Introduction: THE ULTIMATE LIGHT BULB WALL HOOK
A few months ago while looking through some of the awesome Instructables, I came across the Concrete Light Bulb Wall Hook by Whamodyne. Ever since reading that Instructable, I've been literally... "hooked".
I decided to make my own version by improving upon the idea by making it as realistic as possible.
I've taken my old unused lightbulbs and turned them into something very unique, very useful, and very different than what Edison intended.
I think this makes a nice addition to the BEFORE & AFTER CONTEST.
I started a few months back with just an idea, not sure whether it would work out or not.
I do have this to say: this is the most difficult Instructable to date. I had almost given up a few times trying to figure it out - but persevered and finally reached my goal.
Hope you enjoy this Instructable!
Step 1: MATERIALS + TOOLS
Ok, the tools and materials you will use are:
1) Dremel tool
2) Diamond bits
3) Mixing cups
4) Painters tape
5) Plumbers torch (MAP gas)
6) Leather gloves
7) Safety glasses
8) 5/16" x 3" anchors bolts + nuts
9) Light bulbs
10) Epoxy resin
11) Respirator
12) Wet/dry sandpaper (800, 1000, 1200, 1500, 2000, 3000 grits) OPTIONAL
13) Liquid car wax
14) Disposable nitrile rubber gloves
Step 2: Let's Get Started...
#1 priority is safety at all times working with glass! Light bulb glass really wants to fly....BE CAREFUL!!
ALWAYS HAVE YOUR GLASSES ON AND WEAR YOUR LEATHER GLOVES!
Take your torch and slowly introduce the metal end of the light bulb into the orange part of the flame and rotate it.
(If you're too aggressive you will hear a "pop". This occasionally happens. The glass and metal cap break off together at the seam, making the bulb useless. Keep the metal cap if not wrecked and throw the other parts away. Try again with less flame).
When using your torch on the metal cap - you don't have to totally melt it, just soften it up. It's really soft pot metal and will soften very quickly.
Once it's soft, quickly grab your knife and put the tip into the seam of the metal cap - then cut it off. It will take a swipe or two from the knife.
After the metal cap is off, the glue underneath is still somewhat soft. You can now carefully cut or scrape it off with your knife.
Step 3: DREMEL TIME!
Make sure your have your safety glasses on!
Also - wear a dust mask or respirator.
Take your Dremel tool and attach a diamond coated cut off wheel.
Start cutting around the rim of the bulb. You want the top part to come off clean including the filament. (Put tape around the rim edge for extra support because the fragile glass will want to crack from the vibrations of the Dremel).
Once you cut through the top - carefully remove the filament from the bulb and set it aside for later.
Step 4: Clean Out the Bulb....
FIrst, find the capacity of your bulb by pouring water into it.
It's ~125 - 150ml. This is the amount of epoxy mix you will use.
Now that the empty bulb is ready to go - we first need to clean it out thoroughly.
I first clean it out with hot water, shaking it back and forth - then empty into the sink.
Now, use a hair dryer on the inside of the bulb to dry the water.
Once dry - I like to use Wax and Grease Remover to get rid of the remaining grime that the water never removed. (remember: oil and water doesn't mix) Pour it in the bulb, shake it up and then empty contents back into container.
Dry again with the hair dryer.
Now it is thoroughly clean and ready for the liquid wax. This is what prevents the epoxy from sticking to the glass.
Pour the Meguiare's wax into the bulb and shake it up good, holding your thumb over the top. Empty the wax back into the bottle it came from.
Now use the hair dryer again, and dry the wax inside the bulb. You will see there is a slight cloudiness once it dries. That's ok - it's a waxy film so your epoxy won't stick to the bulb!
Now it's tape time :~)
Step 5: Tape Up Your Bulb, Bub
Now you will tape up your bulb. The reason for this is because when the epoxy resin and hardener mix - it starts what is called and exothermic reaction = gives off heat. A lot of heat! This heat will want to cause the mix to expand and push outward on the glass. This will crack the glass and/or displace the glass somewhat and will make the epoxy dry uneven. This can be prevented with the tape.
You can go without the tape - but you will be doing a lot of hand sanding to smooth down the uneven surfaces.
In the above pics - you can see me dry fitting the filament into the bulb. Do so carefully to not bend the arms of the filament. Try it a few times to get the hang of it because you don't want any unsuspecting issues once you've poured the epoxy.
EPOXY TIME
Find a container big enough to hold your mixing cup. I used an old margarine container.
Fill it with hot water.
Put your rubber gloves on and your respirator too. Make sure you work in a well ventilated area like the garage.
Measure out your epoxy in a mixing cup and your hardener in another mixing cup. (follow the instructions from your epoxy manufacturer).
Place the mixing cup holding the epoxy, into the hot water container.
(this reduces the viscosity of the epoxy so well - it'll pour almost like water! This makes it very easy to work with).
Remove the epoxy from the hot water bath and pour the hardener into the epoxy cup.
Stir well but not too agressive. You don't want a lot of air bubbles.
After a minute or so of stirring and when the mix appears to be clear - pour the epoxy mixture into the empty light bulb. Leave a little bit of room at the top.
Wait 10 minutes for bubbles to rise, then use your torch to quickly pass over the bubbles to pop them.
Now take your filament, and carefully place it into the light bulb. When inserting the filament it will displace some of the epoxy - let it flow down the sides - it's ok.
Now you're done. Wait a few days then you can start removing all the tape from your bulb.
Step 6: Glass Removal
SAFETY FIRST! Wear your glasses and your leather gloves!
Ok, this is the fun part where you get to see your final product.
Stand or sit over a garbage can or bucket and carefully remove the glass.
Be very careful - this glass is very thin and wants to fly!
If you've waited long enough for the epoxy to set - the glass will easily come off there with no problems.
Step 7: Prep Your Cap and Bulb
SAFETY FIRST!
Ok, you now want to remove enough of the glass around the top rim of the bulb so your cap sits on there properly.
Take some of the different diamond bits and use them to clean up the inside of the cap.
Place your cap onto the bulb so it is centered over the hole.
I used a dab of Krazy glue to temporarily hold it.
Place a nut onto your anchor bolt and place into the hole. Adjust accordingly.
Once you're happy everything lines up - mark around the rim of the cap with a marker.
Now use a small dab of glue to hold the cap on.
Step 8: A Little Fun Before the End
I held a small LED in the bottom of the bulb to show the cool effects of this project.
Step 9: Now Install Your Anchor Bolt
Now we will install our anchor bolt and do the final pour of epoxy.
First, tape up your bulb to protect it from the epoxy.
Mix up a small amount of epoxy as per the instructions in the earlier steps.
Pour a small amount into the recessed opening of the filament - then place in your bolt.
Make sure everything is straight and square.
Let it stand for a few days.
Step 10: Final Finishing: Optional
There was some residual epoxy that I had to remove. Also, the black marker around the bottom of the cap seemed to get covered by the epoxy and was hard to remove. I initially thought I was just going to wipe it with acetone and it would be gone. Nope, it got covered a bit so I had to remove the epoxy first with acetone, the clean everything up with the razor. So, maybe try and find another method to mark the cap location.
Start at 800 grit wet/dry sandpaper and work your way up:
800, 1000, 1200, 1500, 2000, then 3000 grit - then final polish.
YOUR DONE!
Step 11: The Ultimate Light Bulb Wall Hook
I hope you enjoyed this Instructable and ask that you vote for me in the BEFORE & AFTER CONTEST
And that's it. Just remember...I didn't invent the light bulb, but I did make it cooler!
Craig Arges
Canada
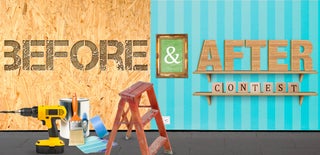
First Prize in the
Before and After Contest