Introduction: Tin Can Stirling Engine
How I built a hot air engine almost entirely from junk. I've wanted to build one of these ever since discovering stirling engines in about 2003. Spending the weekend making things in Steveastrouk's workshop gave me the opportunity to make the precision parts I'd need, and I knew most of the engine was going to be made of improvised materials, so decided to see if I could make the entire thing out of scrap or unwanted materials.
If you aren't familiar with how Stirling engines work, there are plenty of resources online- the Wikipedia page is a good place to start.
Step 1: Design
The "core" of a gamma stirling engine of this design is a large cylinder that holds the displacer, connected to a smaller power cylinder providing the power strokes. I decided to follow Darryl Boyd's "walking beam" design, where the power cylinder sticks out of the side of the dis[placer cylinder, because it suited the materials I had and it looks cool :)
I found that an aluminium drinks can would fit neatly inside a steel soup can, so decided to use that for the displacer on the grounds of being cheap, light and easy to work with. The steel soup can provides a sturdy body for the engine and also meant I could ake the bottom removable to allow maintenance.
I found some decking to use as the base, some 1" x 1/2" pine to use as supports for the moving parts, and a piece of 3/4" aluminium strip to use as the beam. The engine is a messy combination of metric and imperial units- that's what happens when you use scrap materials!
Step 2: Bill of Materials
Displacer cylinder
Two empty steel food cans, at least one with a tapering bottom
Displacer
An aluminium drink can that fits closely inside the soup can without touching the sides
Two thin metal discs (eg lids from food cans)
Power cylinder
Copper or brass pipe, as round as possible, around 40 - 50mm long
Power piston *
Flywheel
A low-friction ball bearing
A CD or other disc to use as the wheel
Pennies for weights
Beam
About 12" of metal or wood thick enough not to bend too much
Frame of engine
Thin wood (1" x 1/2" or larger) for supports, at least 24" (600mm) long
A piece of plank at least 12" long and 4" wide (300 x 100mm) for the base
Other
Thin brass tube 1/8" inside diameter and steel rod 1/8" diameter- about 12" of each (the precise measurement of these isn't as important as the rod being a snug sliding fit inside the tube)
Wire coathanger
Two terminal blocks
JB Weld or other high temperature epoxy
Fast-setting epoxy (eg Araldite)
Necessary tools
Hacksaw
Power drill
Wood saw
Desirable tools
Rotary tool with grinding and cutoff bits
Step 3: Power Piston
There are several ways of getting a power cylinder and piston for your stirling. At one end of the spectrum, you can buy graphite pistons and glass cylinders online. This guarantees you will get good quality parts but feels a bit like cheating :) At the other end of the spectrum, you can attach a rubber membrane made of a piece of balloon over the end of the cylinder, like scraptopower's engines. This is probably the easiest to make but limits travel and introduces friction.
Others have made pistons by casting JB Weld inside their chosen power cylinder. You can read more about that here- I didn't do this because I had the machined piston/cylinder combo, but it seems to be quite a popular method.
The piston is a 20mm x 20mm solid cylinder with a 1/8" hole bored in one end. A short section of steel rod was glued into the hole, and a section of brass tube glued over that. The end of the tube was flattened and drilled to 2.5mm to accept a conrod made of coathanger wire. In engine terms, this is the small-end bearing.
Step 4: Flywheel
The flywheel is a wheel that I think came from a VCR. I used it because the bearing ran smoothly and the wheel looks quite nice as a flywheel :) The axle hole for the bearing was conveniently almost exactly the size of the brass tubing I had, so that would work for an axle.
I initially tried gluing a short piece of brass tubing to the surface of the wheel to act as a crank, but the glue bond between the metal surfaces was weak and kept breaking. Drilling a small hole into the wheel and gluing a piece of coathanger wire into that made a much stronger crank. A piece of wood with a short section of brass tubing fixed into a hole drilled through it provided a support for the flywheel.
Step 5: Displacer
The displacer is a section cut from an aluminium beer can, with lids taken from other cans glued over the ends to make a flat-ended cylinder. This made the displacer air-tight, so to avoid the risk of it pressurising and exploding in the engine I made a small "breather" hole with a needle. The top end plate was drilled in the middle and a section of steel rod glued into it. The steel rod I had is a sliding fit in the brass tubing, which offers low friction but an almost airtight seal, so was ideal for the displacer rod seal.
The length of the displacer is important- it should take up about two thirds of the space inside the cylinder. I worked out how far the crank on my engine was going to move (the "throw", about 20mm), and subtracted that from the length of the displacer cylinder (90mm) to find the largest size the displacer could be (70mm).
I actually glued the rod into the displacer with it inside the engine once I had assembled the displacer cylinder to make sure the two lined up- if everything was measured with sufficient precision this would be unnecessary. I used JB Weld for this join as fast-setting epoxies tend to soften at high temperatures.
Step 6: Displacer Cylinder
To make the displacer cylinder, I cut the bottom off a can with a can opener which removes the entire end of the can. I then cut the bottom two inches off another can of the same size with a tapered end, which I could force into the first can to form an airtight seal, but which could be removed if I needed access to the inside of the cylinder later.
The top of the displacer cylinder was drilled in the centre and a section of brass tubing glued in with JB Weld to form the displacer rod seal. A hole large enough to accommodate the power cylinder was cut into the side using a rotary tool and the power cylinder glued in.
When assembled, a short section of brass tube was glued onto the end of the displacer rod, flattened and drilled like the power piston to provide a joint for the beam conrod.
I also cut out the bottom of a tuna can and glued that around the top of the displacer cylinder to use as a water jacket for cooling, but this was actually less effective than plain air cooling, and developed a leak that was letting water into the cylinder so I removed it.
Step 7: Connecting Rods
The conrods are made of coathanger wire. Where a joint is only required to rotate a small amount these are simply 90 degree bends in the wire fit into 2.5mm holes, with a dab of hot glue on the end to keep the wire in place. Where the conrods make a continuously rotating joint (where the power piston and beam conrods attach to the crank on the flywheel) these were made of drilled brass pieces from a section of "terminal block" electrical connector.
These are a very convenient size and shape to join the end of a piece of wire perpendicularly to another piece. One of the screws was removed and a hole drilled sideways all the way through the brass, and the other screw used to clamp the end of the conrod in the connector. I got this idea from reukpower's Coke Can Stirling Instructable.
The conrods all have a Z-shaped bend in the middle which allows for length adjustment by tweaking the bends.
Step 8: Framework of the Engine
Before building anything I drew a diagram and worked out the necessary dimensions of the engine so that nothing would collide, then dry fit all the pieces before cutting and gluing. The base is made from a piece of scrap decking. The beam is a 250mm section of aluminium strip with a hole drilled for a pivot in the middle and two smaller holes near the ends to accept the conrods. The beam support and engine support were made of more pine, screwed into the base.
Despite working out all the dimensions beforehand, my apparent inability to drill a hole straight through a piece of wood coupled with my cheap wobbly power drill resulted in a certain amount of trial and error being applied to the placement of the engine parts.
Step 9: First Run!
Step 10: Design Tweaks
After the engine had run successfully, I addressed some of the issues that had become apparent. The flywheel support wasn't in quite the right place, so the piston conron was running at an angle creating excessive friction on the crank. The flywheel itself wasn't really heavy enough to sustain rotation of the engine, so I added the CD and pennies to give it more momentum. The beam and flywheel tended to wobble on their mounts slightly so I added some spacers on their axles to keep them in place better.
After all these mods, the engine runs more reliably than any fuel source I have to test it with :) It will run at approximately 150-200rpm on a decent candle flame, and has run at nearly 500rpm when I accidentally overheated it slightly with a large meths burner. The engine is mechanically sound at that speed- my concern is the displacer overheating and the epoxy that keeps it attached to the rod failing.
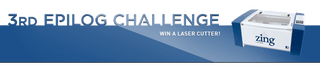
Participated in the
3rd Epilog Challenge