Introduction: The Sprintronic - Clock With Laser Cut Case
If you have read Sky Mall magazine on a plane, then you have seen the inspiration for the Sprintronic clock.
This is a very easy, inexpensive, and quick project. The clock's movement is a standard battery powered quartz movement from an arts and crafts store. Its case is made of inexpensive 5 mm (0.2 inch) plywood. The face lens is a small piece of Plexiglas.
The case and lens patterns were cut on a laser cutter, however neither are too complicated to fabricate using a scroll saw and drill. The face lettering can be transferred using the toner transfer method when cut with a scroll saw.
A complete kit for this clock is now available at http://www.dougparadis.com/products-page/clock-kits/sprintronic-clock-kit/
Step 1: Materials and Tools
Materials:
1 - Battery Powered Quartz Clock Movement. I have used movements
sold under the labels "The Clock Shoppe" and "ArtMinds". The
movement shaft should be sized for either 1/4 or 3/8 inch face thickness
(you may need to adjust spacing slightly with washers).
2 - 11 inch by 12 inch pieces of 5 mm (0.2 inch) plywood
1 - 3 inch by 4 inch piece of Plexiglas or clear plastic
(I used 1/8 inch thick Plexiglas)
2 - Popsicle craft sticks
1 - Sheet of 110 weight (lb) card stock.
1 - #4 - 1/2 inch (3 mm x 12 mm) screw
2 - #4 washers
1 - #4 lock washer
1 - #4 nut
1 - Credit card size cold laminating pouch
TOOLS:
Scissors
Ruler
Craft knife
Glue (wood and super)
2 small Clamps
Sand paper
Block of wood
Access to laser cutter or scroll saw and drill
Optional:
3/32 and 3/16 inch hole punches
Stain
Finish (varnish or other)
Mallet
Step 2: Cutting the Case
The patterns for the clock's case are attached below. The files with .svg extensions can be opened in Inkscape, a free vector drawing program that is available for all major operating systems. The files with .pdf extensions can be opened in Adobe Reader which is also free.
Note: If you use material of a different thickness (i.e., not 0.2 inches or 5 mm) you will have to adjust the height of the tenons and and the width of the mortises (grooves).
Step 3: Staining and Finishing the Case
If you have laser cut your case pieces they will most likely have some areas where smoke from the cutting process has left a stain on the wood. The way I addressed this was to lightly sand the wood to minimize the smoke stains. I then stained and finished the wood with a wipe-on varnish. The stain camouflages any remaining smoke stain and enhances the beauty of the wood.
Staining and finishing the case is an optional step. It slows the project down, since you have to wait for them both to dry, however the results are in my opinion well worth it.
STEPS:
Sand
Stain
Wait for stain to dry
Buff with soft cloth
Wipe on the varnish
Wait for the varnish to dry
Repeat with 2nd coat of varnish
Buff with soft cloth
Step 4: Making the Clock Faces
The file for the clock faces is attached below. After printing out the clock faces on card stock, use scissors to cut them out. Work slowly and you should not have any issue making nice round faces.
I have added a second option for the clock faces where the minute dial is made of a transparent material. In this clock face option the minute dial will be on the outside ring and the hour hand will be on the inside ring. The hour hand should still be printed on card stock. This option was suggested by many people in the comments. See the 2nd .pdf file below.
The second picture shows the holes that you want to make in the center of the faces (assuming you used the recommended clock movements). These holes can be cut with a small pair of scissors, however an easier way is to use hole punches. It turns out that 3/32 and 3/16 inch hole punches work perfectly.
Punching the round hole in the hour face is easy. The shape that is in the center of the minute hand can be achieved by using the 3/32 inch punch in two overlapping punches that stay within the red border marked on the minute face center. The third picture shows the first punch being made on the minute hand. If you look closely, you can see that there is still a area of paper not punched within the red border in the center of the face.
Step 5: Mounting the Clock Movement
To mount the clock movement select the three pieces of the movement mount and assemble them as shown in the second picture. The hole for the movement's shaft may appear centered, but it is actually shifted a little towards one of the end pieces. The end piece that the shaft hole is closest to will be towards the top of the clock.
The fourth picture shows the movement being mounted. If the movement has a hook built into the case, remove it. You may need to adjust the amount that the shaft sticks out the front. When the hour hand is attached it should just clear the edge of the end pieces. After the depth of the movement is correct, tighten the retaining nut.
The minute hand shaft should be positioned so that the flat part of the shaft shape is perpendicular to the 12 O'clock position. See the last picture. The hour hand should then be placed on the movement, with its position so that it points at 12 O'clock.
Make sure that any temporary protective plastic covering the hour hand has been removed, then carefully place super glue on the front of the hour hand. Make sure that you do not glue the movement so that it can't turn. Next, place the hour face dial over the hour hand with the 12 O'clock position corresponding to the hour hand position. Hold the face dial in position with your fingers for 20 seconds. Wait 15 minutes before putting on the minute hand.
The minute hand face should just slip on to the minute shaft, being held in place by the oblong shape of the shaft and the punched hole in the minute hand face. After you have the minute hand in place, screw on the nut that comes with the hands set onto the shaft.
If you did everything right, the 12 O'clock position on the hour hand face should line up with 60 minute position on the minute hand face.
Step 6: Attaching the Lens
The first step of attaching the lens to the clock case, is to make sure the lens fits in the lens hole.
Next prepare the cold laminating pouch by removing the side that has no adhesive and discarding that piece. Using the side with adhesive, carefully peel the protective cover off.
Remove the protective cover from the backside of the lens, and wash that side thoroughly with window cleaner. Do not skip this step.
What we are going to do is attach the piece of the laminating pouch plastic that has adhesive to the backside of the lens. The part that overlaps the lens will be stuck to the backside of the case front. This step is a bit fussy. We want to make sure that all the air bubbles are removed from where the plastic film contacts the lens. Do not be surprised if you are not successful the first time. The trick is to touch the back of the lens with the laminating material only in the center of the lens, then use the tip of your thumb to slowly smooth and attach more of the plastic to the lens. When you get one half done, do the same for the other side. I got it right on my second try.
Now carefully insert the lens into the back of the front piece of the case and smooth the overlapping adhesive covered plastic film firmly onto the case. Turn the clock front over and remove the protective covering from the front of the lens.
Originally I tried to use clear packing tape for this purpose. What I found was that the packing tape isn't as clear as you want, so even if you get out all the air bubbles, it will not look as good as the laminating pouches.
When you are done you should not be able to tell that the laminating film is there.
Step 7: Assembling the Case
Assemble the front and back of the case to one of the side pieces. Then slide the movement and its supports into the notches that are cut into the side piece. Make sure that the 12 O'clock position is correctly orientated.
Next place the clock on its side and carefully position the second side piece. You may need to adjust the position of pieces to make sure everything lines up. Use the palm of your hand to gently tap the second side into place.
After the sides, front, back, and movement mount are all attached, place the clock on its feet and align the top. Again use your palm to gently guide the pieces together. All the pieces should fit together snugly. No glue should be needed for the case.
Step 8: Assembling the Battery Door
The picture shows the back of the clock and the battery door. Take one of the Popsicle sticks and cut it in half. Sand the cut ends so that they are smooth. Glue each of the half sticks about 3/4 inch from each end of the back of the battery cover door. The two pieces should both be centered on the door so that there is equal overlap of the door edge (See pictures). I used wood glue for this purpose. If you have clamps, place them on the pieces for about an hour.
Next take the other Popsicle stick and cut off about a fourth of its length. Round the end of the long piece so that it matches the non-cut end. Drill a 1/8 inch (3 mm) hole into the center of the stick. Place a washer on a #4x1/2 inch screw and insert the screw into the Popsicle stick. Insert the end of the screw through the door. Finally, place another washer, then a lock washer, then a nut on the screw and tighten. The door should look like the last picture when you are finished.
The door is installed by pushing the door into the clock and holding the clock overhead on its back. Shift the clock until the door falls into position. Finally lock the door by moving the outside stick across the door.
Step 9: Fine Tuning the Clock Disks
You can slightly adjust the relationship between the hour face and the minute face by moving the body of the clock movement as indicated in the picture. After shifting the movement body, reset the minute face with the adjustment dial on the back of the movement.
Before installing the battery and closing the battery door, turn the movement time adjust knob around several times to make sure that there is no binding in the two dial faces. If everything looks good, install the battery, set the time, and lock down the door.
Now sit back and enjoy your new clock!
Step 10: Conclusion and FAQ
I have found this project to be so easy, quick, and inexpensive that I have actually made two. I plan to make a few more as gifts for family and friends. It makes a great desk or shelf clock.
FAQ:
Q: What is the one thing that you would do differently?
A: The wood I used was very inexpensive, I would like to build one
using a better grade of wood.
Q: What type of wood did you use?
A: I used a scrap piece of luan underlay plywood bought at a local
home improvement store.
Q: What are the fussy parts?
A: There are two parts that are a little fussy. Sticking the laminating
pouch plastic to the back of the lens, and getting the hour/minute
hands just right.
Q: Why is it named "Sprintronic"?
A: The watch that it is emulating is called the "Dashtronic". So keeping
with the idea of "dash", I chose "sprint".
Q: Do you have access to a laser cutter and if so how?
A: I do have access to a laser cutter through membership in the
Dallas Maker Space. If you are in the Dallas area, come by and visit.
See www.dallasmakerspace.org for location and meeting times.
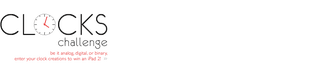
Runner Up in the
Clocks Challenge
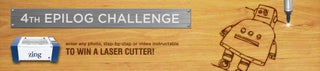
Participated in the
4th Epilog Challenge