Introduction: The Makeup Box
As a daily make-up wearing person, I have a specific set of things that are used regularly and are rather oddly shaped. How do you store these items so they are handy, organized, and safely stored? Since I was a teenager, I've used the same small bag to store all of my current makeup. The bag has never quite fit everything and anytime I find a new shade of eyeshadow or lipstick I want to buy I had to play this game of how to line everything up to try to zip the thing closed. This box has more than enough storage for all of my current daily items and sits near the mirror with a lovely presence that feels more like a romantic addition to my daily routine than an awkward and forced "resolution" to how one stores many small round objects.
In addition to being lovely and useful, this box has a secret! Hidden in the back is a secret drawer where I can keep all of my beauty secrets and favorite items that I don't want to lose. With a simple push in the right spot, a drawer opens and my lovely things are ready to be worn and enjoyed.
Below is a video of the box and its hidden drawer and how it all works.
Step 1: Determine Size and Shape of the Case You Wish to Build
Everyone has different needs when making cases to hold items you own. I’ve never found a store bought case to fit everything just right. Sometimes spaces are too large for what I wish to store and leaving a bunch of unused area taking up room without adding any value. Sometimes things don’t quite fit the space that is designed to hold the object. Either way it can be very frustrating attempting to make a store bought case work for your needs.
To make sure you have the perfect fit, take some time to measure the items you wish to store in the case. Use these measurements as your starting point for laying out the shape of what you are building. I found that the makeup products I use come in 2 different shapes - skinny tubes (mascara, lipstick) or flat round containers (eye shadows pots). Upon further inspection, the skinny tubes could easily be divided into two groups: items smaller than ½” in diameter and items between ½”=1” in diameter. This realization launched the first compartments I laid out - 2 deep narrow boxes to hold those items upright. The second set of items - the flat round containers - were less difficult to build a space around but I still layed them out to figure out the best dimensions for the tray that would hold them.
After the rough dimensional sketch is made, it is time to clean up the sketch and figure out exactly what your pieces need to measure and how the case will be constructed.
Step 2: Planning the Construction and Pieces
There are a variety of ways you could construct a small wooden case like this one. I have very limited access to woodworking tools (apartment living doesn’t lend itself well to owning large tools) but I can use a laser cutting service to cut custom wooden pieces. I set up my pieces to be cut by a laser cutting service which meant I spent a lot of time using a computer drawing program and I was limited by what I could do with pieces which interlocked.
Don’t forget to pay attention to the thickness of the stock you are using when creating your layout. For this project I used exclusively ¼” thick stock so I wouldn’t have to remember which thickness to use for each piece. As I built the case in the drawing program, I ensured that each piece of wood had the thickness accounted for and the inside dimension of each compartment was correct for what it was designed to hold.
After each piece was laid out and the places where they would interlock were marked on adjoining pieces it was time to create the interlocking box joint design for the perfect fit.
Step 3: Incorporating the Hidden Compartment
Building shaped compartments for specific items means you might end up with some “dead space” somewhere in the box. One option is to do something clever with the space to make the box more useful on the surface. Another (much more fun!) option is to create a hidden space only you know exists.
If you look at my diagrams in the previous steps, you’ll likely notice the large dead space toward the back of the box under the shelf designed to hold the flat wide objects. There are a few different ways to handle accessing the space. You could work out a way to lift the self out, or maybe a trapdoor in the back. I’m sure there are many other Instructables projects that show you how to manage those types of secret spaces.
After thinking a lot about how I would use the case, what I might want to secretly store in the case, and what makes the most sense for a case like this I came up with a plan to incorporate a drawer.
This raised several questions. How do I prevent the drawer from sliding out on its own? If it is hidden, it should not be difficult to move since there will be no external indicator of its existence and it cannot have a handle or hole so how do you make a wooden drawer resting on wood slide easily? How do I hid the drawer so that if you look at the back of the case you would not suspect anything is there?
Let’s talk about how to prevent the drawer from sliding out. Some sort of magnetic closure or discreet latch would work. I settled on a push latch. The strong magnetic clip securely holds the drawer and it is something which can be carefully positioned so that the drawer front perfectly aligns with the back of the box - keeping the illusion that there is nothing there.
How do you make wood slide easily on wood? Drawer tracks would be an option if they made them small enough to fit inside this tiny hidden spot. Finding (or making) some type of tiny wheel to mount to the bottom of the hidden drawer that would allow the drawer to glide along the bottom of the box would be a great solution. I found a pre-made option that is typically not used with wood but had all the characteristics I was looking for - I found very small shower track wheels.
To make the drawer very hidden, the drawer face needs to be the perfect size and shape. I used a laser cutting service for my pieces and the drawer front is the exact piece of wood cut from the box back. How do you hide the drawer? In my early ideation of the project, I was planning to do a wood veneer motif that had design lines that matched the edges of the drawer to camouflage the edges of the drawer. What I ended up using to cover the box disguised the drawer very convincingly.
Step 4: Make a Test
In several places, 3 different pieces will come together. When working in 2 dimensions at a computer screen or sheet of paper to create a 3 dimensional box a lot of theoretical thought goes into the layout. Before cutting the pieces from wood, a test cut and construction of the pieces is an incredibly handy tool for ensuring a great end product. Do the pieces fit together how you expect? Are there conflicting pieces or gaps anywhere? How does it look size and shape wise? What about your hinges or closures? Are they positioned well? Do they have enough space to be securely attached?
After making any adjustments to the pattern you are ready to move on to cutting the pieces from wood.
Step 5: Supplies
The supplies required for this project really depend on the features you want and need in what you are building. Below is a list of what I used to complete the project.
Special Supplies for the Hidden Drawer:
Magnetic Touch Latch Catch
Tub Enclosure Sliding Door Rollers (flat)
Box Supplies:
Assorted 1/4" thick stock - 3 pieces of 12X24" hobby plywood, a few pieces of 4" wide aspen
Assorted Hinges - Continuous Hinge, 1"x3/4" hinge (4qty), 1 1/4" hinge (2qty)
3" x 4" Mirrors (2qty)
Hobby Wood "boy" 1 11/16" x 5/8" - box legs
Wood Stain (optional)
Screws
Preferred Box Covering
Suggested: Veneer, Paint, Leather, Fur
Other Supplies and Tools
Wood Glue
Barge Cement
E6000 Glue
Straight Edge Blade (x-acto/box cutter)
Pencil
Drill
Screwdriver
Dremel with Cutting Wheel
Safety Glasses
Clamps
Sand Paper
Step 6: Dry Fittings and Gluing the Pieces Together
Once the pieces are cut, it is a great idea to put them together without glue to make sure everything fits correctly. You will also see if there are any spots that are tricky to align so you are not scrambling with wet glue.
With box joints like I used, adding dots of glue in the valleys of the pieces is enough to hold pieces which interlock tightly. Clamping the pieces together helps hold everything while the glue sets. In addition to clamping, dry fit the adjoining pieces so that what you are gluing does not set into a position which creates problems later.
Step 7: Building the Hidden Drawer
The hidden box has a pretty simple construction. All the pieces lock together and need just a bit of glue to hold them together.
Before assembling the box, add the flat pieces of the magnetic touch latch catch to the inside of the drawer front. It should be centered and placed down from the top edge to match the placement of the latch catch mechanism. The push button part of the mechanism is attached to the main part of the box and should be attached before final assembly for best results. Use care to ensure the two pieces line up correctly.
If the screws are too long for the stock you are using, you should cut off the ends of the screws for a flush finish on the outside of the box. I used a Dremel tool with a cutting wheel (don't forget your safety glasses!).
Glue all the pieces together and attach the tub wheels to bottom of the hidden drawer.
Step 8: General Assembly
The box joint pieces go together in a logical way but care should be taken to ensure that the pieces are put together in an order that makes sense and doesn't leave anything out. For this box, I assembled all the middle pieces - the vertical dividers for the skinny tube objects and the shelves first. The dividers were glued to the bottom of the box, then the sides were added. The last pieces to be added were the back and front.
The lid was glued together and clamped to set in position over the box to ensure it ended up at the correct angle.
Step 9: Small Touches and Accents
Finishing the Inside of the Box:
I preferred to stain the inside of the box. I had an oil based stain which could have interfered with the strength/connection of the glue if some stain got into the joints so I waited until the box was mostly completed before staining.
Giving it A Lift
After seeing how the box looked after it was mostly assembled, I decided I wanted it up on feet. It gives it a lighter feel plus if I keep this in the bathroom the fur/bottom of the box don't risk getting wet.
I found these wooden pieces in the woodworking part of a craft store. They were marked as "Boy" pieces - most likely for simply children's toys. I liked how they looked with the ball on the ground so I drilled some holes into the bottoms to attach them to the box.
The Mirrors
I wanted a couple small mirrors in the box which could be adjusted for the best angle when applying makeup. I attached a couple hinges and glued the mirrors to the hinges with E6000 glue.
Step 10: Hinge Assembly
I was lucky to find a continuous hinge that was the same size as the box. The assembly was pretty easy - mark and drill the holes, line up the hinge and add the screws. This was almost the last construction step for the box. Attaching the lid had to be done before adding the outside finish.
Step 11: Adding a Fur Coat
Before attempting to glue down fur to a wooden box, clean up the back sides of the hides. Depending on the quality of the hides, there may be a bunch of loose skin that will only get in the way and prevent the fur from adhering to the box properly. Sharp scissors will make easy work of this.
For the most part, I tried to work with the given shapes of each animal hide. I used 3 total - one with tan/grey markings and 2 all white hides. Think about the direction of the fur when considering any placements.
Trimming for edges is necessary. For the best possible fit, fold the fur back and mark the edge with a pencil. This worked all over the box for cutting the correct shapes to fill certain gaps.
When cutting fur (faux or real) never use scissors! Use a straight edge blade (like an X-acto knife or box cutter) on the back side of the hide. Hold the fur up when cutting to avoid giving the fur a 'haircut' on the front. It is not a particularly easy way to cut something with stretch but a very sharp blade is your friend here.
Apply the fur to the box with barge cement. Smooth out thin layers of the barge cement in small segments (I used a toothpick to do this) and carefully position the fur on the cement. Do what you can to avoid getting the fur in the barge cement - it does not come out.
Hidden Drawer:
The fur was carefully placed to hide the drawer on the back of the box.
Hinges were added for the lid supports before fur was placed on the edges of the back.
Step 12: Finishing Up
Attach the lid supports to the back of the box. Complete any last minute touch ups and you are all done.
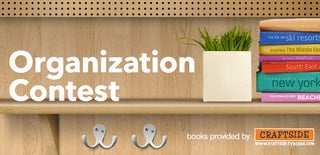
Runner Up in the
Organization Contest
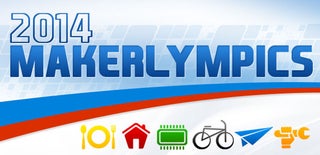
Participated in the
Makerlympics Contest
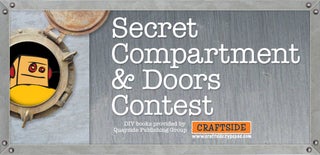
Participated in the
Secret Doors and Compartments Contest