed the engine first, and then started adding cogs to the engine by drilling the hole, lining up the heights and distances (close enough, but not pushing too hard on the neighbouring cog), putting superglue in the hole and pushing the assembly down and meeting the other cogs.
The next challenge was to transfer the drive from one level of cogs, down to a lower level, in order to achieve a more interesting aesthetic finish with cogs moving at multiple heights. To do this I super glued multiple cogs to the bottom of the larger cog, until I had a cog at the lower height. With enough surface area of glue the torque is transferred ok.
The cog sizes need to be arranged carefully in order to avoid then clashing together, and also fitting the in the enclosure.
I then added multiple non-moving cogs to the empty areas, and also to the tops of the nail heads, in order to avoid them being seen.
Step 3: Light It Up
Once I was happy the things were working ok mechanically, I wanted to add some light so that the moving parts would actually be seen! After a few various tests, I decided to use an led strip.
I cut one to length to fit around the outside border of the clear lens (on the other side from where the cogs are mounted) - However it was too bright. Therefore, to drop the light intensity, I simply used some white electrical tape to cover the LEDs, which provided the perfect brightness. I also tried with various electrical tape colours for effect, but then the cog colours would not show up.
Once all was working, I soldered the LED strip and the engine together with a standard plug connector. This plug hooks up to a 8 x AA battery pack, providing the 12v required to run everything.
Step 4: Finished Product
here you can see how it all fits together. The assembly sits on the chest with lateral straps and a neck strap. The battery pack is in my pocket and the wires run inside the jacket.
The video shows the entire thing in working operation. The flickering light is due to a temporary poor connection (I was manually holding the wires together)
As you can see, the main problem I had was that the hole I made in the cog that is pushed over the engine assembly is not quite dead centre. Therefore, when the cog rotates, the radius to the other cogs that it is driving varies. This means that at times it does not drive all the cogs.
I really wanted to fix the issue, but this would have meant undoing a LOT of work. If this eventually fails, I should be able to replace it.
I hope you have enjoyed this project as much as I did making it !
Keep up the creativity !
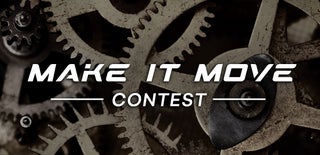
Participated in the
Make it Move Contest