Introduction: Two Canoes and a Crazy Idea
The idea began with a book I never read called The Six Hour Canoe. The idea of building a canoe in a short period of time seemed to open up the possibility of building the boat in a foreign country with local materials and leaving the boat when the vacation was over. I needed advice and went online to find a country, a boat to build and the skills and tools to create this project. I was overwhelmed by the information and support.
There were some skeptics, my friend Pete said, “Obtaining materials in a foreign land on a set time..I would suggest not bringing a watch but, instead, a calendar.”
Matt from Jem Watercraft suggested I build a prototype and, “beat the hell out of it,” to see if it would be up to my expectations. Then he offered to draft any designs I wanted for this crazy idea. I accepted his offer and had the plans drafted in both metric and inches. I thought since I might be building this outside of the U.S.A. I might as well use metric. I loved it try dividing 14' 7 19/32" by 11 in your head. (Stubborn Americans is all I can say.)
Step 1: Lofting and Cutting
I cut all the panels with a hand saw just in case I would not have power tools. This was not as hard as I expected. Just make sure you flex the plywood so as not to pinch the blade. The pull saw worked great and it did not raise near as much dust or make as much noise.
Step 2: Butt Joints and Testing
I tried 4 brands of epoxy and three fillers plus drywall tape instead of fiberglass cloth. Wood flour and dry wall tape with no scarf or butt blocks. I used plastic film to stop the epoxy sticking to the table and boards. Instead of using a scarf joint or butt blocks one suggestion was three layers of glass cloth on both sides. This was brilliant it was quick and stronger than the wood.
Step 3: Tape Stitch and Glue
Duct tape was suggested as a method of holding the panels together. That was one idea I had to reject. Copper wires or cable ties worked much better. The putty was used to tack the panels into place between the wires and tape.
Step 4: Tricks We Discovered.
Note the self stick drywall tape. When it would not stay put I used a strip of plastic. The plastic would stick to the epoxy and usually had enough adhesion to hold the errant tape down. Detail of capping the raw edges of the plywood.
Step 5: Bow Seat
This shows how the bow seat was latched. Note foam rubber and bolts that go inside the holes to attach the rear of the seat. Wide shot of the bow seat
Step 6: Dry Box
Bungee cords were used to latch the rear hatch. The rear hatch makes for a great dry box. The rear hatch cover with bungee cords make a great spot to store the painter. The knot in the bungee cords are snapped in place under the notched boards.
Step 7: Testing If Wood Floats.
Testing the prototype for final stability. This took a few tries with the camera on a piling and the self timer.
Heeling position. The boat was more stable than my Grumman, Mad River or Coleman canoes full of water. Even full of water this floats.
Step 8: Canoe 2 in Chile Begins.
Billy Gerhard Ernst Elizalde from Chile (Billy from Chile) offered the use of his shed and tools for constructing the boat. He had built several wooden boats and lives a few miles from the Bio Bio River in Southern Chile. My son Andrew at the home of Billy from Chile. Setting the seats and bulkheads. This is not the way the prototype was built. In the second image I am screwing the inwales down.
Step 9:
- I used cable ties instead of wire. They were much easier to remove.
This `was a better way to use the duct tape, to prevent putty leaks when turned over. I brought all the hand tools to build this boat in a small briefcase. When talking to Billy from Chile I did not know what to expect when he offered the use of his boat building shed. I was shocked at his generosity in the use of his precious power tools. In the background look at one of the boats he built.
Step 10: Finishing the Hull
Andrew cleaning up the putty after removing the tape. Smoothing the seams before the final taping. Slopping on the epoxy over the fiberglass seams.
Step 11: Success
Finished hull on Largo Grande in Concepcion Chile. I had 40 years of canoe prejudice about what hull design would be adequate. I wanted a rounded chine with some rocker and a slight V. I found plywood was manufactured in Chile and calculated two sheets would create a 15’6” hull (4.7 meters). That would be fine for 2 people and gear.
Step 12: Designed Around the Seats
When running white water I usually move the bow paddler behind the bow seat to a kneeling position to keep the bow from diving into standing waves and lower the center of gravity. I began with the seats in this position closer to the center of the boat and low in the hull. This allows for fore and aft bulkheads that serve as frames to simplify the construction process and provide storage.
A special thanks to Matt from Jem Watercaft (jemwatercraft.com) for drafting the plans for any boat of my design. We exchanged 24 emails on how high the bow what was the rocker where are the bulkheads and seats.
Step 13: The Project As It Was Planned.
The plan was day one to cut the plywood panels, coat them with epoxy then build the seats. Day two the panels would be butt spliced with drywall tape and then epoxy resin and wood flour was mixed to make putty. Scarf joints would be made for the long boards on the gunwale and glued with putty. Day three the fore bulkhead and seats would be used as construction frames as the panels were attached with temporary screws and shaped with cable ties and copper wires. The outside seams would be covered with duct tape epoxy putty would be spread inside the hull between the cable ties. Day four ties and screws would be removed and the uneven hull seams shaped on the outside. Drywall tape would be applied to both the inside and outside of all seams and a coat of epoxy would be brushed on the tape and very dry epoxy putty would be squeegeed into the tape on both the inside and outside of the hull. Day five touch up the holes and coat the hull with one more coat of epoxy. That was the plan which went quite well except for a few problems.
One disaster occurred while using epoxy that was mixed by weight. I had read you could spread a nice even bead of putty by putting it in a Ziplock bag then cutting off the corner to squeeze out a bead like a pastry chef. The epoxy was curing too fast so, I figured a little less hardener would give me a little more time to get it spread into the proper place. I had built a scale to measure the 2 to 1 weight ratio. My crude scale was a board balanced on a sharpened piece of wood with the resin twice as far as the hardener from the fulcrum. This was working fine until I decided I needed more time and changed the ratio but instead of putting the hardener closer to the fulcrum I adjusted the resin. The putty looked good as I mixed the wood flour into peanut butter consistency then filled my baggie with goop. As I began to squeeze the baggie the putty began to get warm in my hand this quickly escalated to very warm then to hot. When I could not stand the heat I threw the baggie away and smoke began to billow out of the trash can while I worried about setting the rags sawdust and shop on fire.
I tested the online advice about glues, tools fillers joints and fasteners on my prototype. I tried 4 different brands of epoxy resin. I tested wood flour, fumed silica, white all purpose flour and sawdust for fillers. I tried fiberglass, and drywall tape for joint strength. I experimented with copper wires cable ties and dry wall screws for positioning the panels. I tried various tools and ultimately took a minimum of tools: my smallest surform two card scrapers (used instead of sandpaper on green epoxy) my contour gage, a pull saw and metric tape measure. I also packed a handful of screws and some ringed bronze boat nails.
Step 14: Lessons Learned
What did we learn? Joe and Andrew from Oregon, with drafting help of Matt from North Carolina and logistic support by Billy from Chile and advice from paddlers across the world can build a boat in a foreign country in 72 hours.
Sea snails, barnacles, mussels and blood sausage taste better than they sound. You can build a butt joint in plywood with drywall tape and epoxy putty that is stronger than the wood. When crawling about the floor of the shop with epoxy on your 12 panels make sure the dogs don’t come in to play with you.
There are a lot of wonderful people out there messing about in boats and their love of boats crosses all the cultural barriers.
I can't believe you read the entire story thank you. Go back to the top of the page and on the right select the Vote button if you would like to reward me.
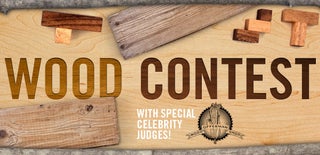
Third Prize in the
Wood Contest