Introduction: The New and Improved Brushless Electric Scooter Power System Guide
In 2008, I put together a guide on Instructables about upgrading the power system of your small personal electric vehicle . It was a primer on the basics of an electric vehicle power system and offered resources and tips specific to compact electric scooter conversion. As of right now, it has a solid 5 rating - I didn't know you could write that much on Instructables without telling anyone how to build anything and still receive perfect reviews.
I am delighted to report that in 2011, three years after the fact, that putting together a compact, powerful, and efficient electric vehicle drivetrain for local commutes (such as your campus, neighborhood, or urban area) using both R/C hobby hardware and specialized EV components is now cheaper and easier than ever. Price competition, new technologies, and just plain increased availability of fabrication and material resources means that building an electric personal transport device is now within the capabilities of just about everyone.
I will assume that you already know the fundamental parts of an EV or have built them before. If not, you're welcome to refer to my previous Instructable on this topic (linked above), or check out one of the many great Instructables on EV systems. This Instructable is intended as a conglomeration of resources, and so will discuss the pros and cons of component choices, specific vendors, design strategies, and other high-level considerations. It will also offer tips and tricks that I've found or had passed on to me pertaining to building small electric scooters. The guide will be overtly calibrated towards said scooters, since I favor them over electric bicycles, though much of the advice is just as pertinent to e-bikes. It should also be helpful for the occasional odd electric skateboard or other unconventional vehicle.
The format of the Instructable will primarily be a page or two on each primary component of an EV - such as the motor, controller, battery, and drivetrain (and associated mechanics).Then I'll present some designs that have emerged as being relatively easy to execute and fabrication advice for fully custom vehicles (i.e. not conversions).
Step 1: R/C Hobby Parts: the Pros and Cons
The focus of my previous instructable was on repurposing R/C hobby, namely model aircraft, parts for vehicle propulsion. It will also make up a substantial portion of this one. Why on earth would you use parts designed for things which aren't technically supposed to be touching said earth when they're working correctly?
R/C aircraft components are the highest power-to-weight electric power systems easily available to the average consumer.
In the quest for ever-increasing flight durations, model sizes, and acrobatic performance, the R/C aircraft world has seen most components such as motors and motor controllers pushed to the limit of realizable power densities. The performance of the average brushless airplane motor greatly exceeds that of an average ferrite-magnet, DC brush scooter or bike motor - typically by three or four times. In the size and weight of a 500 watt electric scooter motor (about 3 inches diameter, 4 inches long, and weighing about 4 pounds), the example motor shown at the bottom can handle 2 - 3000 watts (i.e. 3 to 4 horsepower) of power throughput, and up to 6,000W peak.
The advent of mass produced, high performance lithium ion batteries is another factor. A modern lithium polymer (more on the distinction between different lithium flavors later!) battery the size of a U.S. house brick (about 1.3 liters) can store up to 300 watt hours, at the usual lithium polymer energy density of 240 Wh/L, and discharge at several kilowatts for a few minutes. No traditional lead-acid, or even nickel-chemistry battery system can come close to that. Granted, there are downsides to having such a dense energy source, and those will be addressed, but the truth is there in the numbers.
Part of my engineering interest is taking advantage of these increased power densities to create ever more compact but still practical vehicles. For instance, only with brushless technology is the miniature hub motor I've been working on a possibility...much less electric inline skates using them . Electric scooters are still imagined by most people to be large, low-performance, lead-acid battery powered monstrosities that are reserved for kids with back yards too big to run around efficiently in. While this may be true for most commercially sold ones due to cost reasons, if you're building one yourself, there's no reason to not expect better.
R/C aircraft components are the best power-to-price electric power systems, period .
You'd notice I left the fine print "commonly available" up there, because there are things which are more hardcore than a cheap brushless motor in terms of power density. The problem is, you can't buy them. Not easily, and definitely not cheaply. However, because R/C aeromodelling has become so prolific, parts are readily available over the internet and extremely cheap. Most R/C parts these days are manufactured in China and other East Asian countries and sold by dealers directly from those areas.
Even three years ago when I wrote my previous piece, this was not as true as it is now. The electric flight market, for the better part of the last decade, was dominated by high-market European manufacturers, and so was extremely expensive and also exclusive. The American market had two major motor manufacturers in this era which were well established: Astroflight and Aveox (which seems to have left the hobby market), and probably also Neu Motors . While the most hardcore of aeromodellers still stick with the highest performance European and American brands and companies, the majority run some inexpensive East Asian power system.
For a custom small vehicle, it's hard to find parts which have better price numbers. Depending on your power needs, a motor that has enough wattage to propel a vehicle will run between $40 to $100. A controller that can run the motor will be around $50 to $150. Batteries are the big cost breaker for EVs, still, but typical model aircraft lithium polymer packs price out to between $0.40 to $0.70 per watt-hour . A scooter may have around 150 to 200 watt hours of battery onboard, so expect about $70-100 in commonly available batteries. As I will show in more detail, you can assembly a roughly 1500 watt electric power system for something like $200 to $300 - and that is for everything , even including batteries, and a charger if you're good at shopping.
All of this might seem like cheap airplane parts are the way of the future. However, they also have their downsides.
Unfortunately, R/C aircraft components are usually very rudimentary and somewhat fragile .
Let's face it - airplanes are, in the purely mechanical sense, pretty easy loads to handle. The torque and power required increase directly with speed, so there's no static or locked-rotor (stall) conditions to worry about, unlike in vehicles where maximum torque is required at zero speed in order to accelerate from standstill. Airplanes are never supposed to hit things, bound over rocks and sidewalk cracks, or be jostled by suspension movements. What matters more in aeromodelling is light weight.
As a result, model motors are usually made as lightweight as possible, using thin metals and plastics, and undersized bearings and shafts. Substantard metal alloys (such as soft architectural aluminum) are common in "cheap" motor construction. R/C power controllers are usually single-PCB affairs which pack power semiconductors and logic right next to eachother using the minimum amount of support components possible by design, and only capable of reaching their ratings when placed in a constant airflow (such as, you know, the draft of a propeller), and are rated to just under the peak power handling capabilities of the semiconductors. One of the major themes I'll hit on later is that you must derate everything . The ratings given for aircraft parts, especially cheap ones, are generally unrealistic for EV use.
Even worse is the fact that the average aircraft lithium ion pack doesn't have a hard shell. Lipo batteries are little squishy bags of volatile electrolytes and active alkali metals. I don't know who's great idea it was to make a battery without a shell, but the abuse of a vehicle dictates that batteries must be properly mounted and proofed from shock, impacts, and weather. It makes me cringe a little even recommending using lithium batteries to the public because of those reasons.
You've been warned.
Overall, though, I think my point is clear: R/C model aircraft components are a good economical choice for those looking to begin experimenting with electric vehicle technology . It may not be the best solution for someone looking for a reliable, maintenance-free, long-life commuting vehicle. Many R/C components are definitely not manufactured to vehicle specifications and may fail or become finicky over a period of time. There are definitely commercial EV solutions available which are even plug-and-play - but I'm assuming if you are reading this, you have a little sense of adventure.
Step 2: A Typical Brushless Outrunner
The dominant type of motor found in the aeromodelling world today is called the outrunner motor. The first image shows literally the first result I got when I searched "outrunner" on Google Images, and is pretty damn representative of most of them.
Mounting the Outrunner
So the cool thing about outrunners if the name didn't give it away already is that the outer case of the motor is the part that spins . In the first image, only the faceplate of the motor - the part the wires exit through - is stationary, and that is the part which gets mounted to something solid. Otherwise, the entire rest of the shiny gold and silver bell spins. This tends to render the motor unsuitable for conventional "DC" mounting styles like clamp mounting or double-supported mounting. The idea of the outrunner in aeromodelling is that you can directly mount a propeller to that rotor bell end.
However, for EV usage, mounting a sprocket, pulley, or wheel directly to the motor in this fashion is a bad idea . The reason is shown in the diagram in image 2. The bell shaft bearing is effectively cantilevered, which means a strong side load (like tensioning your chain or belt, or a wheel load) can bend yourwhole motor . The longer the motor case, the worse this effect is. Instead, all but the tiniest motors also hang the shaft out the other side of the motor, so it can be conventionally mounted and used. This is the end you would want to mount a radial loading component like a sprocket on - sprockets and belt pulleys, or gears for that matter, can often by purchased stock with the right bore size.
Reading the Outrunner
Outrunners are typically given a numerical designation similar to
AA-BB-C(Y/D)
There's two overlapping, almost indistinguishable, and sort of conflicting systems about what the letters mean.
First is the stator-referenced system. In this system:
1. The first number AA indicates the stator diameter in millimeters. This is the active component in a motor which generates all the torque, so this is akin to selling cars by engine displacement.
2. The second number BB indicates the stator length (stack height), or the length of the magnets.
3. The third number C may be a low number (single digits to 20s), indicating the number of wire turns per stator pole. If it is a high number (high tens to hundreds) it is the motor's "Kv" constant, or voltage constant in RPMs / V
4. An optional Y or D means the windings are terminated Y or Delta - for the same TURN COUNT, Y-terminated motors rotate slower and with more torque for the same current draw, but need a higher voltage to achieve said current draw. It's a design tradeoff, but the vast majority of R/C outrunners are Delta terminated for convenience.
The second is the motor-referenced system, more common for inexpensive motors, in what I can only assume is a ploy to amplify the apparent size of the motor.
1. The first number AA now refers to the total diameter of the motor, in millimeters.
2. The second number BB is the total length of the motor case, from front to back, minus the shaft.
The third and fourth numbers typically remain the same.
...
So how do you tell which one is which? If its not explicitly given to you as stator diameter , it is probably the latter system. The most definitive way to tell is if you have both data points - stator and outer diameters. A list of typical stator-to-motor diameter cross correlations for typical vehicle-sized motors is given below:
42 to 45mm stator > 50 to 55mm motor case
50 to 52mm stator > 63 to 65mm motor case
68 to 70mm stator > 80 to 85mm motor case
Sizing the Outrunner
Most electric scooters will find a motor in the 60mm (motor) diameter class more than sufficient. A good seller will give at least two important specifications which you can use to determine rudimentary drivetrain parameters.
1. The Kv rating is how fast the motor will spin per applied volt. Conversely, it is how many volts the motor will generate across its terminals if you spin it . This is largely a remnant of the DC motor days when you could dump your motor on a battery and it will spin. Electronic controllers, such as BLDC controllers, can actually vary this parameter of the motor significantly, so the Kv is just a rule of thumb unless you are a motor engineer .
You can use the Kv rating in RPM/V, your system voltage, your anticipated drive ratio from motor to wheel (x to 1), and wheel diameter (in inches). to calculate a theoretical top speed for the vehicle. This is a purely theoretical number in an ideal, frictionless world. The equation goes
Speed (mph) = [( RPM/V * System voltage ) / (Gear ratio )] * (Diameter * pi ) * (60 minutes per hour / 12 inches per foot) / (5280 feet per mile)
A cool little resource that does all this for you and even provides you with acceleration and battery figures is the Tentacle Torque and Amp Hour calculator , written for the combat robot community by the late Steve Judd, a long time Battlebots and robot combat competitor. The website is still maintained as a resource for robot builders. As expected, it's very "robot oriented", but to use it for vehicle calculations, just plug in your own motor statistics (or take a best guess), and use 0.5 motors per side if you have single motor drive. Note that "Average % of Peak Drain " should be turned down to 5% or 10% for EV usage - that is the amount of time you spend doing burnouts or launching from standstill. A database of cataloged motors exists for sanity checking.
If you only have a KV rating, then the only thing you can estimate is the top speed.
2. The internal resistance of the motor, also known as winding resistance, terminal resistance, etc. It will generally be a low number (less than 1) ohms . Given this value and your system voltage, you can calculate the maximum current draw the system can theoretically see based on Ohm's Law, I = V / R . Real current draw will be less (but not much less) than this value due to the inherent resistance of copper wire, semiconductors, switch contacts, etc. But again, a ballpark figure.
Additionally, as described in my just-build-your-own-damned-motor-already writeup , given the Kv of a motor in RPM / V, you can also find the torque produced per amp of current draw. RPM/V is not a SI unit, but a little math will get you to the SI definition of an electric motor's voltage constant, V / (rad/s) ; that is, volts per (radian per second). In short, the voltage constant in V / rad/s is also the torque constant in Nm / A, or newton-meters per ampere .
If you're that inclined, Nm/A can be directly back-converted into ft-lb/A or in-oz/A, as they are all units of torque.
Therefore, if you know the IR of the motor, and your system voltage, you can find a theoretical peak torque value for the system, which is useful for calculating maximum accelerations: Torque (Nm) = (Nm/A ) * (System Voltage / Motor Resistance ). This number is, indeed, very theoretical. I'll address special considerations for R/C motors near stall in a little while.
More Sizing of the Outrunner
Some times, you will also see a power rating - usually in the hundreds or thousands of watts. It's important to remember here that the value given will almost invariably be power input - that is, the power your battery is feeding into the motor. If you are familiar with DC motor principles, you know that the motor can only ever deliver 50% of this value back out as mechanical output power - torque times speed. (If you're not, read this ). And that's if it's a ideal motor - at this operating point, 50% or more of the input power is being dissipated as heat. Essentially, the "power rating" figure is not very helpful, since if the motor is operated at anywhere near half of the figure, it will quickly overheat.
Ultimately, the way to size a motor by power is to roughly calculate your total drag force using the Drag Equation, and assuming Cd is about 1.0 (for a person standing up and moving forward), and multiply that by your desired cruising speed - in SI units, the result is the power the motor needs to output to keep you going at that speed. In other words, Pmotor in watts = (Drag Force in newtons * Cruising Velocity in meters per second).
As a rule of thumb, this should be less than 15% of the maximum motor input power.
Why not an Inrunner?
An "inrunner" is the back-constructed word for a conventional brushless motor. In the aircraft domain, they are much less suited to vehicle propulsion because they spin significantly faster i.e. have very high Kv values. Subsequently, they require much more geardown to achieve the same torque levels. While inrunner drives are definitely possible, the added mechanical complexity is suboptimal. However, they're definitely easier to mount and less susceptible to getting dirt and road junk in the motor.
Step 3: Buy an Outrunner!
HobbyKing!!
Anyone who recognized the motors in all the previous pictures will know exactly where they came from. In 2007, HK was just another random East Asian hobby store peddling shady equipment, and they were not exactly known for quality. Now, HobbyKing has pretty much taken over the entire modelling universe.
For ease of reference, I've been using the term "ICBM" to refer to Hobbyking motors - not ICBM as the military uses the word, but I nexpensive C hinese B rushless M otor. Yeah, you can tell people your scooter is ICBM powered. They have several house brands for their equipment, of which Turnigy is just one. Last time I checked, they have 42 pages of outrunners.
Now, most of those are still very small, but the sheer volume makes finding good motor candidates hard. This is why I have chosen to point out specific candidates which I have used, seen used, or recommended to people. If you want to hunt there on your own, I would stick to the "Large Motors " category - since the rest range in size from fingernail sized to something like a small guava.
Update July 2012: As of May or June of 2012, most of these large motors are no longer sold by Hobbyking. Maybe they figured out that nobody actually uses them for planes! The information below should therefore be used strictly as reference for selecting motors from other vendors as a result.
The same motors are still sold under the "EMP" brand by places such as Leader Hobby and other smaller overseas retailers.
- An example of the "EMP" 63/74 motor
- An example of the "EMP" 80/100 motor.
Hobbyking's replacement for these motors seems to be their own in-house designed "SK3" series. The SK3 63xx motors are very much equivalent to the older type, but they are actually slightly smaller in dimensions with the 63xx series being actually 59mm diameter. They also have slightly higher internal resistance (but still very low - we're talking like 40 milliohms over 30 and similar scales).
When selecting a motor, remember that ones with skirt bearings (explained below) tend to be more durable than ones without.
End Update
1. The Turnigy 60mm class motor (63-54 through 63-74) Example
Shown in image 1, these motors are good to about 1 horsepower output, which is more than reasonable. They're about 2.5" in diameter and have a 10mm shaft. These and similar 60mm class motors have been used to great success with 6" pneumatic tires in a scooter-building class section hosted at MIT, and on many e-scooter conversions like Jerome's and the EVPlasmaman scooter.. They have a modest Kv (200 to 280) and peak current draws of 50 to 60 amps.
The Turnigy 60mm motors would make for a more than reasonable cruising vehicle with a very low profile, and is the motor I'd recommend to anyone who thinks of asking me what motor they need (because clearly you don't need any bigger).
The reason I picked that motor line over the other HK lines is their use of askirt bearing / can bearing, which makes the motor more durable overall. Historically, these motors have been known to ditch magnets while at speed, resulting in pretty instant destruction. The addition of the can bearing in the latest iteration eliminates the high speed vibration that could break magnets free.
The 63-64 is the motor that is behind Fanscooter .
2. The Turnigy 80mm class motor (80-85 and 80-100). Example
This is my choice of weaponry for attacking the open road. These motors are almost absurdly powerful and torquey, and can output up to 3 horsepower. These would be better suited to a serious moped , road-going motor scooter, or full fledged electric bicycle conversion. They are easily capable of drawing over 100 amps, so a substantial controller will be needed - no current "cheap" model airplane controller can actually handle them reliable due to the very low resistance of the motor and subsequent high current draw
That said, my Melon Scooter (so named because of the melon-sized motor) runs one of these on 40 volts, and is very conservatively geared to reach 25 miles per hour in just a few seconds. The gearing is more to save the controller and my life than anything - power conservation shows a top speed of more like 50mph.
The 80-100 comes in two Kv flavors - 130 and 180 RPM/V.
3. The Turnigy Are You Serious, Hobbyking?120mm class motor
I'm only including this for novelty sakes, because I have yet to conceive of a vehicle short of an e-bike or e-trike that can hit U.S. highway speeds that can use this motor to full potential. Maybe two of them on a real electric motorcycle?
Seriously, what do you fly with those things? Why don't you just get in the airplane and fly it yourself at that point?
This motor will need a legitimate EV traction controller for vehicular purposes. The highest current model aircraft controllers by Castle Creations, JETI, and other "legit" companies, in the 48 volt and 300 amp range , cost close to (or more than) that of a real vehicle controller anyway, so making the jump is a reasonable thing to do. And the EV controllers offer more specialized features that... you know, a vehicle would find useful, such as variable regenerative braking, torque control (close to the dynamics of a gas engined vehicle), and accessory lighting integration.
Controller choices are a forthcoming topic, so stay tuned.
AXi, Hacker, and other "Legit" Brands
Before Hobbyking et. al. unleashed a sea of ICBM s upon the world, large outrunners were exclusively the domain of European manufacturers. I'm not going to talk too much about them, since if you already have one of them you'd know their power capabilities, but the AXi 5300 series and Hacker A50 and A60 are motors in the same power class as the HK 60mm motors described above, and would work just as well in the application.
Shop around
Those three are definitely not the only possible choices by far, but they were included because I have a pretty long history with them and know them well, among other reasons mentioned above. Hobbyking is also not the only dealer of BLDC motors, but they, in accordance with my justification at the beginning, seem to have the best price to performance ratio so far.
Step 4: Controlling the Outrunner: Sensorless or Sensored?
Unlike a regular old DC motor, brushless motors require an electronic controller to commutate the motor. The methods by which they do this differ, but it commonly boils down to whether or not the motor has Hall Effect sensors placed strategically in the windings to sense the magnet rotor's position so the controller knows which coils to switch. Other strategies include position encoder wheels, but the Hall sensor is by far the most prevalent in small motors.
The vast majority of model motors are sensorless
That's the first rule to keep in mind. Because the load experienced by an aircraft increases predictably with speed, and is zero at zero speed, pretty much all aircraft motors (especially outrunners) are just spinning rings of magnets on a stick. That is why they can be made so cheaply. Industrial motors for general motion control like servo systems and robots and whatnot need to deal with constantly varying and transient loads, so they therefore have some kind of feedback built in already.
Usually, the only model motors that come with sensors built in are small R/C car and truck motors like this .
Sensored control, the fundamental method
In a sensored motor (and associated controller), there are generally three sensors positioned at 120 or 60 electrical degrees apart in the motor that output a 3-bit Gray-like position code. The placement of these sensors depends on the winding configuration, number of slots, and number of magnet poles. For more information on how and why this works, see my hub motor instructable .
The advantage of sensored commutation is that the controller always knows where the motor is. Therefore, sensored motors usually have low-speed and stall characteristics more like a classic DC motor. Sensored commutation has its downsides - sensor failure or glitchiness could mean the motor controller stops running the motor. Most inexpensive industrial and commercial controllers, even EV controllers, are just governed by a state table whose input is the 3 Hall sensors, and so sensor failure would mean an erroneous output and non-running motor. There is also the issue of finding the correct combination of Hall sensor leads and motor phase outputs - up to 12 possible ways of matching them together, if your motor doesn't come with a controller.
Finicky details aside, sensored commutation is the way to achieve consistent stall- and low-speed behavior, and "real" vehicle controllers are usually sensor-commutated.
Sensorless control, i.e. R/C speed controllers
A sensorless controller has to detect the position of the rotor through some other means. The most common method is to randomly bump the motor (drive two phases) and observe the back-EMF, or generated voltage, profile on the third phase. The slope of the BEMF dictates which direction the motor moved in, and therefore which coils to switch next. Sensorless commutation uses more sophisticated position state estimators which have to have some speed feedback to "pick up". In other words, sensorless motors can't technically move without being already moving. This clearly poses a quandary for vehicles and other inertial loads. If the initial "bump" is not strong enough, the motor will not move enough to generate a meaningful voltage pulse.
For viscous loads like a propeller (load proportional to speed), this is not a problem at all. Therefore, the vast majority of R/C controllers are sensorless.
Sensored ones do exist - again, for cars and trucks, which as you might guess, are just like tiny versions of EVs you personally ride, an inertial load. Sensorless controls for cars and trucks are also commonplace, since modern motors are powerful enough that a pulse on the phases is enough to move a small model.
The biggest implication of sensorless control is the dubious availability of stall torque. This makes the torque equation presented two pages ago a little misleading. You will generally not be able to stand on a vehicle and challenge someone to a drag race. Sensorless vehicles, especially those using R/C parts, will need to be "kicked off" or push started .
Sensor Augmentation
The only real difference between a sensored motor an a sensorless motor is... sensors . You can actually take any common R/C outrunner and add Hall Effect sensors to use them with EV traction controllers. Numerous ways exist to append sensor feedback onto your motor: I cover installing sensors within the windings (inside the motor) on my hub motor Instructable; and here are twoways people have used externally mounted sensors. You would end up with an additional 5 wire harness coming out of the motor, comprising three Hall sensor outputs, logic power, and logic ground.
Hall sensors are typically "open collector" i.e. they can only sink current. Controllers have internal pull-up resistors built in, so there's generally no need to internally pull the Hall sensor output to the logic rail. However, power supply decoupling capacitors placed right at the Hall sensor leads seem to be helpful. The Hall cable should not be routed parallel or immediately next to the phase conductors, since the high switching currents in the phase wires can cause induced noise problems with the sensor cable.
Update June 2013: Outrunner Hall Sensor appendages
I hate to plug myself usually, but in the past few months, I've successfully developed and am currently selling a line of Hall Sensor Boards and Hall Sensor Mounts sized to several of the typical outrunner suspects. Placed externally, they allow a sensored-only motor controller to drive these motors. See the boards and mounts on Equals Zero Designs. I designed these specifically as a "stock solution" for everyone asking me how to add sensors to your outrunners!
Step 5: Special Mechanical Considerations for R/C Sensorless Control
Half of the point of this guide is me telling you to use R/C equipment in unintended ways, for better or worse. So I've compiled a list of guidelines that I have found to be helpful. These encompass both design and operation, so it's more of a state of mind to be in when you put together a vehicle using R/C components.
The more electrical cycles your controller sees, the faster it will lock in
AC motors (and brushless motors are technically AC - the details are inconsequential here) can have different ratios of electrical speed to mechanical speed. In the most basic 3 phase motor where there are 2 magnet poles and 3 stator slots (three coils, in other words), the electrical rotation speed is the same as the mechanical rotation speed. As the number of magnet pole pairs increases, so does the ratio of electrical speed to mechanical speed - in fact, one to one. A good animation of this principle can be found at the LRK site (the guys who made high pole count outrunners popular in the aeromodelling world)
It's important to note that a high pole count motor does not necessarily have more torque, but to a limit, the addition of slots and poles divides down the Kv value of the motor (and increased the torque produced per amp such that they no longer needed gearboxes to drive propellers. The angle the motor has to move between magnet-stator pole alignments is lesser, so it needs to be switched often to accomplish the same displacement.
However, because sensorless controllers depend on having a regular motor voltage waveform to "lock on" to, this can be advantageous. Gearing down the motor does two things. One of them, as stated, is the fact that the controller has to switch more in order to accomplish the same displacement. When coupled with vehicle mass and the motor's own rotational inertia, it tends to result in a smoother BEMF profile.
The header image is a picture of what a motor terminal voltage profile actually looks like when it's running.
The second effect is that...
Speed reduction also divides your inertia.
Remember when I said that aircraft propellers aren't inertial loads i.e. need nonzero torque to begin accelerating? To approximate that in a vehicle, you need to reduce your inertia as seen by the motor as much as possible. It can be shown that the apparent mass of a load as seen by the motor goes down as a factor of 1/ R^2 , where R is the speed reduction ratio (i.e. R to 1). You can already see that if you gear down a motor even around 8 or 10:1, you pretty much become nonexistent as far as it's concerned.
Therefore, sensorless drivetrains benefit from very high geardown ratios
It's important to note that no matter how far you gear your motor down, some amount of push starting is needed . It may be as little as the action of jumping on the vehicle that scoots it forward slightly, but with the possible exception of absurd limiting cases, you won't be able to just stand on it and hit the throttle. It may work, but the start will be unstable and jerky (a phenomenon in the R/C world known as "cogging") and causes high currents to be drawn. Extended attempts to launch from standstill can therefore cause quick ESC overheating and failure. So that means...
Don't floor it.
...unless the vehicle is already moving. Sensorless operation at low speed usually requires a steady finger and can be unstable. The controller may lose sync with the motor, which just means it switches the wrong phases at the wrong time. Sync loss can also occur if you're moving slowly and then suddenly increase the throttle command. Most controllers will assume the motor can spin up at some minimum angular acceleration - which, with your load on it, may not be true. This also results in sync loss.
Summary
Sensorless R/C controllers can result in a vehicle with unexpected (or just underwhelming) standstill and low-speed performance. Gear down a fast motor with a high ratio can alleviate this issue, so keep it as a design consideration when running drivetrain calculations.
Step 6: R/C Controller Examples and Usage
General Guidelines for Picking Generic ESCs
High voltage specification and Battery Elimination Circuit
The cutoff for when a controller is considered "High Voltage" seems to be around 6S lithium batteries, or around 24 volts. Below this voltage, controllers often come with linear regulated power supplies built into them which can power (in their intended application) a receiver and servo motors, called a BEC. This is handy for when you need to convert a throttle signal (more on that later), but the logic power supply is often not enough for things like lights. However, linear supplies work by burning off excess voltage - therefore they tend to run hot and the power dissipation is unacceptable for voltages much above 20 volts for most 5 and 3 volt regulators. Therefore, some controllers will advertise a "SBEC" or "UBEC", both designations for a switching regulator built-in. These types are usually more expensive for the same amp count.
Controllers designed for use at above 6S ltihium cells (8S-12S) are usually advertised specifically as High Voltage. These usually do not come with a BEC and the signal wire only exists to take inputs.
It is generally not recommended to operate a R/C controller anywhere near its maximum rated voltage. Due to cost cutting, components with breakdown and failure voltages just barely above the advertise threshold are often used - 25 volt capacitors and 30 volt power semiductors in a controller rated for 6S (22.2v nominal, 25v peak) are common. Power surges resulting from motor speed change can exceed those limits and cause rapid (fiery, smoky) controller failure. For EV systems, a HV type controller is most likely necessary unless you are intending to run an 18 volt system (5S lithium batteries or 15 nickel cells), which is actually just fine and workable - but less power than I would like.
Speaking of "rated", it's important that you...
Derate everything. No, seriously, everything .
A controller the size of a credit card will not actually flow 100 amps all day at 36 volts. The specifications given for aircraft controllers are generally a continuous operating current at maximum temperature of the components assuming a constant high speed airflow is present and there are no surges . In aircraft, this is expected since propellers and fans create high speed exhaust streams, and throttle is generally constant and unvarying during cruise. In a vehicle... not so much. In fact, the opposite is true. You might be tempted to stuff the controller into the frame, this eliminating the airflow cooling potential. And a vehicle is pretty much entirely a surge load. Most industrial controllers achieve their ratings using a continuous thermal equilibrium method too, but with no assumptions of cooling. Surge ratings are often a function of maximum acceptable semiconductor or circuit board trace temperature rise, or possibly a maximum voltage ripple specification. Things aren't that strict in the modelling world.
Given no airflow (convection-only cooling), it's wise to derate the "continuous" amps by at least 3 to 5 times and the maximum current, usually given as no more than a few amps above the "continuous" rating, by 25% to 50% (i.e. reducing 100 amps to 75 or 50). If you can build in active cooling, such as a fan or waterblock, you are much better off. However, I'd still derate continuous amp draw by 40% or more (i.e. a 100A controller is a 50-60A controller).
Peak demand on acceleration can of course exceed this maximum, and the more frequent the excursion the closer to the lower end of the derate is necessary. Frequent start-stop driving in a city environment would warrant more derating, cruising along a trail or roadside less. It depends on the application, but current capacity must be derated as part of design.
Soft-Start and other special features are useless
Many ESCs come advertised with a 'soft start' feature. What that does is reduce the amount of current the controller delivers to the motor upon startup, such that your airplane doesn't start spinning instead of the propeller. However, we're not driving propellers with this, and therefore all the soft start does is make the vehicle more likely to cog and rattle on startup. Lower current means lower force to overcome inertia. You must check the calibration settings to make sure it is turned off.
Another common feature is speed governor mode, commonly used for R/C helicopters which keep the rotor speed constant but vary thrust by changing the blade pitch. Speed Governer mode sets an internal control loop that links motor speed with throttle position. While this may sound like what an ESC should be doing in the first place, the default most is in fact open loop - if you set a certain throttle, and then grab the motor and apply load, the controller does not try to compensate for the extra load, and the motor slows down. With governor mode on, the controller actively ramps up the power applied to the motor to try and keep the speed constant.
I imagine this would function kind of like eternal cruise control on a vehicle, but I have never experimented with Governor mode on my own. Sudden changes in speed command with a closed loop control are liable to cause current surges no matter if the command difference is large or small, in my opinion, and it should be avoided.
Timing is important
While the technical explanation is mostly out of the scope of this Instructable, you will also see things like 7.5, 15, 22.5, 30 degree, etc. adjustable timing on the controllers. This part is important: timing refers to how soon the controller switches to the next motor state in relation to the magnet rotor position. This affects the current draw and torque production of the motor at high speeds. The simple technical reason is that winding inductance causes slow current switching in the motor coils, and at high speeds, the stator magnetic field generated by the windings falls behind the magnet rotor position, causing reduced torque and wasted power since all of it isn't going to producing torque any more.
For outrunner motors especially, high timing is crucial. The massive iron cores in most outrunners have lots of inductance, and on most product pages they will even warn you to use "high timing" for outrunners.
By the way, adjusting this timing advance on-the-fly using current and rotor position feedback such that the motor always produces maximum torque is called field oriented control or vector drive .
If it looks alike, it's probably alike.
Most "cheap" Chinese ESCs descend from a few original bloodlines and are knockoffs of eachother. It's some times amusing to watch emergent strains that combine features of other controllers into one, and Hobbyking is a veritable tropical rainforest of a controller ecosystem. Since most of these controllers are made by a few houses and just colored differently depending on the contractor or distributor, one behaves much like another for non-HV types. The difference between one LV 80 amp controller and another on Hobbyking are probably minimal to literally none. HV designs are more varied, however, so this guideline doesn't really apply for them.
Controller Examples
So now I will introduce some of the common aeromodelling controllers I have seen or have personally used in vehicle builds. Most manufacturers and distributors will explicitly warn you against using their controllers on vehicles, since as mentioned before, vehicle loads and propeller loads are vastly different and the software written for one is suboptimal for use on the other. So I guess I should really say that you should not use airplane controllers on any kind of passenger-carrying ground vehicle.
...
Now then, onto my personal favorite for these kind of things, brought to you once more by Hobbking:
Turnigy Sentilon 100A HV
Pictured in the lead image for this page, this controller has some of the best low-speed stability (lack of cogging) I have seen. It seems to be a Hobbyking exclusive version of a HobbyWing (watch those letters) OEM design , which seems to be a possibly grey market evolution of the Jeti Spin Opto 99 . For an airplane controller, it seems to be rather primitive and limited in configuration options; but this is what makes it well-suited to being a vehicle controller. This is the controller I have run in melon scooter and several of my hub motor scooters in the past.
This thing can actually sustain 90 to 100 amps in strong airflow (having been tested on a ducted fan experiment of mine), but in vehicle usage with convection cooling I would try to make cruise current no more than 30 amps and keep peak currents under 100 amps. The second image shows what happens when you try to pass 140 amps through it for 5 seconds. However, otherwise, at a dollar per amp, it's quite economical for powering vehicles in the 1 to 2kW range.
Castle Creations Phoenix HV 110
Castle is a long-time manufacturer of model controllers whose products have also seen extensive usage in small EV conversion. The Phoenix series has the reputation within the electric bicycle community of starting and running just about anything - meaning its estimation algorithm is robust and can handle faulty or poorly wound motors. I haven't personally used the Phoenix line since they are much more expensive, but Jerome's scooter uses a Phoenix 60 with a 50mm type outrunner. Being a reputable brand in the R/C community, I would expect their ratings to be closer to the truth.
Larger Sensorless Controllers
There are indeed much larger sensorless controllers, up to 200 and 300 amps capacity. However, while I will list them, I will not recommend them - this amount of power should be handled by a real vehicle controller, which can pay attention to how much current it is passing (R/C controllers do not actually measure and control current draw), and have more robust designs, more failsafes, and vehicle-related features. The "legit" brands are getting close to, or exceeding, the cost of a vehicle controller for the same number of amps anyway!
The Turnigy Monster 2000 seems to have had a first-generation spontaneous combustion problem, but more recent reviews are positive.
The JETI Spin 200 and 300 are some of the best model ESCs available, and are ungodly expensive as a result.
If you want even more extravagance, Schulze is like the Armani Exchange or something of the R/C world, and they have 300 to 400 amp designs . Their controllers also feature options like full datalogging and sensored commutation (but if you want sensors, there are better options... read on!)
Update November 2013: I've added some more controllers to this list; ones that I've used, have, examined, or otherwise have messed with.
Trackstar 200A 8S 1/5 Scale
This humongous thing is the subject of a full teardown on my website. It has ultra-low resistance, a ground-vehicle optimized starting routine, and active fan cooling. Based on the semiconductor count and thermal design, I think this can push 70-80 amps in a vehicle application, and definitely nameplate for acceleration. I'll have more to say about this once I have it on one of my own devices, but for 50 cents per (nominal) amp with actual robust construction, it's most likely legit.
dLux 160A HV
This line from Hobbyking seems to be a derivative of the Castle series below. They have a double sided heat sink (and the FETs on both sides to use them). I paired one of these with a 50-60 type outrunner, and two of that combo push around my go-kart BurnoutChibi with no problems. Based on examining their power devices and board layout, I think these are suitable for 25-30 amp continuous current draws in a vehicle application, with short bursts up to nameplate. There are "shorter" versions of it with 120 and 80 amp nameplate ratings, but I'd say the overhead is worthwhile since this is an air ESC and the starting algorithm is basic.
Generic "200A" Suppo-type controllers
These are marketed under various brand names with slight variations - I took apart no less than 4 of them in the same post that I investigate the Trackstar 200A. I both love and hate these, because there's some things about them that are nice but most things about them are disappointing. The nice things:
- They are extremely simple and basic programming and intelligence-wise
- The number of devices in parallel make for good burst and acceleration current overhead, from sheer thermal mass
- The three stacked layers of FETs mean that there is extremely poor cooling no matter how hard you fan it - only the top layer receives significant cooling. You'd need to unshell the controller and fan it directly, and even then the center "core" is likely to remain hot.
- The heat sink often is installed incorrectly and might cause phase-to-phase shorts as they contact the output wires
- They're low voltage, relying on paralleling many shady or off-brand semiconductors to achieve the current rating, and the switching time is long, so they switch inefficiently.
Types to watch out for
I only have two data points as of right now based on personal experience for controllers to absolutely avoid: The "K-force" series from Hobbyking and the "Super Brain" are all very smart (read: specialized) controllers which implicitly perform soft-starting and locked rotor detection. They will treat almost all low speed loading as a stall condition and shut down. As outlined above, controllers that are too smart aren't well suited to running vehicles.
Step 7: R/C Controller Communication and Signalling
Because R/C controllers take as an input the hobby industry "standard" servo pulse, you cannot just communicate with it using a 3-wire potentiometer. A signal conversion must take place, and it can either be done in hardware or in software.
The lead image is a graphic of a typical "servo command" pulse-width pulse: 1500 microseconds is a neutral or zero speed signal, 1000 microseconds usually full power one way, and 2000 full power the other. While servos and robot controllers respond to the pulse durations as indicated, a typical airplane controller is unidirectional. The most common "default" is 1000uS as zero speed and 2000uS as full speed, or something resembling that range. Of course, the ESCs can be recalibrated to accept different endpoints at will, so this distinction is mostly inconsequential.
A Simple "Servo Tester" is Your Friend
A vehicle throttle is basically a knob you turn to generate a signal to something which controls how fast the vehicle goes. In gas engined vehicles, this knob might literally have pulled on the engine's throttle body, but generally these days it's an electronic signal to the engine computer.
In the hobby world, there exists a small device that is sold commercially which does precisely the task of converting a knob motion to "servo" pulses, and it's called a servo tester . An example is shown in picture 2; this one in particular . They are used in lieu of setting up a whole radio and receiver just to make sure your servos work. Notice that one (and most cheap ones sold today) have three outputs - this lets you test all 3 servos in a helicopter main rotor simultaneously. You only need to use one.
The cool part about most servo testers is that you can directly drop a 0-5v source, such as a 3-wire potentiometer or commercial vehicle throttle, into the place of the knob (which itself is a potentiometer). The 3rd image shows a conversion I have done to that particular servo tester model - the 3 pin connector goes to a commercial hand throttle (more on those parts in a bit). After this stage is complete, you have a direct analog voltage to servo pulse converter that can be installed in a vehicle.
Note that these come with different modes available such as "neutral", useful for keeping your servo centered while you adjust linkages, and "sweep", which automatically does a full 1000-2000uS sweep. These modes are not useful, and if accidentally selected during operation, can result in bad . It is recommend to remove the button which selects the modes.
Full hardware method
If you love torturing yourself, you can build a 100% hardware (i.e. resistors, linear integrated circuits, caps) timing circuit that will convert a 0-5v reference to the appropriate servo pulse. I link to a few in the older edition, but these days, you have no excuse to use a full hardware servo tester given that they cost like 5 cents. Hardware component values change with temperature and even humidity, and there are more parts, leaving them more prone to failure.
Throttle ramping
Because sensorless R/C controllers can't really control how much current they send to the motor (and current is directly proportional to torque output), and low-speed starting can be erratic and hard to control, it is useful to have a "ramp" somewhere in the throttle chain. Without ramping or some other kind of control input damping, sudden jerk motions of your hand or foot can result in the vehicle responding unexpectedly such as a sudden application of power. This is not only hard to operate, but it can be outright dangerous if you are in traffic or around other people.
Ramping can be accomplished either in hardware or in software.
Hardware resistor-capacitor filter
In the fourth image is a "RC filter" type circuit, where RC is resistor-capacitor , which smooths out sharp transients in the control input. The general form of the circuit is known as a low pass filter, and its technical details will not be discussed (Wikipedia can provide a better treatment than I ever can). The values of your choice of R and C determine the damping "time constant", and that's just given by Trise = R * C .
No, really, that's it. So in the example, a 100K resistor and a 10uF capacitor together form a filter which has a rise time of 1 second - meaning if you floor it from standstill (like you shouldn't be doing anyway, right? ) the control signal takes 1 second to reach 63% (the defined standard threshold for this circuit). True settling time is defined as the time it takes for the output to reach over 90% of the final value, and is generally accepted to be 3 time constants (3 * T). You may adjust the R and C values to achieve however fast a filter you want.
It is important that the resistor is of significantly higher (at least 10 times) value than the throttle potentiometer, and should be at least 10K ohms. The reason is that if the resistor is too close to the pot's total resistance, the potentiometer affects the filter's time constant strongly. I put 100K as an example, but with most vehicle throttles being 5K ohm resistors, try to use at least a 47K resistor. The capacitor can be any polarized or nonpolarized type, but if it's polarized, please put it in straight. The whole circuit can be soldered inline with a throttle harness.
The second variant of this circuit adds a one-way bypass to the system such that throttling down is unramped - meaning if you let go from full throttle, it doesn't take a full second for the throttle signal to slowly come back down, it will do so almost instantly . The diode conducts if the input voltage on the potentiometer side is lower than the capacitor's voltage (which is the output), so it effectively shunts input to output for those positions.
In software using a microcontroller
Ramping is also achievable in software if you're making your own servo tester-like device anyway. For instance, the following Arduino code implements ramping by taking a R/C pulse in on one digital pin and spitting it back out on another. This was written by Arduino and motor control master Shane Colton .
#include <Servo.h>
#define THR_MIN 178
#define THR_MAX 870
#define PWM_MIN 1000
#define PWM_MAX 2000
#define SPEED_LIMIT 0.33 // fraction of full speed
#define RAMP_LIMIT 0.13 // fraction of full speed per second
Servo tgypwm;
float pwm_f = (float) PWM_MIN;
void setup()
{
pinMode(9, OUTPUT);
tgypwm.attach(9);
/*tgypwm.writeMicroseconds(PWM_MAX);
delay(5000);
*/
tgypwm.writeMicroseconds(PWM_MIN);
delay(5000);
Serial.begin(9600);
}
void loop()
{
signed int thr = THR_MIN;
float thr_f = (float) thr;
float pwm_target = (float) PWM_MIN;
unsigned int pwm_i = PWM_MIN;;
thr = analogRead(7);
thr_f = (float)(thr - THR_MIN) / (float)(THR_MAX - THR_MIN);
pwm_target = thr_f * SPEED_LIMIT * (float)(PWM_MAX - PWM_MIN) + (float) PWM_MIN;
if(pwm_target > pwm_f)
{
pwm_f += RAMP_LIMIT * (float)(PWM_MAX - PWM_MIN) * 0.05;
}
else
{
pwm_f = pwm_target;
}
pwm_i = (unsigned int) pwm_f;
tgypwm.writeMicroseconds(pwm_i);
Serial.println(pwm_f);
delay(50);
}
Step 8: How About a Real Vehicle Controller?
But there are such things in the world as inexpensive brushless motor controllers which aren't rudimentary and lightly built. They don't need a weird throttle converter, instead being able to use a 3-wire voltage source directly as the command. They tend to have real current (torque) control, variable electronic braking, and some times come with useful accessories such as a main relay driver or light controllers. It's like they were built for vehicles or something.
Luckily, in the past two or three years, specialized small EV controllers have become very common and also inexpensive. Here's some general characteristics about them.
They are sensored controllers
Positive starting from zero throttle and no desynchronization from control inputs too fast to follow. Then downside is that you'll have to add sensors to your motor if it doesn't have them already.
Current control and regenerative braking
A brushless motor's inverter circuit is implicitly capable of performing regenerative braking - where kinetic energy is capture from the motor and returned to the battery. There is nothing magic about regen , despite it being a marketing tagline for all sorts of consumer electric accessories (and cars). Regen is not available on most R/C controllers just out of cost reasons and no real necessity. While regen can only capture back a few % of the energy contained in a moving vehicle, it can contribute to longer brake life and less necessity to use mechanical braking to make a small speed adjustment.
Current control emulates the dynamics of a gas-powered vehicle better by keeping the acceleration constant. It also means the motor is limited from producing too much torque, which is handy for large brushless motors with very high torque capability.
Multiple inputs and outputs including reverse
Typically, an EV controller has at least two analog inputs: one for a throttle pedal or knob, and the other for a variable electric brake. It might also have inputs for throttle and brake switches which are tripped as soon as you step on either, and can signal to the controller that you indeed want to either go or stop (A single analog input cannot distinguish between you flooring it and a loose wire, possibly leading to dangerous situations). The brake switch would signal the controller to stop driving the motor because you want to stop instead. Maybe that's bad for doing burnouts, but it's not good to fight your brakes with your engine or motor anyway.
Other switches and doodads include key switch inputs, reverse inputs, status light outputs, datalogging, etc.
Better built
Because vehicle controllers have to be more rugged, they are generally built inside sturdy metal cases which also act as heat sinks for the power semiconductors.
Common small EV controller examples
Like quite a few other situations in life, a Chinese company offers a solution for the entry-level and basic functionality seeker where American and European manufacturers could (or actually would) not. The undoubted champion of inexpensive small EV controllers is Kelly Controller . Back in 2007 and 2008, they were really shady... but things have improved alot there, apparently. Kelly's KBS line of brushless controllers has everything I just described up there and the typical price is about 2 dollars per amp... real amps . Not barely-on-the-edge-of-destruction amps.
Kelly KBS Series
These things are about the size of a 12oz drink can (except square) and the chunkiest model can process up to 7Kw (72v, 100A) peak and 3-4 kW average. The one I've had the pleasure of dealing with the most is the KBS36051 , which is a 20/50 amp type. I've found that 20 amps is a little sluggish for most vehicles, but that doesn't mean you can make fun go-karts using them.
If you want more power, the KBL type goes up to 500-600 amps and 120+ volts. Now that's getting into electric car domain, so I'm actually not going to recommend them to small EV builders. They are also legitimately the size of a house brick or more.
Kelly controllers can be extensively calibrated using the the shady visual basic application they come with and a USB-to-Serial dongle.
Shady Electric Bike Controllers
These some times pop up on eBay for $50 to $200. They function kind of like Kelly controllers, but are more rudimentary, not calibration-enabled, and were often produced for a specific model of electric bike sold in Asia. They come in fixed voltage and current ratings (and are internally current limited to that fixed amount).
I have no specific product page link for these things, and the actual wiring harness changes depending on the model you get. They're made in nameless factories throughout southern China and have no brand name attached. There are definitely several "bloodlines" of them, and they might even warrant an entire Instructable on what the hell they actually are. I can only recommend going to eBay and searching "brushless e-bike controller " to see what I mean.
Because of the indeterminate wiring conventions, I can't recommend these to complete beginners, but if you have been hacking around with EVs for a while, they are great starting foundations for modding controllers. Speaking of which...
Community-modified Shady Electric Bike Controllers
There is a large community of electric bicycle builders who have spent some time reverse engineering those controllers and are now selling upgraded versions of them as kits or whole modules. The largest concentration of these users are at the Endless Sphere Technology forums.
*NEW*January 2012Sensorless E-bike controllers, a.k.a "Jasontroller"
As I recently discovered, there are several nameless e-bike controllers which can run fully sensorless. They are my current recommended small EV control solution because their sensorless startup and run algorithm is optimized for vehicles, which are inertial loads (as covered before). Instead of forcing the motor to start by dead-reckoning a minimum frequency, which would mean jerking your vehicle to several mph, these controllers ramp up to speed in startup mode. While the "ramping" takes less than a second, the effect is very pronounced and different from R/C controllers - the launch is smooth and generally seamless and without "cogging" or pole slipping. Being generic e-bike controllers, they also feature current limiting and a variety of different brake inputs. The only downside so far is that they do not perform regenerative braking...and they're kind of big.
As the only place I have found which retails these controllers is eBay, I can only link to confirmed sellers and general search terms. They are usually advertised directly as "Sensorless", or in some amusing roundabout way as "Without Hall". Current, bobzhangxu is the only seller which clearly advertises some of the controllers in his store as sensorless capable. The controllers I have investigated personally are retailed by him.
I have performed a full teardown and inspection of a "350W" type in this site post (and the next several posts show integration into some of my vehicles, including the hub motored RazEr and the titular Melonscooter). I like these things alot now, since fiddling with proper Hall sensor timing is both critical and very much a pain unless you have an adjustable sensor mount. The nice things about them are:
- They're sensorless. Not like crappy R/C airplane sensorless, but actually optimized with ramping functions for inertial loads.
- Cycle-by-cycle current limiting, so they are fairly robust. Like their sensor-only brethren, this current limit can be violated and messed with in multiple ways, including bypassing the current-sense shunt or changing the MOSFETs out.
- They are fairly large. Even the 350W is the size of an average single-serving juice carton or so, much bigger by volume than an R/C controller, but still smaller than a Kelly.
- They're not that power-dense or robustly designed. Low cost means cheap components and modest over-rating ability. The circuitry is fairly generic, the gate drive is discrete and made of really cheap small transistors, and almost everything is thru-hole or large surface mount packaged.
Being sensorless and not particularly high performance, they like motors with a reasonable winding resistance and inductance - something R/C motors are not known for. I've killed some by accidentally powering the motor with the drivetrain locked or restrained, and the resulting massive fast current spikes overcome the in-built protection and seem to destroy the gate drive circuitry. They seem to have some trouble starting up large airplane motors such as the melon (as-tested on melonscooter),so I would recommend them on the 60mm type motors at most. Else, you may elect to rewind your motor to a reasonable BEMF constant. They're designed with bike wheel hub motors in mind, which have many poles, are slow, and usually high resistance and inductance - a case proven by testing these on RazEr.
Finally, they have a commutation frequency limit. This is a point where the ESC can no longer keep up with the motor, and as a result could lost synchronization and draw huge current spikes. While airplane ESCs, with their simpler commutation dead-reckoning scheme, can usually commutate up to 3000+ electrical Hz (maximum speed of switching the phase outputs from one motor state to another - this has nothing to do with the PWM frequency), the Jasontrollers seem to be limited to only 500 electrical Hz or so. To convert eHz to mechanical RPM, divide by the motor magnet pole pair count, then multiply by 60. This implies that for an average 14 pole outrunner, the highest attainable motor speed should be no more than about 4,700 RPM. Again, this implies that they were built to drive bike hub motors. If you want to utilize these controllers effectively, you should make sure your motor doesn't regularly go over 4,700 RPM, which with a fast and high Kv airplane motor, could prove difficult.
*New!* June 2013: "Miniature" e-bike controllers
These controllers seem to be in the same family as the Jasontroller above, but they are substantially smaller. I purchased these from eLifeBike and performed a teardown on my website as usual. The smaller size, especially when uncased, means it can be stuffed into smaller and more portable vehicles! Their behavior, including the unwillingness to play with low-turn R/C motors and top speed limit, mimics the Jasontroller.
Summary
When you're ready to make the jump from super hacked and rudimentary to something more legitimate, a real EV controller is the way to go. Kelly is generally the most well-documented and supported mass production upgrade path, but there are options worth experimenting with if you want to go out on a limb and learn something about how motor controllers work.
Step 9: Batteries: the Good, the Bad, the Ugly, and the Cheap
While battery technology hasn't quite gathered enough punch to take on the automotive market, modern batteries are perfectly capable of powering personal electric vehicles. The focus of this Instructable will now shift to giving a brief overview of the types of battery technologies easily available to a builder, where to get them, how to charge maintain them, and most importantly, how not to use them. The primary topic will be lithium ion batteries of various types. Most of the details on battery types is better gleaned from the likes of Wikipedia, so I won't go into too much quantitative analysis.
Forget about lead and nickel.
Still the most common in small electric vehicles you can buy just because they're cheap (and heavy... does that make them the Chevy cars of the battery world?), there is absolutely no reason in my mind for staying with lead-acid batteries today. There's almost no point to building a light personal vehicle if it's going to be weighed down by 50 pounds of lead. Typical small 7 to 18 amp-hour SLAs have poor cycle life when used in vehicle situations, becoming unable to retain more than 80% of capacity in as little as 300 charge discharge cycles.
Lead-acid batteries are more suited to long-term backup power provision...which is incidentally exactly what they're used for the most these days. Hint: Backup power systems usually don't move around.
The upside is that they're pretty damn easy to charge, and lead chargers are very cheap.
If you want to kick it old school, nickel cells are still a strong contender for personal EV use. They have 30-60% more storage capacity than lead and on a weight-for-weight basis can dump more watts (higher discharge ability) and charge faster. However, Ni cells are not the cheapest option any more - high capacity, low resistance cells are still expensive. A typical 4.2Ah, 1.2V nickel metal hydride cell can still cost $7 or more per cell, and you're going to need at least several dozen to make a useful pack. Many R/C vendors have completely droped Ni cells from their lineup, but places like Batteryspace (and any other of the front companies for shady Chinese battery vendors) will have them. Battlepack is a reputable dealer who has served the robot community for many years.
NiCd and NiMH cells are also very easy to charge and do not need battery maintenance systems, however.
Lithium is where it's at.
I had to think for a while before advocating publicly the use of lithium ion batteries, because it is rather easy to mess up with them. Along with the 100-150% higher energy density compared to lead-acids that lithium batteries offer, they also bring to the table less tolerance to over- and undervoltage, more propensity to enter thermal runaway when those conditions are reached, and the need for battery management systems or more careful charge monitoring.
However, they are also the most versatile and potentially cheapest option (oddly enough) for powering your vehicle. Here's a brief overview of the subtypes of Li batteries.
Lithium cobalt oxide, hard case cell (i.e. laptop batteries and their ilk)
These are the classic "lithium ion" battery, and are 3.6 volts nominal, 4.2 volts charging. The most common form factor is the 18650 cell which measures.... 18 millimeters across and 65mm long. Typical cells in this size have a capacity of 1.8 to 2.4 amp-hours today. I'm actually not going to focus on them too much, since you can generally only get loose cells (which need assembly) and they are also not built for high-rate discharge.
Lithium "polymer" soft pouch cell
I don't know whose idea it was to stuff a battery into a sandwich bag, but Lipolies are now the most common lithium battery around. They come in Cobalt Oxide and Manganese Oxide types, but the subtleties are negligible. The nominal voltage is 3.7 volts and 4.2 volts while charging. They are usually flat cells made in various rectangular shapes.
Lipolies are now the standard in the R/C world, a fact I will expand upon. They can be made to have incredibly high discharge and charge rate tolerance, and are generally close to the theoretical maximum 240 watt hours per kilogram possible with lithium ion batteries today. Because they're mass produced hobby parts, they are also cheap - possibly the cheapest battery option you can get. However, being soft-cased, they are easily damaged, and can become very dangerous if damaged mechanically or shorted out. Their high discharge capability is also a curse, since short circuits can easily turn into electrical fires fueled by hundreds of amps.
Lithium Nanophosphate (LiFePO4)
The latest heavily commercialized lithium battery technology is the LiNP battery, whose poster cell is the A123 26650 (by none other than MIT-affiliated A123Systems). The "nanophosphate" part refers to using lithium-transition-metal-phosphate nanoparticles as the cathode. The short story is much higher discharge and charge rate tolerance than a classic Li-Co cell and much less propensity of lighting on fire. The one downside is cost and somewhat reduced specific energy density.
If I had to name one reason why I would advocate LiFePO4 over everything else, it's the amount of abuse they can take for being lithium chemistry. While no battery is impervious to catching fire, overcharging an A123 cell is generally more palatable than an equivalent Lipoly cell - they tend to fizz and vent hot gas and electrolyte rather than shoot flames . There are certainly options for getting your LiFe packs premade, and I'll talk a bit about that.
LiFePO4 cells are 3.2 volts (or 3.3... I find 3.2 easier to do math for) nominal, and 3.6 to 3.8 volts charging. All lithium chemistries require special chargers which use constant current constant voltage charging, and LiFe cells in particular require different termination voltages (A Li-Co or Lipoly charger cannot be used directly on LiFe packs).
Loose cells vs. packs
Alot of the time, you can find loose cells being sold next to battery packs. Due to the varying experience levels of potential readers, the physical dangers of working with loose lithium batteries , and the special soldering techniques needed to assemble a pack, I am not going to advocate people making their own battery packs here .
Premade packs will already have individual cell taps (crucial for a future battery management system or charge balancer, to be details soon) instapped and wires pre-attached. In some cases, they come with a charger and integrated BMS.
Step 10: Premade R/C Lithium Polymer and LiFe Packs
This whole Instructable might be summed up as "How to Shop on Hobbyking", because that's exactly what I'm about to tell you to do. There are several reasons why I focus on HK's lipoly selection and LiFePO4 selection specifically.
First, there are tons of them , in varying grades, capacities, and physical sizes. They are well-sorted into categories, and the customer review system is extensive. HK also has a good battery warranty system now. There was a time a few years ago when their batteries had poor quality control problems and overrated numbers. However, having gone through several packs (purposefully and accidentally), I generally believe their numbers to be reliable now
Oh, yeah, they're also cheap . Here's some things to watch out for when you're sizing up a battery to use.
The C rating
In batteryland, the unit "C" is one battery capacity in amps . In other words, for a 1.0Ah battery, 1C is 1 amp. 10C is 10 amps, and so on. Batteries are almost always rated for a certain continuous and burst (order of several seconds) discharge rating. High C-rating cells have stronger, thicker interconnects and are physically bigger to handle the power throughput.
Higher C packs will exhibit less voltage drop on high current loads. For a battery of reasonable capacity, you generally don't need the insane 40-50C discharge packs, which are comparatively more expensive. What I have found is that only the 30C type cells and higher have copper interconnects, which are crucial for high current sustained draw.
Keep in mind that the cruise current of a small EV should be dictated by the maximum continuous current of your motor (which contributes to motor heating), and with the common 50-60mm motors should be 20-30 amps at the most, which for a 5Ah pack is only 4 to 6C. This doesn't mean you should get a cheap 15C battery, however, because the current demand on startup can easily exceed that rating and frequent excursions can cause excess battery heating and short life.
The capacity
Sizing battery capacity is wholly up to the designer. The amount of energy a vehicle needs to travel a certain distance is given in units of Watt-hours per mile (or per km), and is the same thing units-wise as (inverse) miles per gallon, or liters per 100km. Many factors come into play here, including the cross sectional area of the vehicle (drag), whether you're going up or down hill, how inflated your tires are, how much you weigh, the roughness of the road, did you oil your bearings, etc.
In other words, there isn't really one definitive easy rule of thumb for battery pack sizing. However, one good resource to use as a lookup table is the Austin EV EVAlbum - you can search for vehicles similar to the one you are designing and see if Wh/mi data has been collected by other builders.
Small electric scooters seem to average between 25 and 40 watt hours per mile. My own RazEr hub motor scooter is the low end of that (25 Wh/mi measured), and melon-scooter is a total battery hog due to its huge motor and knobby tires at 39 to 42 Wh/mi.
Keep in mind that you can never get 100% of nameplate capacity out of the battery. Typically, a battery charge-discharge cycle in the EV world is defined as 80% state of charge to 20% state of charge . A Li battery is finished "fast charging" when the constant current stage finishes, and it is at approximately 80 to 85% full charge then. 20% is an accepted minimum safe discharge threshold. So really you get about 60% of the battery if it is used with regularity and not allowed to top off (say overnight).
Multiple cells in parallel vs. multiple packs in parallel
Some packs are available as multiple cells in parallel internally (indicated as "xSyP " where the P is number of cells in a group). While it is tempting to just put multiple packs of single cells in parallel, you have to have a dedicated charger for each pack, i.e. can perform charge management on each one individually.
This is necessary in a parallel pack situation because there is no guarantee that the same cell in each pack will discharge at the same rate or to the same level. If the packs are charged all at once in parallel, then these cells could settle out to different voltages over time. Because Li batteries cannot tolerate overcharge or overdischarge, periodic balancing is then required, and having to balance multiple packs is a PAIN IN THE ASS . Guess how I know.
This isn't to say it isn't possible, but you should be prepared to do some battery babysitting every once in a while.
A better option is to get the largest single-cell pack you can. If you are making your own pack, put multiple cells together first such that they act as one large cell.
Balance plugs
R/C packs come with a small connector that breaks out the middle of each cell connection. This often used for battery balancers which may or may not be built into a charger - more on charging later. The most common connector is known as JST-XH , which is good because it uses a standard 0.1 inch (2.54mm) pin spacing. The connectors (as components) are extremely cheap on places such as Digikey, and you can also buy harnesses, adapters, etc. which combine packs in series or parallel.
If you are running multiple parallel packs , make sure to grab a parallel balance adapter or two (example , with different connectors ) and always charge using it.
Mechanical protection
Lithium polymer batteries are soft and plushy, and HK's LiFePO4 flat cells are no exception either. R/C models are generally also soft and plushy, and so this is not a problem in their intended application. However, vehicles are usually not very soft. It is essential that the battery is mounted properly or inside a shell or protective housing.
Always support the whole length of the battery
Never just zip tie a lithium pack to something - the concentrated stress of the zip tie will damage the cell mechanically and could potentially lead to a pierce-like thermal runaway situation.
Never compress just the battery between surfaces
Just like too loose hanging can be bad, cramming the battery between two surfaces can be just as bad. Excess pressure can be placed on the roll-sealed cell edges and they can burst open, and then Bad happens.
No sharp things around the battery
Not only can they cut wires and destroy insulation leading to frame power faults, but sharp sheet metal edges can also cut open the cells.
Keep the battery away from water, road debris, etc.
Water (and if you're from where I am, salt and de-icing chemicals) seeps into the layers of the battery pack wrapping and can cause fast corrosion at the terminals, helped along by electrolytic action.
Ideally, the battery should be in a hard case that fits it perfectly but transmits all the mechanical loads of the vehicle around the battery. If I can't stress this enough, then I can only say that people have made entire youtube careers predicated on setting lithium batteries on fire . Go watch enough of them - you will be more careful.
Incidentally, HK has an entire line of hardshell packs for use in R/C cars (which are more liable to smashing into things). While I have not used them, I believe them to be good things.
General Appraisal
Based on vehicles I've built or seen built, a good starting point for an electric scooter is a 5Ah pack of 6S to 10S (which may need to be 2 packs in series), of 25 to 30C discharge specification. This can be gotten for about $100. If you take the cheap LiFePO4 option, this is closer to $150 or $200 (as of this writing).
Step 11: A Sneaky Premade A123 Pack Option
There's one segment of the consumer market where A123 cells are sold in packs with integrated battery management systems and bundled chargers and used every day by people who aren't electric vehicle nuts.
That's the high-end cordless power tools market. Specifically, the DC9360 36 volt lithium ion battery for DeWalt's 36 volt power tools line has been the subject of great praise by the crazy electric bike guy community. A DC9360 battery and charger (Dewalt part number DC9000) set can usually be obtained on Ebay or Amazon for $200 or so, and the battery itself around $120. For 10 A123 cells with an integrated battery manager, that's quite a steal at market prices. It is much more expensive than the Hobbyking option, but A123 cells are serious quality.
The DC9360 does need a bit of hackery to turn it into a full fledged EV battery, however.
BMS Hack
The battery has three terminals:
1. Positive, which is connected directly to the cells inside.
2. Negative terminal connected through a hard 15 amp fuse inside the BMS module , distinct from the fuse described below. Pulling more than 15 amps from this would just blow the fuse.
3. Another negative terminal connected through an internal power MOSFET.
Several hacks have been documented on the BMS module's internal workings which indicate this FET is used as a speed controller for the tool motor. A document which details how to connect to the BMS such that the FET is turned on (allowing the higher current output to be used) is here . It also describes a multi-battery "ORing" system which any number of batteries can be paralleled and swapped in and out. I can't vouch for that circuit, however, since I've never built one.
Another option which has been validated is to simple solder wires directly from the positive terminal and negative terminal of the cells, completely bypassing the BMS for discharge purposes, but continuing to use it for charging. This operation usually leaves a discharge cable exiting the rear of the pack and leaves the tabs and connections on top unmodified.
Fuse Bypass
Once cell interconnect inside the pack is deliberately made narrow so it acts as a fuse if the current draw becomes too high or the battery is shorted past the BMS. The location of the battery-level fuse is detailed in this RCGroups post (the post itself describes the complete removal of the BMS module, which is great if you want to make your own packs, but otherwise not helpful). This narrow area can be bridged using copper desoldering braid, grounding braid, or just some pieces of wire. A large soldering iron (60 to 80 watts) with a high thermal mass tip should be used to solder the reinforcement without heating up the cell too much.
Many resources on the Intertubes have been compiled by Crazy Electric Bike Guys about chopping and screwing these batteries - here's another one.
Step 12: *NEW July 2012* LiFe Lead-Acid Replacement Modules
How I love progress. In the past year or so, several battery companies have produced "Lead-acid replacement" packs which are essentially LiFe cells in a box, with charge management circuitry that makes them compatible with conventional "dumb" lead-acid chargers. They generally feature auto charge cutoff, internal cell balancing, fused or protected outputs, and other nice features which makes your electrical systems plug-and-play. The downside is, of course, added cost. They're also not the best in terms of energy density, of course, because they're designed to fit into applications for existing industrial battery sizes.
I've listed some possible vendors below along with commentary and use considerations.
K2 Energy
My current favorite for SLA replacement bricks because I've actually had the chance to use them and they're commercially available, these are from a somewhat under-the-radar battery company called K2 Energy, but they've actually got product. Nice product. The models in question are the K2B12V7EB and K2B12V10EB, both of the "7Ah" lead-acid battery format. The 12V10 has an extra cell in parallel for higher capacity in the same package. These modules are rated to 25A discharge with 40A peaks, which is more than enough for average cruising vehicles, but may not be sufficient alone for a drag racer setup.
It's important to note that they come in a version with internal battery management module, as well as without. The "B" in the part number indicates the presence of the BMS board. The plain version (e.g. K2B12V7E) is, as far as I understand it, just a box of cells. The cost is usually $30-40 less than the BMS version, but if you are just getting a box of cells, then the cost per watt hour is not very competitive at all with HK lithium iron phosphate packs.
I've taken apart one of the 12V7 modules on my site because I was curious about the internal layout of a SLA replacement module, so if you also want to take a look inside, the post is here.
These generally retail for $140 for the 12V7 and $170 for the 12V10. The watt hour per dollar cost for the 12v10 is actually much lower: about $1.40/Wh for the 12V10 compared to $1.70/Wh for the 12V7, in the same package size, so I consider the 12V10 superior in this regard.
A123 Systems
My electric vehicle lab class in the Spring of 2012 was made possible in part by A123's donation of a whole set of ALM12V7modules. They're A123's own house-developed SLA module with some of the highest discharge ratings around. They have an externally accessible fuse, too, which is nice because if you blow up the internal BMS on any of the other modules, the whole module is trashed. If the fuse blows, the BMS shuts down until the fuse is replaced and then charging voltage is applied to the battery, upon which it will wake back up like a Pokemon. For the student-built vehicles, this happened several times and I'm kind of glad that the fuses are there as a result.
I'm now going to stop singing the praises of A123, no matter how nice they were to us, and point out that YOU CANNOT BUY THESE. A123, in my opinion, suffers from "classy American company disease" where the company absolutely refuses to do business with end users and only seeks large supplier contracts. You can't buy the ALM12v7 online or really through any supplier - if you search ALM12V7, all the links consist of user guides and people who have gotten them secondhand or from insiders. A123 has done nothing to market these products to the people who will actually be using them in the end. No matter how good the product is compared to others on the market, they're impossible to get and therefore might as well not exist.
But just in case they wise up, I'm going to leave this space to link to vendors of the ALM12V7s when they pop up.
*NEW* November 2012: Yes, now you can buy them!
The aptly named buya123batteries.com website is the embodiment of the company's efforts to actually, like, sell things. The ALM modules as well as loose cells in 18650 and 26650 size are available.
Generic / unbranded SLA replacement modules
There's a whole other world of shady Chinese batteries out there. Battery Space, my favorite Chinese battery front company, has an entire page of them. These likely use the ingredients sold separately elsewhere on the site (cells, PCM boards). I have neither seen these or used these in person, so I cannot recommend them either way. Many of them have seemingly low discharge rates for their capacity which may make them less suitable for vehicle use.
Step 13: Care and Feeding of Your Battery
Unlike nickel cadmium and lead acid batteries, you can't just throw a lithium pack onto a power supply with a fixed voltage and trickle charge it until it's finished. For long life and safe charging, a lithium battery needs a charger that was specifically designed to charge them. Typically, you also need a system to keep the individual cell levels equal, a process termed balancing. The same goes for LiFePO4 as it does for LiCO and lithium polymer packs.
Fortunately, since 2007/2008, there have been massive reductions in price and increase in accessibility for fully integrated charger-balancers.
R/C Hobbymultichargers with integrated balancers
I use the term "multicharger" just to refer to a charger which can charge and manage most battery chemistries. These are by far the most common and the cheapest type out there right now. The cost is dependent on how many Li cells you want to charge. The cheapest (such as this thing ) can usually charge 6 cells in series, that particular one at a rate that is limited by its 60 watt power - 6 cells (22.2v) means a charge rate of about 3 amps instead of the maximum of 6.
High voltage (10S capable) chargers are much more expensive. I have the IMAX 1010b+ and am very satisfied with it (it's my main robot AND vehicle charger), but it's quite pricy. The new 3010B+ seems to have the same capabilities, but with even more power dumping ability.
All of them need a 10-18 volt (12 is the usual) power supply as the input, which may raise costs depending on what you already have or want to buy.
These chargers can be set up and left on the battery setting you use the most. They will then retain that setting after a power cycle - so really all that needs to happen is plugging it in. They have built-in balancers and cell voltage monitors. Overall, getting a pile of these seems to be the most economical option since the solution is all-in-one, or perhaps all-in-n if you have a complicated electrical system.
If you obtain an isolated 12 volt power supply for each small charger, you can literally just connect the outputs in series to charge especially weird battery configurations. I explore this in making a 4-channel series charger for a quadrotor project. The supplies must be isolated (notice how I keep bolding that word isolated ) so the chargers don't interfere with or destroy eachother as soon as they're plugged in!
Another multi-channel multicharger project is documented at the Jedboard blog .
Dedicated single-voltage charger with offboard BMS or balancer
There are plenty of battery houses that will sell you a dedicated single-voltage charger, with my eternal example of "shady-ass battery vendor" BatterySpace's selection here . They are really not much less expensive than an R/C charger and you lose the flexibliity of changing cell counts and integrated balancing, but they
1. plug straight into mains power and
2. can be the only option if you have very high cell counts like 12 to 14S and want a decent charge rate too. Alternatively,
3. you know it's the only battery config you're ever going to use.
Besides nameless dedichargers, constant-current LED sign driving power supplies have been pressed into battery charging duty. They are tiny CC/CV power supplies in a box - LEDs being current-mode devices, they keep the current limited to a maximum and allow the voltage to swing to a preset point. When the voltage is reached, current is allowed to taper off and vary. If that sounds like how you charge a Li battery, that's because it is. The MeanWell PLC and HLG-A series have been explored for use as battery chargers at MIT. If your battery is conveniently near one of the available voltages, Mouser Electronics is a reliable vendor of them.
You will need an external BMS or at the very least a cell monitor. One neat little device is called the CellLog 8M (which doesn't actually seem to support datalogging) which you plug into a balance port on a battery and it will monitor the voltage on the individual cells - and alert you using an annoying buzz if any go over or under preset Li battery thresholds. At the least, that tells you to stop charging .
Quite a few "kit" BMS systems for EVs are available. I can't say i have ever messed with any of them, since I have always used the first route. The "MiniBMS " project is one example which was developed from several electric vehicle forum members.
Dedicated single-voltage charger with manual balancing for A123 cells
Truth be told, balancing is not an activity you perform frequently. It is more common with cheap R/C equipment and batteries because those cells are generally not matched before being assembled into packs, since that QC step takes alot of time (read: costs alot of money) and most users of the packs will have balance-enabled multichargers. However, if you are running A123 cells, the MITelectricscooterflock has found them reliable and well-matched enough such that balancing is only something you do every few weeks to a few months; and then only after checking the cell voltages to see if it's even worthwhile.
For instance, on melon-scooter, I take the batteries out and check the cell voltages every semester/term. Generally, if the pack was well-balanced the first time (which a multicharger helps immensely in), the cells will not be too far apart. Mine have always been 0.02 volts or better matched at every inspection, but I've thrown them on my charger anyway because it's there.
With the manual balancing system, the whole pack is charged until the Constant Voltage Stage cutoff - i.e. the final charging voltage has been reached and the current tapered off. The whole pack is taken off the charger and allowed to settle. Then, either low cells are charged one-by-one to match the rest of the pack, or high cells are drained using power resistor loads to match the others.
Step 14: Electrical System Loose Wires
So at this point I've covered most of the major electrical components of a small EV. I've basically laid out how to size motors and which ones are my favorites, which controllers (and control school of thought) to use, how to make sure you don't start a battery fire, and probably am making Hobbyking very nervous right now. I don't care, because I've blown my money there at least once a month for the past year or more. I think they kind of deserve it for that.
What's left is random links and tips to other things i've found helpful for putting together an electrical system.
Don't use a cheap Radio Shack rocker switch as a main power switch. Get a real high-current key switch or similar (the Hella key switch is very popular along with its Giant Red Knob cousin). A cheap rocker switch will erode very quickly from power-on sparking unless you have built a precharge circuit or inrush limiter (both helpful terms to search). Furthermore, even though a switch might look kind of beefy and metallic like figure 2, the contacts inside are still very small and can only pass 15-20 amps without overheating. Besides, every watt of heat going into cooking the switch is one that is not making it to the motor.
Here's a whole asston of power switches from the RobotMarketPlace. Note: you should avoid the Hella knockoffs - I've measured the contact resistance of those things at upwards of 15 milliohms. This doesn't sound like much, but that's potentially 30+ watts of heat at 50 amps continuous!
For lower powered vehicles, some times jamming the main battery connector is enough as a switch. A robust connector with a shroud like the XT60 type should be used here - while the common Deans "T" offers low resistance and compact size, I and others have found that they are difficult to insert correctly and you often miss multiple times (hence power cycling the system rapidly multiple times - not good for the electronics)
Do NOT skimp on wiring.
It might be tempting to just get some 16 gauge house wire to finish everything, but really on a vehicle your wiring runs should be as short as possible and as fat as possible . Long runs must be a heavier gauge than short connections. Every wire in a vehicle is technically a resistor, and resistors burn off power. Get some high quality "noodle" silicone-insulated high-strand-count copper wire while you're shopping for motors and controllers. The usual recommended capacities for copper wire are a good guide to follow, but keep in mind these are continuous amps with no surge - push 100 amps through a few feet of 14 gauge wire briefly and you will lose several volts.
For instance, on melon-scooter, my main battery bus wiring is twin 10 gauge (i.e. 2 10 gauge positive, 2 10 gauge negative). This ensures the least resistance going into the controller that I can reasonably achieve. There's no need to use 4/0 wire on everything, but 12 and 10 gauge should be making up most of the main power distribution unless the vehicle is very small or low powered.
Shield or twist all signal connections and keep them short.
A vehicle controller is an electromagnetic nightmare because it's usually hard-switching dozens, if not hundreds of amps at several thousand times a second. It's a really hardcore, scientific way of touching 2 wires to eachother. The result is alot of EM noise broadcast in the local area. Long signal wire runs, such as throttles and motor Hall sensors, can pick up this radiated noise and it can cause interference at the controller. This often manifests itself as twitchiness under heavy acceleration or rapid throttle changes.
Twisting wires together is one way to mitigate the noise issue. Another means is to run sensitive wiring, twisted together, through a conductive shield tube that is grounded to the vehicle frame or controller case.
Small EV throttles are about as standardized as.... you know what, I can't even think of something so unstandardized. If you have a mystery throttle, chances are these days that it is a linear Hall Effect type sensor, not a potentiometer. If it only has 3 wires, you are in luck. One will be black, blue, or brown . Or some other dark color - this is generally ground (0v). Another will be red, orange, yellow. .. or some bright color, and is 5 volts input. The 3rd wire is generally green, yellow, or white - notice that there's alot of overlap, and is the signal output. These aren't hard rules - I have actually seen white be the logic power before, and orange has once been ground. If you have 4 or 5 (or more) wires, the same guidelines are helpful.
It's almost better if you start with new commercial throttles (examples ). I personally favor thumb throttles over full grip ones since you can brace your hand against the handlebar with them. Here's a great example of a custom-made thumb throttle!
Get a stiff 12v accessories bus because you can run any multitude of obnoxious lighting, sound systems, and... maybe like, control logic or something... off it. A DC-DC Converter which has your battery voltage within its input range and 12-15v output is desirable. These are available all over eBay - make sure to get the chassis-enclosed modules instead of open-board or board-mounted types. Some permanent vendors also exist, such as CurrentLogic .
Notice that alot of "Discount EV" involves shopping away from mainstream vendors, and performing much eBaying. Lots of these "discount" parts vendors don't have permanent businesses or their own product line. I'm more than okay with this, though it can be difficult for some people to wander off the path of Amazon et. al.
Step 15: Mechanical and Drivetrain Resources
The vast majority of small EVs use either synchronous belt ("timing belt") or roller chain drive. If you're designing a drive system that isn't one of those two, I assume you already know what you're doing. This section will discuss the pros and cons of the two styles for people on the fence about drive components, as well as highlight a few places to get them.
A good source of reading on any type of power transmission ever is the RoyMech website. In fact, they're great for reading about anything remotely engineering-related ever.
Roller chain, the proven method
Chain drives are by far the most common method for dynamically engineered vehicles since it's adjustable in length, very cheap, and strong. Chain also tolerates a degree of misalignment between sprockets, and is much narrower than a comparable belt - important for working in tight spaces. If you're whipping together something quickly, chain is probably the way to go.
Avoid bicycle chain
While it may be tempting to just grab chain from a junked bicycle, bike chain has very thin sidewalls compared to industrial power transmission chain, and usually hollow (and flexible, to enable derailleur shifting) rivets. The result is a chain that can easily break when subject to the loads of an electric motor as compared to a human.
Chain size
Common small chain for vehicles are ANSI #25 and #35, the leading number of the specification being the chain pitch (inter-link distance) in units of 1/8" (0.125"). By far, #25 is the most common, the cheapest, and can reliably handle 1 horsepower or so, more with reduced lifetime. Actual chain life depends strongly on the load and tension - gory engineering details can be found in places like The Complete Guide to Chain , but you can expect #25 to work for most purposes.
Higher power systems, such as those over 2 to 3 horsepower, would find #35 helpful - as will systems which suffer from poor alignment and tension, due to the larger teeth of #35 sprockets. Unless you're making some kind of drag racing vehicle, #40 chain is utterly too large and heavy; it's used more for go-karts and mopeds.
Chain tools
To effectively work with chain, a worthwhile investment is a high quality chain breaker. These little things cost around $20 to $50 and have an adjustable screw handle to force out the chain rivets and let you cleanly separate chain and remove and add links. The type shown in the image is the most common, and is usually advertised to handle #25 to #60 chain sizes. However, I find that they are a little too large to reliably press #25 chain rivets - the punch tends to slip off the end of the rivet and deform the plates, which weakens the chain.
Chain and sprocket vendors
My favorite go-to place for chain and sprocket is Surplus Center . I consider Surplus Center to be like the Hobbyking of random power transmission hardware and farm equipment - they have a little bit of everything . Most of their power transmission parts are actually new and not actually "surplus". They have sprockets with hubs (useful on the motor side) as well as hubless plate sprockets for custom rim attachments.
Oh, and bearing (mounted or unmounted)...and shafting, and shaft collars, and everything else you might need to build a random vehicle in one stop. The only thing they don't really have is timing belts.
Remember to pick up master links and adding links for your chain.
Another useful place to look is the very aptly named ElectricScooterParts sprocket division . I would recommend ESP to anyone seeking a complete matched set of sprocket and wheel . If you don't have fabrication facilities available, coupling a sprocket to a wheel may in fact be difficult.
Of course, the the trivial answer is always McMaster-Carr - who has updated their website to be more friendly to people not knowing exactly what they are looking for. Their prices are very competitive with Surplus Center in the common pitches and sizes, and for most people in the Continental US, McMaster somehow delivers your order 5 minutes before it is placed.
Random trivia: Chain is one of the only power transmission components in existence where metric specifications are based in inches. Metric chain is specified in units of 1/16" (0.0625") ... so a #4 metric chain is a #25 ANSI chain. #5 metric chain, some times called "8mm chain" is very rarely seen in some mass produced scooters and other small rideables.
Timing Belts
I'm personally a synchronous belt fanatic, since belts are quieter and less messy than chains. They do, however, require much more precise alignment both angularly and axially on a shaft. Timing belts also must be run under the correct tension. They can be marginally more efficient than chain (on the order of 5% for well designed systems), but this difference is in my opinion negligible for small vehicle use. Belts come in different widths, and the wider the belt, the more power the teeth can reliably transmit. Belts cannot be fudged as much as chains in this manner - in belts, the power transmission medium is made of little rubber and fabric backed nubs, which will be smeared and mashed if too much power is put through them at once.
ANSI sizes
The most common U.S. timing belt size is called XL (apparently for Extra Light, since the really big ones are XH for Extra Heavy) and has an inter-tooth spacing of 0.200". The ANSI type belts have trapezoidal teeth and are an older design. McMaster-Carr has a decent selection of XL pulleys and belting because of their prevalence in U.S. engineering. Because the vast majority of small EVs are foreign-made, XL belts are actually quite rare in that field.
Metric HTD type belts
The HTD belt is a staple for small power transmission uses. They have round (semicircular) teeth and were eengineered to transmit more power in the same belt size. HTD belts come in 3, 5, 8, and 10mm pitches (Real metric this time!), and the most common by far for small vehicles is the 5mm size. Typical 5mm belts come in 9 and 15mm widths - the 15mm being able to transmit that much more power.
A metric belt is specified ina fashion similar to 535-5M-15. The first three digits are the total length of the belt loop in millimeters. To find the number of teeth, divide this number by the pitch. "5M" indicates this is the 5mm pitch, and 15 indicates the width. So this is a 107-tooth 5mm belt that's 15mm wide.... the most common individual size found in scooters.
Metric GT type belts
The GT belt is another round-tooth metric belt specification produced exclusively by Gates Corporation, a prolific rubber products manufacturer which invented and popularized the V belt several millennia ago. They are interchangeable with HTD belts of the same pitch.
Get some belting
Being more "high end" or "precision" components, places like Surplus Center and McMaster don't have good stocks of HTD type timing pulleys and belts. While ElectricScooterParts does have a selection of common belting for scooters, I find them to be horrifically overpriced - probably just taking advantage of people seeking hassle-free 1:1 replacements for a broken part. I don't blame them, but I wouldn't get stuff there either.
However, if you're just messing around or building your own driveline, the place to go is Stock Drive Products . I have personally sworn off SDP until they update their web store to be less 1990s, but they are great in general and their metal timing pulley selection is extensive. Another belt house I've found is B & B Manufacturing , whose prices seem to be a little more competitive in the common small sizes. What belts McMaster-Carr do have in 5mm HTD, however, are very high quality (Kevlar-banded, Goodyear rubber).
Hub motor drives
Okay, I'm not going to let any scooter-related subject pass without mentioning hub motor drives, which I would pick as my "area of research" if you really pressured me to be academically productive. The MIT Electric Scooter Team has recently seen a surge in the number of hub drive powered vehicles. The motors, unlike those featured in my Just Make Your Own Hub Motor Already Instructable, are based off the "layered 2d plates" principle explored by Kitmotter and piloted by the BWD Scooter and the Jedboard .
Here's one vehicle with a hub motor in progress, and here's a completed one (easily the stealthiest thing ever).
Step 16: Good Mechanical Ideas
This section will address some small mechanical details that can be headaches to those who are not machine shop endowed. If you do have metalworking tool access, then attaching two things together or changing bore and shaft sizes is generally a trivial operation. But I started building vehicles when I did not have extensive shop access, so the following advice is mostly aimed at the starving vehicle hacker.
Set screws may suck, but they work well if done properly
An old adage in the combat robot community I have been part of is "set screws suck". They rattle and come loose, they mar and damage shafts, they strip out, and are generally horrible to deal with. However, I contend that a large part of the disdain that robot builders have towards set screws is caused by them doing it wrong .
While the average set screw you may receive with a pulley or sprocket can be tiny - the common thread on a 5M-15 motor pulley being #8-32 or #10-32 (metric 4 to 5mm) - what's more important is how the set screw is seated in the shaft.
If a set screw only has a round shaft to grip, then all of the transmission forces must pass through a very tiny tangential contact patch. The result is the familiar marking and ring-shaped groove that forms when (not if, when ) the set screw slips due to shock torque or overload. To effectively use a set screw, it must have a flat or a dimple in the shaft to grip . A flat can be filed or ground and a dimple can be drilled using the pulley or sprocket's set screw hole as a template. It doesn't have to be deep nor expansive - any concavity will do. The contact patch is changed from a small tangential deformation to a much larger solid material interference fit. Now, instead of just overcoming a small ring-shaped patch of metal, motor loads have to essentially crank the entire set screw through the shaft.
Another important but often overlooked detail with set screws is that they must be as large as possible to obtain as much face contact area with said flat or dimple as possible. Too small a screw can just shear off or indent the shaft and become loose. While having a flat or dimple is more important, I often take the opportunity to "upgrade" the set screw size on a pulley or sprocket - especially pulleys, because sprockets tend to come with keyway bores I can take advantage of. I've done ridiculous things like use a 5/8" set screw on a 3/4" diameter shaft, and just about the minimum I use on a standard 10mm diameter shaft is 1/4"-20 (or M6 coarse thread).
Bore changing - large to small
One of the hardest parts about putting together the power transmission system of a vehicle is how to attach the initial chain sprockeet or pulley to the motor. For those with a shop at their disposal, bore adaptation and remachining is a trivial matter. But otherwise, you'll have to pull some tricks and hacks to adapt the bore of the sprocket or pulley to be mountable on a motor shaft.
If the shaft is smaller than the sprocket or pulley bore, it's relatively easy. Plain bronze bushings ("bronze bearings, oilite bushings") can be used as a shaft diameter adapter. You'd have to find one with an OD that fits the pulley or sprocket bore and an ID that fits the motor shaft. If both are metric, which is often the case, this is relatively simple. Metric bronze bushings are available now from most industrial suppliers, including McMaster-Carr .
If the pulley or sprocket has a simple cross-drilled set screw, then you can use the existing set screw hole as a template to manually drill through the inserted bushing. This hole is important, since having the set screw press against the bushing is an ineffective way to transmit power - a solid mechanical connection must be made between the pulley or sprocket and the motor shaft.
Aluminum can shims
The boring soda can is in fact a very precise source of shim material. Can wall thickness generally varies from 0.003 to 0.004" near the center to 0.006 inches near the base (but not the rolled base itself). So, if you cut a sliver of drink can and stuff it into a misfitting bore, you can take up slack of around 0.01" diameter.
Bore changing - small to large
For operations where the bore of the pulley or sprocket needs to be enlarged , this is a much more difficult affair to the non shop endowed. Drilling out a bore is almost certainly guaranteed to render it off-center and wobbly. There is no technique that I know of which can use garage tools (up to and including a drill press) to create an on-center non-wobbly new bore in an existing old one. If you know one, please share it.
One option is to use reamers if the diameter is close - for instance, 3/8" to 10mm (0.375 to 0.393 inches), or 5/16" to 8mm (0.3125 to 0.3145 inches). The multiple straight flutes of the reamer tend to keep the reamer centered in the existing bore, but this still only works to a limited degree if it is not started straight to begin with (i.e. you're chucking it in a hand drill). However, the reamer itself can be expensive - $15 to $30 depending on type and size
For large bore size changes, like 8mm to 12mm - very common for fitting a 5M-15 HTD pulley to a large outrunner, metalworking machinery is practically indispensable. You may be better off asking a friend with machine tools or getting to know an area machine shop. Such a large change requires multiple "passes" of larger drills and reamers, and without a fixed center on a metal lathe, each pass causes more concentricity loss.
Imperial drill bit sizes that are almost metric
These drill and reamer sizes are close enough such that you can fudge around and make a fit if the correct size is not available.
A #9 drill is 0.1960 and is a spot on slip fit for 5mm shafts.
A 15/64" drill is 0.2340 and creates a tight press fit for 6mm (0.2360) shafts
Likewise, a B drill is 0.2380 and creates a loose slip fit for 6mm shafts
5/16" is within 0.002" of 8mm (0.3125 vs 0.3145 )
An O (that's the letter O) size drill is 0.3160 and therefore will make a loose slip fit on 8mm shafts
15/32" is almost 12mm , but the difference is 0.004" and is too great to create a press fit.
19mm is almost 3/4" (0.748 vs 0.750 )
Here's my favorite wire gauge and drill size chart for those of you interested in the hard numbers.
Gap-filling retaining compound is your friend
If you're in a situation where there is a few thousandths of an inch of diametric gap, it's not quite the end of the world. Thick retaining compound is beneficial here. The difference between threadlocking compound and retaining compound is that the latter is designed for use in situations where there aren't threads. Loctite type 635 and 638 are very thick retaining compounds that can fill gaps of 0.01" or more. Type 609 is very thin and my favorite for sticking bearings in pockets where they should be.
This does not mean you should rely solely on Loctite for power transmission - a set screw or similar should still be used, but the Loctite, once set, will bridge the gap and make the joint less prone to wobbling.
Step 17: Wheels
For the most part, you'll probably be picking a wheel off ElectricScooterParts or similar - their wheel selection is pretty much unbeatable, especially for matched sets of front and rear with drive sprockets. I would recommend, however, taking a trip through the likes of eBay and searching for the wheel size first.
Non-pneumatic wheels
Most small scooters have 100 to 150mm solid rubber or polyurethane wheels. These are often not designed to be driven (are caster wheels) however, and myriad methods exist of adapting them to drive sprockets or shafting. If your means of fabrication are limited, it might not be wise to start with a caster wheel.
In the 125mm range, scooter wheels seem to use either a 7 or 12 spoke design. The latter type, which I've termed "Yak" type since that company seems to have made them first, is the most amenable to limited-resource hacking of sprockets and pulleys because of the even number of spokes. In the second image, one hack I did for my 2007 scooter is shown - it uses pins that are pushed into the spokes, with the spacing such that the pressing friction alone retained the wheel sideways. For those fabricating spacing plates at home, these should probably be bolts with washers instead.
In the 140mm (about 5.5") range, there are several options for wheels that come with pulleys or sprockets mounted. A fairly common type uses a four-hole spoke design and has a 5mm pulley attached. ElectricScooterParts P/N #WHL-100R and WHL-101R are examples, but the type is also available from a range of dealers. Otherwise, the Razor E100 rear wheel is easy to find as a stock replacement part and is also a 140mm wheel, but has a #25 chain sprocket instead.
*New* February 2012Colson Caster wheels
Colsons have been a staple of robotics for ages, but they also make very good vehicle wheels. They're non-pneumatic, but at 65A durometer hardness they're rather soft (the average urethane scooter wheel is 80A and skateboard wheels are usually over 90A hardness) and give a much less bumpy ride. They're also easily machinable because the wheel cores are made of polypropylene plastic. If you need a weird wheel size like 3 or 4 inches, say for an electric skateboard or longboard, they're worth looking at.
Razor Wind is a scooter that uses gray 4" Colson wheels. RazEr Revolution, one of my own steeds, was recently switched over to using 5" black Colson wheels.
Pneumatic wheels
If you don't want bone- and component-rattling death, it's wise to start with a pneumatic wheel. The most common small scooter wheel is the 200 x 50 (metric) or "8 x 2" (U.S./imperial) wheel, and ESP has those with 5mm-HTD type pulleys built right into the rim, such as their product number WHL-220R. The tooth count on these integrated pulleys is generally 72 teeth. Monster Scooter Parts also sells 200 x 50 wheels with 56-tooth #25 chain sprockets, an OEM part for the Razor E200, alongside the 5mm HTD belt kind.
One excellent resource of small pneumatic tires is Caster City . Discovered by my partner in small EV crime Shane, they have rare 6 inch pneumatic tires (which he has adapted for hub motor duty in the Pneu Scooter ). These 6" pneumatics might be handy if you're seeking a very small vehicle frame but want the ride smoothness that air-filled tires offer.
*New* November 2012: Harbor Freight, Northern Tool, and other Discount Tool Caster Wheels
One very inexpensive source of 6 to 10 inch diameter pneumatic tires are discount/import tool shops such as Harbor Freight and Northern Tool. These wheels are made to be casters only, so they have bearings in the hubs and there is no way to attach a sprocket directly to the hub. However, the hubs are bolted together, and several builders have used these bolt holes as a chance to locate a plate sprocket or belt pulley using standoffs - little round spacers.
An excellent example of adapting a sprocket to a pneumatic caster wheel using this method is Amy's Blitzen bicycle. She used a custom welded standoff-hub, in part because the rear sprocket was required to match a reasonable pedaling pace and could not be made larger.
The only down side to these wheels is that they may be of lower quality than a comparable wheel sold through a reputable industrial supplier. However, being so cheap, it's hard to argue.
There's nothing much I can say about wheels - if you try hard enough, just about anything that is round can act as a wheel.
Live shaft vs. dead shaft
It's harder to convert a nondriven wheel into a wheel with a sprocket or belt pulley on it, due to the need for large-diameter concentricity, than it is to just stiffly attach the wheel to a rotating shaft. Therefore, it might be easier to adapt a nondriven wheel to a live (rotating) shaft. In this case, the wheel and axle would be suspended by pillow blocks (bearing blocks) on either side.
Small vehicles often use the rear axle as a structural member to prevent the forks from wobbling sideways. If a live shaft is used, this structural member is lost, so the forks should either be reinforced from bending or bridged (connected) at another point.
For small wheel hubs, the Robot Marketplace has a selection that matches some of their pneumatic tires. Another option is known in the power transmission world as a "keyless bushing", which functions kind of like an adjustable collet for a shaft. McMaster has a selection of keyless bushings (search those terms). These have a bolt circle you can directly drill into a wheel and retain it, and tighten onto a shaft usually using the same bolts as a clamping mechanism.
Another popular live shaft transmission part is the TranTorque bushing, prodced by Fenner Drives, which expands its out diameter and reduces its inner diameter when tightened, thus coupling two parts together. They are found through almost all industrial suppliers including McMaster.
*NEW*July 2012: Turning caster wheels into drive wheels
Many small caster wheels that can be used on vehicles have their own built-in bearings. With some judicious use of digital fabrication services (waterjet machining, 3D printing, etc.), you can adapt caster wheels to become belt- or chain-drive wheels pretty easily by using their built-in bearings as a crude alignment jig. This method was explored and used in creating Chibikart (Steps 10 through 12 show how the custom designed sprocket was mounted to the wheel).
Step 18: Fabrication Resources for the Machine Shop Deprived
I keep forgetting at times that not everyone is spoiled by constant machine shop access. Many of the tricks I've developed to deal with fussy parts and assemblies are useful only to people who are in similar situations as me.
Specifically, if you know me in person, you know that my favorite anything ever is the abrasive waterjet machine . Almost everything (okay, fine... everything) I build these days seems to be made primarily of waterjet-cut parts erected 3d puzzle style. Same deal with laser cutters - I've become well accustomed to so-called 2-dimensional fabrication techniques because they are fast and easy when Apple-like appearance and Built Ford Tough strength isn't the priority.
This is actually a good position to be in, because recently, many services have sprung up across the Internet that will take your part design and actually make it . And unlike large shops and many machine services, you don't have to be making one million of something either. The general name for this kind of stuff is "personal fabrication".
Waterjetting, laser cutting
If I haven't turned this into a single large product advertisement yet, I'm about to. Currently, the only go-to place for online waterjet part ordering is Big Blue Saw . I can't recommend these guys enough - until others open up to compete, it's the only place I can direct people when they want something waterjet-cut and cannot access a machine in their area or on campus. Many MIT student projects have also used BBS. The turnaround time is short and prices include materials . This is key: buying materials in bulk, huge plates saves money and lowers unit cost of parts.
For precision metal parts, there's essentially no better option.
3D printing
Another personal fabrication resource that I have taking a liking to is 3-dimensional printing. Not just because I have my own so I insist on 3d printing everything (everything that isn't waterjetted), but because there are also plenty of companies which will take your 3d design and pop out a plastic (or metal) version of it for you. Shapeways and Materialise are two reputable 3d printing houses.
Structural vs. nonstructural plastics
One important distinction that must be made is the type of material. Most structural parts (i.e. usable mechanically) made on 3DP machines are made of ABS and Nylon (Polyamide, PA) plastic, high-impact thermoplastics. The most common process is fused deposition modeling , which produces immediately usable ABS parts. Nylon parts are typically made with selective laser melting/sintering .
Of the two, ABS tends to be cheaper. Shapeways calls ABS "Gray Robust" and Nylon "White, Strong, and Flexible". Materialise just straight up indicates their material as ABS and PA.
For structural parts, avoid photopolymer resin or similar - they're generally decorative, but the processes are capable of very high detail.
How can 3d printing be used on a vehicle? You can make weird integrated spacers or hubs using them - ABS plastic is usually strong enough in bulk for the purpose. Custom motor mounts are also a possibility. That motor sensor holder for the 63mm class motor that I showed earlier.
Design-for-waterjet
Through fighting my addiction, I've accumulated quite a few tricks for putting things together using solely waterjet-cut parts. I've compiled some of them in a document I wrote for the MIT 2.007 class, called "How to Build Your Robot Really Really Fast ". This file is hosted on my website, which is worth a look (in the projects sidebar) if you like seeing how much waterjet gluttony I am actually guilty of. It's slightly outdated - I've gradually transitioned to the full cross style of t-nut, so it might see updates to reflect that.
My 3d printer , a Makerbot gene transplant, is full of waterjet and laser edge-stitching and T-nutting.
Another cool use of waterjet-cut plates is using square tube stock and making clamping plates to fit parts on them. Amy's tinybike is a great example of a single tube construction with waterjet-cut parts clamped to it.
Shane's "Tinykart" uses waterjet-cut plates in conjunction with 80/20 structural framing stock. This thing is incredibly stiff, and I'd recommend 80/20 if you can find it cheaply - buying new is quite expensive.
Step 19: Conclusion and Epic Resource Dump
I have somehow managed to write yet another long Instructable without telling anyone how to make anything. That's fully intentional - this guide is intended not as a manual to build a specific vehicle, but instead to list some of the resources and guidelines I have found useful. Nothing I have said here is backed up 100% by engineering principles or math - it's all experiential and rule of thumb based.
Now, go off and abuse model airplane parts to make ground vehicles. Here's a recap of the big vendors of parts I linked to repeatedly:
Electric Power Systems
Hobbyking : Motors, batteries, chargers, controllers, wiring, connectors... How about "everything-minus-drivetrain"?
Kelly Controller : EV-grade controllers, throttles, user interface, some motors.
Robot Marketplace : More robot than vehicle, but good large DC motor selection, some controllers.
Battery Space : My favorite shady Chinese battery front company.
eLifeBike: Shady Chinese company with good stuff.
Drivetrain and Mechanical
Surplus Center : Cheap sprockets, chain, shafts, bearings, wheels... "Everything-minus-Hobbyking". You can build a vehicle using ONLY parts from these two places.
McMaster : Everything ever. Good for chain, sprockets, shafting, and some timing belts. Their wheel selection is also extensive, but many are caster-only.
SDP-SI : Precision parts, timing belts and pulleys.
B & B : Timing belts and pulleys.
ElectricScooterParts : No further explanation needed. Wheels, both driven and undriven. Most everything you would otherwise want on a scooter.
*NEW* Monster Scooter Parts: Like ESP, but larger selection in motors and wheels, as well as controllers.
Fabrication
Big Blue Saw : Waterjetting and laser cutting of most materials that exist.
Shapeways : 3d printing.
Random People's Websites
The EVAlbum
Shane
The Jedboard
Julian's hub motor build
Amy's various small and stealthy vehicles
Jerome Demers
Jamison Go / Iron Man
EVPlasmaMan scooter
All my random scooters
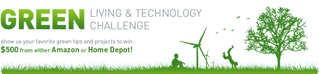
Participated in the
Green Living & Technology Challenge