Introduction: UberCool MiNi RECHARGEABLE POWER SUPPLY
For the people who are indulged in electronics either as a hobby or as a profession, one of the most essential parts of work is the power supply. Without power, electronics circuits and devices are a piece of paperweight. Power supplies are the devices which provide energy to the electronic circuits and thus form the basic foundation of an electronics workplace. Power supplies come in different varieties and configurations to suit different purposes and needs. Depending on the power requirements and cost of an application, the power supply is chosen to suit the best. For e.g. in critical applications like industrial deployments, the designers will need a robust and efficient power supply to meet the industrial standards and so forth for their testing. But for general purpose applications like for an electronics hobbyist’s lab, a low cost power supply will serve its purpose. We all have been familiar with the simple LM317 and LM78xx linear ICs based power supplies those are usually the first project choice for an electronics hobbyist. However time and technologies have come so far and one can see highly sophisticated, robust and efficient power supplies today.
Majority of the power supplies that we use are the ones which takes power from the mains power socket that is usually 220/110 V AC and then using a step down transformer with a couple of other circuitry like rectification, filtering and regulation it derives a regulated DC output that goes into you projects or equipments. These power supplies have both their advantages and disadvantages: the advantage is that they can deliver continuous power throughout the time and the disadvantage is that they consumes more space and are tied up to a physical location only (i.e. to the mains power socket). What would you to do if you need to test a project which would work outside your home like some sunlight sensing project or weather station project, etc or imagine if you are in a situation where the power cord of your power supply could not go to the nearest wall power socket. The point is that these power supplies are not portable to be carried around. To the alternative of this, we can use batteries which are portable power sources. Presented here is a mini rechargeable power supply that will fulfill nearly all your basic needs of powering your small projects and equipments and as this mini power supply is very robust and portable, you can carry it wherever you want. The power supply uses a rechargeable Li-ion battery (that is used in all mobile phones and MP3 players nowadays) and a couple of other circuitry to deliver a portable power supply solution with sufficient power to your projects. The power supply can deliver 9.2 volt up to 1 A (approx), 5 volt up to 1 A and 3.3 volt up to 500mA. It accepts single 3.7v Li-ion battery pack ranging up to 3000mAH capacity. It uses dedicated Li-ion charging IC to safely charge the cell without letting it to undercharge or overcharge. The charging circuit not only displays the user about bad charging input source and charging status but also ensures safety against reverse current, short circuit and thermal protection. The dedicated circuit also monitors the battery discharge and shuts off the load when the he battery is discharged up to a certain limit and need to be recharged again. Even if your battery is fully discharged, you can power the supply from external power source without disturbing the output regulation and charging of the battery. The power supply is so versatile that it can be charged from various power sources like DC wall adaptors, USB source or a solar panel. This mini power supply also includes a female-A type USB connector so that you can power and charge other equipments like mobile phones and also houses white LEDs so that you can use it as a flashlight too.
Step 1: Block Diagram Description
The charging input source for the power supply can be anything from 4.35 to 10.2 volt max which can be harnessed from DC power adaptors ,or USB port or 5 to 10 volt solar panel (with a bypass diode in series). This DC input then goes to the battery charge management circuit to which a 3.7v single cell battery is connected. It is to be noted here that Li-ion batteries are very sensitive to charging voltage and current, and need a stable charging source. Most cells charge to 4.1 or 4.2V/cell with a tolerance of +/–50mV/cell. If the charging voltage and current is not what it should be like most people take these Li-Ion batteries and plug them directly into any source, this is not correct. You may end up losing the capacity of your battery soon and degrade it. So to the point, a dedicated charging circuitry is needed for the Li-Ion battery which executes the necessary charging algorithm inside it to safely charge the battery. In the later article, we will also discuss the Li-Ion battery charging technique in short. Next the power from this battery management circuit goes to the battery under-discharge protection circuit which continuously monitors the battery voltage and when it reaches at a certain limit where the battery is supposed to be fully discharged and needs to be charged again, it shuts off the load that is connected to the next section thus not to further discharge the battery. Li-Ion batteries are again very sensitive to discharge limits, if you discharge them further, then a certain limit is reached where the battery looses its actual performance and sometime it is not even possible to recover it again, so a discharge monitoring circuit is must to have. The under-discharge protection circuit not only shuts-off the load connected to it, but also tell the user that battery is discharged and needs to be recharged again. Next we have the Boost converter section which is a DC-DC converter and its function lies in the fact that it steps up the low voltage DC to high voltage DC. Here it takes any voltage between 2.95 volts to 5.5 volts and steps-up to 9.2 volts. However the boost converter can be configured to a maximum step up voltage of 15 volts but in our case, we will use 9.2 volts only and that is sufficient for portable power applications. After we have derived regulated 9.2 volts from our 3.7 volts Li-ion battery, 5 volt and 3.3 volt positive linear regulators are then used to derive regulated +5 and +3.3 volts. These three voltages that are +9.2 v, +5v and +3.3v are routed to an external connector so that it becomes easy to connect your projects to it. The regulated (but not current limited) +5v also goes to a female USB-A type connector so that you can power and charge most of your USB powered products. You can directly connect you embedded learning kits like ARDUNIO boards, MSP430 launchpad, etc to this +5 v USB power source. At last we have four white LEDs connected which serves the function of flashlight. The circuit of the power supply is so deigned that not only it delivers regulated voltage rails to power your loads continuously but also ensures safety to the LI-Ion battery.
Step 2: UNDERSTANDING LITHIUM-ION BATTERIES
Li-Ion is rapidly becoming the chemistry of choice for portable applications because of its high capacity-to-size ratio and a low self discharge characteristic. It uses a cathode (positive electrode), an anode (negative electrode) and electrolyte as conductor. The cathode is a metal oxide and the anode consists of porous carbon. During discharge, the ions flow from the anode to the cathode through the electrolyte and separator; charge reverses the direction and the ions flow from the cathode to the anode. Figure 1 illustrates the process. When the cell charges and discharges, ions shuttle between cathode (positive electrode) and anode (negative electrode). On discharge, the anode undergoes oxidation, or loss of electrons, and the cathode sees a reduction, or a gain of electrons. Charge reverses the movement.
Li-ion is a clean system and only takes what it can absorb; anything extra causes stress to the battery and degrades it. Most cells charge to 4.20V/cell with a tolerance of +/–50mV/cell. Battery capacity C, expressed in mA hours is a measure of battery life between charges. Battery current has the units of C-Rate. For example, a 800 mA-h battery has a C-Rate of 800mA. The current corresponding to 1C is 800 mA and for 0.1C is 80 mA. A Li-Ion battery charging process consists of three stages:
• Pre-Charge/Slow charge: Pre-charging stage using current of 0.1C basically to rejuvenate a dead cell
• Constant Current (CC) Charge/Fast charge: Constant current charging stage uses current of 0.2C to 1C. (Some fast chargers even use 1.5C or 2C charging current, but it is not recommended)
• Constant voltage (CV) charge: After the battery voltage reaches 4.2V
The basic algorithm is to charge at constant current (0.2 C to 1 C depending on manufacturer and application demands) until the battery reaches 4.2 Vpc (volts per cell), and hold the voltage at 4.2 volts until the charge current has dropped to 10% (0.1 C) of the initial charge rate. The higher the current at you charge your battery, the lower the life of your battery will be. In this power supply we will set the charging current to 0.5 C current approx. The termination condition is the drop in charge current to 10%(0.1C). The current vs voltage curve for charging Li-ion battery is given in figure 2.
During the pre charge stage, the battery is charged with a constant low charge current of 0.1C, if the battery voltage is below 2.7V (point A). The pre charge stage is rarely used during the charging process of a Li-Ion battery. The constant current and constant voltage charging (CC-CV) are the most important stages during a recharge process. Most Li-Ion batteries have a fully charged voltage of 4.1 or 4.2V. The battery is first charged with a constant current from 0.2C to 1C until a battery voltage reaches 4.1 or 4.2V (point B). The charge manager IC continuously checks the charging current and the battery's voltage. Whenever found the battery's voltage reaches 4.1 or 4.2V, the charger will switch to constant voltage charging mode. The battery is then charged with a constant voltage source at a fixed battery voltage of 4.1 or 4.2 V. During this process the charging current will start to fall due to internal cell resistance. When the charging current falls below 0.1C (point C), the charging process must stop. When the battery is fully charged, most of the electrical energy is converted to thermal energy. Overcharging batteries can cause overheating, explosion due to out gassing of the electrolyte and severely reduce battery life. Li-Ion batteries are extremely sensitive to overcharging and hence it is critical that the final voltage be controlled to within ±50 mV of 4.1 or 4.2V.
The discharge curve of the Li-Ion battery is shown in figure 3.The full capacity of the battery is presumed to be when the terminal voltage is 4.2 volts i.e. max. When being discharged and the terminal voltages reaches nominally 2.7v, the battery is deemed to be at the “End of capacity” then i.e. fully discharged. It should not be discharged beyond this point and the protection circuit must shut off the load connected to the battery at this point.
Step 3: CIRCUIT DESCRIPTION
At the heart of the Li-Ion battery charge management circuit is the Li-Ion battery charger IC BQ24074 from Texas Instruments. The BQ24074 are integrated Li-ion linear chargers and system power path management devices targeted at space-limited portable applications. The devices operate from either a USB port or AC adapter and support programmable charge currents up to 1.5A i.e. we can charge up to 3000mAH batteries at 0.5C. The input voltage range with input overvoltage protection supports unregulated adapters. The bq24074 features dynamic power path management (DPPM) that powers the system while simultaneously and independently charging the battery. The DPPM circuit reduces the charge current when the input current limit causes the system output to fall to the DPPM threshold; thus, supplying the system load at all times while monitoring the charge current separately. Not only this, the IC support programmable input current limit up to 1.5A, programmable charge termination current, programmable pre-charge and fast-charge safety timers but also reverse current, short circuit and thermal protection. Additionally, the regulated system input enables instant system turn-on when plugged in even with a totally discharged battery. The power-path management architecture also permits the battery to supplement the system current requirements when the adapter cannot deliver the peak system currents, enabling the use of a smaller adapter. The battery is charged in three phases: conditioning, constant current, and constant voltage. In all charge phases, an internal control loop monitors the IC junction temperature and reduces the charge current if the internal temperature threshold is exceeded. The charger power stage and charge current sense functions are fully integrated. All the current settings like charging, input-limiting, and termination for the IC are programmable by selecting the right resistor values at appropriate pins. The charge source input ranging from 4.35 to 10.2 volts is fed to the pin number 13(IN) and 8(Vss) of IC1 from the DC jack CON1.The three pins of the LI-Ion battery are connected to the TS (pin 1), BAT(pin 2,3) and ground pin of IC1. It is to be noted that most of the Li-Ion battery packs available today have at least three pins - positive, negative and NTC thermistor out . The NTC thermistor is built into the battery pack itself to monitor the battery temperature. The IC BQ24074 supports only batteries with 10k thermistors. If your battery do not have this thermistor option, then either you can yourself attach a 10K thermistor from ground to pin 1(TS) of IC1 mounting it to the battery pack, or you can disable this feature by shorting the thermal bypass jumper which enables a 10K resistor from pin TS to ground thus bypassing the thermal monitoring feature. As shown in the circuit, one green LED is connected to the pin 7 (PGOOD) which glows if the input charging source is valid and acceptable for charging the battery. A Yellow LED is connected at pin 9 (CHG) which displays the charging status of the battery. This LED glows when the battery is being charged, shuts off when finished charging and flashed at the rate of 2Hz if the IC’s internal safety timers have expired thus depicting an error state which signifies that your battery is not in a good condition. Because this IC works on linear topology so a 10uF (C1) electrolytic capacitor at the input and a 47uF (C2) one at the output is required for stability purpose.
As we have used a 1200mAH battery in our power supply project, so now we will go through the programming steps of the various current limits for BQ24074 IC. First for setting the charging current at 0.5 C, we have to find the value or Rset that will be connected at pin 16 (Iset) to ground. For 1200mAH of battery capacity, 1C=1200mA and thus 0.5C =600mA. So, for Iset =0.5C=600mA, the formula for calculating Rset (as per datasheet of BQ24074) is:
Rset = ( Kset / Iset )
Value of Kset = 890 (as given in the datasheet)
Thus Rset = (890/600mA) = 1.48K ohm
The value of 1.48K ohm is not practical and is not available so we choose 1.5K which will set the charging current Iset to about 593mA which is acceptable for the purpose. Thus Rset=1.5K (which is resistor R6 in the circuit).
Now for setting the charge termination current at 0.1C = 120mA, we find out the value of Rterm that is connected from pin 15 (Iterm) to ground. The formula for calculating Rterm (as per datasheet of BQ24074) is:
Rterm = (Iterm x Rset)/0.03
Thus Rterm = (120mA x 1.5k)/0.03=6K ohm
Thus Rterm = 6K ohm (which is resistor R5 in the circuit).
Now we will calculate the Rlim value which will set the max input current consumption limit for IC1 which will include the battery charging current plus the current supplied to the load. We select a nominal value of about 1A for the purpose in our project.
So for Ilim = 1A
Rlim = (Klim / Ilim)
Klim = 1610 (as given in the datasheet)
Thus Rlim = (1610/1 A)=1.610K ohm
But again, the value of 1.61 K ohm is not practical so we choose 1.5 K ohm which will give us Ilim=1.073 A which is again acceptable for the purpose. Thus Rlim = 1.5K ohm (which is resistor R3 in the circuit).
We can also manipulate the internal charge timer expire values for IC1 by calculating the value of a resistor which will be connected from pin 14(TMR) to ground. By not connecting any resistor at this pin, it selects the default value of 1800 second for pre-charge and 18000 seconds for fast charge. We used the default timer values by not connecting any resistor to the TMR pin. Here we complete the setup for our battery charging circuit. The output (positive rail) from this section is taken from pin 10 and 11 (OUT) of IC1 and is fed to the next section via a SPST toggle switch SW1. SW1 is the main power switch which will be used to switch ON the power supply.Four white LEDs are connected in parallel through a 5 ohm (0.5 watt) current limiting resistor in series and a switch SW2 to the positive rail directly.
The next section is the battery under-voltage (or under-discharge) protection circuitry that continuously monitors the battery voltage and switches off the load in case the battery has reached the “End of capacity” limit. As we have already discussed in the previous section, that at about 2.7 volts (vary with different circuit applications), the battery is deemed to be reached the “End of capacity”. The battery should not be discharged further then. This circuit section deploys this functionality by using a low-power comparator TLV3011 (IC2) and a 3A PFET load switch TPS27082L (IC3) from Texas Instruments. The TLV3011 is a combination of a comparator and reference with ideal specifications for threshold detecting. Its internal precision 1.242 Volt reference comes with 100ppm/°C (max) drift sustainability. TLV3011 have 5µA (max) quiescent current, input common-mode range 200mV beyond the supply rails, and single-supply operation from 1.8V to 5.5V thus ideal for this low voltage battery monitoring application. The inverting input of the comparator is connected to 1.242 volt internal reference voltage which is accessible at pin 5 (REF) while the non-inverting pin of the comparator is connected to a potential divider network consisting of three resistors R9, R10 and R11. This potential divider is so designed that its output falls to 1.242 volts when the input is about 2.8 volts (slightly higher than 2.7v standard to be on the safe side), thus when the positive rail reaches 2.8 volts (which is the battery voltage) and crosses further down a bit, then the inverting terminal voltage of the comparator goes above the non-inverting one and the output of the comparator goes low thus stating under-voltage/under-discharge condition. The IC3 TPS27082L is a PFET load switch which switches ON if its pin number 5 (i.e. ON/OFF) is fed with voltage greater than 1 volts. Now as this ON/OFF pin is directly connected to the output of the comparator (pin 1), so whenever the battery rail goes below 2.8 volt it turns the output of the comparator low and thus switching OFF the load switch and thus the load connected further to this stage is disconnected, hence no further discharging of the battery takes place. A red LED is also connected from the comparator’s output to the positive rail, which will glow when comparator’s output goes low thus stating a discharge condition. A pull-up resistor R18 is provided to turn ON the load switch IC3 normally because the output of the comparator is open-drain. Resistor R8 and C3 in the IC3 circuit is provided to set the slew rate of the load switch.
The output from IC3 is taken from pin number 2, 3 (Vout) and is then fed to the next section. The next section comprises of a boost converter module PTN04050C (IC4) from Texas instruments. Operating over a 2.95V to 5.5V input range, the PTN04050C provides high-efficiency, step-up voltage conversion for loads of up to 12W. The output voltage is set using a single external resistor. The PTN04050C may be set to any value within the range 5V to 15V. The positive rail taken from the previous section goes to the pin number 2 (Vin) of IC4. The voltage output of the boost converter is set using resistors R15 and R16 which are connected in series to give a value of 350k ohm in total. This sets the output voltage of the converter to 9.2 volt which is accessible at pin number 4 (Vout) of the device. Then this 9.2 volt rail is fed to two 5 volt and 3.3 v positive voltage regulators LM7805 (IC6) and uA78m33 (IC5). Thus we get three positive rails +9.2v, +5v and +3.3v which are connected to the terminals post (CON3) so that the user can access these voltages. Some electrolytic capacitors are provided at the input and output of these regulators for stability purpose. A female USB-A type socket is also provided that uses the +5 v rail from LM7805 output and the ground rail.
Step 4: Using the Power Supply
Enclose the power supply in a suitable box and test the circuit at the test points before powering it for the first time. Safely connect all the terminals of the battery to the circuit board and set the thermal bypass jumper accordingly. Now switch ON SW1 and the power supply should provide +9.2v, +5 v and +3.3 v at the output terminals. It is safe to draw about 800mA from the 9.2 and 5 volt output terminals while 3.3 v output is able to provide 500mA of current only. Switch SW2 will enable you to turn ON the flashlight LEDs while switch SW1 is also ON. You can connect batteries up to 3000mAH capacities to the power supply but you have to recalculate the current setting resistors as described in the previous section. When the battery voltage reaches below 2.8 volts, the red LED will glow depicting the “End of capacity” of the battery and the loads are automatically turned OFF.
To recharge the battery you can connect it to a 4.35 to 10.2 volt DC adaptor or to any USB power source. You can also charge the battery by connecting it to a 6v to 10v solar panel with a bypass diode in series. If the input charge source is a valid source, green LED will glow depicting the power good indication. The yellow LED glows when the battery is being charged, shuts off when finished charging and flashes at the rate of 2Hz if the IC’s internal safety timers have expired thus depicting an error state which signifies that your battery is not in good condition.
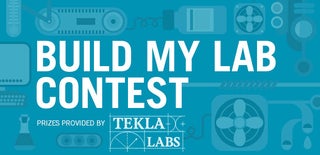
Finalist in the
Build My Lab Contest
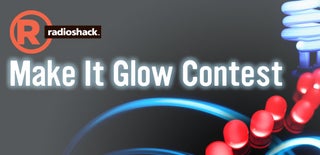
Participated in the
Make It Glow Contest
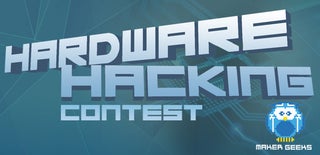
Participated in the
Hardware Hacking