Introduction: Timber Light Saber
Time to let out some of the dark side and make Vaders Light saber out of timber. Fairly basic wood turning and a bit of additional work. I chose Darth Vaders as I wanted to use a red timber but the other designs can be easier to make. Hopefully with this tutorial you can make one of your own.
Step 1: Design
All projects start with design. Fortunately, making replicas, its all done for you. I happened to print it of at 1/2 ration so that makes getting measurements easy. Take all the measurements that you need. This is broken into 4 main parts, 2 in the darker section and 2 in the lighter section. Most of it can be done on a wood lathe and the rest using a bandsaw and sander. I chose walnut and kauri pine for the saber and then red cedar for the laser part
Step 2: Timber Lengths and the Base of the Handle
The timber blocks are cut at 15mm longer than required. They were all off cuts from other projects. Start by fixing a block in the 4 jaw chuck and roughing with a gouge. To get a clean cut use a planing cut with a skew. That is where the tool is held at 45 degree angles and lightly slice off the timber. You should get well sliced shavings that look like pigs tails. The timber should be very clean and require very little sanding. This sections is a very basic shape, essentially a cylinder with a fractionally bigger cap on the end. Make sure you leave a tenon on the end.
Step 3: Mid Section
Very similar to the section before just had 2 small beads on the ends. Make sure that you have tight fittings to join the bottom to the mid section. If the bead was not there, you would want it to be flush (same diameter). I also forgot groves in the capping of the base of the handle. I jam chucked it so i could add them on after. Ideally that would have been done before. The next kauri pine part is a straight section with a tenon
Step 4: Top Section of the Handle
This is the hardest part. With the angle cut in the top, this hole has to be perfectly straight. Looking back, i could have used a forstner bit. That would have been the easiest. I used a bedan to take the center and then a scraper. I used the scraper with the tool rest elevated above center. A straight plunge cut allows a clean edge. The reason the tool rest is raised is so that the rest of the tool doesn't get in the way.
Also, there is a square part so don't rush and take it all away.
To turn the other side, I gripped it with thin cardboard in between to prevent the damage of the jaws. I then took only light cuts make a hole that perfectly fits the shaft of the mid part. At first I only made it to fit the tenon, not the shaft. It was after that I realised it had to fit the shaft too because of the cut out. I made a jam chuck and used tape just to be sure to lock it in.
Step 5: Shaping on the Sander
Use the square section to hold to stop the cylinder from rolling and sand up to a pencil mark. Then take off the 2 corners that you do not need on the short side. Careful not to sand a flat spot at the top of the cylinder. My home made sanding table is slightly sloped back so that makes it a little easier for me. The shaping on the bottom is a little harder. Start with the flat spot and used the edge to remove the radius. This will need to be finished by hand.
Step 6: Glue It All Together
The tenons should be enough to hold it together with a bit of glue. As i removed the tenon on the top one, I used a screw. I could have counterboared the others and done the same but I didnt see the need. I used no clamps, just pushed them together as my tenons fitted well. Make sure you do the simple things like line up the grain. I little think like that will make any project much nicer.
Step 7: The Block
This block has to be fitted to a round. To get that done well I had to carve out a similar radius. With the little beads either side, it does hide any slight variations. This is a process of trial and error until you get it right. I was using a rotary bur to slowly remove the waste. I used a clamp to glue on straight. Use sand paper to take the edges off and arise it.
Step 8: The Laser Part
Easy turning here. Use the roughing gouge to take it to the rough shape. Then use the skew for planing cuts to get the clean finish and shape. It will taper off but the beginning has to be straight to fit the hole that had the angle cut.
Step 9: Polishing
I uses lacquer to finish most of my work. The spray gun gives the most even finish. 2 coats and then cut back. Then a final coat to finish it off. After that, may the force be with you
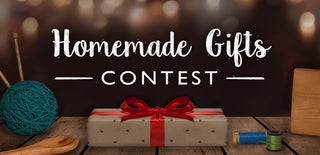
Runner Up in the
Homemade Gifts Contest 2017
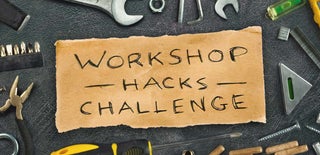
Participated in the
Workshop Hacks Challenge 2017