Introduction: Tooled Targe (Shield)
The targe is a round shield that was used from the dark-ages up to the 17th century all through Europe and is the root for the modern word target. It was especially used by the Scott's and some examples were said to even stop musket balls, though it was traditionally used for cover from arrows and in hand-to-hand combat. The targe was the main line of defense for a Scottish solider and was a center part of the feared Highland Charge.
The Highland Charge was done by a line of men with their targe and dirk in the left hand and basketed sword in the other. They would charge at the enemy line screaming and bash aside the first row with the targe usually killing them with the dirk held behind in a single upward sweep. They would attack the second line simultaneously with their sword by hitting anyone to close with the basket and skewering anyone else with the blade. This was a devastating tactic that was hard to overcome until the invention of the musket, and even then it was still successfully performed many times, just with greater casualties.
This targe is more of a decorative item and great for LARPing, being seen at Renaissance festivals, or just hanging on a wall! Theoretically it could be made for use and is fairly hardy but does not incorporate some of the more cumbersome steps originally taken to make them war ready such as making the plywood and stuffing the inside with wet wool or sometimes a steel plate. If you want to know more there is an interesting discussion here and of course Wikipedia.
I will also state before you read to far that this is a pretty involved project and while the pattern I started with was only two pages it was nowhere near complete in showing the real steps to make this. I have tried to put all my research and additions in as completely as possible.
Step 1: Plan
This step is very important and should be given some time and thought to consider what the finally product should look like. For this project I used Tandy's Targe pattern, and it can be downloaded for free on their website here, however, I changed the pattern somewhat to fit what I liked better. My only complaint is that the instructions are very minimal. Luckily you won't really need them ;)
The first design element to consider is the overall size which will affect the weight. I chose to make mine a bit smaller than the pattern called for, and closer to traditional size anyway (18-20"), so it would not be as heavy since I will carry it around at a Renaissance Festival.
Also consider what tooling design will be placed on the front or if there will be any tooling done. Patterns can also be made with brass studs giving it a traditional look. I choose to tool my leather mostly as a chance to tool a large project. I followed the Tandy pattern fairly closely but didn't like the original design that was at the top of the cross sections; so, I created the interwoven thistle knot to replace it. I'll give more detail on pattern making in the next step.
Parts List:
- 3/4" Hardwood Plywood Circle
- 6-7 oz. Veg Tanned Leather (best from a shoulder) can be thicker as well
- Backing Material : Sheep/Goat Skin or Cow hide or Smooth 3-4 oz. Veg Tan
- Upholstery Tacks (100+, more the better!)
- Brass D Rings or O Rings (Can use Nickel or any color you want, depending on your design)
- Prep
- Neatsfoot Oil
- Saddle Soap
- Dye
- Finish
- Resolene
- Mink Oil
- Others possible
- Contact Cement
Additional Options
- Buckles
- Brass Rivets
- Studs or Spikes
- Center Decoration (Pewter Emblem or Brass Boss are traditional)
Tool List:
- Sliding compass
- Jigsaw
- Metal Square
- Drill and various bits
- Vector Software (Pattern Creation)
- Utility Knife
- Tooling Supplies (Depends on the tooling)
- Swivel Knife
- Beveller
- Backgrounder
- Modeling Tool
- Any specialty tool that is needed (mine has a rope boarder)
- Rawhide or Synthetic Mallet/Maul
- V-Gouge
- Stitch Grover
- Stitching Wheel
- Edge Beveller
- Bone Folder
- Clips or Clamps
- Various Clean but disposable Cloths
- Wool Dauber
Optional:
- Rivet Setter
- Stud Setter
- Oblong Punches for Buckles
- Strap End Punches
- Bowling tools to create a Boss
Step 2: Design
Before moving on to the creation of the product its best to make a pattern to scale and make sure the sizing will look the way you want. I used GIMP but any vector or image program like Inkscape , both are free and very good, can be used to make and produce the pattern. Here are the steps I took for this part:
- Scan in any existing pattern, usually only a quarter of the circle
- Change or add any parts of the design
- Fill in the entire circle and make sure design lines up
- Clean up
- Expand up to a finished size
- Test
Since I used an existing pattern it was easy to take that pattern into GIMP. I then erased the portion that was not what I wanted and drew in the new pattern. Then copied the entire pattern to a new layer. Making a new layer helps to control what you are selecting and turning the pattern. Turn the pattern 90 degrees and make sure to line it up. Repeat to fill in the circle. If there are any lines that don't match up make sure to clean theses up. If the design is a cross or square then make sure the pattern is in fact square and centered. Next, group the layers or flatten them so the entire design can be selected at once. Scale the image to the full size of the project and print. This can take a while and uses a lot of RAM and processor using GIMP, other programs may handle this better.
The printing can be a little tricky, I exported the pattern to a JPEG first and used a program called PosterRazor which takes an image file and cuts it up automatically to print on regular paper, and it also automatically creates an overlap to help line up the pages after printing. It saves it to a PDF first which can then be printed. Once printed you do have to cut off the margin that it adds and then line up the overlap to make the full image. Use some clear tape to secure the edges and make sure that size is accurate as well. I had to play around with the image and the image percentage in the poster program to make the size right and I'm not really sure why. It ended up being at 104.5 percent to get it the same size as the image was in GIMP. Can't complain too much about free software though. After I finished this project I started using Inkscape and it works much more efficiently and can do the printing with out the extra steps and program.
Once you have the pattern put together, try making a cardboard or foam cut out of the core by adding at least a 1/2" to the farthest point on the pattern. If the pattern is the wrong size try making the it smaller using the percentage in PosterRazor. You want to have a very clear idea of the final size before cutting out the leather or the wood! Also do some test tooling of the pattern details. Any smaller sections or intricate details need to be large enough to be tooled and will affect the over all size. If you can not tool them the project will need to be larger or redesigned.
Step 3: Cutting the Plywood and Woodwork
Make sure to choose a good quality plywood to use for the core of the targe. If you use a cheap press board it will not cut smoothly and may bend, warp, or break later on when adding the leather to the project. Also I would not recommend using a solid wood plank either as these tend to warp over time. Good plywood crosses the grains as each thin piece is laminated making it very resistant to warping. I used a 3/4" oak plywood that I got at Home Depot or Lowes (both are close and I don't remember which one I used). It really is not to expensive compared to the other materials so don't go cheap just because it isn't going to be seen.
Cutting the Core-
Now that we know how big to make it, the next step is to cut our board. There are a lot of methods and some good instructables on the subject. Basically, you mark a circle and cut it out, either using a jig or just free hand. I tried making a jig and it fail (I'm not much for jig work) so I just cut it out carefully by hand. It does not have to be perfect as long as it is smooth and the cut is straight up and down, we'll be pulling leather against this eventually.
This is the end of this step unless you are adding a decoration to the front that has posts. I did and I'll go over this for a moment.
Decoration Jig-
The decoration I bought is a pewter circle with a thistle from Nagle Forge and Foundry, the back has two post that are soldered on to the body and take Chicago screws. Unfortunately, the post are not squared and I'd rather mess up some wood then my pewter. To be fair I'm sure that I could have asked them to fix this and they would have with no issues. So I had to make a jig to drill out holes that would allow the posts to be screwed in from the back. This will also allow me to change the decoration after the targe is finished if necessary, for cleaning, repair or to change it out.
I took a spare piece of plywood (same thickness as the circle) and marked the posts on the side so I could see the angle from the top of the decoration. After marking a center hole on the wood, align another piece of plywood to act as the jig on the finished piece. I carefully placed the drill on to match each angle and drilled out the angle with a drill and a 5/16 bit. This may not be the best way do this, but now I have a piece that can act as a guide for the drill and will make the same angle/hole pattern in the core. It worked fine on this piece, but if I do this again I'll get the post corrected or use a drill press that I can set at an angle.
Drilling-
You then take your jig and make sure it is lined up with the middle of the core and is positioned so that the top of the jig is facing where you want the top of your core. It really doesn't matter which way is up until you drill the holes, however, once you do, there is a Top and a Front of the core, make sure to mark them because it might not be obvious without fiddling and the wood will be covered anyway. Once drilled, dry fit the decoration with some scrape leather and make sure the screws will hold snugly, but not so snugly that it will be difficult to secure the decoration once finished. You may also have to widen the holes slightly if the drilling was either not perfectly precise or the screws don't want to sit correctly. Just insert the drill and run it while wiggling it back and forth a little. If the screws will not reach the posts of the decoration you will need to countersink the back holes so the screw head can go farther into the board or get longer screws. I found some brass screws that fit great and didn't use the original Chicago screws. Don't overdo the length or it will be very loose. Once it's dry fit and looks good it's time to get to the leather.
Step 4: Cutting Leather and Backing
There are a couple different ways to fit the leather to the core and they affect how much extra you add to the diameter of the leather. If you want the leather to bend around the edge of the core you need slightly more leather than just the diameter of the core. The extra will be bent over the edge to make a nice covered edge and meet the back. If this is how you want it to look add the thickness of the board plus about an 1/8" at least. You may also want to continue bending it around to the other side of the core to give it a really secure look and cover the edge of the backing better. This is what I choose to do because I was using a sheep skin as backing and the wool is slightly long and would look fuzzy sticking over the edge. If you use a smooth backing however, the other method will work just find.
Front Design-
First, determine the diameter you need to cut, since I'm going over all the way to the back I added 3/4" to go over the width of the core (if you used a different thickness make sure you add that amount) and then added another 3/4" for the wrap on the back. This is where I messed up! I found that the leather shrank just slightly after tooling and dying (not sure why). I would add more than you think you need because you can always trim it off later but can't add it back on. I didn't attempt to stretch it because the tooling is rather complicated and I wasn't sure how well it would work anyway. Instead I trimmed some of the core off to make it smaller (not ideal but better than scraping the project!) It just made the pattern closer to the edges than I originally intended.
Cutting-
Mark the diameter in a large single piece of leather that is free of scars or other major blemishes. If there are some slight stretch marks or nicks and bites, these will show up but add some character as long as they are not overly large or noticeable. Also make sure that if you are using a compass you place a small spare piece of leather to protect the surface in the middle from the point. If you are going to use a center boss or decoration then don't worry about leaving a center mark, it will show up on the finished product but be covered. This mark can also be very useful later to find the center and line up the pattern, core, and holes.
Once the leather is marked, use the utility knife to score the mark. Don't try to cut all the way though in one go because it will make the cut more jagged and make finishing the edges harder. Keep cutting in the same score until you get though and try to keep the cut on the outside of your line, better to be a little big than small! Once cut set aside and go ahead and cut out the backing using the same method. The backing will only need to be slightly larger than the core if you are folding the front over all the way to the back. If not, then make it the same size as the front piece. It will lay under the front piece on the side of the core.
Step 5: Tooling
There are lots of tutorials available on this site and others on how to do tooling. There are several on YouTube that really get detailed so just search for them. I will go over the basics here but you can skip this step as well.
Transfer Pattern to Film-
The first step here is to transfer the pattern to the leather. I ended up using 9 pieces of paper once printed out and taped together. Unfortunately this will make it very difficult to get a good mark from your stylus where the edges have two layers of paper or more, and tape. I was also worried that the paper would break up before getting the whole pattern laid down, since this is a large project and the leather will be damp. There are several options to avoid using normal paper. Tandy sells a tracing film that is thicker and more durable than paper. It's pretty cheap at 3 bucks a yard and you probably only need one yard. However, I found a more readily available and cheaper alternative. There is clear vinyl that is sold all over, got mine at Wal-Mart, for covering furniture when moving or in storage. It's completely clear making it really easy to see what you are doing and it's thick enough to be durable but thin enough to leave a clean mark on the leather. It came in a roll that was 30" tall and sold by the yard for $1.50. One yard was plenty and its reusable if you use a wet erase marker and don't get carried away with pressing in your stylus.
Trace the paper pattern to the film. Once it's all traced out you can get rid of the paper pattern or use it as a visual as you are tracing onto the leather. It can help to keep it for the next step so you make sure you are getting everything lined up and it's a little easier to see the whole pattern on paper. Also the wet erase pattern deteriorates as you scratch, so it will not be available as a guide.
Mark Pattern on Leather-
Next is transferring the pattern to the leather. Wet the leather all over with a clean sponge first and let it sit for a few minutes to soak in the water. Once it is returned to a normal color it should be very pliable and ready for taking marks. Be sure not to bend it too much while it is wet or it may crease. Also be careful not to mark it with your fingernails, rings, parts of your clothing; as the marks will be very hard to remove if possible. Begin at the closest part of the pattern so that you won't rub on the not-used part with your arm. The water removable marker will rub off with friction as you'll see when you use the stylus to transfer to the leather. The places you mark with the stylus will flake off and this is actually really helpful to know what parts are done and which lines may need to be gone over still. However, make sure that you are either wearing long gloves or you don't mind having some ink on your skin (do not wear long sleeves if you like the shirt). It makes a bit of a mess but will eventually come off with soap and water. I didn't realize this until after I was nearly done and had a stained forearm for couple of days. Do not get this on the leather as it will stain it.
Tooling-
Once all of the pattern is transferred and you are satisfied with how it looks it's time to get tooling. Use the swivel knife to cut out all the lines, then do the beveling. Usually you want to bevel any line that is not meant to look very crisp especially lines that will go into the background. Then do any pairing with the modeling spoon if needed. I used this in the leaves of the thistle to give them dimension. I also cheated a bit by using the spoon to create most of my bevels and just used a textured beveller in the crossings on the knots. Next, put in the back grounding and finally use any special stamps to put in texture features like the rope line or letter stamps. I do these last so I can easily see where they go and then clean up around them afterward with additional back grounding if needed. This step is probably the most time consuming because you do not want to let the leather dry out till it's done. You can always add more water later if needed but getting as much done with one casing as you can is best. I think that re-wetting the leather multiple times is why mine shrank up a little.
Punch Decoration Holes-
This is also the point where we need to punch the holes for your decoration to mount through. The easiest way to do this is take our jig from earlier and align it with the center mark on it and the leather. Then use a pencil to mark the hole position onto the leather. Make sure you are using the correct end of the jig! These holes should be exactly the same position as the one on the front side of the wood. If your mounting posts were straight then this might not matter ;) Mine were at about a 10 degree to 15 degree angle so 3/4" later they are quite a bit closer on the back than the front. Use a hole punch that is almost the same size as the post going into the hole, make it too big and the leather will not pull against the decoration correctly in the mounting step, to tight and you can't get it in. Then do the same for the backing making sure that the holes are for the correct side and the piece is aligned well to the outside of the core. If it is not then there will be gaps where the backing cannot reach the edge. Also make sure that the decoration fits with both pieces of leather attached and it can tighten down enough to be flush with the leather. If it doesn't or the screws do not reach far enough to get into the posts then you need to change the screws for longer or shorter. You can also counter sink the holes in the core to get the screws closer to the posts. If you do this then make sure the holes punched in the backing are large enough to allow the screw heads all the way though. You don't have to punch them at all but it is nice to leave a way to take off the decoration to change it out or repair it separately later on.
Once completed set it somewhere flat to let it dry and put a few books on top to keep it flat, if you do not it will curl or warp, and retain that shape making it harder to work with.
Step 6: Straps
The next step is to create straps and other items that will go on the back of the piece. These can be very plain or tooled. They also can be simple single straps attached permanently to the back in one section or have buckles to make them adjustable, or nothing at all. It all depends on how the targe will be used. You can skip this step if you are just hanging the targe as art. You may want to make a billet to hang the targe, so skip to that step below
Design Straps-
I made my straps to be one piece with no buckles. Mainly because I could not find any buckles I liked in a size that looked good to me. The strap that will go on your arm near the elbow should be larger than the front strap. Also the front strap is not a hand hold as some patterns seem to think. It should instead let your hand slip all the way through and sit on your wrist. This is so you can hold your dirk in that hand.
Measure Arm Band-
To figure out how long the straps should be you'll need some help. Just measure your arm by placing it on a table or flat surface then hold the tape about two inches away from the top of your arm and measure around it to about two inches away on the table. This tells you the minimum distance that the strap needs to go to attach to the targe and allow your arm into the strap. Add at least two more inches to this distance so there is some wiggle room. Mine turned out to be 18.5 inches long and 4 inches wide. This gives me plenty of room to place tacks to hold it on and still have room to fit my arm, and the width looks good. If it's a little loose that's ok too. If you are going to be using a buckle then you can be less precise on the measurement here since it can't be too long you can always trim the strap end. You will also need to cut an additional piece out to anchor the buckle and probably shape the strap in to accommodate the buckle or buckles.
Measure Wrist Band-
Next do the same procedure for the wrist strap. However, here the width should only be about an inch to an inch and a half. Also make sure there is plenty of room for your thumb to pass through when the strap is down or you'll have a hard time getting it on and off. I also used an additional strap the same width but not as long to line the back of this strap. This makes it much more comfortable to wear against the wrist and adds some strength to the strap as well. This strap is the only sewing that may be needed unless you are using buckles or make mirrored billets like I did. After dyeing cement the under strap to the top and sew it on as well. I won't go over the sewing steps because this is fairly straight forward but here is a great video that is very detailed. (Beware the video is 1.5 hrs. but well worth watching, full discussion on thread, needles, making holes, and sewing with lots of examples)
Billets-
Lastly, you need to make one or two billets. These are little leather shields that hold D-rings. The billets are to add D-rings to the top and bottom of the targe to make it easier to attach to a baldric or shoulder rig. If you won't be carrying this anywhere and just going to hang it on a wall you may only need one so there is an easy attachment point for hanging.
A billet is a piece of leather with a strap section and a shield section that is attached to a larger item. The strap section will be the size of your D-rings. In my case I used 1" D-ring and so the strap is 1" and then widens to a lip and then makes a shield. The shield can be any shape but must be large enough to stop the ring and make a good attachment point to the rest of the project. I mirrored my shield to strengthen the billet and make it more even. This is not necessary and you can just make a single shield then turn the strap over and rivet the strap trough the shield to close it up. If you use the mirrored billet then you just force on the D-ring then sew up the two sides together or to the backing leather. Both ways work and I'm not really sure if one is stronger than the other but I choose to mirror because I didn't want a rivet alongside the upholstery tacks and was afraid that just tacks might not hold. These billets will also be sewn onto the backing to increase their strength and not rely on the upholstery tacks alone.
If you are going to do any tooling on the straps then this is the time to do it. Follow the process in the previous step and you're ready to move on. I tooled a simple Celtic knot on to the armband but put nothing on the wrist band.
Step 7: Dyeing and Finishing Leather
This is another well covered topic but I'll explain what I did to get my results. Make sure to do each process the same on every piece of leather at the same time. If you skip a step on one piece or wait and do it much later you will not get a consistent look between the pieces. I also suggest writing down exactly what you did so that if you do need to repair or replace a piece later you have a chance of getting it close to the same finish.
Prep-
First, before dying you need to prep the leather. I did this by rubbing all the pieces thoroughly with Fiebing's Saddle Soap which is a yellow glycerin soap. Use a cut up T-shirt or clean rag, NOTHING DIRTY! It does not need water and is just rubbed on and buffed. It should not change the color of the leather much but it will help to remove any oils your hands may have left while tooling. It will also help remove any marks from pens or pencil while tracing. Make sure to get it as clean as possible, any dark stain will show though and become impossible to remove after dying. This is especially true if you are using a light dye, if you go black or dark brown probably not going to matter.
Next, I applied a few coats of Neatsfoot oil to the entire front of the project and the entire back, using some more clean cloth. Don't use too much oil! It is a softening agent and helps to add back in oils that have been lost during casing and tooling, it makes the leather supple and flexible but can make it limp and soggy if you use too much. If the leather is very dry you may need to add more OR if it is already supple and flexible you might just skip this step. Let the oil sit for a while to soak in and even out. You might notice it looks splotchy right after rubbing it in but it should look uniform after a few minutes; if not add a little more to the dryer areas. This will darken the leather slightly and give it a yellowish tint, if you want to keep the leather very light be careful when applying this or don't use it at all.
Finish the Edges-
Use the Edge Beveller to take the hard edges off all the exposed edges. This will make the edge look rounded once burnished. Place the tool at a 45 degree angle at the corner of the leather and push smoothly along the edge. If the edge will meet up with another piece of leather like the backs of the billets then don't edge them. Also the edges of the armband and wrist band where they will be attached to the backing should not be edged, but all of the top edges should be.
Burnish-
Before dying you may want to burnish the edges of each piece, especially the larger strap that rests on your arm. To do this take some of the saddle soap on your cloth or canvas/denim and rub the edges vigorously. After a moment you'll notice that the edge gets nice and smooth, darkens a little and gets shinny. If the leather is very rough then first use a few different grits of sand paper to smooth it down. However, since its only one layer of leather as long as you cut it properly and it's a good quality leather you shouldn't need to sand. Using this method the edge will still take dye; not as readily as an unfinished edge but it will not make much of a difference.
Dye-
Now dye the project. There are lots of different dyes available and each has its own method to apply to the leather. If you want this to look old or traditional using a Gel Antique will give a nice varied surface color and is very easy to apply, that's what I used to get this brown color. Also select a color that is somewhat dark or neutral, there are some examples of targes that were dyed red but most were natural colors or not dyed at all. But again it depends on how you are going to use it: Ren Faire- probably a natural and traditional look, ComicCon - Bright and flashy, LARPing or Fantasy somewhere in between?
Make sure to wear gloves and cloths you don't care about it stains everything! To use the Gel Antique you just put some on a dry sponge, cloth or piece of wool and rub it on, then take a paper towel and rub it off. I wanted mine to be a little lighter so I wet my leather first, this acts as a resist for the Gel Antique because it is water based, it also helps to make it a little smoother without the need for multiple coats that would darken it more than I wanted. The antique is nice because it leaves a varied looking finish, this helps hide imperfections in the leather, and it looks aged and warm. It will also leave a very nice contrast in the tooling impressions that make the detail stand out. However, it will highlight any stray marks that are left in the leather so hopefully we have been careful up to now or there is enough tooling around it to blend in. Make sure to coat the edges as well and you can also dye the back of the leather if it will be exposed; like the armband. Let the project dry completely after dying for at least 24 hrs. Then buff off any excess dye with a dry cloth.
Finish-
Lastly you want to treat the leather to soften it again, dying will harden the leather some, and to add any protective finish you may need. Neatsfoot oil can be applied again or a nice leather cream. The cream acts as a protective and a polish giving the leather a nice glow. After this is dry you may want to apply something to "waterproof" the leather. A good choice is Fiebing's Resolene, which will seal the leather and give a nice water resistant finish.
*It's almost impossible to really water proof leather, but you shouldn't go swimming with it anyway. You can impregnate the leather with bees wax and that will be as close to waterproof as possible, it's how to make leather canteens. But that will make the leather pretty hard and ridged making the next steps very difficult, save it to the very end if you want to try it.
Whatever you use make sure it won't ruin the existing dye by making a test piece first, better to ruin a small scrap and waste some time that ruin the whole project. I did some tests and it turned undyed and dyed leather VERY dark brown, also it cracks when bent leaving a very light color in that spot with lots of variation. If that's the look you want dipped in bees wax is the way to go, otherwise avoid it.
Let the finish also dry before moving on to the next step just like the dye.
Step 8: Placements
This step can be done during the design phase but is a bit easier when you have the actual straps and can see them as there is some custom fitting to this. We also need to determine where the straps and billets will be placed on the backing. This can be saved to almost the end but it's always easier to change something earlier in a project than get everything finished and realized you left something out and it's too late to change it without making a compromise to the way the product looks or functions.
The straps will be held on either side by just tacking the ends on to the core after mounting the backing or can be sewn on to the backing before it is mounted and then tacks added. In either case the placement of the straps is very important for three reasons. First, the targe should be centered when held up so the straps should be placed so that the targe is held at the correct position and the tooling if any is straight. Second they need to be spaced so the strap is loose enough for the arm to slide in while still being tight enough to grip. They also must be placed apart from each other to match the position your arm and wrist correctly, if they are too far away then you can't get the strap over your wrist or to close and the arm band is not tight in your elbow.
Horizontal Placement Armband-
The first thing to do if figure out how far each strap should be from each other, this is the most important thing. Place the bands flat on a table and just place your arm over them. There is no reason they have to be on top of the arm yet. Position the arm band crossing your arm just beyond the pit of your elbow towards your elbow. This will help make the positioning tight so you can pull against the wrist strap. However, don't get to close to the elbow or your wrist strap is now a hand hold and will be very uncomfortable, plus no dirk wielding.
Horizontal Placement Wristband-
Next place the wristband across your wrist right before the bulge of your hand. There will be some play in each strap when it is circular so it will give to the inside. Now remove your arm carefully so you don't move the straps and measure between each one. It should be perpendicular but make sure by measuring the top and bottom and middle. If it's not perpendicular readjust with your arm in place until it is squared up. Again it is better to make it a little wider than closer since there will be play in the straps.
Vertical Placement Armband-
The next and equally important measurement is how far does each strap need to be placed to give you a tight enough pressure to stay connected, but not so tight that it's hard to get your arm in and out of it. To do this you need an extra set of hands since one of yours will be stuck under the strap. If you can do it by yourself let me know how. This is really just trial and error with each strap. Place it under an object about where you think the sewing and or tacks will hold it down and wrap it over the arm about where it should sit. Then hold down the loose end with you other hand about where it becomes tight. Make sure your arm can slide in and out fairly easily with what you will normally wear when using the targe and add just a little slack. You will notice that there might be several angles that work, just try them and see what looks and feels the best. Make sure though that you leave plenty of room for at least two rows of tacks to attach it, about 1 1/2" or 1 1/4", on each side. Measure using a square rule on both sides and make sure they are the same.
Vertical Placement Wristband-
Next do the same thing for the wrist strap, this is a little trickier because you can get it pretty tight on your wrist but then it is not possible to get your thumb back under the strap. You have to make this one a little loose or add a buckle. I'm leaving it as a single strap because I don't have any buckles handy and I think a single buckle would look odd. If you can keep the arm band in position while adjusting the wrist strap and have keep them apart by what we measured earlier you can play with that fit. You may find that you need to move the wrist band out a little further with the amount of play left or move if back in for comfort. This is where the extra person is most needed. It's fairly easy to keep one strap working while a clamp or heavy object holds the other end but nearly impossible with both straps. Make sure to move your arm in and out as well and simulate the motion of putting on the targe, if you can't do it with it on the table you won't later with the targe.
Relative Placement-
Once you have all the measurements it is helpful to make a quick template out of paper or wood to be able to transfer to the core/backing. It will also help make sure the straps will set on the backing completely and in a position that centers the targe while held up. Remember when deciding where to place the top of the straps that the natural way the leather will bend with the targe weight will be down and away from the top, meaning you may need to place the top of the straps a little lower to compensate. If the targe rides a little low it's certainly not the end of the world. Also make sure that the straps will be placed so that the tooling is presented straight. If the angle of the arm is not perpendicular to the top of the targe it will twist the entire thing and makes the tooled image look lopsided or turned.
Billet Placement-
Lastly decide where the billet will be placed, this can be save to the very end if you just tack them on; but if you want to sew them on, it will be important to do this before mounting the backing as it won't be possible then. Just placing them in a couple inches from the edge, top and bottom, should be fine as long as they are out of the way of the edge rolling over. The only real reason to worry about the placement of the billets is if you want the tooled image to be straight while wearing it on a baldric or something. Then it needs to match the angle that the baldric will set. However this makes the top billet unavailable for use to hang on a wall. You can fix this by adding a third billet at the top for hanging and the other two for the baldric. I didn't really find this necessary so I just put them straight up and down. The D ring should be placed up on both of them so the shield provides the most strength to hold up the targe when worn or attached to the wall, unless of course you want to hang it upside down. ;)
Step 9: Mount the Leather
Marking the Gouge-
First we put the leather over the front of the board carefully aligning the holes and attach the decoration to make sure it fits snugly. Note- if you tighten down the decoration to much at this point it will most likely leave a mark which might be visible after stretching the leather over the edge so be careful. Once it's on, flip the board over and lay the board and leather flat on your work surface (make sure it's clean and the decoration is not bent or in the way, you can use scraps of wood and leather to make a support if it is rounded). Use a pen to mark the edge of the core onto the back of the leather all the way around the circle.
Gouge-
Remove the decoration and the leather from the core. You should have a line all the way around the inside of the leather where the edge of the core will sit. This line is the first bend the leather will make to enclose the core. Use a V-Gouge to gouge just to the outside of the line basically on top of it. Make sure that the gouge is not set deep enough to penetrate the leather! We don't want to cut it off just make a channel that the bend can easily turn against. It should be set to about half the depth of the leather or a little less. The gouge is on the outside of the line because the thickness of the leather will pull the leather taunt and then set on the edge of the core making two 45 degree angles at the corner like a miter joint.
Marking the Tags-
Before we reattach the leather to stretch we can do one more thing to make it easier to turn the leather and get a cleaner looking result on the back. Take a string and push-pin and place the pin in the middle point with the string tied around the post. Use the string as a guide and every two inches from a starting point mark a line from about a 1/4" outside the gouge line to the edge of the leather. These lines will be cut so that the leather does not fold and warp when it is stretched over the edge.
Cutting the Tags-
Cut out the lines. Use the utility knife to cut each of the lines out and be very careful to not get to close to the gouge. First it could rip it and make that section very week, and keeping the cut away from the top edge will give it a nice smooth transition from front to side. Also don't go to fast cutting through the leather since we are now cutting from the back to the front we don't want to damage the finished side and mar the visible leather. Once cut you can also see how deep the dye has penetrated, it's pretty neat looking. If you want to go one step further you can also test bend the tags around the core to see where they will bend again, V-Gouge this mark all the way around the targe for the second bend and then cut out an angle so the tags lay smoothing next to each other on the back instead of overlapping; its best to wait until the front and backing are mounted to the core so you have the correct distance for the bend
Mounting the Front-
Once the slits are cut and we fix any edges that are not very neat, with burnishing and dyeing, we can mount the leather to the core permanently. First take the contact cement and apply an even coating to the entire front section of the core. Apply cement to the flesh side of the leather on the inside of the gouge line and just outside but not past the cuts. This section will help the curves we will make in a moment. Allow the glue to dry for a little while, however we do not want to let it get to the point where it is just tacky or not tacky anymore which is normal for leather craft, we want it to still be a little uncured so we can move it around easier. However, it should not still be fresh or very wet that could cause the leather to become wet and cause issues. Very carefully align the leather with your decoration holes or center mark and try to lay the leather as flat as possible in the first go not creating any air bubbles. If you do you should be able to still pick it up and try again. I used to wires pushed through the decoration holes on the core and the leather to help align it, otherwise they could be off and the decoration not be able to be mounted. Once it looks pretty flat take opposing corners and stretch the leather as much as you can. Do this for every tag all the way around so you get it very even and straight. Make sure there are no wrinkles or bubbles and that the gouge mark is visible from the back, if not go around again to stretch it over. Dry place the decoration to make sure it can fit into its mounting holes as you go so it does not get pulled out of place. Once it looks good take a piece of scrap leather and your mallet and lightly tap all over the front to set the glue. You can also place it face down on a large table and hit the back or apply pressure with your body weight. It doesn't take a lot but it makes it much harder to get it apart though it is still technically possible.
Mounting the Backing-
This step can be done before the front if you like, it shouldn't matter unless you are bending the backings edges around the side as well; in which case you need to Mark and Cut tags on to the backing. You will also need to turn the edges, which is the next section, for the backing first so they are under the front leather.
To mount the backing line up the holes punched for the decoration screws with their holes and make sure you know which way the back needs to be oriented. Basically follow the same steps as above, do make sure that the holes are aligned properly and in the correct orientation because unless they ended up perfectly center there will be a slight difference from top to bottom. You can also just attach the screws and do one side at a time since the fur backing will easily bend and make the process a little easier. If the front is already attached and mounted make sure to use a scrap piece of leather to protect the tooling when tacking down the cement.
Turn the Edges-
Now we can turn the edges on the side, it helps to have a small dish of water and a wool dauber but these are not required. Wet the inside edge of the back of the leather near the grove on one slit. Bend up the tag and use a bone folder to gently apply pressure on the fold and hold it there while moving the bone folder back and forth. This will encourage the leather to take this shape. If you applied bees wax earlier then this might be very difficult as it can make the leather hard and it might resist the water even from the inside. However, eventually it should mostly hold the shape when released, it will pull away but still stand on end. Use the same technique to fold over the top of the tag to the backing. Once it is holding its shape some what well, you can clamp down the tag into what should be its final location with pressure clamps, make sure to have a piece of scrape that is longer than the clamp face on both sides of the leather. If you do not have enough scrape at least make sure the front is protected. The clamps will create an indention otherwise and can even remove dye. Leave these in place for at least an hour but over night is best. Once removed the leather will hold the shape and be somewhat difficult to move away from the edge. If you can do more than a quarter at a time that's great, I just only had enough clamps to do that much at a time. Go all the way around until every tab has been wet formed into place.
Now we glue the sides to the core, gently pull back each tab and add some cement to both the core and the leather, try to keep them separated until the glue is tacky and then stick them back together. Only glue the core and the leather touching the core, not the flap that goes over the wool. This will not stick and will end up making a ugly mess, it will be secured with tacks. Give a good tap to each tab with the mallet and a scrap leather buffer.
Step 10: Tacking
The last step is to add any tacks that will be needed either for decoration or to strengthen the fold over or hold on the straps. The upholstery tacks come in a variety of finishes and styles but basically look like small nails with a rounded domed head. I used antique brass tacks to match the rest of my hardware. The easiest way to apply a tack is to either hold the tack in a cut on a scrape piece of leather or even better at the very end of a pair of needle nose pliers. Tap the tack in evenly and carefully as they sometimes bend as you hammer moving off of position. If this happens you can either try tapping it back into position (which gets harder the closer to the surface it is) or pull it out and try with a new tack. Just go slow and you can get everything lined up nicely.
Tabs-
Place at least two tacks on the back of each tab to secure the hold and add an authentic look. I suggest placing as many tack as will fit and not look crowded, these will ultimately be what hold the front leather on for the life of the targe. Do not trust that the glue will hold forever!
Decoration-
Tacks can also be used on the front and the side as decorative items and further strengthening points. If you are not bringing the leather around to the back then you will have to have tacks on the side to do the same job as they would have done on the back. Traditional targes would have had at least some studs on the front to help deflect and slow blows from arrowheads and swords, the side would have as well for catching sword and axe blades. Make sure to add the front decorative tacks before the straps since once the straps are added it will be more difficult to get a good flat surface. Also when hammering near your tooling and front facing leathers make sure to protect the surrounding area with a scrape piece, hammer marks will be permanent.
Test place the tacks and make sure you know how many will fit in a given area, if they will be closely placed then this is very important so it will look even. If they will be spaced wider mark out where each tack will go before putting any into the leather.
Straps and Billets-
Tack on the straps and the billet in your predetermined locations. If you have sewn anything onto the backing you should still use tacks to give it a uniform look and to provide added strength to that section. The sewing is great for spreading the stress over a larger surface but the tack give vertical strength because they pierce the wood and press over the top of the article making it harder to rip up or out.
When tacking the arm band use at least two rows of tacks alternating so they form a comb looking pattern and give the tightest layout. This can help squeeze in a third row if there is room and provides the most strength. The armband is probably the most likely part to rip off since a majority of the weight is held by this strap, except the top billet when hung. Pay careful attention to these locations so that they are as strong as possible or the targe will not last as long or need repair sooner.
On the arm band and billets use at least three tacks in a triangular pattern at the strap ends. More is better in this case as long as the tacks all can sit down on the leather and get a good grip into the under lying wood.
Test the spacing of the two straps to make sure they still fit and are comfortable and hang as expected. If it does not simply pull out the tacks and re-position the straps. The wood is not visible and the fur will cover any holes, if using a smooth backing be very careful when positioning the straps because any rearranging will be visible in the leather.
Step 11: Last Details
Before running off to show off your work, you may want to touch up the finish. At this point you won't be able to change the dye much unless you cut into the leather accidentally, just use a wool dauber or cloth to run on a little dye and then off with a paper towel and that should fix any nicks. Make sure to also put another daub of Resolene on top to seal and waterproof.
Bees Wax-
You could also do a bee's wax coat to try and really water proof the targe, this will darken the leather though and Resolene should not be used if you plan to do this. Don't do it on the fur side, however, since that will matte it down and look very ugly. The best way to do this on a select area is heat up the wax and pour it on to the area that you want to coat. Use a heat gun to keep it warm so it will soak in and then rub off any left over. This can get messy but is fairly easy to control if the wax is not very runny when pored and heated up mostly on site with a heat gun. Do be careful not to touch the leather with the heat gun or let it get very hot while using the heat gun. This could burn, scar, and/or harden the leather. Attempt this step on a scrap piece first! Otherwise you could ruin all the hard work put into it. Once finished the excess should buff off with some elbow grease and leave a slight honey smell to the leather and a shine. This is the only finish that is needed.
Polish-
You can also use several different compounds to polish the surface and give it a little shine. I like to use Mink Oil paste as it smells nice and gives it a shiny matte finish and adds to the water resistance. Rub it on and let it set for a little bit then buff off really well to shine and seal the tacks as well.
Enjoy!-
Now show off your awesome targe, go to battle (fake I hope), or hang it on the wall!
Let me know what you think of the project and if you'd like to see more! Also please let me know if you liked the amount of detail in this instructable or if it was too long! Like I said it's my first attempt, and it drove me crazy trying to figure all this stuff out with only two pages of instruction, and the internet!
I'm also starting to plan out making a back baldric to carry my targe and a sword frog to go along with it. I'll post when I'm finished with those projects.
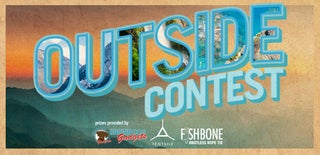
Participated in the
Outside Contest