Introduction: The Ultimate Shrinky Dink Guide - InkJet Version
This Instructable will guide you through the entire Shrinky Dink process. I have worked with and tweaked Shrinky Dinks to a whole new art medium. With the ability to print with an inkjet printer on both sides of the Shrinky Dink paper, your experience will propel you past your colored pencil past. If you are unsure what Shrinky Dinks are, you are in for a good time. I have perfected the art and am now ready to share with you.
In this Instructable I will show you how to:
- Purchase Suppies
- Receive Discounts on Supplies
- Prepare, Format and Print your Shrinky Dinks
- Cut your Patterns
- Shrink in your Oven
- List the Tools Needed
- Apply to projects
Step 1: Tool Needed
SHRINKY DINKS PAPER
First of all, you will need the Shrinky Dink paper. I usually purchase mine at Hobby Lobby using their 40% off coupon. You can find this coupon using this LINK. 6 pages generally cost $12.99 so the coupon really helps to save money. Most hobby stores carry SDs, so be sure to shop around and check for their coupons. Here is the LINK to the SD Ink Jet paper you will need. Be sure you purchase the INKJET paper as the other products will not work for this Instructable. These sheets come in 8 1/2 X 11 inches.
COMPUTER and IMAGING SOFTWARE
You will need a program to print your images to your SD paper. I use Adobe InDesign to create mine. Most computers come with an imaging program installed. Be sure to format with 8 1/2 X 11 inches.
INKJET PRINTER
It is important that you use an InkJet printer as this is how the images are transferred to the paper. I use a Canon MX410 and it works wonderfully.
SCISSORS or CUTTING TOOLS
You will need to cut your images out of the paper before cooking them. I use scissors, X-acto knives and paper stamps as needed. Depending on your project, you may need one or all three tools. That will be your decision. I also use a standard hole punch to create a hole for SDs that I want to string into necklaces or earrings, They are the perfect size after cooking.
OVEN or TOASTER OVEN
I have a little toaster oven that i purchased for $5.00 at a garage sale, it works great for this project. I recommend using the tray inside the oven or a cookie sheet for your kitchen oven.
CARD STOCK
I line the bottom of the cookie sheet with white card stock paper so that it doesn't get dirty from the cookie sheet. I then place another sheet of card stock over the Dinks before I cook them. SDs will curl during the cooking process and the card stock helps to keep them flat and to reduce altering their dimensions.
SPATULA or PIE SERVER
I use a pie serving tool to flatten my SDs after they have cooked. This helps them to stay flat while cooling down.
OVEN MITT
You will need this to pull them out of the oven so you don't burn yourself.
Step 2: CREATING YOUR IMAGE & PRINTING
CHOOSE YOUR IMAGES
- Find the images you want to use for your SDs. Get them from sites online or scan them to your computer if you have created them yourself. Your page should be formatted to 8 1/2 X 11 inches vertical (not horizontal), this is very important.
- Your images will shrink to 1/3 the size after cooking so be sure to scale appropriately. This means that you need to make your initial image 3 times larger than you would like your final SD to be. If you want a 1 inch tall SD, you need to make it 3 inches tall on your computer program.
(ie: Adobe InDesign, Text Edit, MS Word or what have you)
Place as many images as you can onto your 8 1/2 X 11 inch sheet to
maximize your project area. Leave margins for printing, as well. A 1/4 inch on the top and both sides and a 1 inch margin on the bottom of your page.
- Now for the second side of your SD paper. In your image program, copy your page and open a new document. Paste your existing page in to the new document and flip the page horizontally. This will give you an idea of where the backside of your images will go to create the backside of your Shrinky Dinks. This part will take a little fudging so I suggest you print page 1 onto a plain piece of regular copy paper, flip it over, reinsert it into your printer and print page 2. Hold your plain copy up to a light and you will be able to see how your images line up. This may take a few tries but is worth it so you don't mess up your SD paper.
- Now you will need to lighten your images, front and back, by 50%. This will ensure that your images do not come out too saturated. This is an important step as you do not need that much ink to create your end product. Each computer image program is different so read your instructions or Google this step.
- Once you feel that you have the images lined up properly, it is time to print onto your SD paper.
- Print side 1 then flip it into the printer tray so that it feeds the same way as your first copy. Again, practicing with plain copy paper will save you some frustration with this step.
Step 3: CUTTING YOUR SHRINKY DINKS
Once you have printed your images you will be ready to cut them out of your SD paper. I try to cut them as close to the image as possible. You can use scissors for broad cuts and an X-acto blade for detailed cuts.
- Cut out your images as close as possible to your image. The remaining scraps can be used again for other projects. I use the scrap pieces to cut out bones for another project I am working on.
- Tight corners can be cut with an X-acto knife for fine detail.
- If you are creating a necklace or earrings, be sure to leave a tab that you can punch out with a hole punch so you can string your jump rings or string through. It is somewhat difficult to create the hole after you shrink your Dinks, but it can be done. This is intended to save you a step.
- The large circular punch shown in the photo is used to cut 3 inch circles. You can create a 3" circle pattern on your imaging program and then stamp them out with this tool. They make great 1" medallions for necklaces.
- If you have other types of stamps, you can use these as well. They will cut through SD paper with a little extra effort. The difficultly level rises, but after a while you will master this too.
- You are now ready to cook.
Step 4: COOKING OR BAKING YOUR SHRINKY DINKS
This step is the most fun and rewarding part of the process. Be sure to use caution as you will be dealing with hot materials.
- Set your toaster oven to approximately 320 degrees and preheat. If you are using your kitchen oven, I suggest heating at 350 degrees.
- Cut a piece of heavy card stock paper to fit you tray or cookie sheet and place it on your tray. Have another piece of the same size card stock ready to place over your SDs before you place them in the oven.
- Place your cut SDs onto the paper on your tray and be sure they do not touch one another.
- Now place your other piece of card stock on top of your Shrinky Dinks. This helps them to stay flat but they will still curl a bit when baking. This is a little trick I learned to keep them from curling too much and sticking together.
- Place your tray into your preheated oven and cook for approximately 3.5 minutes. Baking times will vary.
- When your SDs have curled and have flattened out on your tray, it is time to pull them out. They will be hot so be sure to use an oven mitt.
- Place the tray on an area that can stand the heat (ie: cutting board) and remove the top paper stock with your spatula.
- Using your spatula, press each SD flat and individually. If you are not satisfied or they will not flatten, you can place them back in the oven for a minute and will be ready to flatten again. They will not burn at this heat level. Remember to use your oven mitt.
- You are now ready for the final step.
Step 5: FINISHING YOUR SHRINKY DINKS
You might be finished or you may want to take extra steps to make sure your Sds will last for some time to come. You might want to use these for another project such as necklaces or pendants. Below I will list ideas I have used in the past.
- Magnets - Use the magnets that come with your phone book. Cut to size and put them on your refrigerator.
- Jewelry - Use a jump ring and string to wear around your neck.
- Pinback buttons
- 3-D projects - The world is your oyster.
- Action Figures - Capture your friends image and immortalize them.
- Let your imagination run wild. Let me know what you create, please.
As a final step, I like to spray these with a clear enamel so they last longer. The image will wear off with extended use. I mainly make necklaces so I want them to last a long time. A gloss enamel works really well and I suggest spraying several coats, front and back, between dry times.
I realize that this is quite a process and I am happy to answer any and all questions you might have, so feel free to ask away.
If you like my Instructable, please vote for it or add to your favorites. Thank you and have fun.

Participated in the
Instructables Robot Contest
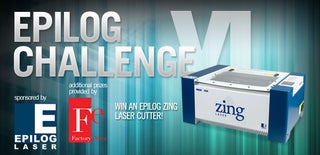
Participated in the
Epilog Challenge VI