Introduction: Turner's Cube (Manual Machine)
Once upon a time, one of my teachers at school brought in a Turner's Cube. He showed it to us, as well as the cube with a sphere in it. He was showing things that you could make on the CNC machine, and I thought the cube was amazing. I knew I wouldn't be able to make a sphere on a manual machine, but a cube within a cube within a cube? That didn't seem too bad!
And so the quest began! I began researching Turner's Cubes, and I found information about CNC projects, turners cube calculators, and all that jazz (I even found some that this guy was making on a wood lathe, with all sorts of amazing shapes inside. Dodecahedron's and the like). But nothing on a manual machine! Something had to be done. I figured out how to make one, made a few prototypes, and once I got a nice one done I came here to share it with you! Here is an Instructable on how to make a Turner's Cube, on a manual lathe (and mill). I'll go through the calculations and everything, so you can make one of any size with any number of cubes!
I think this is an appropriate entry for the "Make it Real" challenge, because this is a project that is hardly ever done on a manual machine, it is usually made on a CNC machine. I believe that making something with your hands and on manual machines "makes it real" more then programming a robot to make it for you does. I made models in Google Sketchup and Autodesk Inventor, and have attached the files here.
This project is actually not as hard as it looks, so don't get discouraged by how complex it looks. Here are the skills you need to be able to make this:
- Working within a +/- 0.005 in tolerance (any more and it looks off)
- Dialling in a milling machine (to as tight a tolerance as you can get it, 0.001-0.002 is the goal)
- Using a face mill + planar bar on a mill to make the cube
- Facing cuts on a lathe
- Boring flat bottomed holes on a lathe
- Undercutting on a lathe
- Know how to dial in work pieces on a 4 jaw chuck
All in all, this is maybe an 8 hour project. Once you get all the tools ready, and know what you're doing, it's less then an hour a side. (times 6 sides, and the the time to mill a cube)
Tools/material needed:
- Aluminium stock
- Milling Machine
- 3 in face mill
- Planar bar
- Bandsaw
- Lathe with a 4 jaw chuck (or some sort of fixture to hold the cube, 4 jaw is easiest)
- Grinder (for making the HSS tools)
- Dial indicator with a magnetic back
- Dial indicator with a magnetic base
- Live centre (to set your tool heights to centre)
- Drill chuck (to hold the drill bits)
- Tool holder (for your HSS bits)
- Boring tool for the lathe (I'll show you how to make one out of High Speed Steel (HSS))
- Undercutting tool (again, I'll show you how to make one out of HSS)
- 90 degree chamfering tool (made out of HSS)
- Countersink to reach the smallest hole (5/8, if you use my numbers, if you make your own numbers, you may need smaller)
- Drill bits (to help rough out the bores)
- Files for deburring at the end
- Measuring tools (calipers or micrometers and telescopic gauges. I like calipers)
Step 1: Calculations
WARNING, TRIGONOMETRY AHEAD!!!
To start out your Turner's Cube, you need to figure out how big you want it to be, and how many cubes you want. 3 cubes is a good number to start with. But you could make any number. These calculations are a guideline, and an example of how I made it. Substitute your own numbers to make your cube unique.
To start, we had 2in x 2in aluminium stock. So the cube was going to be less then 2 inches. 1 7/8 (1.875) seemed like a good size to make. I wanted 3 cubes, so I took 1.875 and divided it by 3, so I would know how big each cube will be. 1.875/3= 0.625, so the size difference between each cube will be 0.625 (5/8). The cubes will be 0.625 (5/8), 1.250 (1 1/4), and 1.875 (1 7/8). Now I needed to figure out how big the bores are going to be.
When calculating the bores, you need 2 numbers. One will be the diameter of the bore, and one will be the diameter of the undercut. The diameter of the bore has to be smaller then the corner to corner distance of the cube that will be contained within, and the undercut has to be bigger.
So, for example, my smallest cube is 0.625. The corner to corner distance on this cube is 0.884 (Pythagorean Theory, A^2 + B^2 = C^2). So, the opening of the bore has to be less then that, and the undercut has to be greater then that. I made the bore opening 0.750. You can open any simple modelling software (Google Sketch-up is nice, and its free!), and draw your cube, and then draw some circles on it to see what size looks good. The undercut I made 0.200 bigger, so the diameter was 0.950. The bigger cube is 1.250, so there is still plenty of material left.
Let's repeat the calculation for the next size. The cube is 1.250, so the corner to corner distance is 1.768. (sqrt(2*(1.250*1.250))). The bore opening is 1.500, and the undercut is 0.350 bigger, so 1.850. As for the smallest hole, you can usually just use a drill bit. Again, draw some circles and see what size would work, then pick a nice drill bit. I used 9/32.
Now we need to calculate the depths of the bores. To do so, we need to calculate the red distance, and the green distance. (Picture #1) For the red distance, take the biggest cube (1.875) and subtract the smallest cube (0.625) to get 1.250, and divide that by two, since we're only working on one half of the cube at a time. So the depth of the first bore is 0.625 ((1.875-0.625)/2 = 0.625). For the second, take the biggest cube (1.875), subtract the middle one (1.250) and divide by two again to get 0.3125, rounded to 0.313.
Now we have all our dimensions! The cubes will be 1.875, 1.250, and 1.625. The hole in the middle is 9/32. The bores are 0.750, 0.625 deep, with a 0.950 undercut, and 1.500, 0.313 deep, with a 1.800 undercut.
Onwards to construction!
Step 2: Making a Cube
To make a cube on the milling machine, you first have to dial in your machine. Since this shouldn't be your first project, you should already know how to do that.
So begin by dialling in the milling machine and the vice, then take your aluminium stock and lets get started! It's good to get long stock (my stock was 2x2x6.1) so that you can make multiple cubes at the same time. I made 3 cubes in a little over an hour.
So to begin, we start with our 2x2 stock. Place it in the vice, and hammer it flat so that it is laying flat on the bottom of the vice.
Note: You may need parallels for this step. The vice jaws I used were 1.75 in, and the cube was going to end up at 1.900 in, so I thought that I needed a little more clearance and used parallels. Parallels are also useful, because you can wiggle them to see if the cube is really flat, if they wiggle, then the bottom is not parallel to the bottom of the vice.
The stock begins as 2x2, and we need to get it to 1.900. So 0.050 must come of each side. Begin by touching off with the face mill, and cut 0.050. This should give you a nice machined surface along the top of your stock.
Note: Whenever you make a cut on the mill, you have to deburr your part, so the edges that are built up after cutting don't mess up your squareness. Make a few file passes along each edge after each cut, before you put it back in the vice.
Now, on to side 2! Mark what number each side is on the end with a sharpie, so you can keep track of what's what. Place side 1 against the solid jaw of the vice, and use a planar bar this time to hold it there. This makes it square, because even if side 4 (the one opposite side 1) is all messed up and not square, the planar bar only touches on the point of tangency, and forces all of side 1 to touch the solid jaw of the vice. Since the vice is dialled in and square, and side 1 is smooth since you just machined it, then that forces the face mill to be perpendicular to it, so that when you make the cut on side 2, it ends up perpendicular to side 1!
That was a large explanation, lets just make the cut. Touch off on side 2, and cut another 0.050!
Now, rotate the part 180 degrees, so side 1 is still facing the solid jaw, and side 2 is facing the bottom. At this point, you can check for squareness. The vice should be square, and therefore the part should be square, unless you have a bad vice. If your vice is not square you can fix it by adding shims. If the angle is greater then 90 degrees, place a paper shim on the bottom of the solid jaw, if it is less then 90, place a shim on the top of the solid jaw. This will push the block over, so that the cut will be perpendicular, even though the vice is not. For a more permanent fix, you could mill the faces of the vice square, but be careful, vice faces are usually hardened steel.
When side 1 is facing the solid jaw, and side 2 is facing the bottom, then side 3 is facing up. So measure the cube (side 2-3), and make the cut to get it to size! Should be around 0.050. Use the planar bar again for this cut.
Now, turn the last side (side 4) to the top to cut that as well! Measure, and make your final cut to get side 1-4 to size. Now you have a length of stock with 4 square sides. You don't need the planar bar for this one.
At this point, if you have a long piece like I had, take it to the bandsaw and cut it into chunks. Leave about 0.100 extra to be machined (so you have 1.9 x 1.9 x 2 cubes). Take your cubes back to the mill for the squaring of the last 2 sides.
You can place the cubes beside each other to do them at the same time. Since they were cut at the same time, they will have the same measurements, so the vice will hold all of them equally tightly. Place your blocks in the vice, and use a square to make sure that they are.... square! The vice will hold them tight, and not allow them to rotate around the Z or X axis, but they can still tip side to side and rotate around the Y axis. There is nothing holding them there, so press the square against the bottom of the vice and against the side of the blocks to make them square, and tighten the vice.
Touch off on the top of your cubes, and make a cut so the entire top is a nice machined surface. I can't tell you how much to cut here, just measure how big your cubes are after band sawing, then cut half of that here.
Flip the cubes 180, square them up again, and make your final cut(s) to bring them to size. Now you have some cubes, ready to be turned into more cubes!
Step 3: Making Tool Bits
Now you need to make your tool bits for the lathe work. Grab some High Speed Steel, a smaller piece (I had a 3/8 HSS tool holder, so I used 3/8 HSS. It was a good size) and a bigger piece, 1/2 is a good size for the bigger piece.
To make the tools, there are some terms we need to know first. I'll go over them quick here, you can find more information by googling about lathe tools. Here is a nice little video: http://www.youtube.com/watch?v=Mn9jpqI8rao
Side rake: On top of the tool, the angle that the chips slide down after they have passed over the cutting edge. You want it smaller, because if it is too big an angle, the cutting edge gets too sharp and will break. 8-12 degrees is good for this.
Back rake: Is similar to side rake, except it goes back towards the body of the tool, instead of off to the side. Again, 8-12 degrees is good.
End relief angle: This is the angle under the cutting tip, and it is there to make sure the front face of the tool doesn't rub along your cutting surface. 10-15 degrees is good
Side relief angle: Is the angle that is on the side of the cutting tip, which makes sure the side of the tool doesn't rub as the tool is feeding into the material. 10-15 degrees is good.
End cutting edge angle: The end angle that makes the point of your tool.
Side cutting edge angle: The side angle that makes the point of your tool
Nose radius: The nose radius determines how nice of a finish is left behind. It is the blend between the side relief and the end relief.
Now, take a look at picture number 1. It shows the 90 degree chamfering tool, and the boring tool. The boring tool is not the prettiest, I know, but it works. You can see in the paint drawings what it would look like if it was perfect (or as perfect as paint drawings can get....)
When grinding HSS bits, rough grind all the angles first, then finish them up on a finishing wheel. You don't want any metal discoloration, and theoretically you shouldn't if you are using the grinding wheel correctly, but just in case, rough grind everything, then finish grind the last little bits to remove the discoloration (if there is any) at the end. It's also good to use a finishing wheel, and maybe even a honing stone at the end.
First, we'll go through the chamfering tool. It is quite simple. Take your HSS, and place it on a 45 degree. Tilt the backside down, so the tip is lifted. This will create your side relief, end relief, and side cutting edge angle, all at once. Look at picture 2, you can see how the HSS should be tilted. Grind the 2 45 degrees (the black lines on the red HSS) to get your 90 degrees. And that tool is finished! It has no back rake, nor side rake, nor any nose radius. Keep the tip sharp!
Second, we'll make the boring tool. This tool needs end relief, side relief, end cutting edge angle, side cutting edge angle, back rake, side rake, and a nose radius! But don't fret, we'll get it done. For this, it would be nice to set your tool rest on the grinder to about 10 degrees, it makes making the nose radius a lot easier. The paint drawing may not look exactly like the tool in real life, that's because my tool is a little funky looking. Just follow the pictures, understand the concepts, and you should be fine. Honestly, since this shouldn't be your first lathe project, you should know about tools already, so what I'm telling you should be stuff you already know.
Any ways, on we go. Check out picture #3. Here we are grinding the end relief angle, and the end cutting edge angle. Hold the tool off to your right, and rest it on the tool rest.
Picture #4 shows how to cut the side cutting edge angle, and the side relief angle. Place the tool on the tool rest to cut the side relief, and tilt it to the left, to cut the side cutting edge angle.
Now, to cut the nose radius, simply do a quick sweep from the angle in picture 3 to picture 4 (top view) to round off the tip. This is where it is nice when the tool rest is set on an angle, because you can rest the tool there (who woulda thunk it?!) and get a smooth radius. It's hard to make a smooth nose radius when you are holding the tool in the air, and trying to keep it steady.
Last but not least, the back and side rake angles. See picture #4 again. The position that you hold the tool in is very similar, but you rotate the tool 90 degrees, tipping it towards the wheel, so you are working with the right side facing you, and the top facing the wheel, as opposed to the left side facing the wheel, and the top facing you.
Finally, see picture #5 to see the front, side, and top views of the completed tool. The black curves would be good to grind off, because we're working on cutting a circle, and we don't want the bottom rubbing. It will shrink the tool a little bit, and make it weaker, but we are cutting aluminium, so it should be fine. If you are making a cube out of steel, then just don't go nuts and make super heavy cuts. Up to 0.015 (0.030 on the diameter) cuts should be fine.
In picture #6, we can see the tool in real life, with all its grinder marks and dings on it.
The last tool we need is the undercutting tool. It looks like picture #7. It's basically a parting off tool, on the end of a stick. So the first step, is take the 1/2 HSS, and grind a thin section in the middle, so there is a big fat section on one side, and a small fat section on the other. Let's get some specs on this, so we know how big to make it. From the tip of the tool to the big fat bit, it needs to be at least as long as your deepest bore (6). My tool is really long, it's a bit excessive. The amount that the tool sticks out should be at least as big as half the diameter of your biggest undercut (5) (for example, the deepest undercut on this cube is 0.300, so the tool needs to stick out at least 0.150. Mine is about 0.250, so plenty of room.) And, the entire end has to be small enough to fit inside your smallest bore (this shouldn't be a problem unless you make a really small bore.) Check picture #9
Instead of repeating everything I wrote for the boring tool, I'll just tell you what to grind, and hopefully you learned how when you made the boring tool.
1) Start by grinding the very front of the tool, grind the end relief and end cutting edge angle. (2)
2) Next, grind the back rake (4)
3) Grind the end relief angle (3)
4) Grind the relief angle opposite the first one (near 5 in top view, the 2 on the right in side view) Between grinding this and the first step, get your tool width (1)
5) Grind the radius on the bottom (7)
6) Grind a tiny tiny nose radius on the tip. You just want a little one, because how big this is affects how deep you need to undercut. If its a perfectly sharp corner, then you need to undercut just a few thousandths of an inch bigger then your corner to corner distance, but if you have a radius that is say, 0.050, then you need to cut more then 0.050 when you're undercutting, which means the undercut needs to be 0.100 bigger on the diameter. If you check our calculations, the undercuts are about 0.070-0.090 bigger then the corner to corner distance, so we can afford a 0.030 radius (~1/32 on an inch). But even still, smaller is better. Try for a 1/64 radius.
And voila! This was a huge long step, but now you have your three tools. We can proceed with the cube!
Step 4: Dialling in a Cube
Now. lets get started on the actual project! I've seen some fancy cube holding jigs and fixtures on the lathe, but I didn't want people to have to use those if they wanted to make this. So I made this in an independent 4 jaw chuck.
Before we do anything, we have to dial in the cube. It's not so hard.
1) Place the cube in the jaws, use shims. Keep the shims flush with the jaws, so there is room to use the dial indicator.
2) Set up the dial indicator so it rests in the centre of the cube
3) Rotate the chuck side to side slightly, to see the needle moving side to side. It should start dropping, hit a low number, then start rising again. Note what that low number is.
4) Lift the dial indicator needle so it doesn't get hit by the cube, and rotate the chuck 180 degrees. Find the low number again, on the opposite side, and calculate the difference. Now it becomes the same as dialing in a round piece. Tighten and loosen the jaws, keep checking both sides, and get the low spots to be equal (or as equal as you want them to be, I usually get them to within 0.001 of each other.)
5) Rotate the chuck 90 degrees, and repeat to align the next pair of jaws on centre.
It's good to draw a X on the face of the cube, so you know roughly where the centre is, then you can test-align your centre drill once you think you are dialled in. The first time I dialled in the cube, I was 0.100 off on both axis, but I thought I was dead on. So when I drilled the centre drill, I was off. No need to do this every time, just once to make sure you're good and know what you're doing.
I wish I had more pictures, but no such luck. I don't even know what pictures I could get.... Maybe I'll try for a video one day.
Step 5: Roughing the Bores
This step is just drilling a lot of holes. It goes by quick. You need to figure out how big of drill bits you want to rough your bores, and how deep they should go. For the numbers we calculated earlier, we need a 1.500 bore, and a 0.750 bore. So the roughing drill bits should be smaller then that. I used a 1 7/16 (1.4375) and a 23/32 (0.719). And the 9/32 hole for the middle. The easiest way to know how deep you should drill, is just draw a line with a marker on the drill bit. These are roughing operations, so all you need is to get it close. This will minimizes how much material you need to bore. If in doubt, make the hole a little smaller/shallower, it's better to bore more then to go oversize.
1) Centre drill (Picture #1)
2) Drill the first drill bit (9/32) halfway into the cube (cube is 1.875, drill about an inch deep) (Picture #2)
3) Drill the second drill bit (23/32) just less then the depth of your deepest bore (the bore is 0.625 deep, drill so the tip goes ~ 0.630 (You go a little beyond, because the tip of the drill bit is angled and will drop into the 9/32 hole)) (Picture #3)
4) Drill the third drill bit just less then the depth of your next bore (bore is 0.313, BUT you have a 23/32 hole in already, so the tip of the drill bit will go a lot deeper before you actually hit your depth. This make take some trial and error, or careful measuring. Using the 1 7/16 bit, I drilled until the diameter of the drill bit just appeared. Had maybe a 1/64 deep 1 7/16 hole, the rest was just the drill point angle.) (Picture #4)
Step 6: Finishing the Bores
Now we'll get to use that beautiful boring tool we made! You can use power feed for this, and just face off by hand (power feed Z axis, hand feed X axis). The dial indicator will tell you when you are getting close, and you can finish off the last ~0.030 by hand on the Z axis. 0.005 per revolution is a good feed to use in aluminium.
Note: X axis is for facing cuts, Z axis is for turning/longitudinal cuts.
1) Put the tool in the tool holder, and set it to the proper height (centre)
2) Using the carriage hand wheel, move the tool right near the face of the cube (don't touch it yet! Just get close)
3) Place a piece of paper on the cube face, and use the compound rest to inch (to thousandth of an inch, actually) closer, until the tool tip is barely touching the paper, and it (the tool) holds it (the paper) to the cube face. Now you know that the tool tip is the width of a piece of paper (about 0.003) away from the cube face. (Picture #1)
4) Move the tool to the side, so you don't crash into the cube or the jaws when you move in ( Picture #2)
5) Place the dial indicator with a magnetic back on the ways of the lathe, and set it to 0. (Picture #3)
6) Move the carriage in about 0.618 (watch the dial indicator). We're roughing the depth of the bore, and the bore should be 0.625. Leave about 0.010 for the undercutting tool, so if your bore is different, make this cut 0.010 less then the depth of bore you calculated. Don't forget to compensate for the 0.003 that is the paper width! (Picture #4)
7) Don't move the carriage now! Remove the dial indicator, and set it to 10 when it's not touching anything (neutral). (Picture #5)
8) Press the indicator against the carriage, until the needle reaches 0. Make sure it makes less then 1 rotation, so you should be moving it approximately 0.090. Now, you may move the carriage away. When you move the carriage back, you'll hit the dial indicator, and the needle will show you when you reach your depth of 0.615 (or whatever you set it to) as it approaches 0. You'll have a 0.090 countdown (should be at 10 when it hits, then travel around until it hits 0), and remember to use the carriage hand wheel (turn off the power feed) for the last ~0.030.
9) Now bring your tool back to the face of the cube, and begin roughing the deepest and innermost bore. Focus on depth first, get it to within 0.010 of the final size (90 on the dial indicator) then make one little (0.010) cut to clean up the sides. Now you can cut the sides, and get them to size (0.750). When you are making your final cut on the sides, go to full depth on the dial indicator (cut off that last 0.010, get to 0!) and face off the back. Now your first bore is complete! (Picture #6)
10) Do the same thing for the next bore. Touch the tool off on paper, reset the dial indicator to the next bore depth (0.313 - 0.010 = 0.303) , rough the depth to within 0.010 (90 on dial indicator), finish the width (1.500), then finish the depth with your last width cut. (Picture #7)
Step 7: Undercutting + Chamfering
Time for the undercuts. This is very similar to roughing the bores. This time around, we want power feed on the X axis, as we won't be doing much on the Z axis. Note that the X axis feed is about 1/3 to 1/2 of the Z axis feed, you can test this with a dial indicator on the carriage and watching how the cross slide moves when the power feed is turned on (example, if the feed is set to 0.010, and the cross slide only moves 0.005, then you know that it's 1/2. I'm sure you can guess what It would move if it was 1/3. Easy stuff.)
1) Put your undercut tool in, set it to centre height, touch it off on the face of the cube with paper, just like we did last step with the boring tool. (Picture # 1)
2) Move it to the side, set up the dial indicator again, yet this time move to full depth (0.625 + 0.003 for paper), and set the indicator to 0.
3) Now we need touch off on the edge of our bore and set the cross slide hand wheel micrometer collar to 0 (since we know that the bores have to be 0.200 and 0.350 bigger). Move the tool to depth (we only cut to 0.615, so the dial indicator should be at 90) and move the tool to touch the edge of the bore. I just turn the chuck by hand, and bring it closer and closer till the tool JUST scrapes the edge. We're going to be cutting here, so don't worry about ruining the finish or anything. You could try and use the paper again, but it's an awkward place to get to, and makes it more complicated then it needs to be. Once you touch, set the collar to 0.
4) Now we can turn on the lathe (you can bring the tool out, we know where it needs to go.) Move the tool into the correct depth, and turn on the power feed, so it begins facing off the back to leave a nice finish. Watch the collar, so you know that when it passes 0 you're at the edge. Turn off the power feed and continue by hand. Make your undercut now, by expanding the diameter 0.200. Once you get to 0.200, pull the carriage 0.010 back towards you, and bring the tool out. This is so you don't scrap back along the nicely finished face you just made. Pull the tool out, and your first undercut is complete! (Picture #2)
5) Do the same thing for the next size. Touch off on the face of the cube, move in 0.316 (0.313 + 0.003 for the paper), set 0 on the dial indicator, touch off on the edge of the bore (1.500 bore), set 0 on the cross slide collar, turn on the lathe, cut the depth, power feed face cut to 0, hand feed the undercut so the diameter becomes 0.350 bigger, retreat the carriage 0.010, and bring out your tool.
6) Chamfering time, to give nice edges on your bores. You can make these chamfers as big or as small as you like. Mine are about 3/64. For the outermost cube, you can do it on the mill when you are making the cube, or just do it with a file. For the inner cubes, follow along here.
7) Use the countersink to put a chamfer on the 9/32 hole first.
8) Using the 90 chamfer tool we made, set it to centre height, and chamfer the other two bores.
9) Voila! Side 1 of your cube is complete! That wasn't so bad, was it? All you have to do now is repeat the same operations on the other 5 sides. I find it best to do opposite sides (Imagine a dice, do side 6 and 1, 2 and 5, 3 and 4.). I think that it keeps the most material in the right places, and its easy enough to dial in each time.
Notes:
- When you get a few sides done, you have to balance the shims so that they cover the holes, yet leave enough room to dial in
- Always work on the smallest cube first, then the middle cube. Work from the inside out.
For the final side:
10) You have 5 sides done, the cube is looking excellent, you've finished the bores on side #6, now you're ready for undercutting. STOP!!! Here we are switching things up a bit. As soon as you undercut, the cube will fall apart. So we need to chamfer first. Chamfering the biggest bore is the same as always, but chamfering the middle bore and countersinking the 9/32 hole need to be done a little differently. You're going to be facing these two surfaces off (removing 0.010), so make the chamfers a little bigger then the others, so when the surfaces are faced, they become the right size.
11) Now proceed as normal, cut to your depth with the undercut tool, begin power feeding the face, when you reach the edge of the bore (0 on the collar) TURN THE MACHINE OFF, LEAVE THE POWER FEED ON. I learned this the hard way. When you try to turn the undercut, as soon as you reach the final diameter, the cube will fall off. Now, when your machine is spinning at 600 RPMs, that little cube begins bouncing around inside and smacking into your tool and gouging the heck out of itself, ruining all the nice finishes you've put on it. My idea to solve this was drop the RPM to as slow as it can go, and get ready to stomp on the brake as soon as the cube fell off. My teachers idea was much better, so we'll be using it here.
Now you should be touching the edge, ready to undercut 0.200. Just start spinning the chuck by hand. Since you left the power feed on, the cross slide will continue moving along, and you can make your cut this way. Now, as soon as you hear/see the cube fall off, you can stop spinning. No ruined finishes!
Note: Sometimes the cube will not fall off right away, even once you get to the 0.200 undercut (or 0.350). This should be fixable, its just the slight errors accumulated, and there may be a few thousandths left on some of the corners, holding the cube on. Just use something soft to smack that cube out. I used a piece of wood and hit it with a hammer a few times. (my middle cube got stuck on one of my prototypes). When you are cutting the undercuts on side #5, you'll be able to see if they will be big enough to break the corners. You should be able to see the corners free floating, ready to fall apart when side #6 is cut. If the corners are still attached, then you messed up somewhere. Recheck your calculations.
12) Do the same thing for the next undercut, use the "hand feed". Power OFF, power feed ON. Spin that chuck! It's really not so bad, you may think that it'll be horrible spinning the chuck by hand, it's really not, but if you want you can just use power feed to get it close, then spin it by hand for the last little bit. Or try my stomping on the brake idea.
Now you have your very own beautiful Turners Cube! Not one built by a robot (CNC), but one built with your own flesh and blood and manual power (hopefully not too much flesh and blood!)
Step 8: Finished!
You're practically done!
The bores and holes are nicely chamfered, but the outside corners of your inner cubes are probably all nasty. Time for oodles of deburring and chamfering! Grab some itty bitty files and get at it!
I haven't done this part yet, but I'll be sure to post pics once I have (EDIT:: Did it, it wasn't as bad as I thought it would be. Just gotta throw it in a polisher to shine it up then you can see the final product.). Chamfer and deburr, polish, and you'll have the best looking paperweight anyone ever saw. I guarantee that everyone will be confused on how you made it. Now you know that it's not that hard! (But don't tell them that. Tell them it's magic)
I'll leave a nice little summary of all the steps here, so you don't have to scour through all my words each time. Obviously, if you have different cubes sizes, your calculations and bores will be different sizes, so change the numbers when it's appropriate.
- Get your calculations and cube done
- Centre drill, and drill 9/32, 1 in deep
- Drill 23/32 so the tip is 0.630 deep
- Drill 1 7/16 so the diameter just appears
- Finish bores (0.750, 0.615 deep and 1.500, 0.303 deep)
- Undercut first bore 0.200 bigger, undercut second bore 0.350 bigger
- Chamfer and countersink
- Repeat on other 5 sides.
When you look at it that way, it doesn't look hard at all, does it?
Have fun and good luck! Post pictures of the cubes you made in the comments! I'd love to see more cubes of all different sizes!
Step 9: 4 Nested Cubes
Here I will show you how to make 4 nested cubes. They are easier to make then the free floating cubes, simply because there are less operations to do per side. I spent 4 hours today on this (I already had a cube made, just did the lathe work today), most of which was me not working very hard/setting up. Once I got the first 2 sides done, I busted out the last 4 sides in an hour and a half. So all in all, I bet it could be done in 3 hours of working hard, once you know what you're doing.
We'll start with the calculations. The cube began at 1.900 after milling, and I wanted 4 cubes. I decided to keep it simple, and make the difference between each cube 0.500 (as opposed to 1.900/4 = 0.475 difference). So the cubes are 1.900, 1.500, 0.900, and 0.400.
For the bore sizes, I drew the 4 cubes on Google Sketch up, drew an X to find centre, and then used the tape measure to find the corner to corner distance of each. I then just drew circles (make sure to keep the diameters of the bores less then the corner to corner distances.) until I thought they looked good. In hindsight, I would have made the bore diameters closer to the corner to corner distances, I think it would look cleaner. Maybe I'll make another. Since the difference between cubes is 0.500, the bore depth is half of that (so 0.250).
The cubes are 1.900, 1.400, 0.900, and 0.400. The bores are 1.700 x 0.250, 1.100 x 0.500, 0.500 x 0.750, and the hole through is a 13/64th drill bit.
- Now we can begin! Put the cube in the 4 jaw, and dial it in.
Note: On one side, I tightened the vice too much, and there are now indents along the side of the cube. It was the 5th side I did, I believe. 5th or 6th. So be careful when tightening, keep it tight for safe machining, but don't tighten it so much that you crush the aluminium.
- Centre drill, drill 13/64th's 1 in deep, drill 7/16's so the tip is 0.750 deep, drill 1 1/16th so the tip is 0.500 deep, and drill 1 5/8ths so the diameter just appears. (I'll say this now, I never quite worked out exactly how far to rough with the drill bits. If you put the tip to the bore depth, you will never screw up (because the drill point angle will go into the smaller hole, so the diameter you are making will not be to depth.). You may have more boring to do, but that's fine. Experiment and find out what works.)
- Get the boring tool set up, set it to centre height, and touch off on the face of the cube (use the paper!)
- Set up the dial indicator on the ways, and move in to your first bore depth. Don't leave extra room for undercutting, all we're doing is boring. It doesn't matter if you do biggest to smallest, or smallest to biggest, since we're not undercutting, and the cubes will always be attached. I did biggest to smallest, because after roughing with the drills, it looked weird. (Again, when roughing, always make the drill hole smaller/shallower if you're having doubts. It's better to have to bore more, then to have a too big, rough hole.) So if you're doing the 0.750 bore first, then move in 0.753 (remember the paper width!) and set 0 there.
- Begin roughing out the bore depth, getting to 90 on the dial indicator (save the final depth cut for last!). Then rough out the diameter of the bore. As before, on your final diameter pass, go to 0 on the dial indicator (full depth) and make your facing cut, so that you have a nice smooth transition between the diameter and the face.
- Repeat for the other 2 bores.
- Chamfer if you like, I didn't for this one because I'm going to throw it in a steel shot tumbler to try and polish it, and that will break the corners. Also, I knew that it would be wicked hard to file the edges of the inner cubes, since they are still attached, and I figured that it would look funny if the outer cubes and the bores were chamfered, and the inner cubes were not. So I left the corners sharp for now, the tumbler will smooth them off a bit (and hopefully smooth them equally).
- Repeat on the other 5 sides (remember to do opposite sides, think of a dice! Do 1 then 6, 2 then 5, 3 then 4)
And you now have 4 nested cubes! I think the nested ones look better in pictures, and are nicer to look at, but the free floating cubes are cooler/more mind blowing/better to play with.
I didn't take many pictures, there is not much to see. Just imagine all the pictures from previous steps, but think of 4 cubes, not 3, and forget the undercuts. I wish I took a picture after all the roughing drill bits had gone through, so you could see what it looked like, but oh well.
Attachments
Step 10: 5 Free Floating Cubes
I don't think this cube is going to work out... I started making it, and got 2 1/2 sides done, and it just doesn't look like its going to work. The edges of the two biggest cubes are only 0.050. I though it'd be enough, but the material there is so weak and bends way to easily, so I won't be able to hold it in the vice tight enough to finish the other sides (I could get sides 3 and 4 done, because i can just hold super tight on the edges that are unfinished, but side 5 and 6, all 4 jaws of the 4 jaw are only holding onto 0.050 thick of aluminium.)
I could just delete this step, but I'll leave it in to share my mistakes so other can learn from them too. The undercutting, however, still looks like its going to work. I'll get some pics of the cube so you can see. It leaves some interesting looking edges, and may not be as pretty, but functionality-wise, its still good.
I still want to make a 5 free floating cube, so I'll see if I can find some 2.5 or 3 in cubes this weekend. All I have available to me now is < 2 in. Which is no good.
EDIT:: No such luck, no more access to a machine shop. What you see is what you get. I hope someone experiments with this, it could turn out pretty excellent.
I calculated the cubes to be 1.900, 1.520, 1.140, 0.760, and 0.380. The bores are 1.800 x 0.190, 1.350 x 0.380, 0.900 x 0.570, 0.450 x 0.760, and the hole through is a 13/64 drill bit (~0.200). The undercut diameters are 2.250, 1.725, 1.150, and 0.600
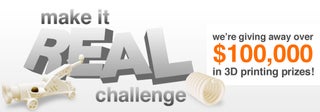
Participated in the
Make It Real Challenge