Introduction: Handmade Harry Potter Wands
If you've read Harry Potter, or at least seen the movies, then you know that a wizard's wand is a very important tool. You also know that wizards and witches have some level of attachment to their wands, and perhaps vice versa, as "the wand chooses the wizard." I'm no wizard, but I like making things and I like Harry Potter, so I made my version of a wand from the world of Harry Potter. I don't have a magical attachment to it, but the time spent meticulously carving it led to an attachment nonetheless.
These are fun to make and collect, and they would make heartfelt gifts, as they are made by hand and can be custom designed.
Step 1: Materials and Tools
Wand Material:
- Wooden Dowel (I chose a 4-foot long 3/4" poplar dowel for $2.99 at my local hardware store, but a smaller diameter would also work)
Tools Needed:
- Saw
- File
- Knife
(The saw, file, and knife are all on my Leatherman multitool, which made it convenient for me)
- Sandpaper (coarse and fine grit, I got sheets of 120 and 220 grit sandpaper for 99 and 79 cents, respectively)
- Pencil
- String
- Stain, finishing oil, paint, etc.
- Mineral oil, spray lacquer, etc.
* If you have access to power tools, use them. These wands could potentially be made entirely with electric sanders and such, which makes it easy. I have limited access to those kinds of tools, so I did everything by hand.
Step 2: Customize the Dimensions
Since my dowel was 4 feet long, 3 16-inch sections can be perfectly cut from it. I made my wand about 16 inches long, which is actually pretty large according to J.K. Rowling. I suppose normal wands are from 10-14 inches, but those seem a bit short for me.
I made marks at 1/8" , 6" , 6 3/4" , and 16" from the end of the dowel. I butted up the end against the wall and held my pencil in place while spinning the dowel to get even marks around the circumference.
The 1/8" was a buffer from the red dye they use to mark the end of the dowel - I just chopped it off. This means my handle is just under 6 inches long. The 3/4 inch section was carved into a ball-shaped accent - if you use a smaller diameter of dowel, match the size of this "ball" to that measurement.
Cut your wand blank from the larger dowel at the 16" mark in my case.
Step 3: The Rounded Accents
Using the file, make two grooves at the 6" and 6 3/4" marks. Then, holding the file at an angle, widen the gaps and eventually round them to make nice curves.
Round the end of the handle the same way.
Step 4: The Spiral Handle
To make a spiral pattern in the handle, file away 2 rings about half an inch from either end of the handle. These rings will be where the spiral stops and starts, and provides a neat transition for those.
- Tie the string to one of those grooves, and then begin looping the string down the handle, adjusting as you go for consistent distances. Slip the end into the other groove and secure it by tying or just by wrapping it around a few times.
- Trace along the path the string makes with a pencil and remove the string.
- File away a groove that follows the line you just drew, and deepen it and widen it with the file or a small roll of sandpaper. The curved shape of a tightly rolled strip of sandpaper creates a smooth groove.
- Do the same to the two rings you started with.
Step 5: The "Blade"
The blade was the most difficult part for me. I knew that sanding or filing it down from the stock shape would take forever, so I whittled it down with a knife first. Poplar is soft, so I kept splitting off huge chunks and making large divets on accident. Luckily, I didn't pit the surface too bad and everything sanded out.
The trick is to make short, light passes with your knife and remove the material a little at a time. For a tapered blade, you will obviously remove more material from the end, but don't see that as an opportunity to dig your knife in to make it go faster. You could easily split off half the thickness of the wand, which is not a good thing.
After the rough taper is achieved by whittling, sand out any imperfections with coarse sandpaper.
Step 6: Sanding & Finishing
Sand all surfaces smooth with fine sandpaper - 220 grit in my case.
I didn't do extra sanding on the spiral groove, as I was hoping that it would appear darker after staining - I think a rough surface absorbs more of the stain. It worked reasonably well.
Follow the directions for your stain of choice. I bought a quart of Minwax Early American stain for 7 dollars at Walmart - I like the color.
The stain left the wand kind of dull and . . . dry feeling(?), so I used mineral oil to give it a smooth and glossy sheen. This is an optional step, but it makes the wand have a more golden glow. Wipe off all excess oil afterwards.
That's it! Your wand is done, and by now you should be proud of it regardless of imperfections. Have fun collecting these as you make more!
Step 7: Explore Other Designs
These are all wands I made before posting this Instructable. They are made out of 1/2" poplar, and most of them are just spray painted. There are different design details in each of them, so feel free to combine those aspects or mix and match them to your liking. They all utilize the basic techniques expressed in my Instructable.
Thanks for taking a look at my project! I really hope you try this one out, and please post pictures if you make it.
Thanks to everyone that voted for me in the Wizarding Contest!
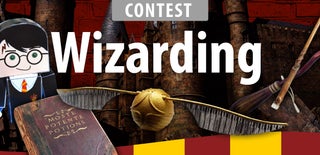
Second Prize in the
Wizarding Contest